Gemelos digitales en aeroespacial. Nuevas aplicaciones
1. Un marco digital para la evaluación automatizada de factores de riesgo laboral en la fabricación aeroespacial (DI-RISK)
La fabricación aeroespacial es un sector industrial clave de la Unión Europea (UE), no sólo por su enorme volumen económico sino también porque impulsa el crecimiento económico en muchos otros sectores relacionados, uno de los principales líderes en la innovación global, genera empleos altamente cualificados y es sustancial en proporcionando soluciones para los principales desafíos sociales, climáticos y energéticos que enfrentan las sociedades europeas. Las condiciones de trabajo seguras son un requisito previo para una fuerza laboral productiva, una economía fuerte y una sociedad resiliente. Pero a pesar de toda su contribución positiva a la riqueza y la creación de empleo de la UE, el sector de la fabricación aeroespacial sigue siendo un entorno de alto riesgo para sus trabajadores [1].
Los accidentes y lesiones relacionados con el trabajo cuestan a la UE 476 000 millones de euros al año, aproximadamente el 3,3% de su Producto Interior Bruto (PIB) [2]. En los entornos de trabajo de fabricación, los resbalones, caídas y tropezones son las principales causas de accidentes mortales, mientras que las causas más comunes de accidentes no mortales son las lesiones provocadas por la manipulación manual [1], como los TME, es decir, lesiones del Tejidos blandos (por ejemplo, tendones, músculos, ligamentos, articulaciones, nervios, sistema vascular). En particular, los procesos de fabricación aeroespacial plantean un alto riesgo para los trabajadores que desarrollan TMERT debido a los turnos de trabajo irregulares, el esfuerzo físico intenso y las posturas antinaturales prolongadas (por ejemplo, agacharse en las cabinas). Estos riesgos para la salud laboral no sólo tienen un impacto negativo en el bienestar de los trabajadores de la UE, sino que también afectan a las economías de los Estados miembros de la UE. Por ejemplo, en Alemania, los TMERT representaron 17 200 millones de euros de pérdida de producción en 2016 y 30 400 millones de euros de pérdida de valor añadido bruto [3].
Por tanto, es fundamental evaluar el estado de salud y seguridad de los trabajadores de la fabricación de forma regular. Para lograrlo, los expertos médicos (ergonomistas, fisioterapeutas) necesitan sistemas de monitorización de la salud que puedan proporcionar facilidad de uso (practicidad) y precisión para evaluar la cinemática del cuerpo humano. Se han propuesto diversas medidas [1] y herramientas de análisis ergonómico [4] que se basan en datos antropométricos, por ejemplo, ángulos formados entre las principales articulaciones del cuerpo, (véase la Figura 1) para mejorar las condiciones de trabajo, con especial atención a la prevención de los TMERT debido a su asombrosa frecuencia entre diversos oficios y ocupaciones. Sin embargo, estas prácticas son subjetivas, poco fiables entre evaluadores y propensas a errores, ya que se basan en observaciones visuales manuales e inspecciones aleatorias en el lugar de trabajo [5]. En consecuencia, a pesar de que los TMERT y las caídas son los principales peligros entre los oficios de fabricación, el estado actual de la técnica aún no ha logrado ofrecer métodos/herramientas para automatizar la detección y evaluación de los factores asociados a estos riesgos, estando esta laguna de conocimiento estrechamente relacionada con el fracaso de los procedimientos existentes para cumplir con los criterios de monitorización aceptados [6].
![Figura 1. Evaluación rápida de los miembros superiores (Rapid Upper Limb Assessment - RULA) [7] Figura 1. Evaluación rápida de los miembros superiores (Rapid Upper Limb Assessment - RULA) [7]](https://img.interempresas.net/fotos/4750534.jpeg)
La propuesta de investigación que se lleva a cabo actualmente en el CFAA ‘Digital twins for occupational risk assessment of advanced aerospace manufacturing processes (o DI-RISK)’ y financiada por el programa ADAGIO, aborda las preocupaciones del público sobre las evidentes debilidades de los métodos actuales en el monitoreo de los trabajadores y responde a la necesidad urgente de un marco automatizado de evaluación del riesgo de lesiones relacionadas con el trabajo para los procesos de fabricación aeroespacial. Para lograrlo, esta propuesta de investigación desarrolla un marco de evaluación de riesgos de seguridad y salud basado en aprendizaje profundo que tiene como objetivo evaluar los factores de riesgo de las lesiones laborales más frecuentes que afectan a ingenieros o trabajadores aeroespaciales, superando el malestar y la falta de precisión de los métodos existentes.
