Kohler/Lombardini reinventa el concepto de combustión limpia y bajas emisiones en FIMA
7 de marzo de 2012
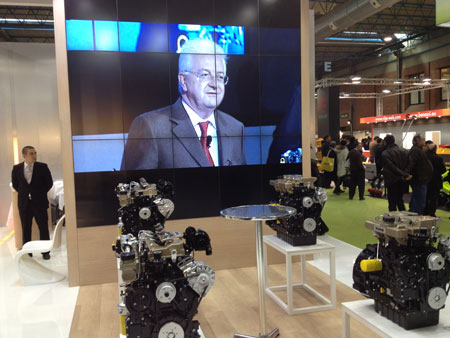
El año 2011 fue satisfactorio para Kohler/Lombardini, y un balance a posteriori sugiere que sirvió, sobre todo, para corroborar el liderazgo de la firma en su segmento de mercado. Así lo hacía saber Juan Cano, director de Lombardini España, filial de Kohler/Lombardini, durante la presentación dirigida a la prensa especializada con motivo de FIMA, el pasado 16 de febrero. Únicamente en nuestro país, se comercializaron 150.000 motores diésel de hasta 50 kW. Además, de Lombardini España, con sede en el municipio de Rubí (Cataluña) también sale una producción de 200.000 motores anuales. La clave está en no descuidar el servicio al cliente que se asienta sobre cuatro ejes: preventa, equipo comercial, administración y ventas y posventa.
La convocatoria de Lombardini España tenía además un componente de actualidad. El año que viene entran en vigor las normas de emisión de motores de 19-56 kW en EE UU y de 47 a 96 kW en Europa. “Esta normativa implicará un cambio total y, desde Kohler/Lombardini hemos reaccionado apostando por la innovación. Para ello, hemos incorporado, a los nuevos motores fabricados en Europa, una serie de novedades técnicas y también hemos ampliado la gama existente”, añadía Cano.
Motores que hacen posible una combustión limpia limitando las emisiones
Los nuevos motores Kohler Direct Injection se distinguen por el acopio de una tecnología a la vanguardia, que permite una combustión limpia limitando las emisiones. Y todo ello, sin utilizar ningún sistema de post-tratamiento y garantizando prestaciones extraordinarias.
Los valores excelentes de potencia y par con relación a las dimensiones reducidas y la ausencia de sistemas para reducir las emisiones, como el DPF, se traducen en ventajas para todos los OEM que pueden sustituir sus motores actuales por otros de cilindrada inferior. Al mismo tiempo, y al no tener que ocuparse del proceso de regeneración, pueden reducir consumos y prolongar los intervalos de mantenimiento.
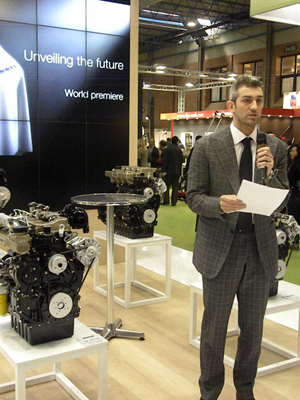
Lo más puntero, desde el punto de vista tecnológico, ha dado como resultado motores con una combustión limpia, gracias a un sistema de inyección Common Rail de alta presión (2000 bar) de última generación. Este último está equipado con la válvula EGR (controlada electrónicamente), para la recirculación de la cantidad correcta de gases de combustión enfriados por líquido a través de un intercambiador agua/aire. Ello permite conseguir la conformidad con los niveles de emisión, a la vez, que prestaciones únicas sin utilizar sistemas de post-tratamiento ‘after-treatment’. El valor añadido del KDI y de las selecciones tecnológicas efectuadas para realizarlo se traducen, para los usuarios finales, en ‘Best Comfort’. En este sentido, se ofrece un motor compacto, robusto, con numerosas prestaciones y bajos niveles de emisión, tanto en términos de vibración como en cuanto al ruido y bajo coste de funcionamiento ‘Low Oprerating Cost’, eficiencia de consumos, uso y mantenimiento.
La ausencia de dispositivos de post-tratamiento aporta numerosas ventajas tanto para el constructor como para el usuario final. Efectivamente, gracias al sistema avanzado de inyección (Common Rail 2000 bar, válvula EGR y cuatro válvulas por cilindro) no es necesario el DPF. La ventaja inmediata que se logra es una mayor envergadura. Los motores KDI están pensados para ser compactos pero con una gran capacidad de prestaciones (potencia, hasta 23 kW/l; y par, hasta 120 Nm/l). La ausencia del proceso de regeneración reduce los consumos de combustible (entre el 3% y el 5%, si se compara con una solución de inyección electrónica de media presión (1.600 bar) más DPF; y más del 10%, si se compara con una solución de inyección directa y DPF autónomo) como también de aceite. En el consumo de aceite también repercute el alisado especial de los cilindros, realizado con maquinaria de última generación que hace posible una reducción de las fricciones, optimiza los consumos y lleva los intervalos de mantenimiento a 500 horas, con una mejora que va desde las 250 horas (comparando KDI con motores actuales no conformes a las normas TIER IV final) hasta las 350 horas (en el caso de consumo de aceite con DPF).