Once nuevos galardonados por el programa JEC Europe Innovation Awards en 2013
En 2013, los ganadores pertenecen a las siguientes categorías: Materias primas, termoplásticos, materiales multifuncionales, mecanizado y herramientas, edificación y construcción, aeronáutica, automoción, energía eólica, deporte y tiempo libre; además de un premio especial.
La ceremonia de los JEC Innovation Awards tendrá lugar el martes 12 de marzo a las 17:00 horas en el JEC Show (en el Agora), y estará abierta a todos los participantes y visitantes de la exposición. La ceremonia está patrocinada por CYTEC, JEC Composites Magazine, Aviation Week e Innovation & Industrie.
La industria de materiales compuestos da trabajo a 550.000 profesionales en todo el mundo y generó 80.000 millones de ventas en 2012.
Categoría: Materias primas:
- Ganador: BAC2 Limited (Reino Unido)
- Nombre del producto o proceso: Una nueva familia de catalizadores de ácidos latentes que facilita el almacenamiento, transporte, manipulación y procesamiento de mezclas prepoliméricas.
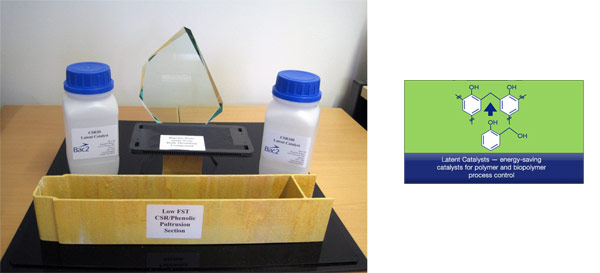
Descripción:
El desarrollo de la familia de catalizadores de ácido latente de RSC (reacción superficial controlada) es fruto del deseo de conseguir que las mezclas prepoliméricas resulten más fáciles de almacenar, transportar, manipular y procesar durante la fabricación de productos. Sin un catalizador latente que controle la polimerización, la duración de conservación de las mezclas prepoliméricas es incontrolable y va de unos segundos a unos minutos. Existen otros catalizadores que amplían la duración de conservación. Sin embargo, normalmente requieren temperaturas de activación superiores a 200 °C, lo que resulta caro en términos energéticos y poco práctico, dado el gran número de materiales que utilizan resinas implicados en los procesos de producción.
Bac2 ha desarrollado una familia de catalizadores de ácidos latentes de RSC que resuelven el problema. La principal innovación ha sido lograr una familia de productos que se activan entre 50 °C y 120 °C, dependiendo de la aplicación y de la velocidad de curado requeridas, permitiendo usarlos con numerosos materiales y procesos. Lo más importante es que los catalizadores no tienen un efecto perjudicial en el flujo de molde ni en otras características de las resinas con las que se usan. En un principio, Bac2 desarrolló su familia de catalizadores de RSC para usarlos con la resina polimérica conductora de la electricidad ElectroPhen, pero ha ido ampliando la gama hasta incluir fórmulas que retrasan y controlan el curado de resinas de fenol formaldehído tipo 'resol', resinas furánicas, resinas uréicas y de melamina.
Con el uso de catalizadores de RSC, la duración de conservación de las mezclas prepoliméricas se ha ampliado a más de tres meses, lo que simplifica su almacenamiento, transporte y manipulación. Se han conseguido mejoras en la eficiencia de los procesos de extrusión inversa de hasta el 130%. En los procesos con compuesto de láminas moldeadas (sheet moulding compound, SMC) o polvo de moldeo por prensado fibroso preparado (bulk moulding compound, BMC), la duración de conservación a temperatura ambiente se ha ampliado a varios meses. Los catalizadores de RSC permiten además fabricar moldes intrínsecamente ignífugos al facilitar la producción de mezclas prepoliméricas estables basadas en fenoles y furanos.