La mejora de las condiciones de trabajo es una preocupación primordial para la Comisión Europea y ha adoptado el Marco Estratégico de Seguridad y Salud en el Trabajo (SST) de la UE 2021-2027 [8] para promover los más altos estándares en el lugar de trabajo. DI-RISK está estrictamente alineado con el objetivo general de este Marco Estratégico y, en particular, con su segundo objetivo transversal de mejorar la prevención de accidentes y enfermedades relacionadas con el trabajo.
DI-RISK también contribuirá significativamente a reducir la brecha de género en el sector manufacturero, teniendo en cuenta en todos sus algoritmos las diferencias de género en apariencia mediante el uso de datos que consisten tanto en hombres como en mujeres, incluso si esta industria es una industria donde históricamente el ambiente de trabajo presenta una mayor presencia de hombres que de mujeres [9]. Al promover nuevos métodos tecnológicos que garanticen un entorno de trabajo más seguro, DI-RISK también podría aumentar el interés de las mujeres por participar en dichos entornos laborales.
Los objetivos específicos de DI-RISK son: a) diseñar un método y un marco que realizará un monitoreo remoto (sin etiquetas) de ingenieros o trabajadores de fabricación aeroespacial bajo varios desafíos, como variaciones de iluminación y oclusiones, al tiempo que se protege la privacidad, b) desarrollar un método que cree un gemelo digital (réplica) preciso del cuerpo humano para extraer datos antropométricos y biomecánicos, y c) convertir datos antropométricos y biomecánicos en TMERT y factores de riesgo de caídas de forma automatizada.
Para lograr todos los objetivos de investigación perseguidos por el proyecto DI-RISK, se propone un marco interdisciplinario innovador, que implica una combinación ambiciosa de visión por computadora, aprendizaje automático, componentes biomecánicos y ergonómicos. El proyecto DI-RISK procesará de forma innovadora todos aquellos datos en los que se basan las herramientas ergonómicas operativas para lograr dicha evaluación de riesgos. La investigación en visión por computadora sobre la estimación de la postura humana en 3D es bastante extensa, debido a su relevancia para muchos campos de aplicación. Sin embargo, ninguna de estas tecnologías ha logrado alcanzar una alta precisión a la hora de extraer una réplica digital representativa del cuerpo humano (postura 3D), debido principalmente a la limitada información proporcionada por las imágenes 2D. Recientemente, los métodos de aprendizaje profundo se han introducido como una solución prometedora, pero el principal desafío al implementar dichos enfoques sigue siendo el requisito de anotar manualmente en 3D a partir de imágenes 2D, una cantidad extremadamente grande de datos de entrenamiento. El proyecto DI-RISK investigará todas estas tecnologías para ofrecer una herramienta eficiente de evaluación de riesgos.
