Moldeo por soplado: equipos y accesorios
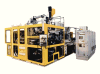
La tecnología de moldeo por soplado ofrece una serie de ventajas sobre otros procesos de grandes volúmenes de producción, como la inyección. Y presenta, al mismo tiempo, factores de coste favorables. El procedimiento utiliza plásticos con un peso molecular más elevado, por lo que es posible obtener paredes más delgadas y resistencias más elevadas a igualdad de peso.
1 - Funcionamiento del moldeo por soplado
En general, todos los procesos de moldeo por soplado consisten en obtener una preforma, que es un elemento tubular o en forma de tubo de ensayo, fijarla dentro de un molde de soplado y, a una temperatura específica de cada material para que tenga consistencia suficiente, inyectar aire en su interior para que se adapte a las paredes del molde, permitir su enfriamiento bajo presión y abrir el molde para extraerla cuando ha alcanzado suficiente consistencia.
1.1 - Conceptos básicos del proceso
El moldeo por soplado ofrece una serie de ventajas sobre otros procesos de gran serie, como la inyección, en tanto que permite contrasalidas, posibilidad de variar el espesor de pared y, en función de las bajas presiones utilizadas (0,2-1,0 MPa), bajas tensiones residuales. Presenta, al mismo tiempo, factores de coste favorables.
El proceso permite utilizar plásticos con un peso molecular más elevado que, por ejemplo, la inyección, por lo que es posible obtener paredes más delgadas y resistencias más elevadas a igualdad de peso, y mejor comportamiento a los agentes ambientales y productos químicos que producen fisuración por tensiones.
Básicamente, el proceso consiste en obtener una preforma (que tiene el aspecto de un tubo de ensayo o un tramo de tubo), situarla en un molde hueco en dos piezas que pinza o no uno o ambos extremos, inyectar aire a presión dentro de la preforma caliente para que conecte con las paredes del molde y tome su forma, permitir su enfriamiento y abrir el molde para retirar la pieza.
Los factores que inciden en la selección de los distintos materiales utilizables o de los procesos posibles de moldeo por soplado son los requisitos de rendimiento, tamaño y forma de la pieza, cantidad a fabricar y consideraciones de coste. Cada proceso presenta ventajas e inconvenientes que deben tenerse en cuenta, al tiempo que debe considerarse la adecuación de cada material al proceso a utilizar.
1.1.1 - Extrusión
La preforma se produce en este proceso mediante el calor generado por las fuerzas de cizallamiento del husillo al pasar por la cámara. Se obtiene una preforma contínua o, según el tamaño de la pieza, se transfiere a un acumulador. En este último caso, el flujo de la preforma es cíclico.
Para reducir la historia térmica de la preforma, el diseño del acumulador debe asegurar que el primer material que haya entrado sea el primero en salir cuando el émbolo vacía la cámara, que debe quedar casi vacía a cada carrera.
Cuando sale la preforma o tubo de la hilera y desarrolla una longitud predeterminada, un molde de cavidad partido se cierra alrededor y pinza un extremo. El proceso continúa como se ha descrito antes.
Para inyectar el aire comprimido se emplean varios sistemas. Uno puede ser a través de la hilera, otro a través de una aguja de soplado sobre la que cae la preforma, o con agujas que pinchan la preforma.
La distribución del espesor de pared se efectúa mediante la programación de la preforma, relación de soplado y configuración de la pieza. El sistema de cierre varía en función de ésta, pudiendo ser en "L", que tiene la línea de partición a 90 respecto al eje de extrusión, en "T" en línea con el mismo o en sobrepuente, cerrándose los moldes hidráulicamente o mediante rodillera.
1.1.2 - Inyección
Este proceso se efectúa en tres etapas. En la primera se inyecta el fundido en un molde para producir la preforma, que tiene el aspecto de un tubo de ensayo con la boca roscada, la cual será parte del acabado final y precisa una tolerancia estricta.
Figura 1 Máquina de extrusión soplado moldeando simultáneamente dos barriles, en una línea en que se realizan sucesivamente las operaciones de corte, moldeo y montaje de fondos, soldadura y verificación con un sólo operador
La preforma se transfiere mediante una barra de núcleo al molde de soplado, donde toma la forma por soplado y se enfría en contacto con la pared fría del molde, habitualmente de aluminio.
En la tercera etapa, la barra de núcleo transporta a la pieza moldeada a la zona de extracción. Algunas áquinas tienen una cuarta etapa, que se utiliza para acondicionar térmicamente la preforma antes del soplado, u otra cuarta etapa antes de la extracción para operaciones secundarias como estampación en caliente o etiquetado. Cuando se trata de grandes volúmenes, el ciclo lo determina el tiempo necesario para inyectar la preforma. Este proceso se utiliza para fabricar contenedores que tengan tolerancias estrictas, cuellos roscados, aberturas de boca grandes, mangos sólidos y formas muy estilizadas, caracterizándose por una buena distribución del material, sin precisar acabado o recortes adicionales.