Bac2 estima que el mercado potencial mundial para sus nuevos catalizadores de ácidos latentes puede ser como poco de 100 millones de libras esterlinas. La compañía ya ha identificado tres grandes sectores a los que la innovación podría brindar ventajas:
- Durante la fabricación de productos de madera como tableros de fibras de densidad media (MDF), tableros de partículas y contrachapados, se usan temperaturas elevadas para curar la resina que aglutina los materiales y eliminar la humedad. Los catalizadores de RSC reducen el tiempo de curado, reduciendo así el tiempo que debe mantenerse una temperatura elevada. Lo que conlleva una reducción del consumo energético y de los costes.
- En la producción de materiales abrasivos, se reduce la temperatura general del proceso, ahorrando energía y costes.
- En la producción de materiales compuestos por SMC o BMC, que se utilizan en aplicaciones de todo tipo (desde acondicionamientos interiores para el transporte hasta asientos para estadios), los catalizadores de RSC pueden usarse para producir productos intrínsecamente ignífugos con temperaturas más reducidas que antes.
Categoría: Termoplásticos
- Ganadores: MVC (Brasil) y Arkema (Francia)
- Socios: PPE (Francia), Chomarat (Francia), 3B-the fibreglass company (Bélgica) Nombre del producto o proceso: Un innovador concepto de transporte que utiliza una revolucionaria solución basada en una resina de material compuesto termoplástico.
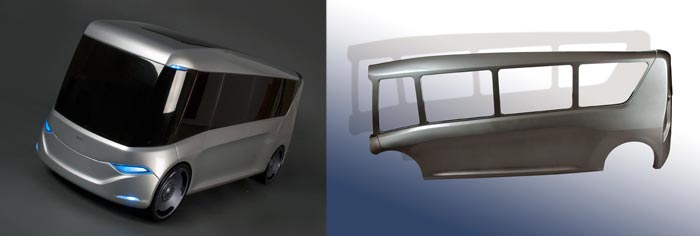
Descripción:
Altuglas ofrece soluciones de material compuesto basado en resinas cuyas innovadoras fórmulas (met)acrílicas son fruto del esfuerzo conjunto de investigación y desarrollo de Arkema y PPE. Dichas fórmulas pueden usarse para producir materiales compuestos termoplásticos (met)acrílicos reforzados con hilos continuos de vidrio, carbono o lino con los mismos procesos y equipos de baja presión que los usados actualmente para producir piezas de materiales compuestos termoendurecibles. Las piezas de materiales compuestos termoplásticos (met)acrílicos resultantes presentan propiedades mecánicas similares a las de las piezas fabricadas con materiales termoendurecibles, pero con las grandes ventajas de ser termoformables posteriormente y reciclables, además de brindar nuevas posibilidades para las combinaciones de materiales compuestos entre sí o de un material compuesto y un metal.
'Proyecto Sofía: Un innovador concepto de transporte': El proyecto desarrolla una nueva tecnología para la construcción de carrocerías de autobús, vagones de tren, caravanas y automóviles de forma sostenible e innovadora. El producto final será un 'kit de montaje' que podrá montarse en pocas horas y sin una gran inversión en herramientas. Se utilizarán diversos tipos de tecnologías, si bien la principal será el nuevo proceso RTM-T, usado para los componentes estructurales de la carrocería. Este proceso de producción con materiales compuestos se basa en el proceso tradicional de moldeo por transferencia de resina ligero (light resin transfer moulding, LRTM), pero utilizará una nueva resina termoplástica de PMMA, desarrollada por Arkema. De ahí la T añadida a sus siglas (RTM-T), que hace referencia a Termoplástico. El material compuesto termoplástico producido con esta nueva resina permitirá producir una estructura principal de carrocería 'reciclable', de menor peso (el PMMA tiene menor densidad que as resinas termoendurecibles usadas normalmente en el RTM), mejores propiedades dinámicas y, en última instancia, una superficie de mejor calidad (muy importante en este sector industrial). Todas las piezas de la carrocería principal tendrán una estructura sándwich, con un núcleo de poliuretano de baja densidad e irán unidas con adhesivos estructurales. Además, el diseño de las juntas ha sido estudiado en profundidad, a fin de mejorar la adherencia de los adhesivos estructurales, haciendo así que el proceso de montaje sea lo más fácil, rápido e intuitivo posible.
