Recubrimientos de ZnNi como alternativa al Cd en el sector aeronáutico
El proyecto H2Free, liderado por Cidetec Surface Engineering, persigue el desarrollo de nuevas reglas de desgasificación basadas en modelos multi-físicos validados experimentalmente. Estos modelos permitirán la definición de tratamientos térmicos específicos con el objetivo de disminuir el tiempo de desgasificación, lo que conducirá a un ahorro de costes y a una reducción del impacto medioambiental.
Los aceros de ultra-alta resistencia (UHSS por sus siglas en inglés) destacan por sus extraordinarias propiedades mecánicas y su bajo peso, características que convierten a este material en la opción preferida para las aplicaciones industriales donde se requieran altas solicitaciones mecánicas durante la vida en servicio del componente. Por ejemplo, el empleo de este material es fundamental para el sector aeronáutico, donde esta combinación de características hace que el uso de los aceros UHSS permita, por un lado, soportar las inmensas cargas mecánicas que sufren los trenes de aterrizaje sin que ello suponga un fuerte incremento de peso y, por lo tanto, un mayor consumo de combustible y la correspondiente generación de CO2.
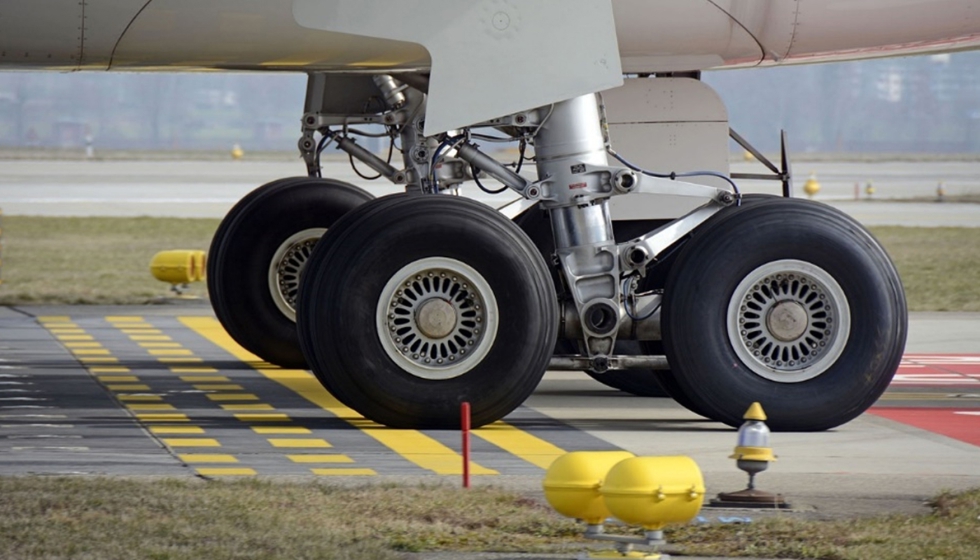
Sin embargo, a pesar de sus excelentes prestaciones mecánicas, este tipo de aceros presentan una limitada resistencia a la corrosión, lo que obliga a su protección para evitar su degradación en servicio como consecuencia de las condiciones ambientales a las que se ven sometidos. La electrodeposición es una de las tecnologías más empleadas para la aplicación de recubrimientos metálicos sobre la superficie de los UHSS aportándoles, entre otras características, una excelente resistencia a la corrosión sin alterar sus propiedades mecánicas.
Históricamente, el cadmio (Cd) se ha utilizado para mejorar la resistencia a la corrosión de una amplia gama de materiales con impacto en un gran número de aplicaciones industriales. Se trata de un recubrimiento de sacrificio, ya que su potencial de corrosión es más negativo que el del acero, provocando que, si se daña el recubrimiento, la capa de Cd se corroa preferencialmente, evitando que la corrosión llegue al material base. Aunque el Cd se ha utilizado durante muchos años en diversos sectores industriales (ej. aeronáutica) para la protección de aceros de alta y ultra alta resistencia, su naturaleza carcinógena y tóxica ha llevado a su inclusión en el anexo XIV del reglamento REACH, motivando la búsqueda de alternativas por parte de la industria. A pesar de que existen una gran cantidad de metales susceptibles de ser aplicados mediante esta tecnología, no todos pueden ser aplicados sobre aceros UHSS. Así, mientras que para los aceros al carbono de baja resistencia o los aceros de baja aleación existen diversas posibilidades de sustitución del cadmio, para los aceros de alta resistencia hay muchas menos opciones debido a la alta susceptibilidad que estos presentan a la fragilización por hidrógeno (HE por sus siglas en inglés).