Una variante del proceso es el moldeo por desplazamiento, en que se deposita una cantidad determinada de resina fundida en una copa con la forma externa de la preforma y se introduce en ella una barra de núcleo. La preforma moldeada por desplazamiento se transporta mediante la barra al molde de soplado, en el que continúa el proceso según lo descrito. La ventaja de esta variante es la reducción de las tensiones a que se somete el fundido.
1.1.3 - Estirado
Desde principios de los años 70 se emplean botellas para detergentes en PP moldeadas por extrusión-estirado-soplado, pero ha sido el uso de botellas de PET para bebidas carbónicas lo que ha hecho desarrollar las técnicas de estirado.
Están ampliamente reconocidas las mejoras que la orientación molecular o estirado biaxial confiere a las botellas, técnica que permite el uso de grados inferiores de material o menores espesores de pared mediante un control preciso, con reducción del coste en ambos casos.
El proceso permite la mejora de las propiedades físicas, ópticas y de barrera, así como la eliminación del desperdicio en la base y boca que se produce en otros procesos de soplado.
El proceso se inicia con una preforma inyectada, que se atempera con un perfil térmico de precisión, se estira y se moldea a la forma final. Debido al estirado y flujo a temperatura controlada, las moléculas en la pared de la botella se orientan biaxialmente, de ahí el término orientación molecular. Las relaciones de estiraje en las botellas de PET son de 3,8 en dirección circunferencial y 2,8 en la axial.
Existen dos variantes del proceso, una mediante equipos de dos etapas, en que la preforma se moldea y se reacondiciona térmicamente antes de pasar al molde de soplado y otra, más moderna, en que se efectúa en forma contínua en una sola máquina.
1.2 - Procesos de moldeo por soplado
Cada uno de los procedimientos citados tiene aplicaciones específicas, utilizándose en función de éstas y de las características de los materiales para los que es adecuado.
Figura 2 Moldeo simultáneo con conformado y mecanizado posterior de las aberturas
La descripción que sigue orientará también al lector sobre los mercados a que va dirigido cada proceso.
1.2.1 - Extrusión-soplado
Esta técnica se inició en Europa hacia 1940 para la coextrusión continua de botellas de PVC y en los EEUU para fabricar botellas de LDPE. Este último, muy versátil para su transformación, se utilizaba haciendo una preforma en una variedad de procesos, incluyendo acumuladores, extrusión contínua y husillos recíprocos.
La fabricación en gran escala, con una multitud de moldes de soplado montados en un caroussel, con extrusión contínua de las preformas, se dedicó a productos tales como lejías y detergentes, para los que la rotura de un envase de vidrio plantea problemas domésticos. El siguiente desarrollo fueron las botellas para leche que dieron lugar al desarrollo de máquinas que utilizan HDPE, con husillo recíproco y moldes estacionarios, que se encuentran hoy en el mercado. Otras son las de cabezal doble, con mayor velocidad, de las que existen ya unas 30.000 funcionando.
Actualmente, las máquinas realizan todas las funciones de acabado, incluyendo el etiquetado en el molde, que dispensa de post-tratamiento antiestático e incluso permite reducciones de peso. El procedimiento ha experimentado crecimientos de alrededor del 10% en los últimos 20 años.
1.2.2 - Inyección-soplado
Esta técnica permite el uso de PE cristal y un perfecto acabado de la boca roscada, por lo que ha sido adoptada para los frascos de perfumería y farmacia, aprobados por la FDA. Sus limitaciones son las siguientes:
1. Para fabricar piezas de forma oval o cuerpos huecos grandes se precisa conformar la barra de núcleo de modo que se obtenga un grueso inyectado de material diferenciado según el estirado posterior de cada área. Aunque el sistema es efectivo, no lo es tanto como la programación de preforma en extrusión-soplado.
2. Las preformas para contenedores de gran volumen obligan a utilizar inyectoras bastante voluminosas y con una gran fuerza de cierre.
3. La relación cuello a cuerpo viene limitada por el hecho que se debe extraer al final la barra de núcleo y, por tanto, debe ser de menor diámetro que la rosca y, si la barra es demasiado larga crea problemas de manipulación.
4. Los costes de utillaje son más elevados que los de la extrusión-soplado, por lo que se necesitan volúmenes de producción elevados para que el proceso sea rentable.