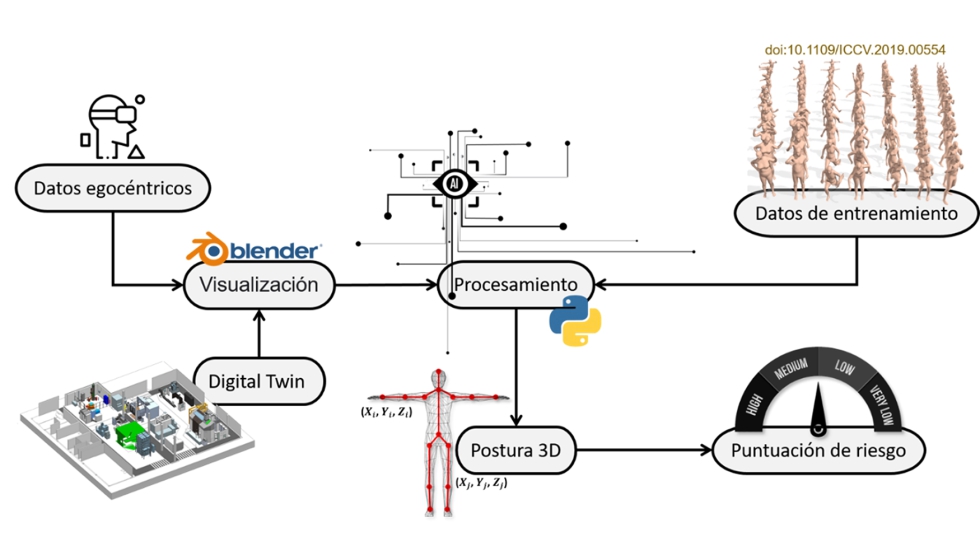
DI-RISK define todos los requisitos específicos de un entorno de monitorización basado en visión remota, haciéndolo más diverso y cercano posible a los entornos de fabricación de la vida real, al tiempo que garantiza la Prevención a través del Diseño (Prevention through Design - PtD) mediante la incorporación de gemelos digitales de las instalaciones de fabricación.
Las actividades de investigación e innovación constan de cuatro pasos científicos básicos. Con más detalle, el paso 1, ‘Detección y configuración remota de la postura’, está dedicado a desarrollar los requisitos necesarios para monitorear sin etiquetas la postura 3D de los trabajadores de fabricación a través de métodos de visión por computadora/aprendizaje automático. El resultado del paso 1 se utiliza luego como entrada en el paso 2 posterior, ‘Estimación de la postura 3D mediante aprendizaje profundo’, que se dedica a desarrollar un algoritmo novedoso basado en el aprendizaje profundo que convierte datos de imágenes 2D en los datos biomecánicos y antropométricos necesarios para extraer la réplica digital del cuerpo humano. La réplica digital del cuerpo humano del paso 2 se utiliza luego como entrada en los pasos 3 ‘Detección y evaluación de factores de riesgo para TMERT’ y 4 ‘Detección y evaluación de factores de riesgo para caídas’ que se dedican a evaluar los factores de riesgo para los trabajadores desarrollar TMERT y caer desde una altura o al mismo nivel. La figura 2 ilustra el diagrama de flujo del método general propuesto.
Bibliografía
[1] European Commission, Causes and circumstances of accidents at work in the EU, (2008). doi:10.2767/39711.
[2] European Agency for Safety and Health at Work (EU-OSHA), Work-related accidents and injuries cost EU €476 billion a year according to new global estimates, Press Release. (2017).
[3] J. De Kok, P. Vroonhof, J. Snijders, G. Roullis, M. Clarke, K. Peereboom, P. van. Dorst, I. Isusi, Work-related musculoskeletal disorders: prevalence, costs and demographics in the EU, Eur. Agency Saf. Heal. Work. (2019). doi:10.2802/66947.
[4] P.N. Kale, R.T. Vyavahare, Ergonomic Analysis Tools: A Review, Int. J. Curr. Eng. Technol. (2016) 1271–1280.
[5] D. Wang, F. Dai, X. Ning, Risk Assessment of Work-Related Musculoskeletal Disorders in Construction: State-of-the-Art Review, J. Civ. Eng. Manag. ASCE. (2015). doi:10.1061/(ASCE)CO.1943-7862.0000979.
[6] E. Konstantinou, J. Lasenby, I. Brilakis, Adaptive computer vision-based 2D tracking of workers in complex environments, Autom. Constr. 103 (2019) 168–184.
[7] C. Maurer-Grubinger, F. Holzgreve, L. Fraeulin, W. Betz, C. Erbe, D. Brueggmann, E.M. Wanke, A. Nienhaus, D.A. Groneberg, D. Ohlendorf. Combining ergonomic risk assessment (Rula) with inertial motion capture technology in dentistry—using the benefits from two worlds, Sensors. 21 (2021) 1–17. doi:10.3390/s21124077.
