El Grupo Kohler da un paso más hacia el futuro
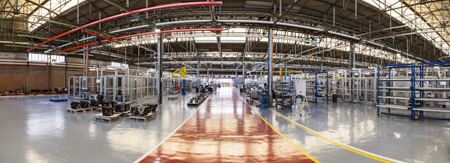
La presentación de la nueva línea de montaje del KDI constituye un hito histórico en la trayectoria de Lombardini/Kohler. Así lo indicaba el propio Gianluca Paini, director de Operaciones de la compañía: “Personalmente considero este evento el más importante en la historia de la empresa, especialmente de los últimos 20 años. Y lo es porque si hace un año presentábamos nuestra intención de hacer algo, de introducir la nueva familia KDI, hoy lo que hacemos es demostrar que hemos sido capaces de hacer realidad esa intención”.
Desde un punto de vista operativo, este proyecto recogía varios desafíos, de tal forma que se consiguiera, al final del proceso, ganar en calidad, competitividad y reducción en los tiempos de suministro. El resultado es una de las líneas de montaje de motores más automatizada y moderna, que además tiene como otra gran ventaja para Lombardini haber logrado que se ubique en sus instalaciones de Reggio Emilia.
Esta nueva gama KDI permite igualmente, como señalaba Nino De Giglio, director de Comunicación de Lombardini, cumplir con dos grandes objetivos. Por un lado, responder a las nuevas restricciones de emisiones que reflejan las normativas Tier 4 Final y Stage IIIB, que entran en vigor a partir de enero de 2013. Y por el otro, extender la gama de productos diesel de esta firma hasta los 100 kW de potencia.
La respuesta inicial del mercado a esta nueva línea de motores no podía ser más positiva. “Los motores KDI van a formar parte de la nueva generación de máquinas que van a aparecer próximamente en el mercado. Desde el año pasado, hemos iniciado nuevos proyectos con fabricantes de maquinaria muy importantes para optimizar la implantación de los nuevos motores en sus equipos. Los resultados obtenidos en estos trabajos conjuntos están siendo excelentes, ganando las máquinas equipadas con KDI en competitividad en casi todos los parámetros: fuerza, potencia, ruido, vibración y consumo de combustible. Todo eso hace que nos orgullezcamos de anunciar que muchas de las nuevas máquinas que se presentarán en ferias como EIMA o Bauma, equiparán nuestros nuevos motores KDI”, decía Enrico Traino, director Comercial y de Servicio.
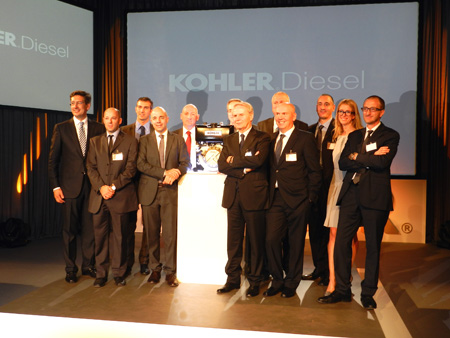
La nueva gama de motores KDI permiten además a Kohler/Lombardini aumentar su gama de soluciones para los fabricantes de maquinaria en sectores tan diversos como la Construcción, la Agricultura o la Generación de Energía. “Los fabricantes cuentan ya con una oferta completa de motores para máquinas desde las más ligeras y pequeñas hasta las más grandes”, añadía Francesca Rubbiani, directora de Marketing. Esto incluye desde pequeñas motoazadas hasta grandes tractores en Agricultura; desde pequeñas bandejas compactadoras hasta excavadoras en Construcción; y generadores de 3 a 60 KVAS en el sector de la Generación de Energía.
Giuseppe Bava, CEO de Lombardini, fue el encargado de cerrar el turno de presentaciones, agradeciendo a todos los departamentos de la compañía su esfuerzo y compromiso con este nuevo proyecto que permite “maximizar la competitividad, valores y destrezas de la compañía”. Una gratitud que hizo extensiva al Sr. Kohler por aprobar el desarrollo de un proyecto tan ambicioso en un contexto de recesión económica, y además hacerlo realidad en la propia fábrica de Lombardini en Italia.