5. Con algunas resinas y tamaños, los ciclos son más lentos que para los mismos en extrusión-soplado.
1.2.3 - PET con orientación biaxial
La industria de bebidas carbónicas ha buscado una botella adecuada de plástico y, hacia 1970, se produjeron en los EEUU botellas de acrilo-nitrilo que satisfacían al consumidor. Pero la FDA consideró que los restos de monómero nitrilo o vinilo podían ser carcinogénicos y se excluyeron tanto el acrilonitrilo como el PVC de las botellas de este tipo, aunque actualmente seha reducido el campo de estas limitaciones.
DuPont desarrolló para ello el PET biorientado, pero no se podía utilizar para extrusión-soplado debido a su baja resistencia del fundido, por lo que se inyectaban las preformas y se mantenían en el molde hasta su enfriamiento. Posteriormente se calentaban a cerca de su temperatura de transición vítrea (93 C) y se estiraban en el molde de soplado provocando la biorientación. Las máquinas eran de tipo rotativo.
El procedimiento de un solo paso lo desarrolló Nissei en Japón y el lector puede encontrar una amplia descripción del proceso de acondicionamiento directo del PET en la pág. 26 del n 26 de Plásticos Universales. Aoki presentó en la Plast’94 la nueva máquina que permite el moldeo de PEN y de PET tanto cristalino como amorfo, con secado del material en la misma máquina, que esperamos describir en un próximo número.
1.2.4 - PVC con orientación biaxial
El envase de PVC ha dominado en Europa, durante 20 años, el mercado de botellas transparentes para agua mineral y otros líquidos que requieran esta cualidad. La búsqueda de una reducción de costes, en una producción de millones de botellas, no pasa tanto por ahorros en la mano de obra o en la amortización del equipo, sino en el coste del material, que está presente en cada botella.
Desde 1975 se dispone de un proceso de un sólo paso, desarrollado por Beckum, por el que es posible biorientar el PVC. Sus principales ventajas son:
1. Mayor transparencia que la obtenida por extrusión-soplado
2. Del 20 al 30% de reducción en peso por la mejora de cualidades mecánicas.
3. No es necesario aditivar la resina con modificadores de impacto, lo que permite una reducción de coste de la materia prima.
Se ha verificado que la orientación del PVC produce un frasco con mejores propiedades de barrera, por lo que se abren nuevas aplicaciones para este procedimiento.
1.2.5 - Coextrusión
La coextrusión de varios materiales entró en la industria del envasado a finales de los 70’s, con el recubrimiento de frascos en PP o PE con una delgada capa de poliamida, que confiere un acabado vítreo, no requiere tratamiento antiestático y es virtualmente a prueba de manchas. La aceptación por la industria cosmética representó el inicio de la coextrusión-soplado.
Se utilizan poliolefinas como materiales de barrera y poliamidas para conferir resistencia química, así como alcohol de vinil-etileno para productos alimentarios. Cuando se trata de unir dos materiales no compatibles, se emplean adhesivos intermediarios. En la pág. 62 del n 32 de Plásticos Universales hay una amplia monografía sobre la selección de materiales para estos procesos y su comportamiento en ante distintos productos.
El proceso ha permitido recuperar para el soplado al acrilonitrilo, por su superior resistencia química a determinados productos agresivos. El programa Selar de DuPont no es una coextrusión, sino un aditivo que multiplica la impermeabilidad de las poliolefinas a los hidrocarburos.
1.2.6 - Moldeo por soplado industrial
El soplado de contenedores mayores de 25 litros difiere de los procesos clásicos debido al problema que representa el estiraje de la preforma por su elevado peso. Los contenedores actuales de 1 m han sido objeto de un reportaje en esta revista en el n 31, así como la fabricación de depósitos para gasolina que, iniciada en Europa, ha entrado ya en los EEUU, donde es obligatoria una capa de barrera fluorada de los tanques en HDPE.
Se desarrollan continuamente nuevas aplicaciones para este proceso. Un ejemplo son las tubuladuras de admisión, en que el refuerzo con fibra de vidrio ha obligado a desarrollar sistemas sofisticados para evitar el pinzamiento de las paredes, que dejaría a las zonas pinzadas sin continuidad de la fibra estructural.
2 - Capacidades huecas sopladas
Los requisitos de barrera para cumplir las necesidades de los envases varían con el producto a contener. Debe hacerse notar que muchos productos sensitivos al oxígeno se llenan en caliente o se recalientan. El éxito de las botellas para bebidas carbónicas no hace olvidar que quedan muchos mercados de gran volumen en que el sistema puede aplicarse, como los de:
1. Envases asépticos, tales como jugos y otros.
2. Aliños para ensalada para verter o extraer con cuchara.
3. Salsas como catsup o de barbacoa.
4. Alimentos para niños.
5. Otros productos cosméticos y farmacéuticos.
6. Productos químicos e insecticidas.
Hay tres métodos básicos para mejorar las propiedades de barrera de un frasco rígido de plásticos. El primero es mejorar las propiedades de un sólo polímero o copolímero utilizado como monocapa. El segundo es colocar un recubrimiento de barrera sobre o dentro de una capa monopolimérica. El tercero es emplear varios polímeros distintos en una estructura multicapa en la que cada uno realiza una función específica.
