El turbocompresor para automóvil
El flujo de gases a través de los componentes del turbocompresor debe diseñarse para garantizar el máximo rendimiento de la turbina, y en este sentido la dinámica fluidos computacional (DFC) desempeña un papel crucial en el desarrollo del turbocompresor. Este aumenta en un motor diésel 4 veces la potencia que con un motor de aspiración natural. El turbocompresor es más útil en el motor diésel, sin bujías, que en el motor de gasolina.
El lector se preguntará cómo tiene que instalar el turbocompresor para que trabaje conjuntamente con el motor de combustión interna. Es una añadidura fácil y no es caro. Para la instalación correcta recordemos aquí el funcionamiento del motor de 4 tiempos.
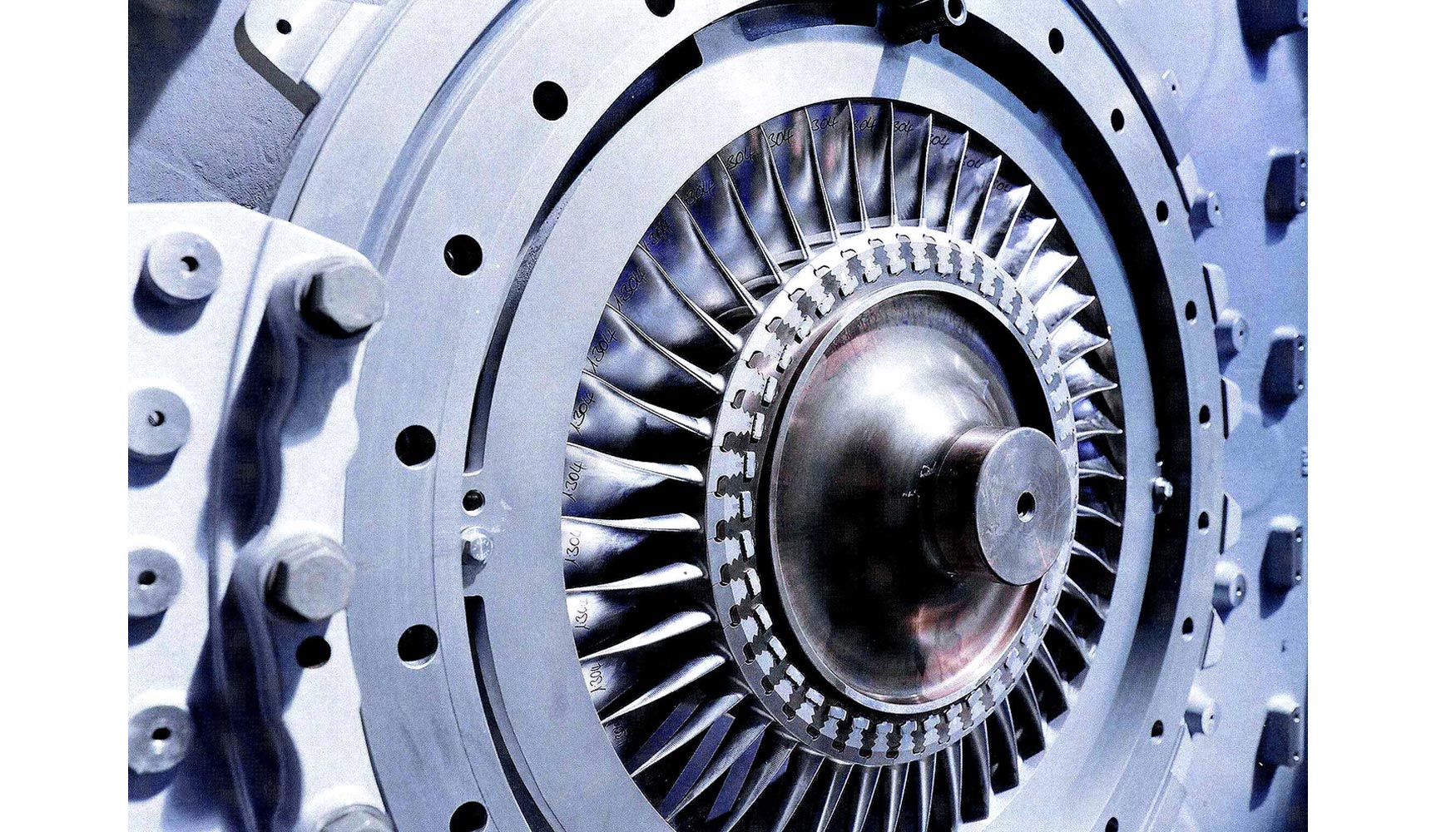
El motor de gasolina y el de gasoil
El motor de explosión es de 2 y 4 tiempos. El de dos tiempos es el de la moto: aspiración de aire y la explosión. Decimos que un motor está sobrealimentado cuando comprimimos el aire de admisión. El motor de gasolina es alternativo y precisa 4 carreras del pistón (2 vueltas completas del cigüeñal) para completar el ciclo termodinámico. Los 4 tiempos son: admisión, compresión, trabajo y escape.