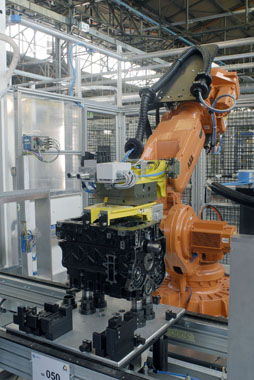
Con vistas a la entrada en vigor de las próximas normas referentes a las emisiones (TIER 4 final, por encima de 19kW en EE.UU.; Stage IIIB, por encima de 37kW en la UE) Kohler presenta la nueva gama de motores diésel KDI, Kohler Direct Injection.
El proyecto, muy centrado en las demandas del mercado, fue desarrollado utilizando el nivel más alto de tecnología existente. Una combustión limpia, realizada gracias a un sistema de inyección Common Rail de alta presión (2000 bar) de última generación, equipado con la válvula EGR (controlada electrónicamente), para la recirculación de la cantidad correcta de gases de combustión enfriados por líquido a través de un intercambiador agua/aire, permite conseguir la conformidad con los niveles de emisión al mismo tiempo que prestaciones únicas sin utilizar sistemas de “post- tratamiento, after-treatment”. El valor añadido del KDI y de las selecciones tecnológicas efectuadas para realizarlo se traducen, para los usuarios finales, en “Best Comfort”, por lo compacto que resulta ser el motor, por sus prestaciones, por su robustez y por los bajos niveles de emisión, tanto en términos de vibración como en cuanto al ruido y “Bajo Coste de Funcionamiento - Low Oprerating Cost”, eficiencia de consumos, uso y mantenimiento.
Los tres modelos de inyección directa, que se distinguen por una cilindrada diferente (1.9L – 2.5L – 3.4L), ofrecen dos distintas configuraciones:
- Inyección Mecánica: Conformidad a las normas de emisión Tier 3/STAGE IIIA
- Inyección Common Rail: Conformidad a las normas de emisión Tier 4/STAGE IIIB
Centro de excelencia
La fábrica de Lombardini en Reggio Emilia ha sido galardonada como centro de excelencia del Grupo Kohler. La meta de la excelencia en la calidad del producto, en el servicio al cliente y en la competitividad, ha sido el “elemento impulsor” que ha guiado las decisiones también para los procesos productivos. Los contrastes entre algunos de estos "elementos impulsores” han sido armonizados gracias a la estrategia productiva adoptada.
Efectivamente, si el objetivo de costes a menudo impone producciones en países asiáticos, China o India, la meta de altos estándares de calidad del producto, y sobre todo la necesidad de garantizar un alto nivel de servicio, asegurado por tiempos de entrega breves, han hecho que la estrategia Kohler optara por importar componentes da países emergentes y realizar el ciclo de montaje en Italia. Se mantienen dentro de la fábrica también los mecanizados principales (cigüeñales, árboles de levas y todas las operaciones de acabado de las bancadas, entre ellas la alisadura de los cuerpos de cilindro y los mecanizados de precisión). En especial estos últimos, fundamentales para conseguir las prestaciones relacionadas con los niveles de emisiones y con la reducción de los consumos de aceite, representan una de las mayores inversiones de todo el proyecto.
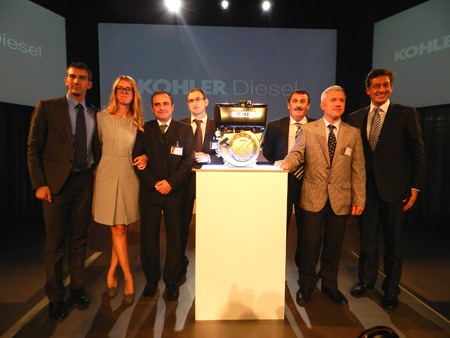
Además, la cercanía a los dos principales puertos marítimos italianos que se asoman al Mediterráneo (Génova y La Spezia) garantiza flujo de materiales, frecuente y rápido, tanto en entrada como en salida, lo cual permite satisfacer las demandas de clientes tanto en Europa como en todo el mundo.
Por último, la presencia de la dirección técnica garantiza la asistencia, inmediata y adecuada, exigida durante la fase de ‘start-up’ de un producto sumamente tecnológico como son los motores KDI.
Línea de montaje
La línea de montaje del KDI se distingue por su alto nivel de automatización y por un esmerado planteamiento de excelencia. La línea se divide en tres partes: la primera, denominada ‘short-block’, monta los elementos comunes para todos los modelos, es decir bancada, bloque motor, cárter del aceite, árbol de levas, cigüeñal, bielas y pistones.