2.1 - Monocapa
El desarrollo de monocapas para envasar productos sensitivos al oxígeno no ha tenido, hasta ahora, éxito comercial.
Tanto Eastman como Goodyear han desarrollado copolímeros de barrera de PET, pero en unos casos se han obtenido estas cualidades en detrimento de otras, como resistencia al impacto o a la fluencia y, en otros, el precio es demasiado elevado.
Es poco probable que en los próximos años se disponga de una monocapa PET de barrera a un precio económico.
2.2 - Recubrimientos
El concepto de recubrimiento es muy antiguo. Muchos de los materiales flexibles de envase iniciales y aún en uso, como celofán, poliéster o PP orientado, se usan con recubrimiento de PVDC y este procedimiento se considera hoy uno de los más adecuados para mejorar las propiedades de barrera de contenedores rígidos monocapa.
Figura 3 Variedad de formas que pueden realizarse por soplado
Existen varios inconvenientes, principalmente la adhesión. El coste de las líneas de recubrimiento de alta velocidad es elevado y resulta difícil obtener una barrera adecuada con una sola pasada.
Habitualmente se utiliza el recubrimiento por rodillo, inmersión o pulverizado del exterior de la pieza. En los EEUU se intentó recubrir las preformas, con el propósito de biorientar el recubrimiento, pero el exceso de adelgazamiento de la capa de PVDC, problemas de adherencia y la lentitud de las líneas han hecho poco popular al proceso.
Pese a todo, se trata de un método comercialmente disponible que mejora, hasta un punto, las propiedades de barrera y que progresará con el desarrollo de nuevos recubrimientos.
2.3 - Multicapa
El factor crucial para el éxito de este procreso fué el desarrollo de técnicas de extrusión que permiten fabricar peículas de 5 a 7 capas, con una excelente distribución de espesores coaxiales y con espesores de pared unitaria menores de 0,03 mm. Esto permite el uso de materiales caros de barrera o recubrimiento de alta calidad a un precio comercialmente aceptable.
Las ventajas son obvias y, mediante combinaciones adecuadas de material se obtienen las siguientes:
* Excelentes propiedades de barrera contra gases como nitrógeno, dióxido de carbono y aire, así como respecto a agua y vapor.
* Resistencia a la transmisión de aromas.
* Protección contra la radiación UV (baja)
* Mayor resistencia.
* Peso ligero.
* Superficies brillantes y resistentes al rayado.
* Resistencia conra medios agresivos.
* Barrera contra disolventes.
* Impresión fácil.
* Prevención de cargas estáticas.
La tecnología de extrusión ha alcanzado un nivel que hace posible reprocesar del recorte de coextrusionado, molido y utilizado como capa independiente. Lógicamente, esto ha llevado al desarrollo de productos en que una parte importante del espesor de pared es material recuperado.
Lo más corriente es disponer la capa de barrera en la parte central de la multicapa. El uso de material recuperado en la capa externa es una opción del cliente, aunque es una técnica muy empleada el uso de 6 capas en que la penúltima es reciclado.
2.4 - Materiales de barrera
Los principales materiales actuales de barrera son el PVDC, el EVOH, EVA y PA. Los preferidos son los dos primeros, aunque el PVDC es difícil de reciclar debido a su sensitividad térmica.
La higroscopicidad del EVA limita severamente su uso pese a su excelente capacidad de barrera. Por su parte, las poliamidas tienen propiedades superiores para algunos disolventes y aromas.
Dada la limitación de espacio, remitimos nuevamente al lector a la monografía de Pierre Chomon, publicada en el n 32 de esta revista, para un más amplio conocimiento del comportamiento de las combinaciones de películas multicapa usadas en el embalaje que, lógicamente, difiere poco cuando se trata de envases.
3 - Máquinas de moldeo por soplado
El material a transformar y el tamaño de la pieza, así como otros requisitos tales como precisión, transparencia y cualidades de barrera determinan en gran medida el tipo de proceso a utilizar y la estructura de la máquina y sus accesorios.
3.1 - Máquinas de extrusión-soplado
Con este proceso se producen grandes piezas utilizando básicamente poliolefinas y PVC. Las poliolefinas suelen precisar un husillo de tres etapas, en las que la primera hace pasar rápidamente el material a la segunda, donde se comprime para generar calor y extraer el aire contenido en la resina y en la tercera se asegura un calentamiento y alimentación regulares al cabezal de extrusión.