- 1º tiempo o admisión: el pistón desciende en el cilindro, el cual aspira la mezcla aire-combustible. Interesa meter en el cilindro la mayor cantidad de aire, porque la potencia de la explosión depende de la cantidad de aire. El aire entra en el compresor de admisión axialmente y sale radialmente. El aire se enfría en el intercambiador de calor para aumentar la densidad. El motor convencional atmosférico aspira el aire a presión atmosférica, y para una misma cilindrada tiene menos potencia que el motor con turbo.
- 2º tiempo o compresión: el pistón desde abajo asciende comprimiendo la mezcla aire-gasolina.
- 3º tiempo o explosión-expansión: el pistón ha logrado una presión máxima, salta la chispa en la bujía e inflama la mezcla, aumenta la temperatura y presión en el cilindro expandiendo los gases, que empujan hacia abajo al pistón y hace girar el cigüeñal produciendo trabajo.
- El 4º tiempo o escape: el pistón en su movimiento ascendente empuja los gases quemados, que salen con fuerza a través de la válvula de escape. La turbina del turbocompresor se opone a esos gases, absorbe su energía y la aprovecha para accionar el rotor de compresión. Sobre el mismo eje que la turbina se comprime el aire de admisión. Los gases de escape inciden radialmente en la turbina saliendo axialmente, después de ceder gran parte de su energía interna.
