Los recubrimientos PVD con base de carbono amplían la vida útil de los componentes de precisión sometidos a cargas elevadas
Toby Middlemiss, jJefe del segmento de Aeroespacio y Defensa de Oerlikon Balzers
06/05/2020Los ingenieros de productos y los fabricantes de componentes suelen recurrir a recubrimientos especializados PVD (deposición física mediante vapor) que pueden aplicarse en espesores de 0,5 a 15 micrómetros (μm) para endurecer aún más la superficie de estas piezas.
Al aplicar recubrimientos PVD optimizados para este tipo de entornos que penalizan tanto, los componentes críticos se benefician de una mayor dureza superficial y un coeficiente de fricción mucho menor. Como resultado, estas piezas críticas no tienen que sustituirse con tanta frecuencia, si es que tienen que hacerlo, lo que reduce el mantenimiento y los periodos de parada del equipo no planificados, a la vez que mejora el rendimiento y la seguridad de la maquinaria.
Hoy en día, estos componentes recubiertos se utilizan para una variedad de aplicaciones en la industria aeroespacial; entre ellas se incluyen sistemas hidráulicos, bombas de pistón, bombas de combustible, cojinetes y sistemas de control de vuelo como componentes de vías de aletas deslizantes. Los recubrimientos son también una técnica probada para mejorar las piezas giratorias críticas en los motores, bombas y válvulas hidráulicos.
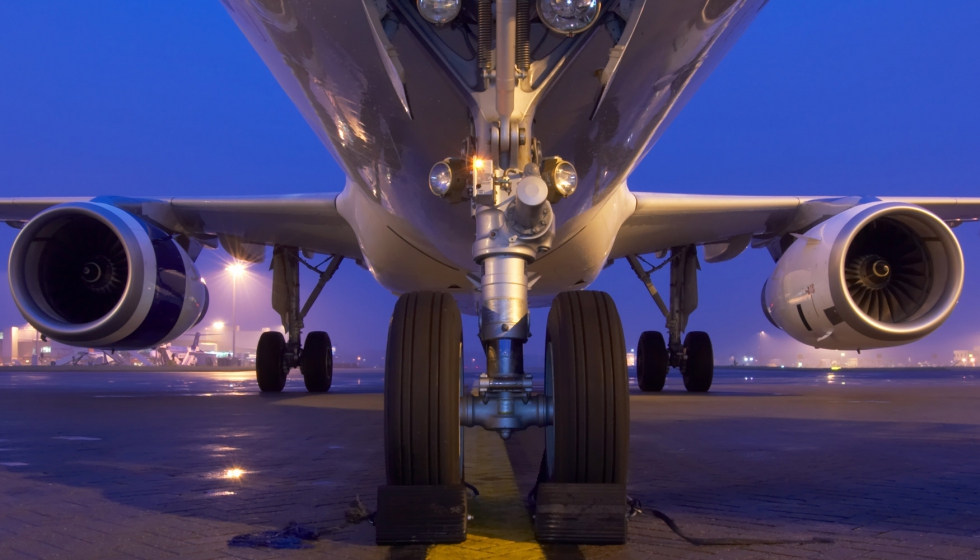
Los tratamientos superficiales alternativos conllevan deficiencias y riesgos
Muchos componentes no están recubiertos en absoluto. En cambio, estas piezas suelen estar fabricadas con aceros termotratados, nitrurados o endurecidos, junto con materiales duraderos de alto rendimiento como el titanio o las aleaciones con base de níquel. Incluso los que se utilizan en aplicaciones de alta carga están sujetos a desgaste y fallos prematuros si no cuentan con una buena lubricación.
Además, la preocupación por los compuestos, las emisiones o los residuos contaminantes está asociada a estas técnicas de cubrición. El cromo duro también se especifica a menudo para proporcionar protección contra el desgaste y la corrosión. Aunque el cromo duro puede aplicarse en componentes que experimentan desgaste por abrasión, las microfisuras inherentes al proceso limitan su uso contra la corrosión. Además, los fabricantes están buscando un sustituto adecuado del cromo duro debido a los riesgos documentados para la salud de los trabajadores y al impacto en el medio ambiente de la exposición al cromo hexavalente, un carcinógeno que se produce durante el proceso de cromado y que es la forma más tóxica de cromo.
Es por ello que el cromo es una sustancia altamente regulada en los principales mercados mundiales. En la Unión Europea, el cromo hexavalente está regulado por el reglamento REACH (registro, evaluación, autorización y restricción de las sustancias y preparados químicos) de la UE, que establece directrices para el uso seguro de determinadas sustancias químicas en toda la cadena de suministro. El cromo también está estrechamente regulado en los Estados Unidos por la Administración de Seguridad y Salud Ocupacional (OSHA).
