Coste previsto y coste real, la diferencia entre ganar dinero o perder la camisa (Parte 2)
En el siguiente artículo destacamos algunos casos con problemas que, por experiencia, pueden aparecer en las series iniciales, o en las primeras pruebas. Algunos de ellos son previsibles con antelación otros no tanto. También mencionaremos algunas preguntas que deberíamos hacernos con el objetivo de confeccionar una lista de chequeo de diseño y aspectos del molde, de chequeo de la inyectora, de diseño de las piezas, etc.
Carrera disponible de expulsión máxima
Se asigna una máquina con tonelaje adecuado, distancia entre barras correcta, volumen de inyección adecuado, etc. Cuando se hacen las primeras piezas completas se observa que la carrera de expulsión disponible no es suficiente para expulsar completamente las piezas. Esto obliga a trasladar el molde a una máquina de inyección de mayor tamaño (coste horario más alto o montar sistema independiente de expulsión (inversión no prevista).
¿Tenemos en cuenta la carrera disponible máxima de expulsión para asignar la máquina de inyección adecuada?
Sistema de expulsión
Cuando hacemos un llenado progresivo e inyectamos piezas cortas, para determinar llenado y punto de conmutación, debemos tener en cuenta el sistema de expulsión.
Recuerdo un caso fabricando una luminaria de PC para farolas de exterior: la luminaria era de forma tronco-cónica y el sistema de expulsión era por placa. Al inyectar pieza corta, en el momento de la expulsión, la placa no empujó la pieza pues el plástico no había llegado a llenar el exterior de la pieza que es donde la placa empujaba para la extracción.
Resultado, pieza clavada en el molde sin posibilidad de expulsión a través del sistema de placa y una complicadísima operación de desclavado de la pieza sin afectar al pulido espejo del molde.
¿Se tiene en cuenta el sistema de expulsión del molde para la puesta a punto inicial?
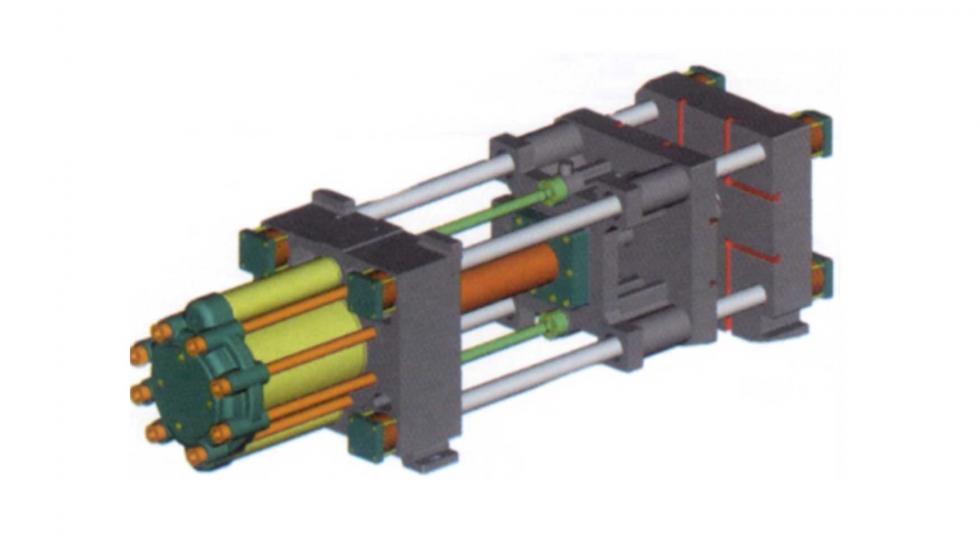
¿Se puede prever la expulsión de piezas faltadas a través del sistema de expulsión?
Si lo tenemos en cuenta y es crítico el volumen inyectado para poder expulsar las piezas, ¿tenemos en cuenta el cálculo de la dosis necesaria para asegurar que expulsamos las piezas?
Sistema de canal caliente
Sistema de canal caliente del molde con 10 zonas, 8 para boquillas y 2 para el bloque caliente.
En la conexión no hay norma de instalación del sistema, por lo que no se sabe qué zonas son de las boquillas ni a qué boquilla pertenece y tampoco se sabe que zonas son de bloque caliente ni de cuál de ellas exactamente.
Con esta situación no es posible un ajuste correcto del sistema de canal caliente y mucho menos realizar correcciones que nos puedan interesar en zonas concretas.
Entonces se utiliza para avanzar el método empírico de prueba y error. Se conectan una por una las zonas de control y se intenta identificar a que boquillas o zonas de bloque caliente pertenece cada control. Normalmente, las zonas de bloque caliente tienen más consumo en amperios que las boquillas calientes y también las zonas del bloque calientan más lentamente que las resistencias de las boquillas calientes que son más “rápidas”.
¿Se solicita esquema de conexiones e identificación de zonas al moldista con la entrega del molde?
Llenado de molde
En un molde por ejemplo de 8 cavidades, 4 cavidades llenan antes que las otras 4.
En esta situación, se comprueban todas y cada una de las entradas y las dimensiones son exactamente iguales, se comprueban los ramales de la colada y son exactamente iguales también.
Aquí hay quien intenta compensar el llenado a través de modificar las dimensiones de las entradas aumentando aquellas de las cavidades que llenan más tarde. Esto hace que finalmente tengamos distintas cavidades con distintas dimensiones de entrada y por tanto, con distintos tiempos de sellado. Esto puede dar lugar a problemas de dimensiones, contracciones, etc. Este tipo de correcciones de dimensiones de canales calientes y entradas en las piezas que llenan diferente tendrá como consecuencia inevitable que los cambios de lote y de viscosidad del material pueden afectar nuevamente al llenado y desequilibrarlo, quizá incluso en otras cavidades no afectadas con anterioridad.