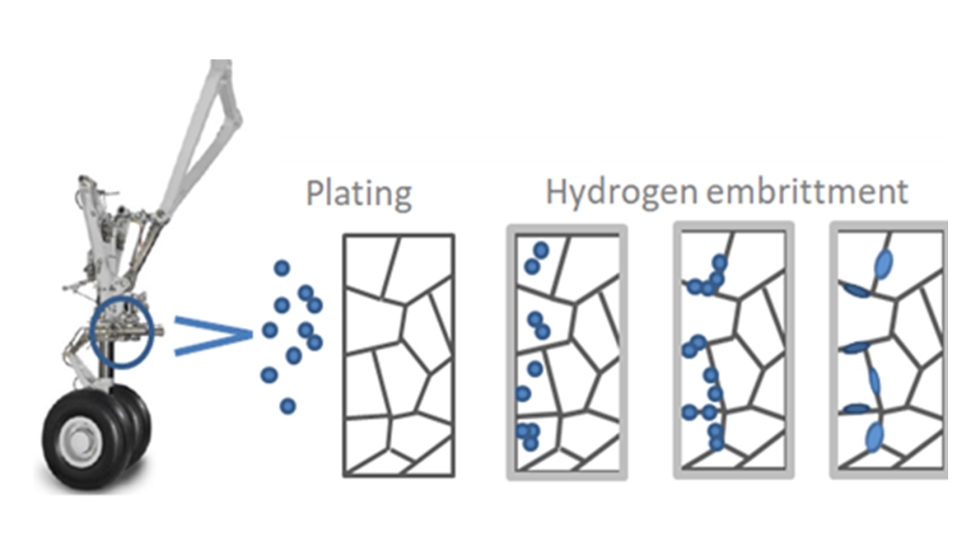
En este sentido, los recubrimientos de ZnNi han emergido como la alternativa más viable a los recubrimientos de Cd ya que permiten superar incluso su resistencia a la corrosión, llegando a proveer a los materiales de una resistencia a la corrosión de hasta 3.000 h en cámara de niebla salina neutra (ASTM B-117). La investigación de alternativas se ha realizado sobre la base de recubrimientos de Zn, investigando el efecto en las propiedades de los recubrimientos derivados de la adición de pequeñas cantidades de otros elementos, como Mn, Fe, Co, Sn y Ni, ya que es conocido que la adición de aleantes tiene un impacto directo en la resistencia a la corrosión del recubrimiento. Las aleaciones en base Zn conservan su comportamiento anódico respecto al acero, manteniendo la protección de sacrificio, pero con una menor velocidad de corrosión, lo cual alarga su protección anticorrosiva. En este sentido, la electrodeposición de recubrimientos de Zn-Ni proporciona una resistencia óptima a la corrosión cuando la aleación presenta un contenido en Ni entre 12-15% en peso. No obstante, un menor contenido de Ni en la aleación reduce las propiedades barrera y aumenta la velocidad de corrosión. Por el contrario, con un mayor contenido de Ni, superior a 25-30% en peso, el recubrimiento deja de actuar como capa de sacrificio con respecto al sustrato de acero y la resistencia a la corrosión disminuye. A pesar del desarrollo de nuevos electrolitos capaces de generar menos H durante el proceso, conocidos como LHE, este sigue siendo uno de los principales problemas relacionados con la aplicación de recubrimientos de ZnNi sobre UHSS.
