Evaluación de la corrosión mediante métodos electroquímicos como alternativa a la niebla salina
Dr. José Antonio Díez Silanes, Business Development Manager-Technological Services; Dra. Gemma Vara Salazar, Head of Marketing and Positioning; y Dr. Jesús Manuel Vega Vega, Head of Corrosion and Tribology. Cidetec Surface Engineering
17/07/2019A modo de ejemplo, si la aplicación del acero al carbono es estructural, la corrosión generalizada forma óxidos e hidróxidos de hierro perjudiciales que provocan la disminución del espesor de la pieza y, por lo tanto, merman sus propiedades mecánicas. Esto, a su vez, supondrá una disminución progresiva de los márgenes fijados por los coeficientes de seguridad (en cuanto a espesor) durante la fase de diseño de la pieza y/o componente y, una vez sobrepasados éstos, el fallo del elemento considerado.
Los procesos de corrosión pueden atender a varias clasificaciones. Si se atiende al medio, se pueden establecer dos tipos de corrosión:
- Oxidación por reacción directa con el oxígeno a altas temperaturas.
- Corrosión acuosa en presencia de un electrolito.
- En ambos casos, factores como la temperatura, diferencias de potencial estándar de reducción, accesibilidad y diferencia de concentración del oxígeno, estado supuerficial (ej. porosidad), combinación con tensiones o desgaste, etc., influyen en el proceso de corrosión.
Por otro lado, en función de la extensión de la corrosión, ésta se puede clasificar en:
- Corrosión uniforme o generalizada: el material es atacado de manera similar por toda la superficie, por lo que la pérdida de propiedades ocurre de forma homogénea.
- Corrosión localizada: suele ser más peligrosa que la generalizada, ya que se trata de un ataque localizado y en profundidad, de forma irregular y difícil de prever. Suele atribuirse a la naturaleza del metal y a las heterogeneidades químicas y estructurales. Se distinguen varios tipos de corrosión local: por picadura e intergranular, que pueden ser agravadas por otros factores como la tensión estática o dinámica (ciclos de fatiga), la cavitación-erosión o el desgaste (tribocorrosión).
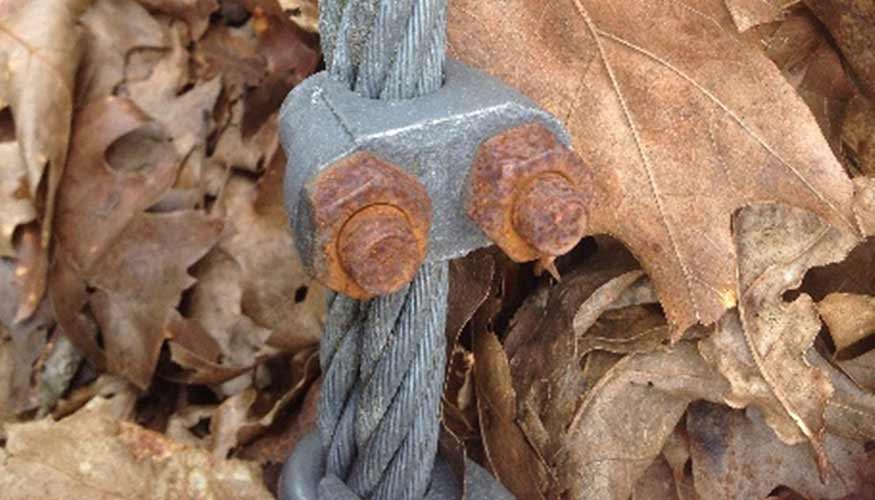
Reacciones que tienen lugar durante el proceso de corrosión y estrategia de protección
La corrosión puede definirse como el conjunto de fenómenos físico-químicos por efecto de los cuales la superficie de un metal es atacada por los más diversos agentes químicos. Dentro del concepto general de corrosión acuosa, sobre una pieza de acero al carbono que se corroe, existen áreas anódicas y catódicas. En las zonas anódicas se produce un proceso de oxidación (pérdida de electrones) habitualmente provocando la disolución del metal:
Fe => Fe 2++ 2e-
Fe 2+ => Fe 3++ e-
En los lugares catódicos ocurre un proceso de reducción, con ganancia de electrones, que habitualmente suele ser la reducción del oxígeno disuelto (aunque también se puede dar la reducción de protones para formar gas hidrogeno si hubiera un medio ácido). Las dos reacciones más comunes son:
O2 + 2 H2O + 4e- => 4 OH –
2 H+ + 2e- => H2
En función de la agresividad de la atmósfera (rural, industrial o marina), y con el objetivo de incrementar la vida del material, es necesario utilizar un sistema de protección. La agresividad del medio se utiliza como punto de referencia y como guía para estimar la vida del acero en función del tipo y espesor de los recubrimientos aplicados como sistema de protección. Sin embargo, si la preparación de la superficie o el modo de aplicación del recubrimiento no es adecuado, puede dar lugar a un fallo prematuro. Por lo tanto, es necesario llevar a cabo una evaluación y control de calidad de los sistemas de protección con métodos o herramientas que den información a corto plazo.
