Acabado mecánico por corriente para el desbarbado y redondeo de discos de turbina
En particular, las superficies de presión con las que las raíces de las cuchillas y los discos están en contacto durante el funcionamiento están sujetas a tolerancias muy estrechas, de 10 a 20 µm. Para que las cuchillas queden perfectamente posicionadas, es esencial que las superficies de presión no varíen de forma durante el desbarbado y el redondeo.
Los procesos robóticos no son la mejor opción
La práctica estándar de ingeniería para este paso del proceso es el desbarbado y redondeo mecánico, semirrobótico, con muelas o cepillos. Estas herramientas se desgastan con el tiempo, produciendo resultados de mecanizado inconsistentes a lo largo de su vida útil. Por ejemplo, los bordes afilados pueden cortar las puntas de los cepillos, lo que hace que el desgaste de los cepillos sea difícil de predecir y, por lo tanto, produce resultados variables, así como una gran contaminación del proceso debido a los residuos de los cepillos. Del mismo modo, las muelas están sujetas a una remoción desigual del material, que los movimientos del robot tienen que compensar, y la abrasión provoca la contaminación del proceso.
En las geometrías complejas de las piezas, los resultados del redondeo suelen ser asimétricos porque las muelas o los cepillos no pueden ajustarse a la geometría exacta de la ranura del abeto, o porque no pueden llegar a las zonas de difícil acceso. Estos resultados de redondeo asimétricos e incoherentes no suelen cumplir las tolerancias, provocan variaciones de forma y, por tanto, aumentan tanto la tasa de rechazos como los costes.
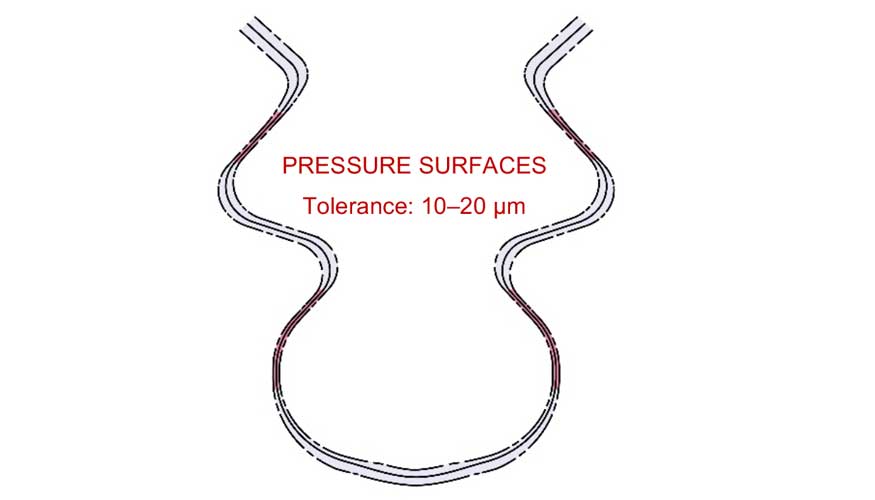
Comparación con procesos alternativos
En la búsqueda de un proceso alternativo con resultados de acabado convincentes, un fabricante de motores trabajó con Otec para evaluar dos tecnologías diferentes de acabado en masa. El primer proceso, en una cubeta vibratoria redonda, resultó ser inadecuado para la aplicación: incluso después de varias horas de procesamiento, fue incapaz de situar todas las roturas de bordes dentro del rango de tolerancia. El redondeo producido en las pruebas no era ni simétrico ni repetible. Además, el aumento del nivel de ruido y las vibraciones asociadas constituyeron un problema, dado que se utilizan dispositivos de medición sensibles en las proximidades.
En el segundo proceso, en la máquina de acabado de chorro de Otec, se obtuvieron rápidamente resultados muy prometedores en el primer intento. Posicionando el componente con precisión, todas las roturas de bordes estaban dentro de la tolerancia en sólo 15 minutos, con un redondeo muy simétrico a lo largo de todo el borde. Otras ejecuciones confirmaron que el proceso era repetible y estable. La variación de la forma fue inferior a 1 µm, tan baja que no fue necesario ni un solo ajuste en el brochado anterior. Por último, el proceso, poco ruidoso y con pocas vibraciones, era adecuado para utilizarlo cerca de dispositivos de medición sensibles.