Categoría: Materiales multifuncionales
- Ganador: Institut für Textiltechnik (ITA) de la Universidad Técnica de Aquisgrán (Alemania)
- Nombre del producto o proceso: Un material compuesto termoconductor reforzado con fibras.
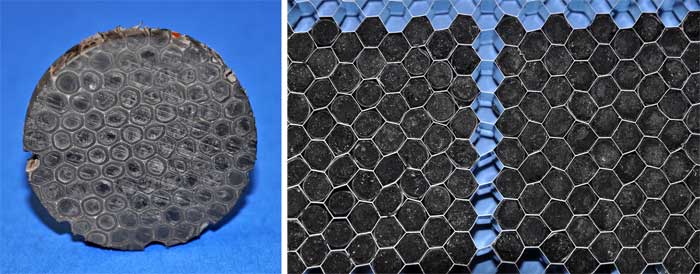
Descripción:
La innovación combina fibras de carbono impregnadas de brea y una resina ermoendurecible para aumentar la conductividad térmica de plásticos reforzados con fibras de 0,4 W/mK a 26 W/mK, especialmente hacia fuera del plano. Las fibras de carbono impregnadas de brea se combinan, protegiéndolas frente al doblado, y se integran en una estructura de nido de abeja. La innovación puede integrarse en áreas seleccionadas de la estructura de nido de abeja, y no necesariamente en todas las celdas. Así, se puede ahorrar dinero y modificar las propiedades locales. Las fibras de las celdas pueden conectarse además con la piel del sándwich de la estructura de nido de abeja para evitar la deslaminación. Además, el flujo térmico se lleva desde dentro del plano a través de la estructura de nido de abeja hasta la otra cara del sándwich, donde se disipa.
Los materiales compuestos se usan cada vez más en aplicaciones que generan calor. Tanto los componentes electrónicos como la propia estructura del material compuesto deben ir protegidos y mantenerse a temperaturas más bajas. Esta innovación puede disipar el calor de sus fuentes o de los componentes en las direcciones deseadas. Así, los componentes metálicos pueden sustituirse por otros más ligeros de plástico reforzado con fibras. La temperatura de uso del sistema de la matriz puede incrementarse, ya que las fibras continuas llevan el calor lejos de su fuente y evitan el sobrecalentamiento.
Se ha construido un prototipo y se ha presentado el invento en la Oficina de patentes alemana de Múnich.
El material compuesto termoconductor reforzado con fibras tendrá aplicación en la dirección fuera del plano en las industrias aeroespaciales, así como de automoción y otros sectores industriales. El invento puede resultar útil allí donde se requiera disipar el calor.
Categoría: Mecanizado y herramientas
- Ganador: Cruing Italy Srl (Italia)
- Nombre del producto o proceso: Una solución de mecanizado para expeler las partículas de polvo calientes producidas durante las operaciones de fresado.
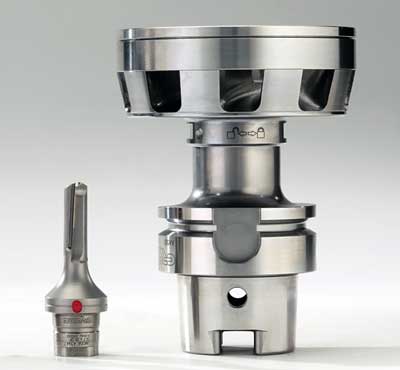
Descripción:
El sistema Aerotech es una solución de mecanizado para expeler por completo las partículas de polvo calientes producidas durante las operaciones de fresado. Refrigerando efectivamente el material y la fresa, se reducen significativamente las temperaturas de mecanizado. Esto permite a los fabricantes de piezas de materiales compuestos optar por el fresado en seco de sus componentes, brindando una alternativa práctica al mecanizado con refrigerantes.
El calor generado durante el ranurado conlleva problemas para la fresa y el material. El fresado húmeda o con refrigerantes resuelve el problema, aunque estos líquidos pueden afectar a la salud humana y los recursos hídricos. Cruing ha sabido ver la necesidad de una solución de fresado en seco refrigerada por aire como alternativa al fresado húmedo, dando lugar al desarrollo del sistema Aerotech.