Las piezas de gran tamaño se suelen fabricar con HDPE de alto peso molecular, que tiene una viscosidad del fundido muy elevada que dificulta su procesado con equipo normal, obligando a aumentar la potencia y reducir la producción. Para superar estos inconvenientes se utiliza un conjunto de cámara ranurada y husillo de compresión cero. Las ranuras se sitúan sólo en el tramo de alimentación de la cámara, que tiene una sección mayor que el resto y proporciona un efecto de carga para forzar al material hacia el cabezal, sin que el husillo cree contrapresión. La temperatura generada en esta zona se aumenta eléctricamente en los tramos siguientes y debido al bajo cizallamiento del material, éste puede extruírse a baja temperatura, aumentando la consistencia de la preforma.
Figura 4 Máquina de doble estación para capacidades de 30 litros
El sistema no puede emplearse en plásticos sensitivos térmicamente, como el PVC, para el que se han desarrollado extrusoras de doble husillo o planetarias que generan producciones elevadas a temperatura controlada.
El plástico, fundido a baja temperatura de modo que la preforma sea autoportante, entra lateralmente en el cabezal de extrusión desde el que fluye verticalmente la preforma. El cabezal puede ser del tipo convergente, de más fácil control, en que se regula la cantidad de material en la salida cónica variando mediante programación electrónica la distancia a la boca de un mandrín interno también cónico. El microprocesador permite, por ejemplo, ajustar así el espesor en no menos de cien puntos a lo largo de una preforma de 30 cm.
Cuando el tamaño es mayor, se utilizan cabezales de tipo divergente que hacen que la preforma se expansione hacia el exterior al extruirla. En estos cabezales, tanto el mandrín como la boca tienen la forma de un tronco de cono invertido.
Para eliminar la línea de soldadura que se forma donde se junta la corriente de fundido, se usan adaptadores en que el fundido pasa alrededor de dos o más patas delgadas que soportan el mandrín y gira de modo que una corriente solapa y refuerza a la otra. De este modo puede procesarse PVC y otros materiales térmicamente sensitivos sin crear problemas en las líneas de soldadura.
Las grandes piezas industriales requieren un acumulador a pistón hidráulico porque, si se utilizase extrusión contínua, el peso de la preforma la deformaría durante el tiempo necesario para producirla. Cuando se ha completado la cantidad necesaria de fundido, el pistón empuja el material, formándose la preforma, a través de un cabezal de regulación como los descritos, en un tiempo mínimo.
Las prensas portamoldes de extrusión-soplado pueden ser de tipo rotativo de eje vertical y usan una preforma extruída de forma contínua, como un tubo, y no cortada individualmente y que los moldes van pinzando en sucesión. Su principal inconveniente es que los tramos de preforma entre los moldes deben reciclarse y que los cuellos de la botella, aunque roscados, presentan una cúpula que debe cortarse en una operación secundaria.
Las prensas rotativas de eje horizontal producen ristras de botellas de forma contínua y éstas se cortan y acaban fuera de la máquina.
Otro sistema de preforma contínua consiste en dos moldes que actúan en lanzadera, con el cabezal situado en el centro y los moldes desplazándose lateralmente de forma recíproca, en la que mientras uno pinza la preforma y se la lleva a su posición lateral, en el otro se ha efectuado el soplado y expulsión de la pieza.
Dado que el transporte de botellas vacías es antieconómico porque su volumen es, básicamente, aire, muchos envasadores deseaban producir las suyas in situ, lo que dió lugar a la extrusión-soplado discontínua, en que se usa un husillo de alimentación intermitente, como en las máquinas de inyección. A la salida de la extrusora suele haber un colector que reparte el material a varios cabezales de preforma, bajo los que se sitúan los moldes. La colocación de la aguja de soplado en el centro del cabezal de preforma permite obtener cuellos de acabado calibrado.
3.2 - Máquinas de estirado-soplado
Las máquinas de estirado-soplado disponen de un sistema mecánico que estira verticalmente la preforma durante el soplado para producir botellas con superficie orientada biaxialmente o estirada.
Algunos materiales con suficiente resistencia de la preforma pueden estirarse biaxialmente, como el acrilonitrilo y el PVC,
en máquinas de extrusión-soplado en un sólo paso. El PP tiene una ventana térmica excesivamente grande para que pueda biorientarse rápidamente, por lo que los tiempos de enfriamiento son excesivos. Las preformas de PET, por otra parte, no tienen ninguna resistencia mecánica y no puede utilizarse la extrusión para este material.
3.3 - Máquinas de inyección-soplado
Este sistema es similar al anterior. Se inyecta material sobre una barra de núcleo formándose el cuello de la botella y la bara tiene un diámetro variable para que se acumule mayor o menor cantidad de material a lo largo de la misma. El molde de inyección se abre para permitir transportar la preforma y núcleo a un molde de soplado, en que se produce el envase.