[8] European Commission, EU strategic framework on health and safety at work 2021-2027. Occupational safety and health in a changing world of work., (2021).
[9] European Construction Sector Observatory, Improving the human capital basis, (2017).
2. Seguimiento a los avances del Proyecto Quolink
El proyecto Quolink, propone un nuevo enfoque para la monitorización intensiva de la producción de aeroturbinas, con el objetivo de alcanzar una evaluación de calidad precisa en la etapa final de fabricación. Para ello, se integra la experiencia de investigadores en áreas clave como la fabricación, la conectividad y la informática, contando con el apoyo del centro CFAA como instalación demostrativa. Quolink se basa en la utilización de datos indirectos obtenidos a través de dispositivos como células de carga, acelerómetros, termopares, CNC, PLC, motores eléctricos y accionamientos; aprovechando la computación perimetral para su procesamiento. Estos datos se almacenan en una base de datos estructurada y se analizan mediante modelos numéricos que correlacionan los parámetros de entrada con el resultado del proceso y la calidad del producto.
La inteligencia artificial se emplea para desarrollar herramientas que detectan problemas con antelación, mejorando la eficiencia y reduciendo los costes. El proyecto se centra en el brochado de alta velocidad de ranuras de firtree, una operación crítica en la fabricación de motores aeronáuticos, y en el mecanizado de carcasas y procesos no convencionales como el EDM.
Las tecnologías clave habilitadoras de 5G, como NFV y SDN, permiten la monitorización remota segura y flexible, posibilitando aplicaciones industriales de alto valor añadido. La principal innovación del proyecto radica en la vinculación de los datos de entrada con la calidad final del producto, buscando una Fabricación de Defecto Cero (ZDM) que optimice los procesos y reduzca el impacto ambiental.
Para su ejecución, se planeó avanzar en el cumplimiento de cinco objetivos:
- Objetivo 1: medir y estimar las variables del proceso cerca del punto de procesamiento.
- Objetivo 2: medir/estimar la calidad del producto en proceso mediante gemelos digitales.
- Objetivo 3: garantizar la confiabilidad de los datos para optimizar la toma de decisiones y mejorar los procesos de fabricación.
- Objetivo 4: optimizar la calidad del producto basado en inteligencia artificial para la fabricación de cero defectos, detectando los problemas de calidad en una etapa temprana e introduciendo acciones correctivas en el proceso.
- Objetivo 5: demostrar y validar el concepto y las soluciones del proyecto.
Para conseguir el Objetivo 1, el proyecto inició con un estudio exhaustivo de las máquinas disponibles, evaluando la criticidad de sus operaciones y el estado actual de la tecnología y la literatura científica relacionada con los procesos allí realizados. A partir de este análisis, se definieron variables clave para una monitorización precisa del proceso, tomando como base las variables disponibles, el conocimiento previo y la revisión de la literatura científica.
Una vez establecidos estos parámetros, se abordó la extracción de información de las máquinas. Se analizaron los protocolos de comunicación disponibles en cada máquina y se identificaron herramientas de código abierto para acceder a sus datos. Con el objetivo de facilitar la replicabilidad para otros usuarios, se diseñó una infraestructura de conexión, lectura y almacenamiento de datos basada en herramientas de software de código abierto. Esta infraestructura se implementó en una red experimental 5G Smart Networks for Industry (SN4I) diseñada y desplegada por el grupo de investigación i2t de la UPV/EHU, donde se alojan las máquinas virtuales que albergan los softwares. La red 5G proporciona mayor seguridad, velocidad de transmisión de datos y servitización de recursos, permitiendo una monitorización continua durante el uso de las máquinas.