Todas aquellas empresas que deseen cortar plásticos reforzados con fibras de carbono, sin que haya deslaminación y con un acabado de calidad en los bordes, pueden recurrir al sistema Aerotech.
Muchos de los productos químicos utilizados en la formulación de los líquidos de corte, como biocidas, anticorrosivos, antiespumantes y otras sustancias, pueden tener un efecto negativo sobre el medioambiente. Por otro lado, los líquidos de corte y refrigerantes se asocian a problemas de salud, como erupciones cutáneas, dermatitis, esofagitis, enfermedades pulmonares y cáncer, derivados o bien de su toxicidad o bien de la contaminación microbiana o fúngica.
El calor generado durante el fresado contribuye a reducir la vida útil de las herramientas y afecta negativamente a la calidad de los componentes acabados. Algunos de los materiales usados actualmente en la industria son especialmente sensibles al calor y pueden deslaminarse debido al sobrecalentamiento.
Si no se disipa el calor, este puede pasar a través del electromandril de la fresadora CNC alterando las propiedades de la grasa que lubrica los cojinetes del primero. Esto puede ocurrir a partir de aproximadamente 73 °C y reduce la eficiencia de los cojinetes. Además, puede dañar el electromandril. El sistema Aerotech refrigera con aire la fresa y el material de forma efectiva al retirar las partículas de polvo, que con el fresado adquieren elevadas temperaturas. Así se evita el sobrecalentamiento del electromandril.
Categoría: Edificación y construcción
- Ganador: Owens Corning (Francia)
- Socios: Ademe (Francia), Exel Composites (Bélgica), CSTB (Francia), Goyer (Francia), Compositec (Francia), ENPC (Francia)
- Nombre del producto o proceso: Paneles de fachada de elevada eficiencia energética basados en perfiles de materiales compuestos.
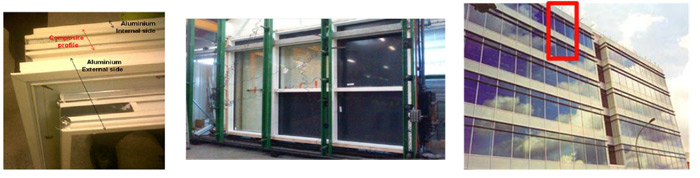
Descripción:
Con el progresivo endurecimiento de las nuevas normativas europeas de aislamiento térmico para el exterior de los edificios (RT 2005-2012), la mejor forma de reducir las necesidades energéticas de estos es el aislamiento térmico de los componentes de la fachada. Los actuales paneles de fachadas, fabricados con perfiles de aluminio con rotura térmica de poliamida integrada no cumplen sino de forma limitada con las normativas. Además, el uso de materiales convencionales da lugar a muros cada vez más gruesos.
Por este motivo, Owens Corning y sus socios estudiaron, diseñaron y planearon la producción industrial de una solución flexible orientada tanto a las nuevas como a las antiguas edificaciones (de menos de diez pisos) a fin de cumplir con la nueva normativa térmica.
La solución integral de paneles COFAHE es el resultado de la estrecha colaboración entre grandes actores industriales, y está compuesta por diversas piezas y materiales. Los perfiles utilizan materiales compuestos para sustituir las roturas térmicas de poliamida y parte del aluminio.
Las principales ventajas de este componente hecho con materiales compuestos son:
- una solución flexible prácticamente lista para usar (panel), que exige cambios mínimos en la tecnología y
maquinaria existentes y ningún cambio estético en el aspecto de la fachada;
- una menor conductividad térmica y un mejor aislamiento, sin sacrificar las propiedades mecánicas, gracias a la combinación de un material compuesto y el aluminio;
- una solución que puede adaptarse en un futuro a fin de responder al previsible endurecimiento de la normativa térmica, al contrario que las soluciones actuales, que ya han tocado techo. Junto con Goyer, OC evaluó el valor que se generaría al sustituir todas las roturas térmicas de poliamida por resina de viniléster reforzada pultrusionada (en este caso, reforzada con fibra de vidrio Xstrand H). El cambio obedece a la mejora en las propiedades mecánicas y el aislamiento térmico.