Métodos empleados en la evaluación de la resistencia a la corrosión
Aunque los ensayos ideales y más fiables son aquellos donde se expone el metal con su sistema de protección al ambiente real u operacional, la principal desventaja es que el proceso de corrosión suele ser lento. En la actualidad, el ensayo por excelencia utilizado como control de calidad del recubrimiento protector a nivel industrial es el ensayo de niebla salina (ISO 9227:2012). Este ensayo consiste en exponer la pieza a una atmósfera rica en cloruros y durante un cierto espacio de tiempo, manteniendo constante la temperatura. El tiempo transcurrido desde que se introduce la pieza hasta que comienza el ataque de la corrosión da una medida de la durabilidad bajo un ambiente agresivo.
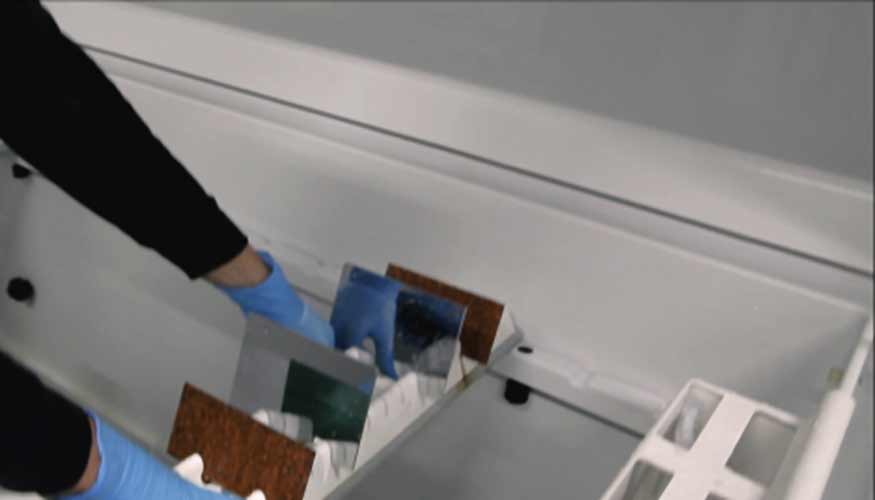
Aunque se pretende conseguir una correspondencia cualitativa y cuantitativa del ensayo de niebla salina respecto a los ensayos de corrosión natural, en realidad no se puede establecer una correlación absoluta entre el ensayo de niebla salina y su equivalencia en años. Existen múltiples factores en los que es complicado o imposible establecer correlación alguna, ya que el mecanismo de protección del recubrimiento se puede ver alterado por las condiciones del ensayo.
Teniendo en cuenta estas limitaciones y sabiendo que la naturaleza de la corrosión es electroquímica, hay técnicas electroquímicas capaces de suministrar información sobre la velocidad de corrosión y su evolución con el tiempo. Una ventaja adicional es la obtención de la resistencia frente a la corrosión a tiempos cortos, permitiendo realizar una estimación de la susceptibilidad de los materiales a ser corroído.
Evaluación de la corrosión por técnicas electroquímicas
Como se ha comentado anteriormente, la corrosión se puede clasificar en función de su extensión. La corrosión uniforme, ocurre sobre toda la superficie del metal de forma similar. Sin embargo, la corrosión localizada tiene lugar en pequeños puntos muy localizados (el rango de dimensión puede ir por debajo de 1 µm a varios centímetros) sobre la superficie del metal, caracterizándose por penetraciones profundas y rápidas a través de la misma. La velocidad de la corrosión localizada es varios órdenes de magnitud mayor que la velocidad de corrosión general, si se normaliza por el área real que sufre el ataque.