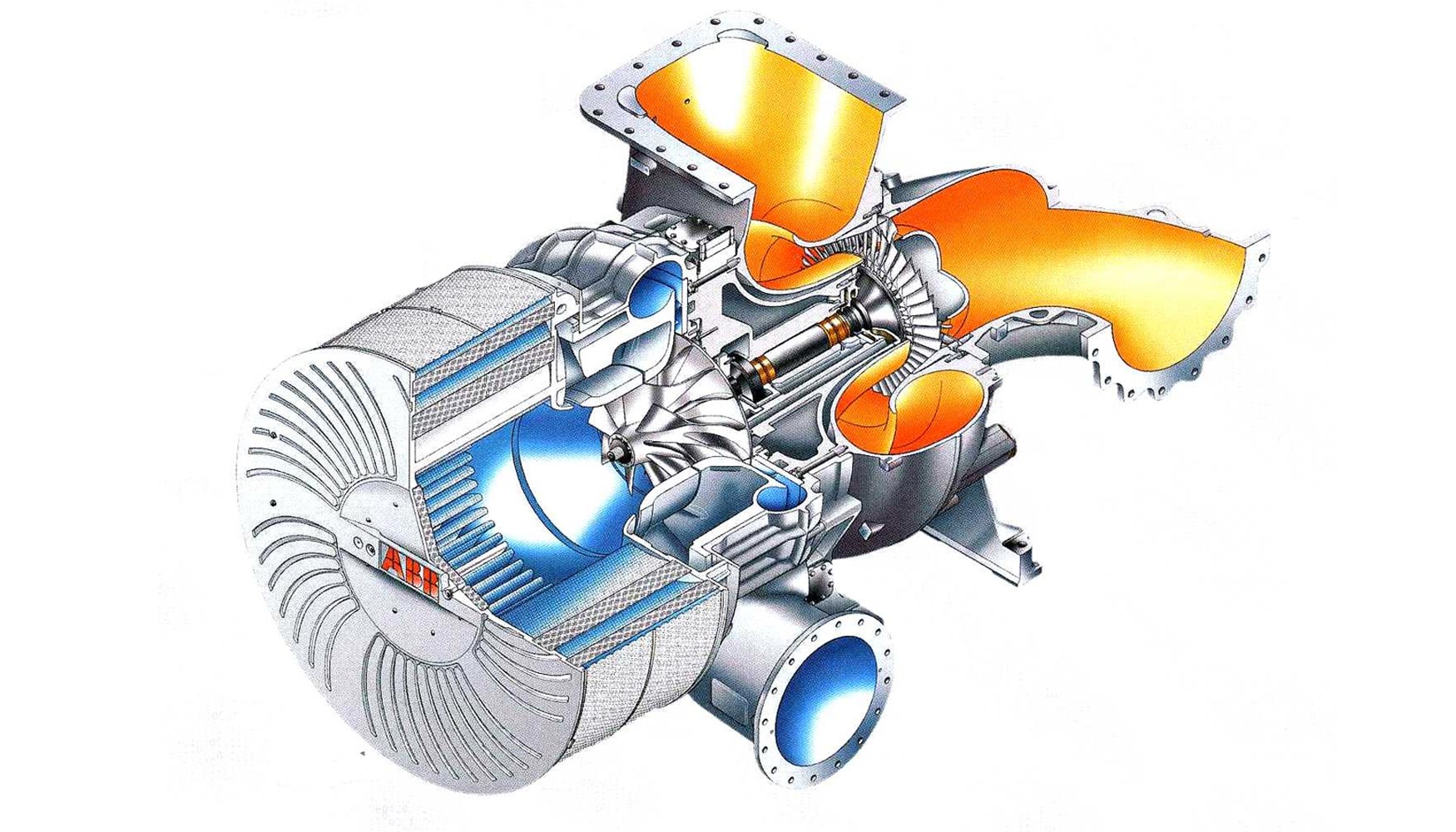
El motor diésel es muy parecido al motor de gasolina pero sin bujías. Con el aire de admisión comprimido al máximo se inyecta el combustible, muy pulverizado, se forma la mezcla explosiva, y ésta empuja con gran energía el pistón hacia abajo. La presión de estos gases quemados es muy superior a la presión del motor de gasolina (de 40 a 80 bares). En el motor de gasolina la presión es de 15-25 bares.
El intercambiador de calor, o intercooler, que enfría el aire de admisión es necesario porque el aire comprimido se calienta y pierde densidad. Así, en un mismo volumen tenemos menos masa de aire, por lo que es capaz de quemar menos combustible, y genera menos potencia.
- El biturbo en el coche: es un sistema de dos turbocargadores de distinto tamaño. Al arrancar, a baja velocidad, solo funciona el pequeño, debido a su respuesta más rápida, y el grande funciona a altas revoluciones, ya que ejerce mayor presión.
- El turbocompresor de geometría variable (TGV) en el coche tiene un mecanismo de aletas, álabes, móviles, que se abren y cierran haciendo variar la velocidad de los gases quemados que entran en la turbina. A bajas revoluciones, con bajo caudal de gases de escape se cierra el paso entre los álabes. A altas revoluciones los álabes de abren. En motores diésel es muy común el TGV.