Las ventajas del proceso son que el acabado del cuello es perfecto y que no existe desperdicio que deba reprocesarse. Pueden moldearse plásticos como el PE cristal o el PET que son difíciles de moldear por extrusión-soplado. Los inconvenientes son el mayor coste de los moldes y la limitación de tamaño de las piezas. Tampoco es posible producir mangos incorporados.
Para obtener ciclos importantes se inyectan moldes múltiples de preforma con sus correspondientes núcleos a través de un colector. La puesta a punto del proceso es más difícil que con la extrusión-soplado.
3.4 - Máquinas para coextrusión-soplado
Las diferencias con los equipos descritos para la extrusión soplado radican en el número de extrusoras que entran en funcionamiento, su sistema de coordinación y control y en el cabezal, antes descrito, que permite obtener multicapas con espesor unitario controlado.
La coextrusión es de sobra conocida y las preformas mixtas permiten un manejo muchas veces más cómodo que las de materiales monocapa, pudiendo usar capas que sirvan no sólo de barrera sino también de soporte a las demás.
Una vez obtenida la preforma, el procedimiento sigue los mismos pasos que los descritos anteriormente.
3.5 - Máquinas de inyección-estirado-soplado
El interés en el uso de PET para bebidas carbónicas llevó al desarrollo de maquinaria compleja que permite la biorientación y soplado del material inyectado en un solo equipo.
Las máquinas actuales permiten el acondicionamiento térmico perfilado de la preforma, en que pueden obtenerse geometrías complejas con un espesor uniforme o programado y, las más modernas, permiten además efectuar la deshidratación del PET, imprescindible para su transformación, dentro de la misma máquina.
Una transferencia rápida de la preforma a la fase de estirado soplado permite también reducir la temperatura del fundido en unos 20 C respecto a las máquinas anteriores, acercándola a la de transición vítrea del PET (70 C) para obtener la máxima orientación del material.
El PET y las olefinas son cristalinos y opacos por debajo de esta temperatura, a menos que el enfriamiento sea tan rápido que no de tiempo a la formación de esferolitos y resulten tan transparentes como en la fase amorfa. Para una descripción más detallada del aprovechamiento de estos fenómenos en las máquinas actuales, remitimos de nuevo al lector al número de nuestra revista citado antes.
4 - Controles para el moldeo por soplado
Obtener el máximo rendimiento de una máquina queda cada día más supeditado a la calidad y universalidad del control de cada uno de los elementos que la integran. Cada elemento interacciona con los demás, por lo que se precisan controles para coordinarlos y detectar con rapidez y seguridad cualquier nivel de deficiencia.
4.1 - Controles de la maquinaria
Para un control correcto de la temperatura, los sensores deben estar situados tan cerca como sea posible de la superficie del fundido, de otro modo darán señales irreales determinadas por el gradiente de temperatura en el acero de la cámara, que no es un conductor especialmente bueno, con diferencias que pueden superar 60 C si el sensor está situado a poca profundidad.
Existen sistemas con doble sensor, uno situado cerca del fundido y otro más superficial, que permiten dar una respuesta más rápida para las necesidades de refrigeración o calentamiento.
Los más adecuados son los de reposición automática con circuito RTD (detector de resistencia a la temperatura) que detecta los cambios de resistividad del metal relacionados con los de su temperatura, y que tienen una sensibilidad 60 veces mayor que un termopar.
El sistema más preciso para la detección de la velocidad es el de fase digital de circuito cerrado, en el que un comparador relaciona los pulsos generados por el eje con los de emitidos por un cristal eléctrico de referencia, con precisiones del 0,001%.
Los controles lógicos programables de temporización y secuencia se utilizan actualmente de modo universal.
4.2 - Controles del proceso
La temperatura que lee una sonda en la corriente de fundido es el parámetro que se utiliza para ajustar la temperatura de la cámara.
Aunque una temperatura correcta implica una viscosidad correcta del fundido, los medidores de la presión de fundido pueden dar resultados aleatorios en el moldeo por soplado porque el programador de la preforma puede afectar a la presión de retorno leída en la extrusora.
El modo más efectivo de estabilizar la producción de fundido es usar una bomba de fundido en el extremo de la extrusora. Estas bombas son particularmente útiles en el soplado de envases multicapa. Al entrar en el cabezal de coextrusión diferentes corrientes de plástico, es inevitable que se produzca entre ellas una interacción y es difícil mantener la relación adecuada de todas las corrientes, y por tanto de todas las capas.
Un fallo en el espesor adecuado de una capa de barrera, por ejemplo de oxígeno, puede notarse meses después, cuando el contenido se estropea en la estantería. Las bombas de fundido aseguran que cada capa tiene el espesor debido.