La segunda, denominada ‘long block’, completa el motor en su parte alta y personaliza la versión. En esta fase se montan engranajes, culata, tapa de distribución, bomba del aceite, bomba del agua, sistema de inyección, motor de arranque y alternador.
Por último la tercera, no en serie sino paralela a la ‘long block’, monta la culata.
Toda la línea de montaje mide 236 metros y se compone de 39 estaciones, 11 de las cuales están automatizadas (14 estaciones, 7 de las cuales automatizadas para la ‘short block’ - 25 estaciones, 4 de las cuales automatizadas para la ‘long block’). La línea de culatas se compone de 6 estaciones, 3 de las cuales son automáticas, capaces de garantizar la calidad de montaje de los semiconos y la prueba de estanqueidad de las válvulas.
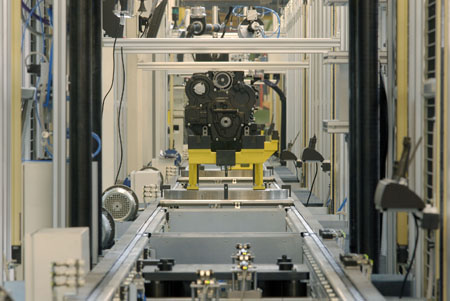
Las dos líneas principales (‘short’ y ‘long block’) están enlazadas mediante un vehículo automático (AGV, automatic guided vehicle).
La teoría en la que se basa todo el proceso es la de “objetivación del proceso productivo”, es decir la realización de un plan industrial que, introduciendo una “best practice” para realizar cada operación, lleva al usuario a seguir una ejecución correcta de la operación eliminando eventuales errores de distracción.
Se han dedicado meses de trabajo para poner a punto el análisis de modos de fallos y sus efectos (FMEA) de proceso y se ha prestado especial atención al concepto de “a prueba de errores” (Poka-Yoke).
Cada estación dispone del ‘LIPS’ (Lombardini Information Production System), un sistema informático de instrucciones que acompaña al motor a lo largo de todas las fases de su montaje y que ayuda al usuario guiándolo en cada estación con información sobre la configuración y las especificaciones técnicas a las que hay que ajustarse para realizar correctamente el montaje.
Mediante controles computarizados sofisticados, se garantiza la conformidad a la lista base, ya que la línea no permite pasar a la fase sucesiva si no se han pasado con éxito los puntos de comprobación de la estación precedente.
El concepto de objetivación de la fase ha sido llevado a los máximos niveles, con vistas a reducir al mínimo el proceso de ensayo final en el banco.
Para este último se utilizará un proceso mixto de breves ensayos en caliente con el motor en marcha y ensayos en frío con el motor accionado. En especial serán necesarios ensayos en caliente para los motores con sistema mecánico de inyección, mientras que se optará por un ensayo en frío para los motores common rail. Todo esto conforme a las tecnologías mejores y más avanzadas actualmente utilizadas en el sector de los motores diésel tanto industriales como para la automoción.
Capacidad productiva
De momento la capacidad productiva instalada es de 33.000 motores/año, con dos turnos de trabajo, y dicha capacidad se podrá doblar fácilmente en un plazo de 8-10 meses.
En cuanto al mecanizado de acabado de las bancadas, se ha previsto una solución escalable conformada por entre dos (para 26.000 unidades/año) y cinco (para 65.000 unidades/año) centros de trabajo de última generación, específicos para trabajar con fundición. Los centros de trabajo están en una célula robotizada capaz de manejar simultáneamente todos los tipos de bancada, tanto de 3 como de 4 cilindros. Esta misma célula alimenta la máquina de alisadura de cilindros, la lavadora de alta presión con chorros posicionados y la máquina de prueba de estanqueidad. Todo esto con vistas a garantizar la máxima precisión y limpieza antes de pasar a la fase de montaje.
Este es el ejemplo más significativo de solución productiva capaz de lograr la mejor combinación de competitividad de costes y altos niveles de calidad. Efectivamente, mientras se importan de países emergentes la fundición y los semielaborados, el acabado ‘high tech’ se realiza completamente con procesos dedicados. Todo esto estrechamente relacionado con la línea de montaje.