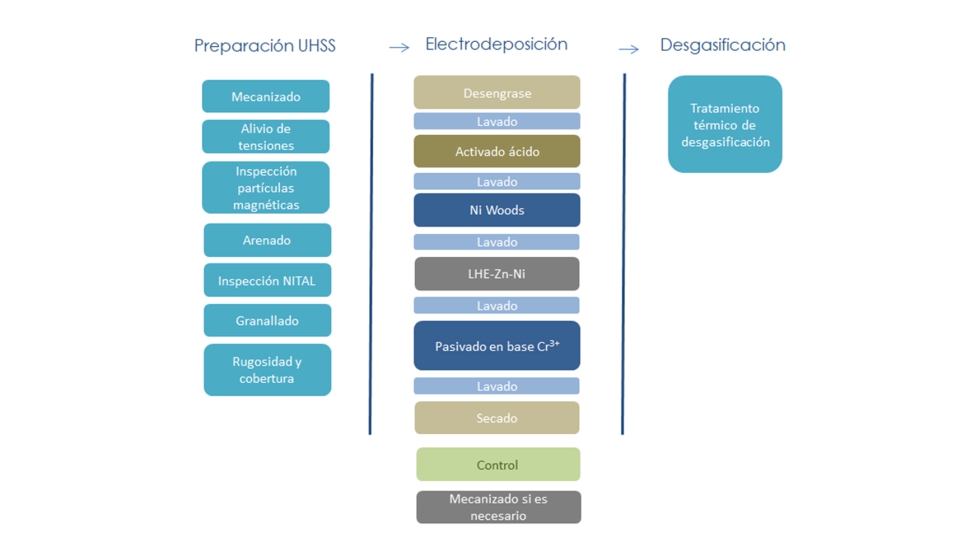
Durante el proceso de electrodeposición se genera hidrógeno (H) como reacción secundaria. Este H se incorpora al recubrimiento durante el crecimiento de la capa metálica y es susceptible de migrar al material base, favoreciendo la fragilización por hidrógeno. Este fenómeno es una amenaza directa a la funcionalidad y durabilidad de los materiales y se define como la diminución de la capacidad de carga mecánica de los materiales, o bien, su fractura, por debajo de su límite elástico. Los daños producidos por la adsorción de hidrógeno por parte de los materiales son un tipo de degradación debido a la acción combinada de la presencia de H y esfuerzo mecánico, bien sea este último residual en el material o aplicado sobre el componente de interés. El daño generado por la presencia de H en los materiales puede manifestarse de diversas formas como por ejemplo mediante ataque por hidrógeno, agrietamiento, ampollamiento, formación de hidruros, pérdida de ductilidad y micro perforación, entre otros. Todos estos modos de fallo se engloban dentro del paraguas de la fragilización por hidrógeno (HE). Para moderar el riesgo de HE en los materiales sobre los que se aplica un recubrimiento metálico, estos se someten a un proceso de desgasificación mediante un tratamiento térmico, a temperatura moderada y por largos periodos de tiempo, con el objetivo de que el H presente en el material base difunda al exterior, eliminando el riesgo de HE. Sin embargo, la eficiencia del proceso de desgasificación depende de muchos factores lo que provoca la aplicación de tratamientos térmicos universales y garantistas para reducir el riesgo de fragilización.
La cantidad de H generado durante el proceso dependen directamente de las condiciones de trabajo del electrolito. Así, factores como la densidad de corriente aplicada, la temperatura, el pH, el área recubierta durante el proceso, entre otros, tienen un impacto directo en la generación de H durante el proceso y, por tanto, en la susceptibilidad del material al HE. Una vez generado el H durante el proceso de electrodeposición, este puede difundir al interior del material base. Los recubrimientos de ZnNi presentan una difusividad de H un 80% inferior a la del acero, sin embargo, la permeabilidad al H depende en gran medida tanto de la microestructura como de la morfología del depósito, que como se ha comentado anteriormente, están directamente relacionadas con las variables de proceso. Esto está también relacionado con la capacidad de efusión del H generado durante la etapa de desgasificación, donde el recubrimiento de ZnNi juega un papel importante. Además, durante el propio proceso de deposición sobre componentes reales de geometría compleja, debido a la irregular distribución de corriente sobre la pieza, se generan diferentes morfologías de depósito, las cuales afectarán al proceso de desgasificación. Actualmente no existen métodos que permitan evaluar la eficiencia del proceso de desgasificación de los componentes recubiertos en el ámbito industrial lo que provoca el rechazo de las piezas sospechosas, aumentando el tiempo y coste de producción de este tipo de componentes clave. Es por ello, que la industria aeronáutica demanda nuevas herramientas que permitan eliminar la incertidumbre del proceso de desgasificación aplicado a los componentes críticos fabricados con aceros UHSS.