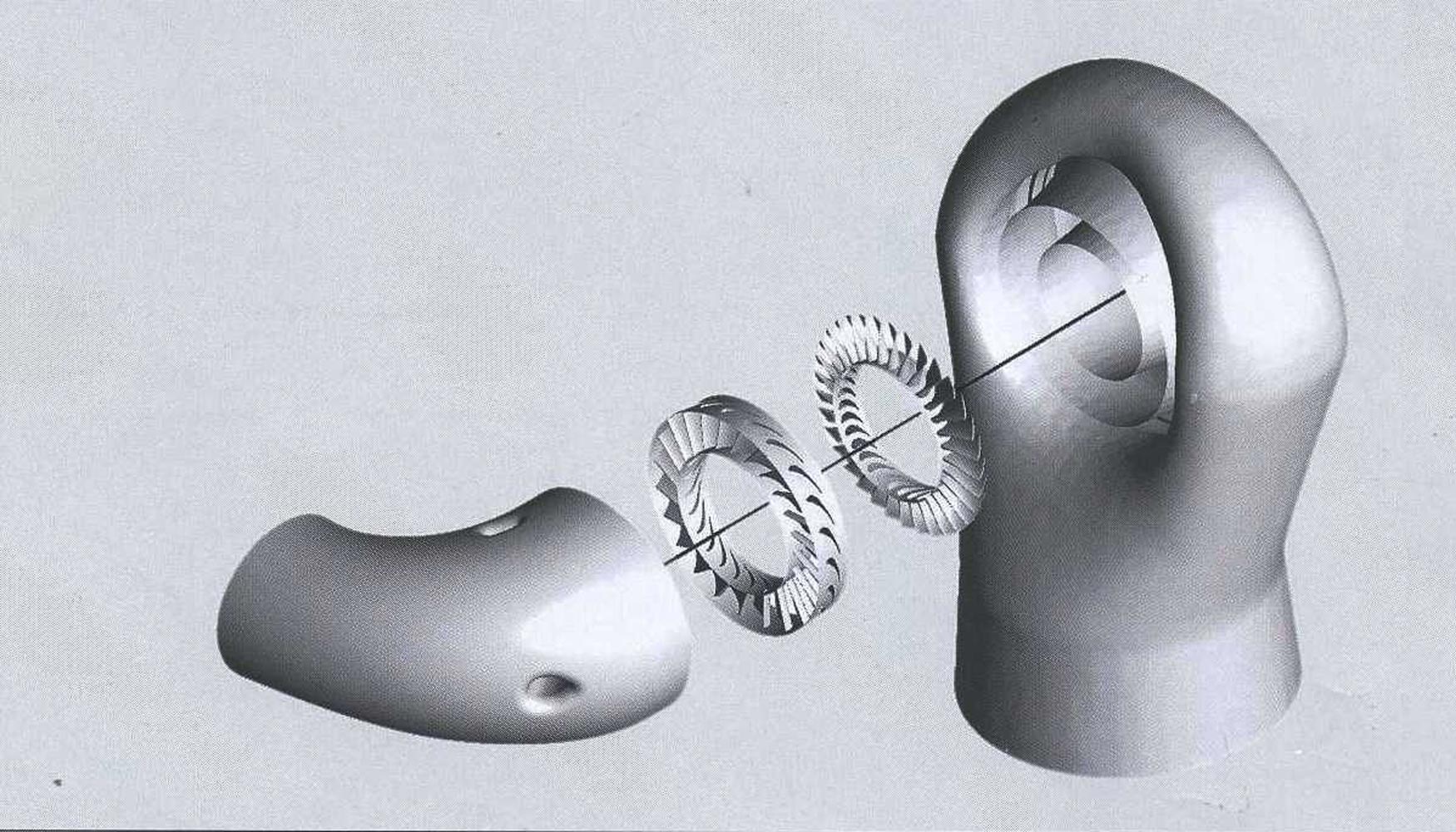
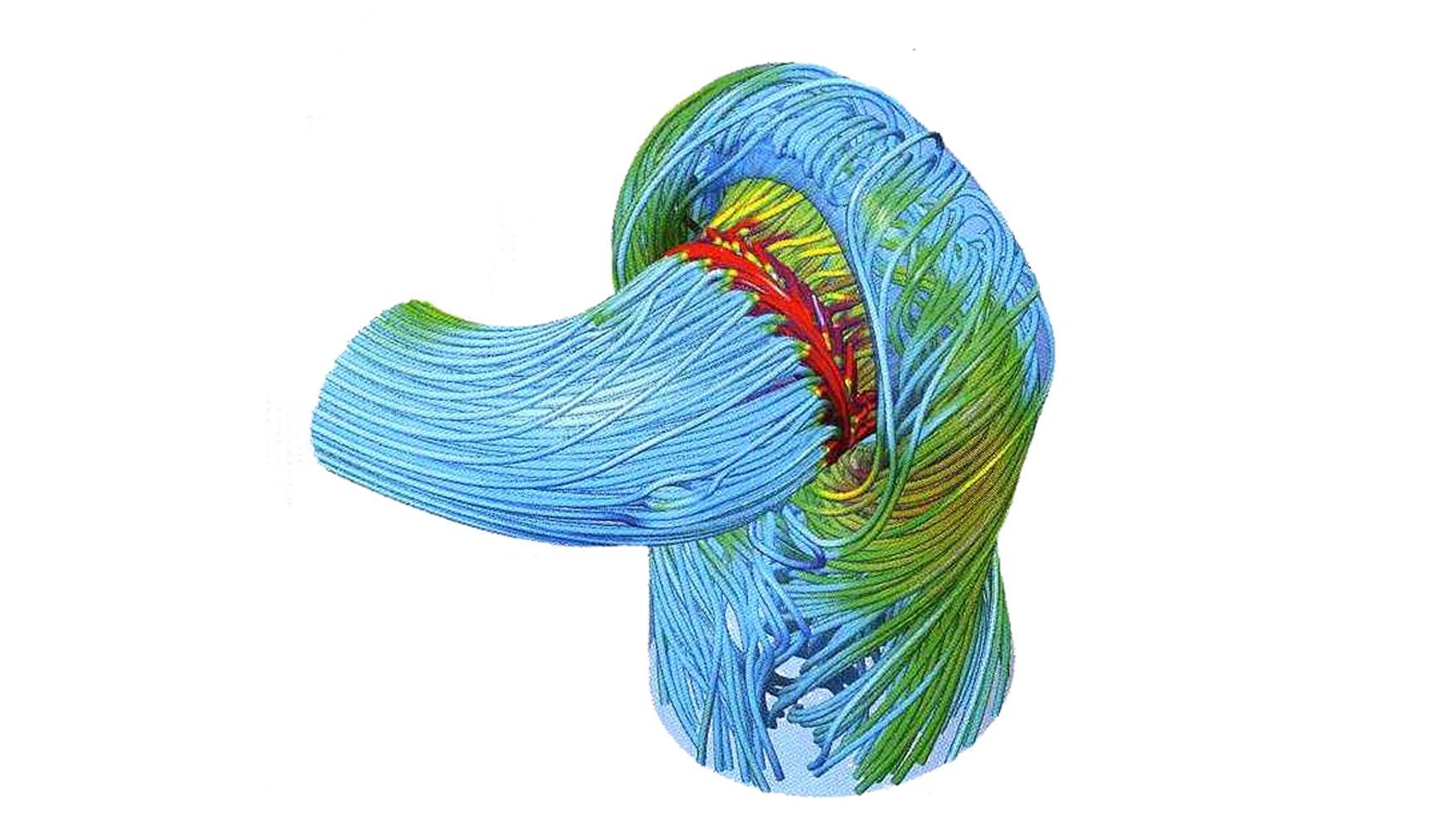
Más potencia con el turbocompresor
Esta tecnología es la principal impulsora de la reducción de costes de combustible y reducción también de emisiones de óxidos de nitrógeno a la atmósfera. El análisis aerodinámico y la optimización de rotores y estatores basados en DFC se han convertido en un procedimiento normal de desarrollo. Las simulaciones del DFC de la turbina completa desde el borde admisión de gases hasta la salida han ayudado a descubrir una geometría de turbina menos sensible a las distorsiones. La simulación de la etapa axial de la turbina mediante DFC se efectúa sobre dos componentes: el anillo de la tobera y el rotor.
La simulación se produce cuando el colector de admisión y el de salida presentan giros bruscos. En este caso ya no se sostiene la hipótesis de que los caminos de admisión y de salida son axialmente simétricos. Estas desviaciones de flujo de gas pueden tener un efecto considerable en el rendimiento del difusor y de la turbina con la consiguiente caída de la eficiencia. Hasta ahora, encontrar un difusor adecuado requería iteraciones de diseño y pruebas muy completas.
Las simulaciones del colector de admisión radial junto con el anillo de la tobera permiten estudiar la falta de homogeneidad del flujo de entrada, que origina el colector de admisión. Hay que evitar la falta de simetría axial entre la admisión y la salida, un flujo no axial, influye también la geometría de los álabes en el anillo de tobera y los álabes del rotor.