Además, los constructores podrán aumentar la superficie útil que vendan en el interior de sus edificios, al usar perfiles de materiales compuestos combinados con paneles de aislamiento por vacío extrafinos, en lugar de la lana mineral. En toda Europa, el mercado potencial de los paneles de fachada de COFAHE es de 4-5 millones de metros cuadrados, y está formado tanto por proyectos de reforma de edificios de menos de 28 metros de altura, como por obra nueva.
Categoría: Aeronáutica
- Ganador: Fokker Aerostructures BV (Holanda)
- Socios: Agusta Westland (Italia), Ten Cate Advanced Composites (Holanda), Ticona (Alemania)
- Nombre del producto o proceso: El primer plano de cola de material compuesto termoplástico desarrollado y producido para un helicóptero.
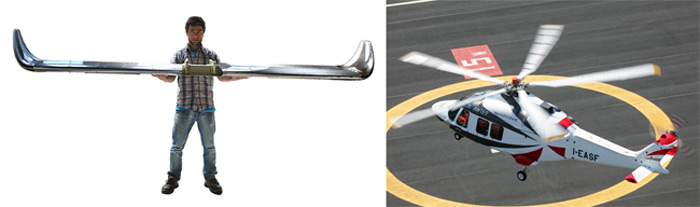
Descripción:
La innovación presenta un plano de cola horizontal termoplástico completo con una caja de torsión multilarguero en una sola pieza integrada, para el helicóptero AgustaWestland AW169. Esta pieza principal portadora de carga mide tres metros de largo y va de extremo a extremo. Está formada por cuatro preformas fundidas juntas a presión. Los bordes de ataque y de salida, de termoplástico y sustituibles, van unidos a la caja de torsión. Los bordes de ataque están hechos de láminas termoplásticas compactadas, soportados por varias costillas delgadas conformadas por presión. Los termoplásticos se han usado en los bordes de ataque por sus buenas propiedades frente a impactos. Los bordes de salida
están hechos de material laminado termoplástico termodoblado, soportados por costillas conformadas por presión. Todos los componentes están fabricados con materiales TenCate Cetex a base de fibras de carbono/sulfuro de polifenileno. Las robustas aletas curvadas han sido fabricadas con piezas preimpregnadas de carbono/epoxi laminadas convencionales. El nuevo diseño ha supuesto una reducción del 15% del peso para AgustaWestland en comparación con el anterior diseño de plano de cola de material compuesto.
El valor de la innovación reside fundamentalmente en la reducción del peso y los costes. La reducción del peso conlleva un menor consumo de carburante y menos emisiones de NOx y CO2. Esta solución más ligera ha sido posible gracias a la dureza del material termoplástico y al robusto y sólido diseño de la caja de torsión multilarguero. El diseño resulta asequible gracias a la integración de preformas sencillas que conforman el principal elemento estructural de la caja de torsión, de una sola pieza.
AgustaWestland espera que el nuevo AW169 sea todo un éxito en el mercado de aviación civil y que la empresa supere cómodamente los 500 pedidos. Este nuevo concepto podría aplicarse también a otros planos de cola. La idea de multilarguero conformado por varias preformas es también adecuada para otros productos, como los paneles del suelo de los aviones.
Categoría: Automoción
- Ganador: ECM (Francia)
- Socios: Peugeot Citroën Automobile (Francia), PPE (Francia), Cedrem (Francia)
- Nombre del producto o proceso: Estructura de material compuesto autoportante para vehículo eléctrico urbano ligero.
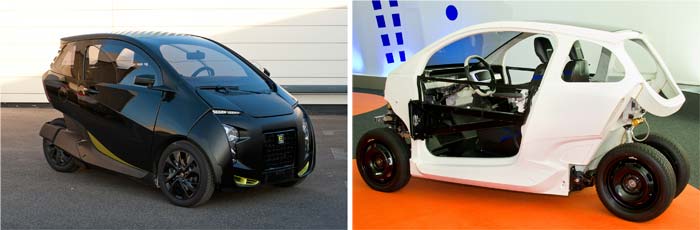
Descripción:
La innovación consiste en una estructura de material compuesto autoportante completa para un vehículo eléctrico urbano ligero, diseñada y fabricada con resina termoendurecible y refuerzo de fibra de vidrio. La estructura sustituye a la tradicional carrocería de acero, con el mismo comportamiento mecánico y una considerable reducción del peso.
