Electrónica flexible impresa para ayudar a las misiones espaciales a perder peso
La capacidad de integrar placas de circuito impreso y conjuntos electrónicos directamente en mecanismos y estructuras gracias a las tecnologías de impresión y termoconformado abre un abanico de posibilidades en diferentes sectores, como el de electrodomésticos o la automoción, en los que ha comenzado a extenderse su uso para el panel de instrumentos de los coches, por ejemplo.
Estas nuevas soluciones están cambiando rápidamente la manera en la que se fabrican e integran las funcionalidades electrónicas en cualquier tipo de instrumento o componente, y son las que se probarán por primera vez en Europa para aplicaciones espaciales en un nuevo proyecto financiado por la Agencia Espacial Europea (ESA) liderado por el centro tecnológico vasco Tekniker.
El principal reto de la iniciativa Printed Structural Electronics (SIPRES) será desarrollar, fabricar y validar el uso de la electrónica flexible, impresa e hibrida con diferentes prototipos que sean capaces de operar correctamente en las condiciones extremas de temperatura, vacío y radiación que exigen las misiones de exploración e investigación espacial.
“Este proyecto es innovador porque marca la primera vez que la ESA experimentará con la aplicación de sistemas electrónicos impresos en materiales flexibles para su uso en el espacio”, explica Borja Pozo, coordinador del Sector Espacial de Tekniker.
“El peso de los dispositivos y elementos que se envían el espacio es un factor clave y determinante para el éxito de las misiones espaciales. Esta tecnología, gracias al menor uso de material y su peso reducido, puede permitir abaratar los costes de las futuras misiones y que sean más sostenibles. Abre la puerta a integrar las capacidades electrónicas más fácilmente en múltiples componentes y superficies independientemente de su forma”, añade el experto.
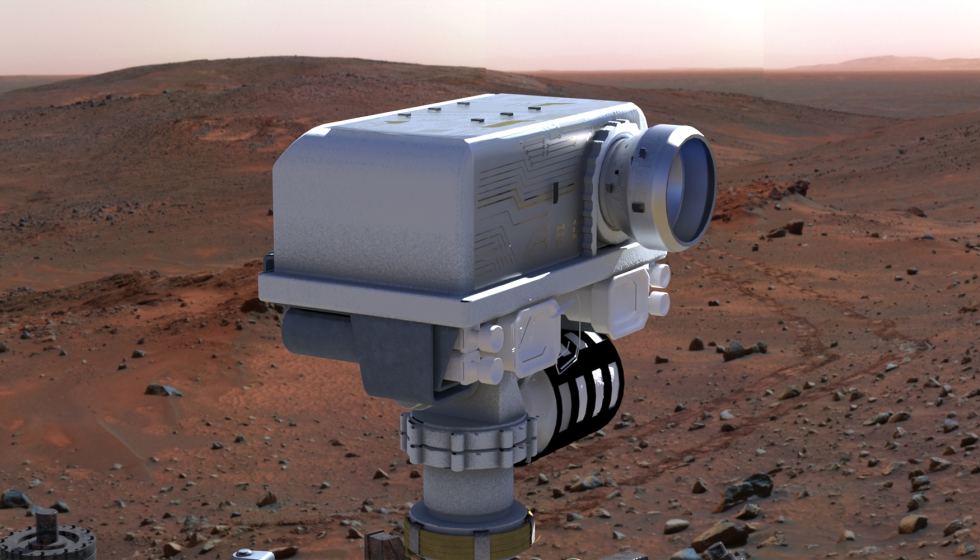
Puesta a punto de prototipos
Tekniker contribuirá con su conocimiento y experiencia en electrónica, fabricación, química de superficies y tecnologías de recubrimientos en toda la puesta a punto de los prototipos, desde su fase de concepción hasta un desarrollo tecnológico más próximo a su introducción en el sector espacial.
En el proceso también participarán las ingenierías Alter Techonology y CT Ingenieros - Cadtech e incluirá la prueba y validación de diferentes materiales poliméricos, tintas y adhesivos conductores y procesos de fabricación para resolver su compatibilidad con las condiciones ambientales requeridas y los componentes electrónicos espaciales.
La impresión de los dispositivos y conjuntos electrónicos se llevará a cabo en el laboratorio de impresión 3D de Tekniker.
Una vez desarrollados, testeados y validados, los primeros demostradores tecnológicos podrían implementarse con plataformas nanosatélites empleadas habitualmente para la investigación en órbita terrestre baja (LEO) o en la verificación de la campaña de pruebas de la Estación Espacial Internacional (ISS).
Paralelamente, basándose en la hoja de ruta establecida por la ESA, se podría considerar la aplicación de los prototipos finales para futuras misiones a la Luna y Marte. “Entre las posibles soluciones que se podrán desarrollar con esta tecnología se encuentran la integración de sensores de viento y humedad para ‘rovers’ marcianos; sensores de radiación, temperatura y fotodetectores para la Luna; sensores de fuerza para mecanismos de naves espaciales, o sistemas energéticos solares y térmicos para pequeños satélites de baja órbita”, añade el experto de Tekniker.
Estas soluciones también abren posibilidades para la supervisión de telemetría en línea, esto es, para el monitoreo y transmisión de datos en tiempo real de forma remota.
La iniciativa SIPRES, que comenzará este mes de octubre y tendrá una duración de dos años, está financiada por la ESA en el marco de su programa de desarrollo tecnológico TDE. Tekniker ha colaborado y colabora con la ESA a través de diferentes proyectos, destinados, entre otros, a testar los efectos del ambiente espacial en los materiales o investigar nuevas maneras de generar combustible para las misiones espaciales.
Esta innovadora técnica integra dispositivos y conjuntos electrónicos mediante procesos de impresión y ya se utiliza en sectores como la automoción. Permitiría reducir el peso, coste y tiempo de fabricación de sistemas para las futuras misiones