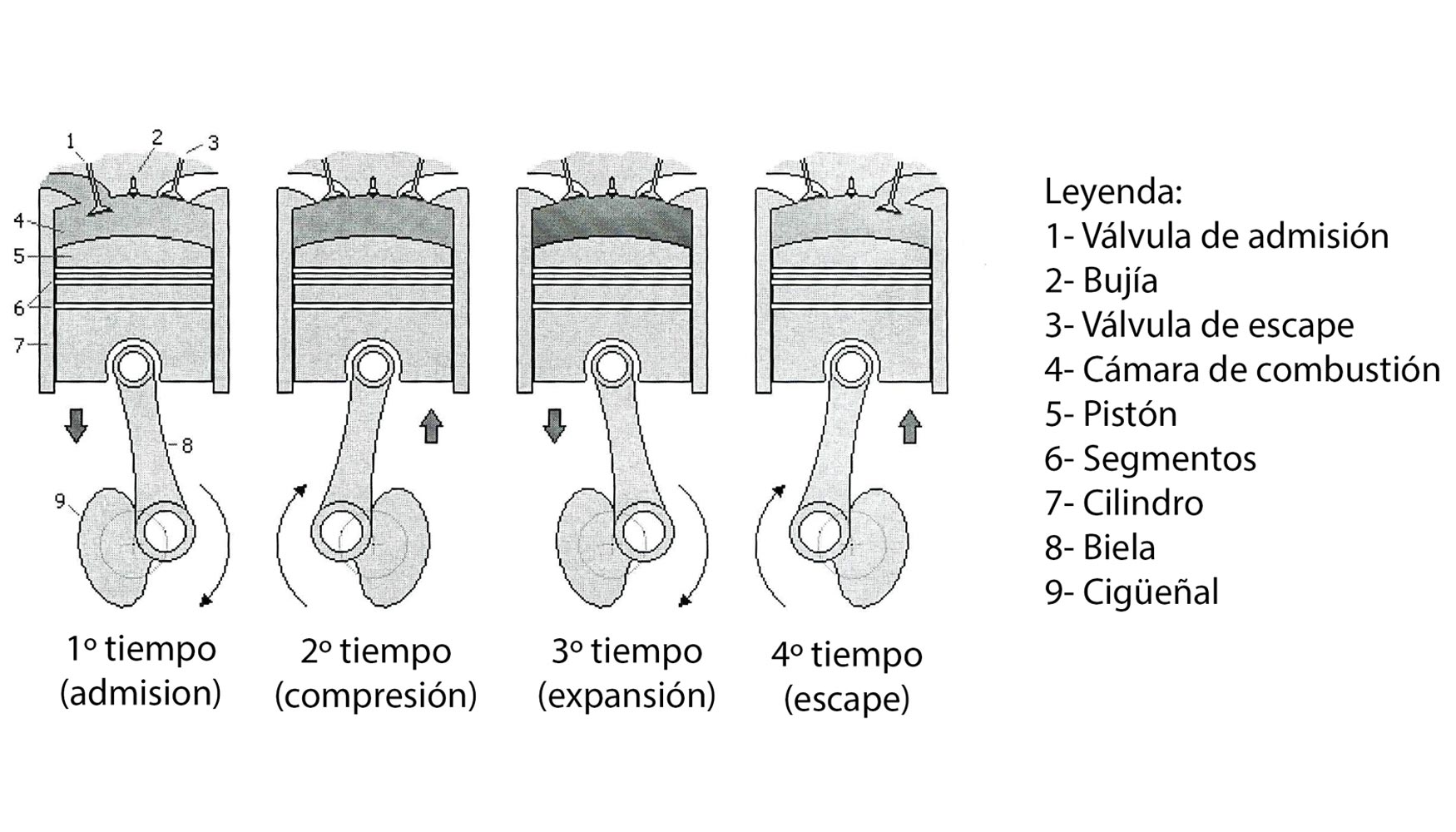
Los 4 tiempos del motor de combustión interna.
Es necesario estudiar la transferencia de calor y el análisis térmico para diseñar la refrigeración del aire de admisión comprimido, antes de la entrada en el cilindro del motor de combustión interna (Tiempo 1). Gracias a la simulación se ha logrado un turbocompresor eficiente, el coche contaminará menos.