En los últimos años, Cidetec Surface Engineering se ha dotado de instalaciones y equipamiento singular para abordar la aplicación y caracterización de recubrimientos metálicos en diversos ámbitos, entre los que destacan aquellos enfocados al sector aeronáutico y sus problemáticas actuales, incluyendo la HE. Las capacidades de CIDETEC Surface Engineering le permiten cubrir toda la cadena de desarrollo y control de procesos, incluso para elementos tan difíciles de monitorizar como el H, desde los estadios iniciales de la investigación a escala de laboratorio hasta su potencial implantación industrial. En este sentido, CIDETEC Surface Engineering lidera el proyecto H2Free: Investigation and modelling of hydrogen effusion in electrochemically plated ultra-high-strength-steels for landing gears, financiado por la Unión Europea en el marco de la convocatoria Clean Sky2. H2Free está formado por un consorcio europeo multidisciplinar compuesto, además de por CIDETEC Suface Engineering, por LIEBHERR Lindenberg, Azterlan, Elhco S.A, Hereon, Elsyca y el Max-Planck-Institut für Eisenforschung GmbH. El objetivo del proyecto H2Free es el desarrollo de nuevas guías prácticas para la desgasificación de aceros UHSS recubiertos con procesos LHE, tanto de Cd como de ZnNi, con el objetivo de reducir el tiempo y los costes asociados al proceso productivo, así como la minimización de su impacto medioambiental al reducir el rechazo mediante la adecuación de la etapa de desgasificación en base al material base y el recubrimiento aplicado. Todo lo anterior permitirá a los recubrimientos de ZnNi superar las prestaciones ofrecidas por el Cd. Además, estas guías proporcionarán reglas simples de desgasificación, basadas en datos experimentales y modelado, para predecir en aceros UHSS recubiertos con diferentes morfologías de depósitos metálicos la efusión de H, el H retenido tras el proceso de desgasificación y la susceptibilidad de los materiales tratados frente al fenómeno de fragilización (HE).
El proyecto H2Free, que se encuentra en sus últimos meses de ejecución, ha abordado la deposición de recubrimientos LHE, tanto de ZnNi como de Cd, sobre diferentes UHSS ya que el proyecto contempla el desarrollo de las nuevas guías de desgasificación para 4 tipos de UHSS entre los que se incluyen los aceros de referencia 300M, E35NCD16H, EZ2NKD18 y CUSTOM 465. En el marco del proyecto, Cidetec Surface Engineering ha investigado y optimizado las condiciones de aplicación de los recubrimientos de ZnNi y Cd que dan lugar a depósitos con distinta morfología, con el objetivo de estudiar su influencia en el proceso de desgasificación. Concretamente, tras los estudios iniciales se definieron 3 morfologías objetivo denominadas compacta, semi-abierta y abierta. En el proyecto se han estudiado y definido las condiciones para obtener, en todos los materiales, los recubrimientos de ZnNi y Cd con las mismas morfologías objetivo, lo que ha requerido de una extensa y minuciosa investigación adaptada a la naturaleza y condiciones del proceso requeridas para cada uno de los materiales.