El prototipo cumple con los criterios de viabilidad industrial. En esta fase, el uso del refuerzo de fibra de vidrio consigue reducir entre un 30% y un 40% el peso en comparación con una estructura de acero equivalente. Según los cálculos, el posterior desarrollo usando fibra de carbono podría reducir aún más el peso.
Tras una primera fase 'convencional' con acero como material principal de la carrocería, los objetivos de la segunda fase de desarrollo fueron:
- diseñar y fabricar una estructura de material compuesto autoportante con fibra de vidrio mediante RTM;
- lograr un proceso de producción industrial que permita producir diariamente de 50 a 100 vehículos;
- minimizar los costes de inversión, producción y montaje limitando el número de piezas producidas e integrando aspectos funcionales en las piezas desarrolladas;
- reducir el peso sin perder de vista el nivel de prestaciones estáticas y dinámicas.
Las principales ventajas de la innovación son: reducción del peso con un coste asequible para la industria de la automoción; reducción de las emisiones del vehículo debido a la reducción de su peso; diseño de piezas del vehículo que integran aspectos funcionales; reducción considerable del número de piezas que conforman el vehículo, y ahorro en costes de inversión y montaje.
Categoría: Energía eólica
- Ganador: SchäferRolls Gmbh & Co KG (Alemania)
- Socios: Institut für Verbundwerkstoffe Gmbh (IVW), MWN Niefern Maschinenfabrik Gmbh (Alemania)
- Nombre del producto o proceso: Un eje de material compuesto de fibra de carbono bobinada con pared gruesa de más de 8,5 metros de altura y casi un metro de diámetro.
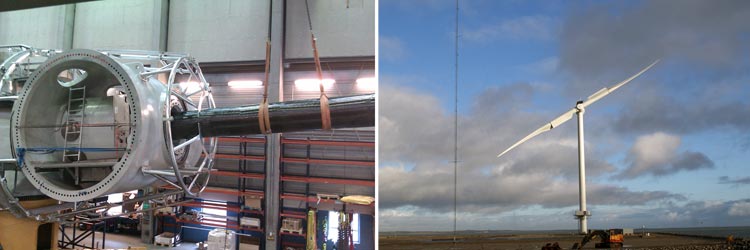
Descripción:
El eje de material compuesto de fibra de carbono bobinada con pared gruesa (unos 80 mm) ha sido diseñado para aguantar cargas de par extremas en el grupo motopropulsor de una turbina eólica. Se fabrica en unas 40 horas, con una resina epoxi personalizada que brinda una larga vida útil.
El eje es flexible al doblado, para reducir las cargas provocadas por las tolerancia del procesos, y ha sido diseñado para soportar una elevadísima carga de par, de ahí su nombre: 'FlexShaft'. Ello ha sido posible gracias a un innovador diseño y al inteligente uso de la anisotropía del material compuesto. El innovador y ligero árbol de torsión FlexShaft puede transferir una carga de par de varios miles de kNm dentro de un espacio con un diseño geométrico limitado. Controlar la reacción exotérmica de varios cientos de kilos de
resina epoxi durante varias horas en el proceso de producción es una tarea que pocas empresas especializadas pueden llevar a cabo. Para ello, se desarrolló un nuevo método que permitiera colocar in situ los elementos de conexión necesarios entre el eje de plástico reforzado con fibras de carbono y las bridas de acero durante el proceso de producción, permitiendo fabricar sin reelaborar y mejorando la calidad general del proceso y la transferencia de carga.
Tras una fase de desarrollo de dos años, en septiembre de 2012 comenzó a funcionar en Dinamarca el primer prototipo a escala real en la nueva turbina eólica marina de Envision, de propulsión directa, con dos palas y una potencia de 3,6 MW.
El mercado potencial es de unos 100 millones de euros.
