En las principales plantas de fabricación de aviones de Europa
Eaton mejora la fiabilidad energética de los Airbus
Eaton ha ayudado a mejorar la fiabilidad energética, seguridad y protección personal en la mayor instalación de producción de Airbus de Alemania con la actualización de una parte de su unidad de distribución de energía de baja tensión a los estándares más modernos.
Para la realización del proyecto se recurrió a la empresa de gestión energética para que ofreciera una solución completa, incluida la monitorización del cuadro eléctrico, el control continuo de la temperatura en puntos críticos del embarrado, así como la implementación de un sistema de protección contra el arco eléctrico.
La instalación, en la nave número 9 de la fábrica de Airbus en Hamburgo-Finkenwerder, ofrece al equipo técnico y de mantenimiento de la empresa, una monitorización sin precedentes del rendimiento del cuadro eléctrico de baja tensión, de modo que se pueda detectar, observar y corregir rápidamente los posibles problemas, tales como caídas de tensión, sobrecargas o fallos de arco. Esto permite garantizar la máxima fiabilidad del suministro energético y proteger a los trabajadores en caso de producirse un arco eléctrico.
La fábrica, que se especializa en la producción final del programa A320, opera las 24 horas del día, los 7 días de la semana, y cuenta con la fiabilidad máxima del sistema técnico. Los Airbus requerían una supervisión constante del sistema y los componentes en conexión con el sistema de control del edificio, además de una mayor protección del personal.
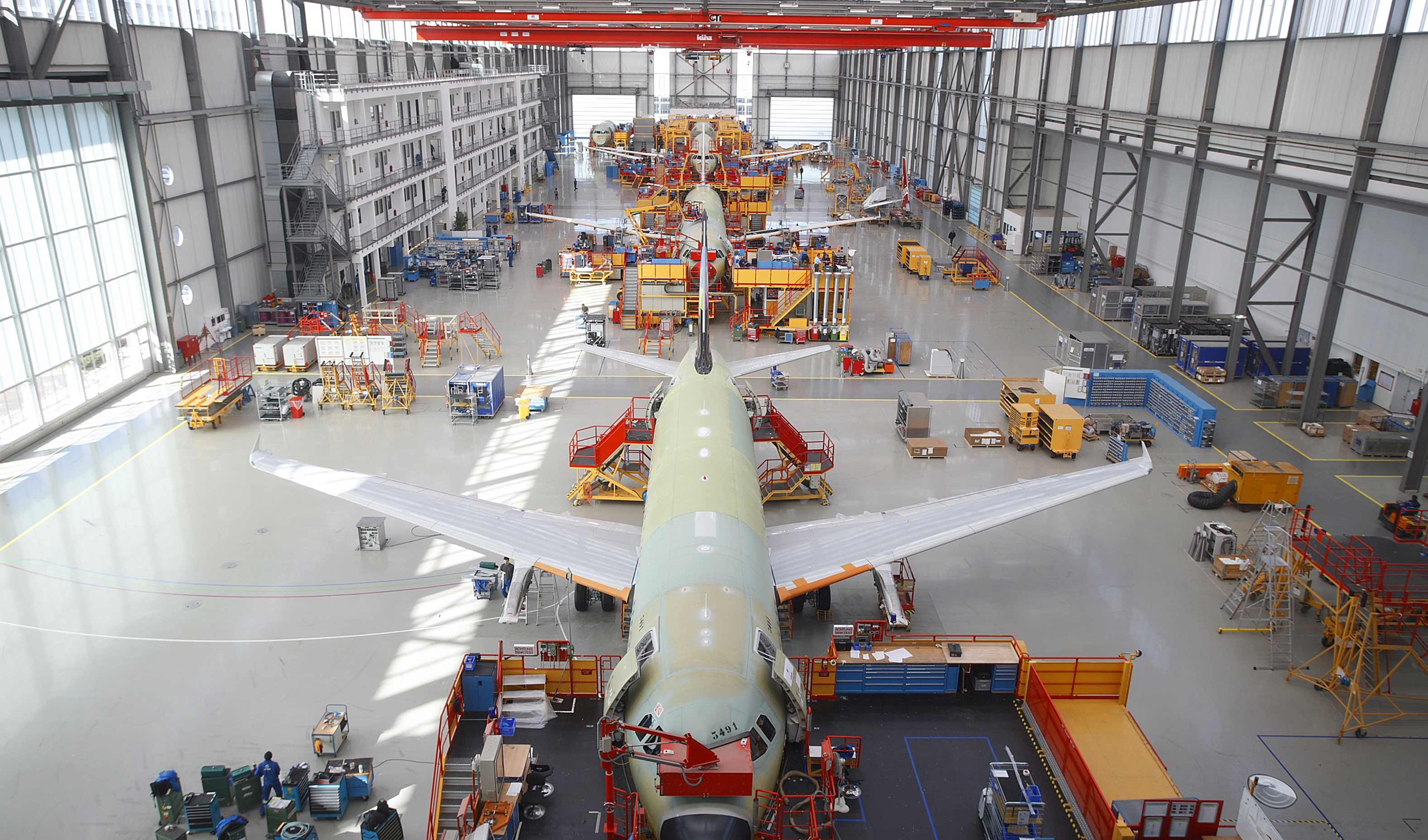
Eaton ofreció una solución completa, incluida la monitorización del cuadro eléctrico y el control continuo de la temperatura en puntos críticos.
Listo en dos días
Para minimizar los tiempos de inactividad, la nueva solución se tuvo que poner en marcha en el ajustado plazo de dos días, en un único fin de semana.
Los interruptores IZM de la serie de Moeller de Eaton son la piedra angular de la solución, ya que ofrecen un rendimiento de entre 630 y 4000 A con una unidad de disparo eléctrico y una función de medición integrada. Estos interruptores pueden transmitir datos detallados al sistema de registro y de visualización de datos "BreakerVisu". El proceso se simplificó gracias al sistema de cableado y comunicación inteligente de Eaton SmartWire-DT. La conexión directa de "BreakerVisu" al sistema de control del edificio implica que el equipo de Airbus ya tiene acceso a todos los datos relevantes sobre el suministro energético a través de la visualización online.
El sistema de diagnóstico de Eaton para el control de la temperatura también permite, por primera vez, llevar un control continuo de la temperatura de las áreas críticas del cuadro eléctrico. El sistema se basa en un controlador de diagnóstico y sensores térmicos autónomos para controlar todos los embarrados y puntos de conexión, así como sensores térmicos versátiles para los demás puntos de medición. Como parte del proyecto, se instalaron casi 80 sensores térmicos en el cuadro para la nave número 9. En el caso de desviaciones, el sistema genera una alerta del error actual o activa una alarma si se supera un límite.
Para mejorar el cuadro eléctrico general en términos de seguridad del personal, Eaton también instaló el sistema Arcon de protección contra cortocircuitos provenientes de un arco eléctrico.
En Airbus quedaron muy satisfechos con la solución desarrollada por Eaton y con la rapidez de su instalación, y están considerando implementar la idea a otras naves de la fábrica Finkenwerder.
La línea de producción de la nave número 9 de la fábrica se extiende por cuatro líneas de montaje, por las que la aeronave circula durante varios días. En estos puntos de montaje, por ejemplo, se montan los componentes del fuselaje y de las alas, el estabilizador vertical, los elevadores, los motores y las ruedas de aterrizaje, y se instalan los asientos. Para garantizar un correcto desarrollo del proceso, las estaciones de suministro se pueden aumentar o reducir según convenga.