La contaminación en aceites hidráulicos
Incluso el aceite nuevo contiene más de 75.000 partículas sólidas > 5 µ por 100 ml. Cuando estas partículas contaminantes circulan a gran velocidad y presión ocasionan desgaste por abrasión, fatiga y erosión.
La condensación producida por cambios de temperatura y escapes en sistemas de refrigeración, contaminan el aceite con agua.
La combinación de partículas de metal, que actúan como catalizadores, con agua y oxigeno a temperaturas relativamente altas, aumentan y aceleran la oxidación del aceite.
Durante este complejo proceso de oxidación, la polimerización produce estructuras moleculares muy pegajosas, que normalmente denominamos “resinas”.
Debido a su tamaño microscópico, no son eliminadas por los sistemas tradicionales de filtración y por su estructura pegajosa y efecto corrosivo, afectan directamente a la eficacia y seguridad del sistema hidráulico.
El aceite contaminado causa el 80 % de los fallos y paradas de las máquinas.
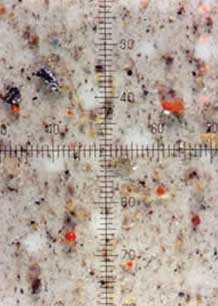
Partículas sólidas
Las bombas y servo-válvulas están calibradas para permitir el paso del fluido de 1-10 µ y como resultado de esto, son altamente sensibles a partículas sólidas. Los fabricantes de este tipo de elementos, estipulan que el aceite debe estar purificado a un nivel mayor de NAS 6 o ISO 15/12, para evitar problemas y alargar la vida de estos componentes.
Como ejemplo por una bomba con un caudal de 200 l/min. y aceite contaminado a (NAS 12 ó ISO 21/18), circulan más de 3.000 kg. de partículas sólidas por año. Por la misma bomba con aceite limpio a (NAS 4 ó ISO 13/10) fluirían tan solo 6 kg.
Agua
El agua causa oxidación en el aceite. Cuanto más contaminación, más aumenta el grado de acidez en el aceite (T.A.N.). Cuando la acidez alcanza niveles de 2,00 mg KOH/g, se requerirá un cambio de aceite para prevenir cualquier desperfecto en la maquinaria.
Las tolerancias en la maquinaria de hoy día son generalmente muy reducidas. Mover partes produce presión y aspiración; la humedad se expandirá considerablemente (a 70°C hasta 1/5,000) y causará diminutas explosiones en las superficies. Esto producirá nuevas partículas abrasivas y como resultado la superficie de los componentes perderán su capa protectora de lubricante.
El agua reduce la vida efectiva de los sistemas hidráulicos en más del 50%.
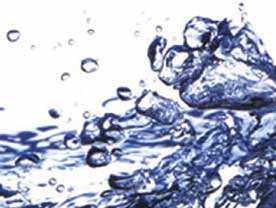
Resinas – medios oxidantes
Sin embargo, su presencia puede acarrear consecuencias muy graves, por ejemplo:
•1. Los calentadores de aceite se vuelven menos efectivos:
Depósitos de fango se adhieren a la superficie de la tubería, formando una capa pastosa. Esto reduce la eficiencia del intercambio de temperatura del aceite ocasionando que aumente y no sea igual a la asignada en la válvula.
•2. Obstrucción en los filtros de la línea principal:
El fango es una sustancia resinosa pegajosa, que bloquea rápidamente los filtros.
•3. La enfermedad de lunes:
A temperaturas normales de operación, la mayoría de las resinas se encuentran disueltas en el aceite. Cuando el aceite se enfría, las resinas se vuelven extremadamente viscosas. Al volver a poner en marcha la máquina, las resinas tardan más tiempo en disolverse ocasionando excesiva presión diferencial.
Por esto, no es sorprendente, que la máquina precise ajustes, aún después de estar en marcha durante bastante tiempo.
•4. Las válvulas se bloquean y no trabajan adecuadamente.
La presencia de resinas incrementa el coeficiente de fricción en hasta 5-6 veces más de su valor nominal. En algunos casos taparán completamente el pistón.
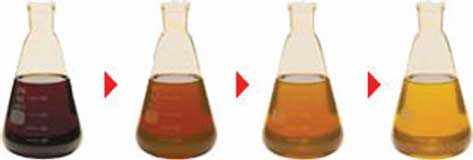
“Mi máquina ya tiene varios filtros: ¿por qué el aceite no está limpio?”
La solución
Por el hecho de que éstos filtros están conectados al flujo o corriente principal, siempre representan un compromiso entre la eficiencia en la filtración y “el no molestar”. La función primaria de cualquier sistema hidráulico, es desplazar el aceite a uno o varios cilindros eficientemente. En este proceso los filtros de la corriente o flujo principal siempre representan un obstáculo.
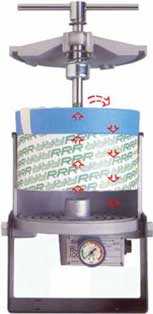
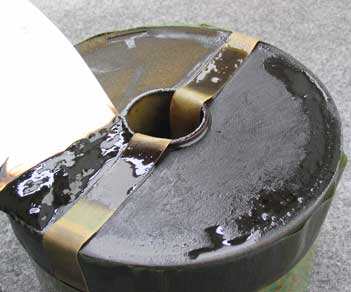
Los resultados de este sistema de filtración se demuestran con un solo filtro, que es capaz de eliminar partículas sólidas hasta 2 µ absolutas, agua, fango, resinas y residuos oxidantes.
El elemento filtrante concentra las fuerzas cuando el aceite fluye a través de 114mm de material, pasando por tres etapas de diferente densidad. Las partículas más grandes son retenidas en la parte superior del elemento, las pequeñas (100-10µ) en la 1a etapa. Y las más pequeñas (< 10µ) en la etapa más comprimida. Este proceso es progresivo, obteniendo una alta capacidad de retención de partículas. Si rascamos con una espátula sobre la superficie del elemento filtrante después de su sustitución, observaremos la enorme cantidad de resinas que a retenido el filtro y que gracias a la efectividad de Triple R ya no circulan por el sistema hidráulico
La implantación de una unidad de filtrado Triple R en una inyectora, garantizará cuadriplicar la vida del aceite, además incrementaremos notablemente la durabilidad de bombas, válvulas y filtros de alta presión. Todo esto se verá reflejado en un descenso en paros de máquina, mano de obra y perdidas de producción.
La firma japonesa Triple R es referente mundial en micro-filtración de aceites hidráulicos, con presencia en los cinco continentes.
A nivel nacional EPA lleva más de 15 años ayudando a solucionar problemas con la contaminación del aceite a un gran número de empresas, entre las que se encuentran las firmas más importantes en inyección de plastico. Gracias a este producto revolucionario con más de 35 años de historia, EPA ha tomado la delantera en tratamiento y purificación de aceites, encargándose de la distribución e instalación de los equipos Triple R en maquinaria de inyección de termoplástico.