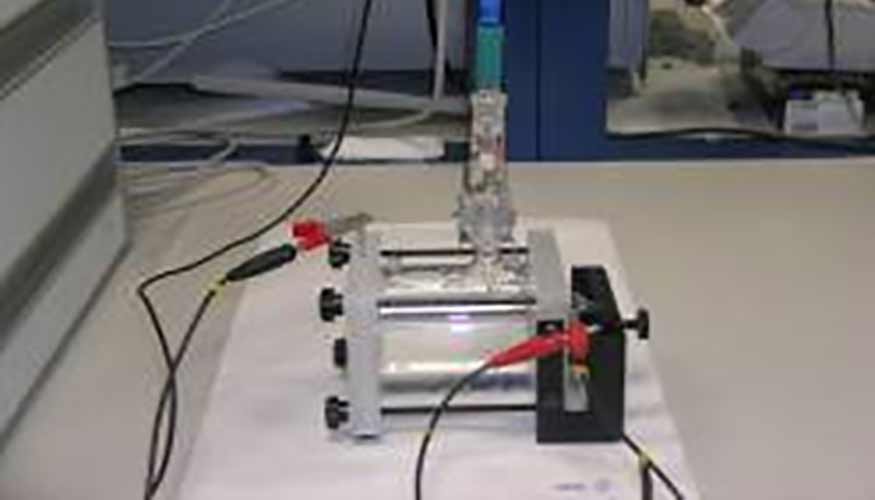
Tanto la corrosión generalizada como la localizada se pueden evaluar electroquímicamente a través de curvas de polarización lineal y potenciodinámicas, así como por espectroscopia de impedancia electroquímica. Además, para corrosión localizada en materiales pasivables, se suele emplear la técnica de ruido electroquímico.
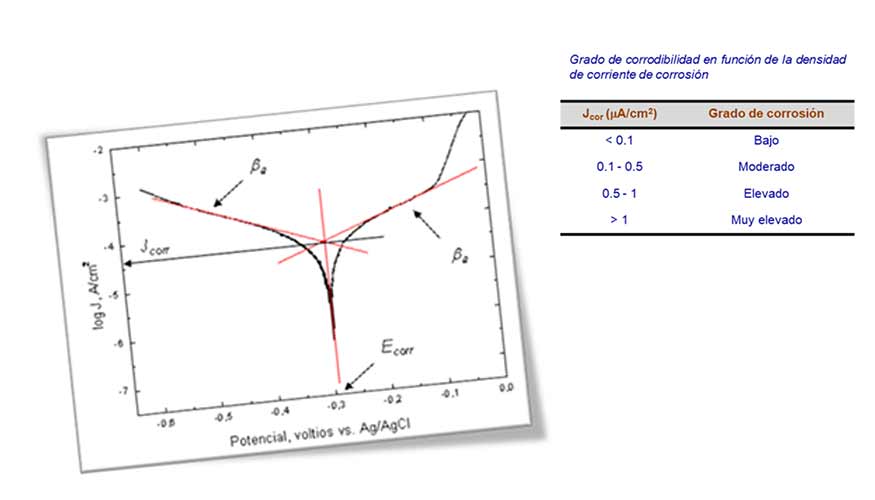
Curvas de polarización lineal
La principal ventaja de la polarización lineal frente a otros métodos de corriente continua es que es un método no destructivo (± 10 mV frente al potencial a circuito abierto), permitiendo estimar la velocidad de corrosión cuando se ha alcanzado el estado estacionario a partir de valores de resistencia a la polarización.
Las medidas de polarización lineal presentan varias limitaciones como son, que solamente miden corrosión general y no pueden determinar la corrosión localizada o qué tipo de cinética controla el proceso. Sin embargo, este método es muy útil cuando se necesita monitorizar la corrosión en un tiempo largo.
Curvas potenciodinámicas: ajuste por Tafel
El ajuste de curvas potenciodinámicas por el método de Tafel es muy útil para determinar la velocidad de corrosión y determinar qué reacciones (anódicas o catódicas) controlan el fenómeno de corrosión.
En el caso de superficies o de materiales pasivos, este método permite determinar parámetros como el potencial de pasivación, el potencial de repasivación y el rango de potencial de la zona pasiva, zona transpasiva y activa. Estos términos permitirán conocer la eficacia con la que una película pasiva protege un metal de la corrosión y caracterizar el comportamiento de la misma.
Espectroscopia de impedancia electroquímica EIS
La principal diferencia con el resto de técnicas electroquímicas es que la perturbación del sistema a estudiar se realiza mediante corriente alterna en lugar de continua. La mayor ventaja es la posibilidad de medir procesos separados que ocurren en el mismo material en función de la constante de tiempo de cada uno de ellos, y obtener valores como el de su resistencia del recubrimiento. Esto hace que sea una técnica muy utilizada para la evaluación de recubrimientos protectores, ya que proporciona información adicional a la obtenida por técnicas basadas en corriente continua. Además, es un método no destructivo, ya que habitualmente se aplica una pequeña perturbación (± 10 mV), que permite monitorear la degradación de un sistema con el tiempo.