Los recubrimientos PVD como opción al cromo duro que cumple con REACH
Una alternativa que se utiliza cada vez más, especialmente en la industria aeroespacial, son los recubrimientos PVD, que son una opción de sustitución del cromo duro no peligrosa y conforme a REACH. Entre las opciones de PVD están diversos recubrimientos a base de carbono que proporcionan una combinación única de dureza superficial extrema, bajo coeficiente de fricción y propiedades anticorrosivas. Los recubrimientos PVD ofrecen muchos de las mismas ventajas y, en cierto modo, son superiores al cromo duro.
Según Toby Middlemiss, Market Segment Manager Aerospace and Defence de Oerlikon Balzers, un proveedor global de recubrimientos, el recubrimiento Balinit C de la empresa ofrece una solución ideal: “Se trata de un recubrimiento de carburo de tungsteno dúctil WC/C muy resistente al desgaste por adherencia (roce) y al desgaste por fricción en particular. Tiene una gran capacidad de carga incluso en condiciones de lubricación deficiente o de contacto seco”. Debido a su bajo coeficiente de fricción, actúa para reducir la corrosión por picaduras y la corrosión por fricción. Así que no es de extrañar que el Balinit C también haya atraído la atención de algunos de los mayores fabricantes aeroespaciales del mundo, incluido Airbus. La calificación técnica de Balinit C como opción inocua y acorde con el reglamento REACH frente al cromado duro constituye la culminación del Proceso de calificación industrial de Airbus para los centros de producción de Oerlikon Balzers Reino Unido y Oerlikon Balzers Francia. Oerlikon Balzers cuenta con instalaciones de recubrimiento acreditadas por la NADCAP en Guelph (Canadá), Milton Keynes (Reino Unido), Ferrières-en-Brie (Francia) y Niedercorn (Luxemburgo).
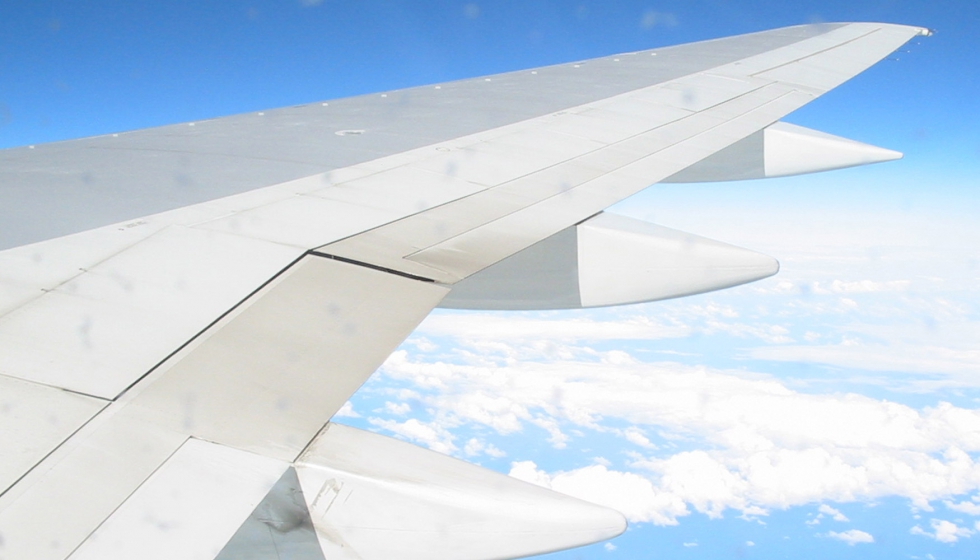
Recubrimientos PVD especializados
La deposición en fase de vapor por proceso físico constituye una variedad de los métodos de deposición en vacío empleados para producir recubrimientos finos. El PVD se utiliza habitualmente para recubrir componentes a temperaturas de aplicación relativamente bajas de 200 a 500 °C. Se trata de las temperaturas ideales ya que se encuentran por debajo de la temperatura de templado de los aceros y evitan así la alteración de las propiedades fundamentales del material.
Afortunadamente, están disponibles diversos recubrimientos a base de carbono que proporcionan una combinación única de dureza superficial extrema, bajo coeficiente de fricción y propiedades anticorrosivas.
Un buen ejemplo es el recubrimiento Balinit DLC, un recubrimiento sin metal y con base de carbono que es aún más duradero. Aplicado a través de Deposición química en fase de vapor asistida por plasma (PACVD), este recubrimiento está diseñado para condiciones de desgaste más duras y altas velocidades de deslizamiento para proteger contra la abrasión, el desgaste por fricción y la soldadura por presión en frío.
Estos y otros recubrimientos de la familia Balinit que se adaptan a necesidades específicas pueden aplicarse a una variedad de aceros templados o revenidos, acero inoxidable austenítico, así como níquel, titanio, cobre, magnesio y aleaciones de aluminio.
Los recubrimientos también tienen la ventaja de ser delgados, habitualmente en torno a 3 μm. Esta característica, junto con la baja tolerancia +/- 0,5 μm, significa que el componente conserva su forma, ajuste y dimensiones después del recubrimiento sin necesidad de procesos de remecanizado ni rectificado.