Categoría: Deportes y tiempo libre
- Ganador: Zodiac Recreational (Francia)
- Socios: Dehondt – Flax Technic (Francia), Fimalin (Francia)
- Nombre del producto o proceso: Nuevas generaciones de embarcaciones semirrígidas con diseño ecológico.
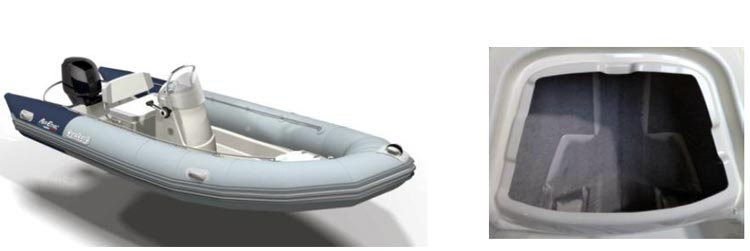
Categoría: Premio especial
- Ganador: Grupo BMW (Alemania)
- Nombre del producto o proceso: LifeDrive - La primera carrocería del mundo diseñada y construida específicamente para la producción en serie de vehículos eléctricos.
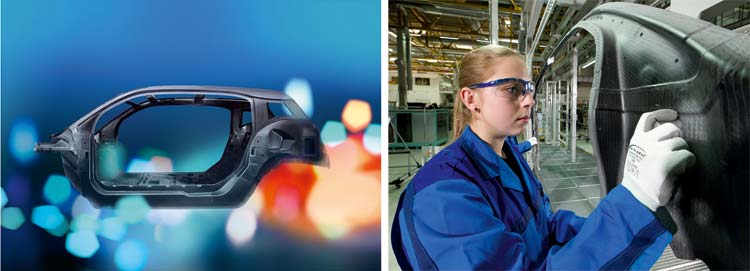
Descripción:
A pesar de que los fabricantes de automóviles de todo el mundo se apresuran por lanzar modelos eléctricos, el concepto LifeDrive de BMW constituye la primera carrocería construida específicamente para vehículos eléctricos. A principios de los años 30 del siglo XX, los avances en fresado de metal y el deseo de automóviles más ligeros y potentes dio a luz a una innovación que dominaría la producción mundial de vehículos con motor durante décadas: la carrocería monocasco integral. Tres cuartos de siglo después, en los albores de la era del vehículo eléctrico, el equipo de BMW vuelve a afrontar el reto de reducir el peso del vehículo: esta vez con el fin de acoplar la batería de un motor eléctrico. El resultado de sus investigaciones es el desarrollo de la primera carrocería del mundo específicamente diseñada y construida expresamente para la producción en serie de vehículos eléctricos: el concepto LifeDrive.
Al contrario de lo que ocurre con los vehículos con una carrocería monocasco, la arquitectura LifeDrive consta de dos unidades funcionales independientes. El modulo superior Life consta básicamente del habitáculo para los pasajeros, ligero y extremadamente resistente, hecho de plástico reforzado con fibras de carbono. Este innovador concepto no solo compensa el peso adicional de la batería, sino que además reduce el centro de gravedad del vehículo, haciendo que resulte más dinámico en la conducción. Pero el diseño ligero no es la única ventaja que aporta LifeDrive. El habitáculo de pasajeros de fibra de carbono es excepcionalmente rígido y robusto. Además, en el caso del BMW i3, no hay túnel que ocupe espacio en el centro del vehículo, ya que todos los componentes de potencia se alojan en el módulo del motor. Así, los pasajeros pueden disfrutar de un asiento corrido, con la sensación de un espacio más amplio.
Hasta 2020, BMW prevé una cuota de mercado de entre el 4% y el 8% en el sector de vehículos eléctricos (con batería e híbridos con enchufe). Además, junto con el gobierno alemán, BMW pretende lograr el objetivo de un millón de vehículos eléctricos circulando por las carreteras alemanas de aquí a 2020.
Aunque el concepto LifeDrive, con su habitáculo de pasajeros de plástico reforzado con fibras de carbono, es un diseño independiente expresamente ideado para el BMW i3 y el BMW i8, otras series de modelos podrán también beneficiarse a largo plazo de la experiencia con este material desarrollada por BMW.