Ruido electroquímico
Esta técnica suele utilizarse para evaluar la corrosión localizada (ej. picadura), monitorizando el potencial en circuito abierto y la densidad de corriente con el tiempo. Para el análisis de resultados, se utilizan modelos matemáticos como el estudio de las características fractal de la señal o transformar los registros de tiempo en frecuencia, los cuales suelen ser tratados mediante transformadas de Fourier. Es necesario tener un dominio sobre esta técnica para llevar a cabo un análisis e interpretación adecuada.
Éxito en el seminario sobre métodos electroquímicos de caracterización y evaluación de la corrosión
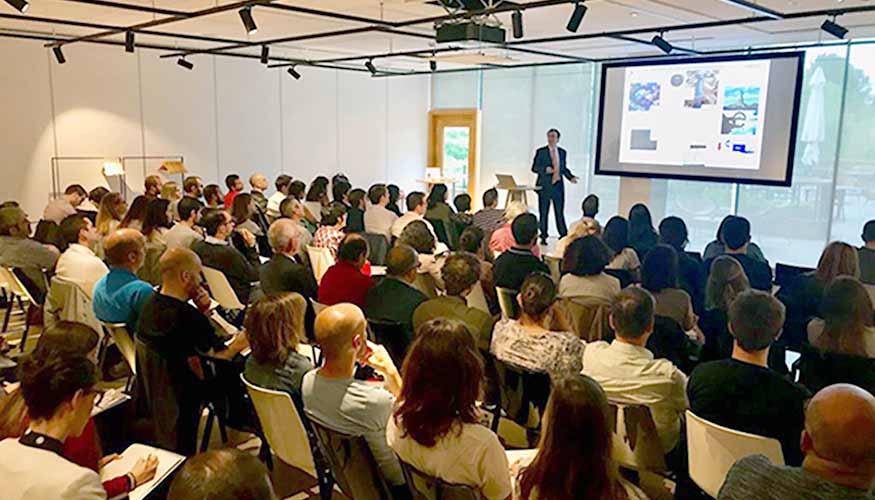
Cerca de un centenar de profesionales tuvieron ocasión de conocer de primera mano estas técnicas gracias a las intervenciones de diferentes expertos en la materia. La jornada fue presentada por los doctores José Antonio Díez y Gemma Vara, de Cidetec, y Roberto Conde, de Gomensoro. El doctor Jesús Manuel Vega, de Cidetec, ofreció la charla ‘Técnicas electroquímicas para el control de la corrosión’ mientras que Jesús García de la Fuente, de Gomensoro, disertó sobre la normativa aplicable a la hora de trabajar con técnicas electroquímicas.
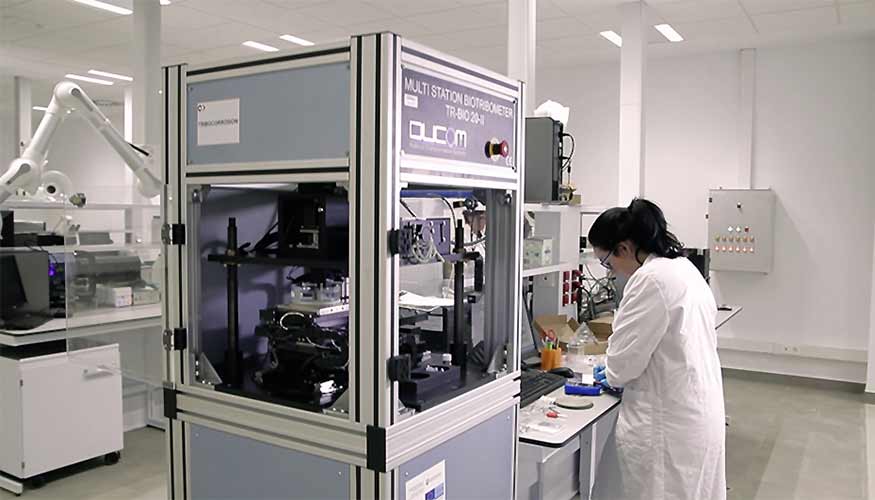
En la segunda parte de la jornada se presentaron diferentes casos prácticos de la mano de los profesionales tanto de Cidetec como de Gomensoro, abordándose la aplicación de diferentes técnicas a casos industriales. Además, se mostró la utilidad de combinar técnicas electroquímicas junto con fenómenos que ocurren de forma simultánea, como puede ser el desgaste (tribocorrosión).
La jornada concluyó con una visita a las instalaciones de Cidetec Surface Engineering.