La variación de espesor en la preforma se obtiene al pasar el extruído por el sistema cónico descrito antes que se mueve bajo el mando de un programador, que al mismo tiempo lo monitoriza y puede verse su perfil en una pantalla. Los cambios deben programarse con unos gradientes adecuados para evitar que se generen bordes agudos o excesos de material.
La preforma debe evitar cambios en longitud, mediante otro control, para que se sitúe siempre en la misma posición respecto al molde aunque haya cambios menores de viscosidad. Este control asegura que la posición sea la misma en cada ciclo.
4.3 - Controles del producto
La clave del rendimiento económico de la operación es que el peso de cada unidad se mantenga constante. Por ello es deseable -y posible- disponer una estación de pesada de los productos, incluso en el moldeo a alta velocidad, a la salida de la máquina.
Los equipos actuales permiten pesadas precisas en ciclos menores de 1 segundo.
Otra medición práctica es la del espesor de pared en zonas determinadas mediante un equipo nuclear o ultrasónico. Este es el sistema más práctico para envases o depósitos grandes.
5 - Equipo auxiliar
Al elegir el equipo auxiliar es necesario mantener un criterio de eficiencia energética, especialmente en el enfriamiento, puesto que las mejoras de productividad pueden tener un coste mayor de energía que el ahorro en tiempo de ciclo.
El reprocesado y, especialmente, el compounding en fábrica necesitan de sistemas de conducción cuyo coste de funcionamiento, incluídos filtros, no debe superar al ahorro con respecto al uso de material en gránulo. Lo mismo es válido para la introducción de sistemas perfeccionados de secado.
5.1 - Manejo y secado del material
La selección del material de manejo de las resinas depende de:
- forma del material, tamaño, densidad a granel y características de flujo.
- Requisitos de la producción tales como kg/hora en cada localización, distancia del contenedor o silo de almacenaje a la máquina, número de materiales distintos a conducir, etc.
-Métodos de recepción y almacenaje del material.
El secado de los plásticos depende de que sean del tipo no higroscópico, como las olefinas o el poliestireno, en cuyo caso la humedad se adhiere a la superficie de los gránulos y se elimina mediante soplado con aire caliente, o higroscópicos, como las poliamidas, ABS y PET, que sólo se secan mediante aire deshumidificado.
En el primer caso se utilizan cámaras secadoras de aire caliente, pero en el segundo, para eliminar la humedad del aire se utilizan coladores moleculares, que son complejos denominados zeolitas. Cuando se calientan, las zeolitas desprenden agua y la absorben al enfriarse. Los equipos que las contienen pueden tener un lecho único o múltiple y funcionan en circuito cerrado.
Figura 5 Contenedores de granel de 1250 litros; una de las mayores piezas moldeadas por soplado
El PET presenta un problema particular en tanto que debe secarse hasta rebajar el 0,002% para que tenga una viscosidad correcta, además de que es necesario controlar el nivel de acetaldehído. Por el contrario, las poliamidas deben contener aproximadamente un 0,1-0,3% de humedad; si están más secas no fluyen ni cristalizan bien y si se pasa del 0,35% pueden resultar productos quebradizos.
5.2 - Atemperado
Hoy se considera necesario utilizar sistemas de enfriamiento en que se recupere el medio refrigerante. Hay tres categorías de temperatura del agua utilizada: en la de 27-29 C se utilizan torres de enfriamiento u otros dispositivos de evaporación, en la de 7-13 C es preciso refrigerar el agua y en la de de 1 a -18 C se debe además añadir anticongelante para evitar dañar el equipo.
Los refrigeradores pueden equipar condensadores refrigerados por aire o por agua. En las operaciones de gran volumen de producción se utilizan sistemas centralizados de enfriamiento del agua, que en muchos casos sitúan los intercambiadores de calor en la atmósfera exterior. Naturalmente, los cambios climáticos afectan el rendimiento de este tipo de instalaciones.
El aire comprimido utilizado para el soplado debe estar exento de humedad, utilizando para ello sistemas mecánicos de expansión directa, que utilizan refrigeración para reducir la temperatura a 3 C, donde se encuentra el punto de rocío más bajo, lo cual permite extraer el máximo de agua del aire.
Actualmente se va introduciendo el uso de bombas de calor para mejorar el rendimiento energético de todos los procesos térmicos.
5.3 - Decoración
El desarrollo del etiquetado en el molde, en que la etiqueta se sitúa en el molde para que quede formando parte integral al ras de la pared del envase, elimina problemas de arrugas o burbujas en la etiqueta, al tiempo que el etiquetado en línea añade resistencia al envase y permite ahorros de material del orden del 10%.