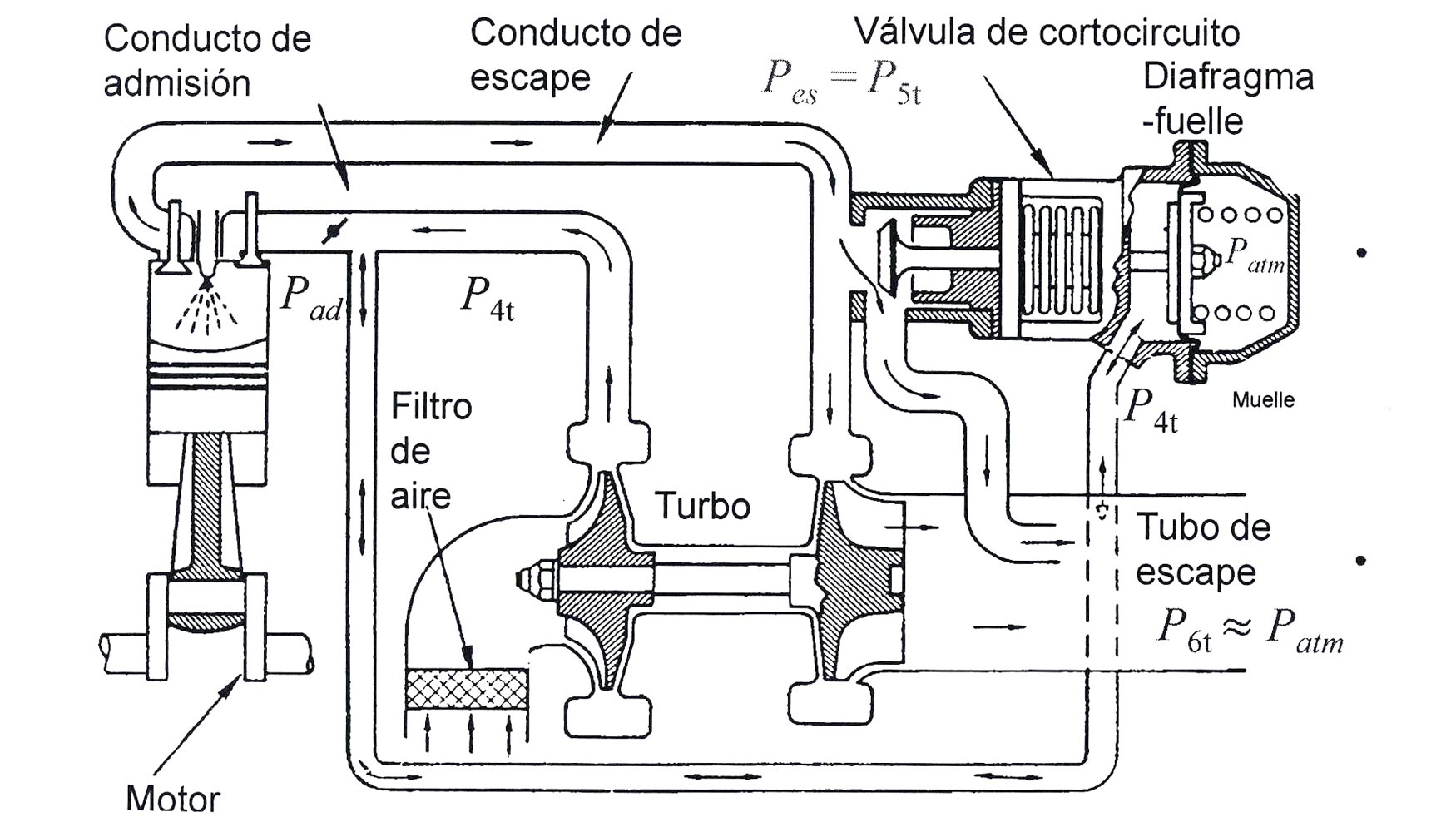
Referencias
Bent Philipsen. Forzar los límites. Simulación de turbinas. ABB Process automation. Turbocharging -review 2/2014.