Ventajas que ya han convencido a diversos fabricantes de motores
- Tiempo de proceso mínimo de sólo 15 minutos
- Redondeo altamente simétrico y uniforme
- Resultados de proceso fiables y repetibles
- Eliminación de rebabas sin residuos
- Variación mínima de la forma en las superficies de presión de las ranuras sin abeto
- Cumplimiento fiable y medible con tolerancias estrechas de menos de 1 µm
- Eliminación de material puramente mecánica, sin el uso de un proceso químico
- Acelerante
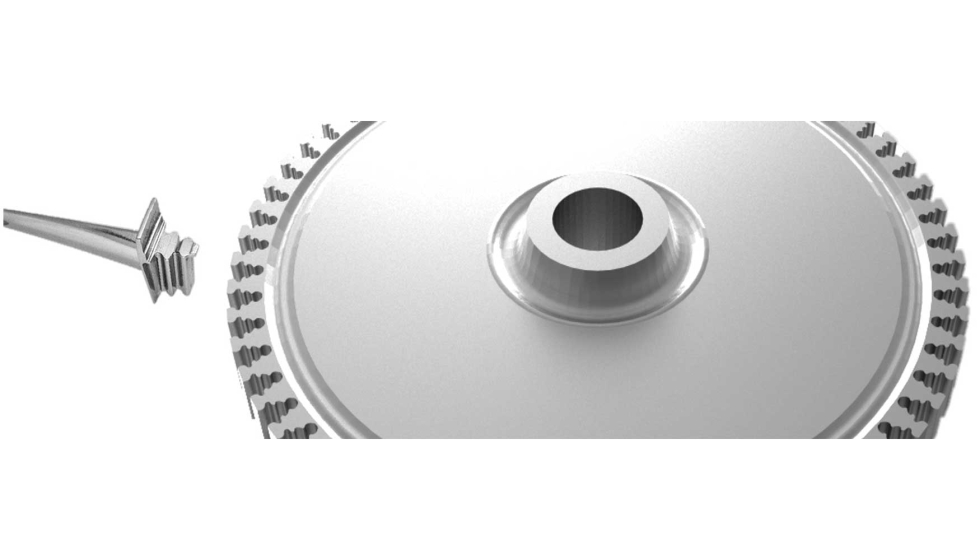
Funcionamiento del acabado por corriente
En el acabado mecánico por corriente desarrollado por Otec, los componentes, como los discos de turbina y los álabes de turbina o compresor, se sujetan en un soporte y se sumergen en un recipiente giratorio lleno de un medio abrasivo o de pulido (medio). Las piezas también pueden girar o colocarse en ángulos específicos en el flujo del medio.
El movimiento relativo entre la pieza y el medio produce un acabado uniforme. Las enormes fuerzas de mecanizado de hasta 9 toneladas que se utilizan en el acabado de corrientes pueden eliminar el material con mayor rapidez y precisión que cualquier otro tipo de proceso de acabado de superficies: dependiendo del tamaño del componente, el estado inicial y la preparación (por ejemplo, el biselado previo) pueden producir un radio de hasta 700 µm en 15 minutos. Y como los gránulos de material son tan finos, el proceso de redondeo también es adecuado para geometrías complejas y de difícil acceso.
Otec, como proveedor de máquinas de acabado de chorro con automatización integrada para componentes grandes y pesados, ha desarrollado recientemente el modelo SF-HP, una máquina adecuada para piezas de hasta 650 mm de diámetro y un peso de hasta 200 kg.
La tecnología de acabado de corrientes de Otec es la opción ideal para componentes con requisitos de posprocesamiento igualmente exigentes. Algunos ejemplos son los álabes de turbinas y compresores, las raíces de los álabes de las turbinas, los blisks, las servoválvulas, las ruedas dentadas, las tuercas de los husillos de bolas y los componentes de los trenes de aterrizaje.