Otras técnicas son la pintura por pulverización convencional o electrostática, en que también puede rebañarse la superficie pintada de modo que sólo quede pintura en las zonas refundidas o, alternativamente, aplicar la pintura a rodillo de modo que sólo cubra las superficies realzadas. También se pinta por serigrafía, a través de una pantalla cegada donde no debe pasar el color.
La electrodeposición galvánica confiere un acabado metálico funcional que puede ser mate o brillante. La metalización bajo vacío recubre con una delgada capa de metal en fase vapor sobre una superficie preparada con una capa de base. La tampografía se utiliza también, así como la transferencia off-set.
La última novedad decorativa en envases de formas no cilíndricas la constituye la transferencia a la preforma de imágenes modificadas que adquieren su forma propuesta cuando el envase toma su forma final.
5.4 - Automatización
Los productos soplados han llegado a tamaños tan grandes que en fábricas cuyas líneas están totalmente automatizadas todavía deben realizarse a mano operaciones tales como el transporte desde el molde y la terminación de bocas porque la poca consistencia dificulta estas operaciones para envases de 640-1250 litros de capacidad.
En los demás casos, la práctica totalidad de las operaciones de líneas de gran producción están automatizadas, desde el transporte de materiales hasta la extracción del molde y el manejo robotizados de los productos.
Una operación delicada es el recorte de los envases que incorporan un asa. Se efectúa normalmente por cizallamiento entre dos moldes de corte, pero si un envase está torcido, puede quedar aplastado y bloquear el cortador, que es una pieza de equipo peligrosa.
5.5 - Detección de fugas
Una incidencia de porosidad relativamente pequeña puede representar una pérdida económica considerable. Una sola máquina en que los envases con fuga sean uno entre cien puede representar una pérdida de doscientos millones de pesetas por año sólo en el producto perdido.
Dada la velocidad a que se producen los envases, su bajo espesor de pared y la temperatura a que salen del molde, no pueden usarse presiones importantes para ensayar la porosidad porque se deformarían o reventarían.
Por ello se emplea el ensayo de presión obtenida, en el que se somete a baja presión a una tasa controlada y un sensor detecta si se ha alcanzado la presión prevista, indicio de ausencia de fugas.
Otro es el ensayo de mantenimiento de la presión, en que una vez alcanzada determinada presión, se verifica si ésta cae. Similar a éstos es el ensayo de desplazamiento, en que se llena una cavidad con aire en una cantidad y presión determinadas y se transfiere al envase, permitiendo un ensayo más rápido.
Conclusión
Estos procedimientos están alcanzando cada día más campos de aplicación, incluyendo los de piezas complejas en las que los sistemas de soplado requieren moldes múltiples por pieza, con sistemas robotizados de deposición de las preformas.
Estimulados por el desarrollo de la maquinaria, las aplicaciones salen del campo del envase para producir elementos de automoción, juguetería e incluso elementos para la construcción, como un original sistema de tejas que se transportan en vacío y se llenan con agua o arena en la obra, con un importante ahorro en el transporte.
La economía de coste de los moldes convierte a estos procesos en un desafío para el diseñador, en el que es económico efectuar series de ensayo que la aceptación del mercado transforma fácilmente en producciones de gran volumen sin variar de proceso.
El proceso permite utilizar plásticos con un peso molecular muy elevado,obteniéndose paredes más delgadas, o resistencias más elevadas a igualdad de peso, y mejor comportamiento a los agentes que producen fisuración por tensiones. | La distribución del espesor de pared en la extrusión se efectúa mediante la programación de la preforma, relación de soplado y configuración de la pieza, cerrándose los moldes hidráulicamente o mediante rodillera. | La inyección se utiliza para fabricar contenedores que tengan tolerancias estrictas, cuellos roscados y formas muy estilizadas, caracterizándose por una buena distribución del material, sin precisar acabado o recortes adicionales. | La orientación molecular o estirado biaxial permite el uso de grados inferiores de material o menores espesores de pared mediante un control preciso, con reducción del coste en ambos casos. | En las tubuladuras de admisión, el refuerzo con fibras ha obligado a desarrollar sistemas sofisticados para evitar el pinzamiento de las paredes, que quedarían continuidad estructural. | Materiales flexibles de envase iniciales y aún en uso, como celofán, poliéster o PP orientado, se usan con recubrimiento de PVDC. El recubrimiento es uno de los procesos más adecuados para mejorar las propiedades de barrera. | El desarrollo de técnicas de extrusión permite fabricar paredes de 5 a 7 capas, con una excelente distribución coaxial de espesores unitarios menores de 0,03 mm y un uso económico de capas de barrera costosas. | Las grandes piezas industriales requieren un acumulador a pistón hidráulico porque, si se utilizase extrusión contínua, el peso de la preforma la deformaría durante el tiempo necesario para producirla. |