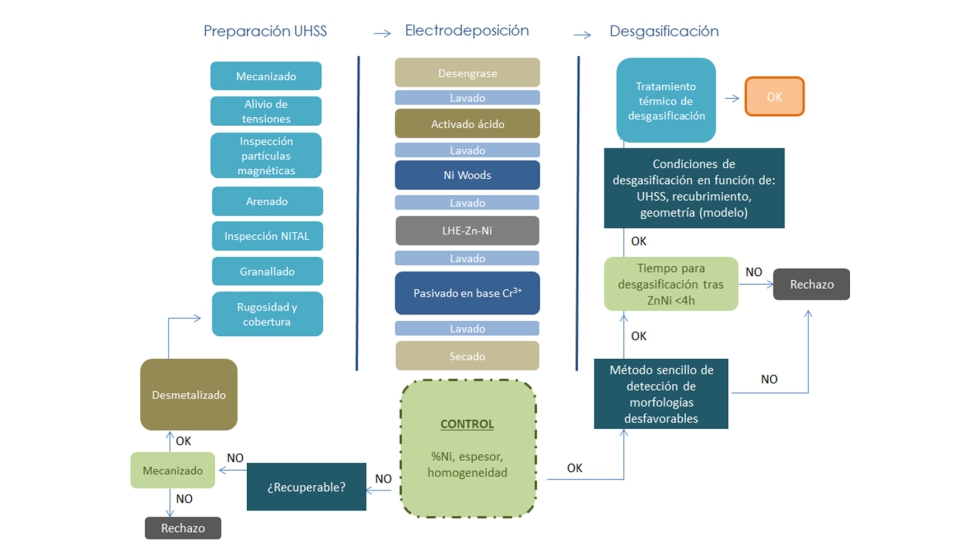
Los recubrimientos generados, han permitido abordar la definición de los coeficientes de difusión del H tanto para el recubrimiento en sí mismo, como para cada una de las morfologías objetivo, así como para los diferentes aceros involucrados en el estudio. En paralelo con esta investigación, se determinaron las cinéticas de desgasificación de los diferentes materiales recubiertos con ZnNi, estudiando tanto el contenido inicial de H tras la aplicación del recubrimiento en cada una de las morfologías, como tras el tratamiento de desgasificación a 2 temperaturas diferentes, evaluando en todos los casos el H remanente tras 12 y 24 horas de desgasificación. La generación de estos datos ha permitido alimentar los modelos para la predicción de la carga y efusión del H generado durante el proceso de electrodeposición y la posterior desgasificación. Estos modelos han sido integrados en un software comercial de simulación de procesos de electrodeposición, dotándolo así de una interfaz adecuada. Actualmente, el proyecto H2Free se encuentra en su fase de validación. Los resultados ya obtenidos para el acero 300M y E35NCD16H han permitido verificar que los modelos desarrollados son capaces de predecir de forma satisfactoria el contenido de H de cada una de las morfologías objetivas en estos aceros, junto con el espesor y la composición del recubrimiento en función de las condiciones de aplicación del recubrimiento a escala laboratorio. Actualmente, se están realizando los ensayos de validación sobre componentes reales del sector aeronáutico los cuales permitirán evaluar los modelos desarrollados sobre piezas de mayor tamaño y geometría compleja en condiciones industriales y poder así validar los desarrollos alcanzados durante el proyecto.
Cidetec Surface Engineering continúa apostando por el desarrollo de nuevos recubrimientos metálicos, como alternativa a los procesos convencionales, a partir de la generación de conocimiento de vanguardia que abarque toda la cadena de desarrollo, permitiendo mejorar las prestaciones funcionales de los componentes sobre los que se apliquen.
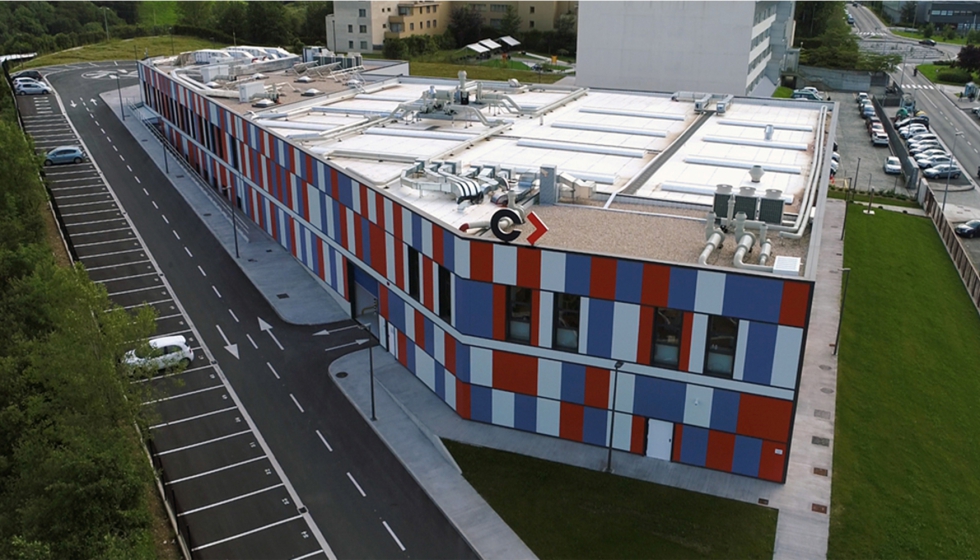