Por otro lado, se definieron sensores virtuales a partir de la información disponible, con el objetivo de monitorizar parámetros críticos del proceso en tiempo real. Un ejemplo de estos sensores virtuales es el que se utiliza para determinar el estado de la herramienta de corte en el proceso de brochado, mediante el análisis de datos del proceso. Adicionalmente, se diseñaron y definieron gemelos digitales de la máquina y el proceso. Estos gemelos digitales permiten identificar desviaciones en el proceso y predecir la necesidad de mantenimiento preventivo o correctivo, basándose en el estado de la máquina.
Con relación al cumplimiento del Objetivo 2 del proyecto, y tras la fase de estudio del proceso y la definición de los sensores virtuales, se llevó a cabo una serie de ensayos, utilizando como ejemplo el proceso de brochado. El objetivo de estos ensayos era detectar el desgaste prematuro de las herramientas de brochado, un aspecto crítico dado que la infraestructura de la máquina dificulta y alarga la evaluación manual del estado de las herramientas. Adicionalmente, se determinó la influencia de las características de los bordes de las herramientas en las fuerzas y temperaturas generadas durante el proceso, y su impacto en la calidad final de la pieza.
Adicionalmente, se implementaron dos gemelos digitales para los procesos estudiados:
- Gemelo digital para brochado: este gemelo digital permite analizar los datos del proceso para identificar alteraciones como rotura de herramientas o desgaste excesivo en la herramienta de corte.
- Gemelo digital para centro de mecanizado: este gemelo digital utiliza un ‘fingerprint’ y la monitorización continua de las variables definidas previamente para predecir cuándo la máquina está o va a operar de forma errónea.
En cuanto al desarrollo del Objetivo 3, y para garantizar la confiabilidad de la información recolectada, se diseñaron pruebas rigurosas que abarcan diversos aspectos:
- Validación manual: se realizaron pruebas manuales para detectar anomalías como valores atípicos o lecturas incorrectas. Estas pruebas garantizan la precisión y coherencia de los datos a simple vista.
- Validación cruzada: se compararon datos de múltiples fuentes sobre el mismo proceso para asegurar la consistencia interna. Esta validación cruzada verifica la confiabilidad de los datos desde diferentes perspectivas.
- Verificación de protocolos de comunicación: se realizaron pruebas para verificar la correcta lectura de valores a través de protocolos como OPC-UA, Modbus y S7. Estas pruebas garantizan la integridad de la información durante la transmisión.
- Validación de la infraestructura: se plantearon ejercicios para contrastar los datos con la fuente original, asegurando su correcta llegada a la infraestructura de análisis y almacenamiento. Se implementaron estrategias de replicación de datos (Hadoop HDFS) para evitar la pérdida de información en los nodos.
- Evaluación del rendimiento: se diseñaron pruebas para determinar la cantidad y frecuencia óptimas de lectura de variables, analizando los requisitos de cómputo necesarios. Estas pruebas permiten optimizar la eficiencia del sistema de adquisición de datos.
En cuanto al Objetivo 4, y a partir de la información recolectada y los sensores virtuales desplegados, se han desarrollado diversas aplicaciones con un alto impacto en la industria:
- Detección temprana de desgaste de herramientas de brochado: se emplean señales eléctricas de la máquina para monitorizar el movimiento y la fuerza ejercida durante el brochado. Se realizan mediciones del desgaste de la herramienta mediante un dispositivo diseñado en el CFAA, sin necesidad de desmontarla. El análisis de imágenes con técnicas de visión por computador y las señales eléctricas permiten desarrollar un modelo para la detección temprana del desgaste de las herramientas.
- Detección automática de ‘outliers’ en centros de mecanizado usando sistemas de visión artificial: se implementa un sistema de visión artificial para estimar automáticamente el desgaste de la herramienta de brochado. Esta tecnología permite evaluar el desgaste bajo diferentes condiciones de mecanizado, facilitando la toma de decisiones sobre el reemplazo de la herramienta. La detección precisa del desgaste previene roturas catastróficas de la herramienta y garantiza la calidad de las piezas mecanizadas.