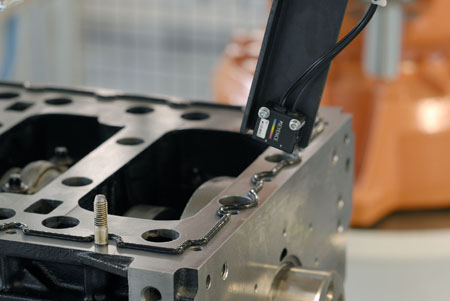
La nueva línea de Producción de motores KDI no constituye una innovación enfocada en sí misma; gracias al sistema integrado de planificación de los recursos de la empresa SAP, la gestión productiva se relacionará estrechamente con todos los procesos empresariales: desde las compras hasta la programación, desde las ventas hasta la logística.
Para responder a las demandas siempre más apremiantes del mercado, el grupo Kohler/Lombardini renueva su propia gama de motores diésel monocilíndricos refrigerados por aire, presentando el nuevo modelo KD15-440 que, con nuevos dispositivos y soluciones técnicas, fortalece y mejora la gama actual de motores de la familia 15LD y se coloca en la cumbre de su clase de potencia.
El modelo 15 LD 440, ya líder de mercado en muchos segmentos, como la agricultura, la construcción, los grupos electrógenos y las motobombas, ha sido adecuadamente reconsiderado volviéndose el modelo KD15-440, para mejorar sus prestaciones al mismo tiempo que permite reducir los costes de mantenimiento y facilitar el uso por parte del usuario final.
El nuevo motor KD15-440, monocilíndrico refrigerado por aire, con una cilindrada de 441 cc, se vuelve el ‘best in class’ en su gama de potencia, como definía durante su presentación el director de Ingeniería, Massimiliano Bonanni. Gracias al nuevo filtro del aire y al nuevo depósito, el modelo KD15 es el motor con el intervalo de mantenimiento más largo (Best Comfort) y con las operaciones de mantenimiento más simples (User Friendly).
El poder de acumulación del nuevo filtro del aire es cinco veces mayor que el actual y tres veces mayor que la referencia. Se ha logrado este resultado empleando un pre-filtro separador, con un alto grado de eficiencia, y una válvula de expulsión de los polvos acumulados en el propio filtro. Además, el cartucho más grande y el papel con un gran poder filtrante con el cual está realizado, aumentan la protección del motor y brindan una reducción notable de los costes de mantenimiento.
El nuevo depósito, con elementos modificados, contribuye mucho en facilitar todas las operaciones de mantenimiento, gracias a algunas mejoras importantes: como el nuevo filtro del combustible que se enriquece con una doble protección. Filtro primario y filtro de seguridad, utilizados conjuntamente, impiden la penetración accidental de materiales extraños durante las operaciones de sustitución. Se accede fácilmente al filtro primario, alojado dentro del depósito, y se puede cambiar sin tener que utilizar herramientas.
Además el nuevo grifo de descarga permite vaciar el depósito eliminando agua e impurezas que puedan depositarse en el fondo, con lo cual es posible efectuar la limpieza sin tener que desmontar todo el elemento. Por último la nueva polea del arranque recuperable, revestida en goma, reduce en hasta un decibelio la intensidad del ruido.
El KD15-440 es sólo el primero de la nueva familia KD15. Los nuevos modelos que la conforman se derivan de los modelos principales de la familia 15LD. Manteniendo los mismos puntos de fijación, las mismas medidas máximas y sin modificar las conexiones de los mandos a distancia, los nuevos KD15 sustituyen perfectamente a los modelos 15LD anteriores.
Los motores KD15-440 y KD15-440S estarán en venta a partir del mes de febrero de 2013, mientras que para los modelos KD15-350 y KD15-350S habrá que esperar hasta el final de 2013.
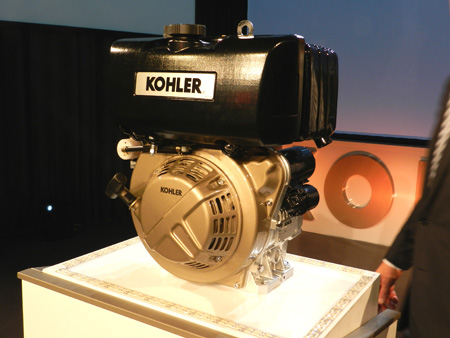