Y finalmente, con respecto al Objetivo 5, se propuso un método de monitorización para un brochado eficiente combinando la monitorización en tiempo real y la inspección del desgaste de herramientas fuera de línea. En primer lugar, se definieron las características de la herramienta de corte y las afectadas por la degradación de esta. Posteriormente se llevaron a cabo algunos ensayos de ciclos de brochado midiendo aceleraciones del proceso, fuerza de corte a través del uso de células de carga, y el consumo de los accionamientos del motor. Estableciendo la sensibilidad entre el desgaste de la herramienta y las frecuencias naturales del proceso de brochado. Por otro lado, se realizó una investigación sobre el proceso de preparación de filos de corte mediante arrastre (DF) en herramientas de carburo, evaluando dos tamaños de grano y tres proporciones de mezcla, variando la profundidad de inmersión de la herramienta en el abrasivo y el tiempo de arrastre. Con el estudio se demostró la viabilidad y confiabilidad del método DF para la preparación de filos de corte en herramientas de carburo. Su precisión y capacidad de predicción lo convierten en una alternativa atractiva a los métodos tradicionales.
Gracias a todos estos desarrollos, el proyecto nos ha permitido realizar algunas publicaciones tanto en Revistas del alto impacto como en Congresos científicos:
- Tapia, E., Sastoque-Pinilla, L., Lopez-Novoa, U., Bediaga, I., & López de Lacalle, N. (2023). Assessing industrial communication protocols to bridge the gap between machine tools and software monitoring. Sensors, 23(12), 5694.
- Villarrazo, N., Martínez de Pissón, G., Fernandez, P., Pereira, O., & López de Lacalle, L. N. (2023). Titanium blade milling with minimum piece deformation based on tool orientation. MM Science Journal.
- Pérez-Salinas, C., López de Lacalle, L. N., Fernández-Lucio, P., Gómez-Escudero, G., & Del Olmo, A. (2023). The effect of broaching tool cutting edges polishing on process forces and temperature. MM Science Journal.
- Pérez-Salinas, C. F., Del Olmo, A., & López de Lacalle, L. N. (2022). Estimation of drag finishing abrasive effect for cutting edge preparation in broaching tool. Materials, 15(15), 5135.
- Tapia, E., Lopez-Novoa, U., Sastoque-Pinilla, L., & López-de-Lacalle, L. N. (2024). Implementation of a scalable platform for real-time monitoring of machine tools. Computers in Industry, 155, 104065.
- Aldekoa, I., del Olmo, A., Sastoque-Pinilla, L., Sendino-Mouliet, S., Lopez-Novoa, U., & de Lacalle, L. N. L. (2023). Early detection of tool wear in electromechanical broaching machines by monitoring main stroke servomotors. Mechanical Systems and Signal Processing, 204, 110773.
- Holgado, I., Pérez-Salinas, C., Ortega, N., de Lacalle, L. L., & del Olmo, A. (2022, November). An intelligent machine learning based method for tool wear estimation in the vertical broaching process. In Ibero-American Congress of Mechanical Engineering (pp. 306-312). Cham: Springer International Publishing.
- Del Olmo, A., De Lacalle, L. L., De Pissón, G. M., Pérez-Salinas, C., Ealo, J. A., Sastoque, L., & Fernandes, M. H. (2022). Tool wear monitoring of high-speed broaching process with carbide tools to reduce production errors. Mechanical Systems and Signal Processing, 172, 109003.
- Pérez Salinas, C., López de Lacalle, L. N., Fernández Lucio, P., & Pereira Neto, O. (2022). Tratamiento de filos de corte por arrastre planetario ‘Dragging’ y predicción de redondeo de filo en herramientas de carburo.
- Pérez-Salinas, C., de Lacalle, L. L., Fernández-Lucio, P., & Pereira-Neto, O. (2022, November). Planetary Dragging Cutting Edge Treatment and Edge Rounding Prediction on Carbide Tools. In Ibero-American Congress of Mechanical Engineering (pp. 293-299). Cham: Springer International Publishing.
Sin embargo, aún queda pendiente la ejecución de algunas tareas definidas en el proyecto, por lo que su ejecución se prorrogará hasta el primer semestre del 2025.