¿Se ha verificado el equilibrio del sistema de refrigeración?
¿Se ha verificado que no estemos ante un “efecto espiral”?
(Ver artículo de Interempresas, “El efecto espiral” de 2 de enero 2017)
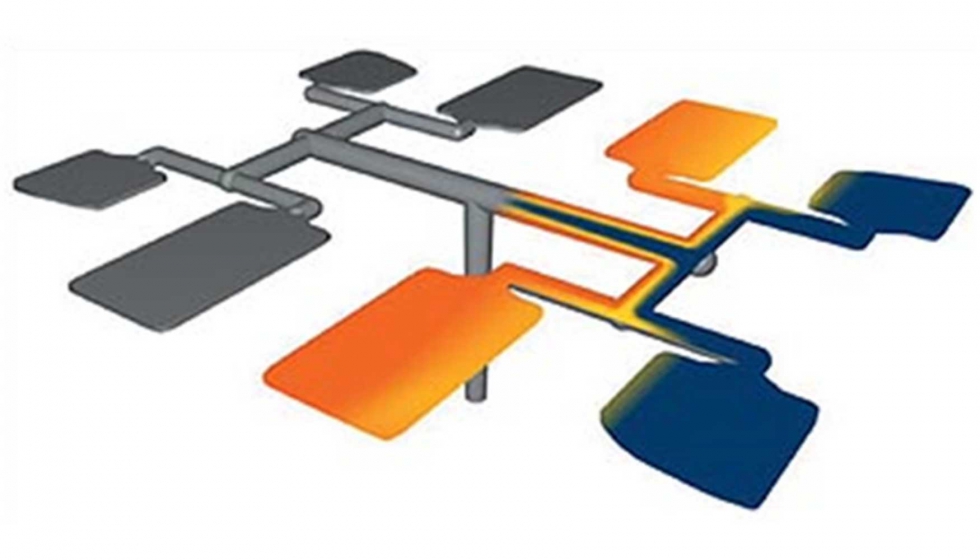
Fuerza de cierre
El análisis de Mold Flow, o simulación o la estimación previa nos indica que el molde requiere 200 toneladas de cierre. El molde es testado en una máquina de 250 toneladas.
Cuando se pasa a la fase de compactación, para obtener un calidad aceptable, necesitamos compactar y aparecen rebabas de cierre.
¿Pueden reducirse las zonas de contacto del partage para obtener más fuerza de contacto en la zona de ajuste?
¿Las placas de molde son suficientemente robustas?
¿Los tacos de apoyo del molde son suficientes y están bien ubicados?
¿Se pueden aumentar las dimensiones de las entradas, número de entradas etc para disminuir la presión de inyección?
¿Se ha probado una programación de la presión de compactación interpolada?
Tiempo de ciclo
¿Se pueden hacer vaciados en las piezas para eliminar acumulaciones de masa?
¿Se puede utilizar sistemas de cobre berilio o similares para mejorar la refrigeración?
¿Se puede ubicar mejor las entradas para compactar (regla thick to thin)?
¿Estamos en régimen correcto del sistema de refrigeración?
Entradas submarinas y entradas de cuerno o banana
Cuando el molde abre y se produce la expulsión de las piezas, la colada submarina rompe quedándose la entrada obturada por la propia submarina impidiendo la producción.
Frecuentemente el problema está en el expulsor empujador de la colada submarina o de cuerno. Este empujador debe permitir flexar a la colada lo suficiente para ayudar a la extracción de la entrada.
¿Diseño de la entrada submarina adecuado?, revisar ángulos y distancias
¿Distancia entre la submarina y el expulsor empujador de la misma suficiente?
¿Longitud del expulsor empujador correcta?
Por supuesto, muy importante los pulidos etc. de las entradas submarinas y de cuerno o banana.
Salidas de gases
El llenado de una pieza delgada es necesario que sea rápido y esto provoca efecto diésel, quemados y mal aspecto de la pieza. En piezas que no son delgadas, es conveniente una reducción de la velocidad final de llenado dentro de lo posible.
¿Están las salidas de gases bien ubicadas?
¿Se puede hacer salida de gases perimetral en todo el partage con salidas cada cierta distancia para tener al menos el 25% de la longitud del partage ventilado?
¿Se pueden utilizar sistemas de ventilación en los expulsores, postizos porosos, etc.?
Desmoldeo
Para obtener piezas con buen aspecto y dimensionalmente correctas, el nivel de presión en cavidad es alto. Al desmoldear las piezas tienden a agarrarse la cavidad y cuesta desmoldear.
En ocasiones este problema puede llevar a marcas de expulsión o rotura de las piezas al desmoldear.
Aplicando desmoldeante el problema desaparece hasta pasados unos ciclos, esto obliga a aplicar desmoldeante con cierta frecuencia. Aumentos de ciclo o tener que trabajar con ciclos semi-automaticos con mano de obra para aplicar desmoldeante.
¿Conicidades de desmoldeo correctas?
¿Se puede estar produciendo efecto vacío?
¿Se pueden ampliar las secciones de empuje de los expulsores?
¿Se puede texturizar ligeramente la superficie? En el caso de termoplásticos elastómeros
¿Se puede aplicar tratamiento superficial o coating desmoldeante en la zona critica?
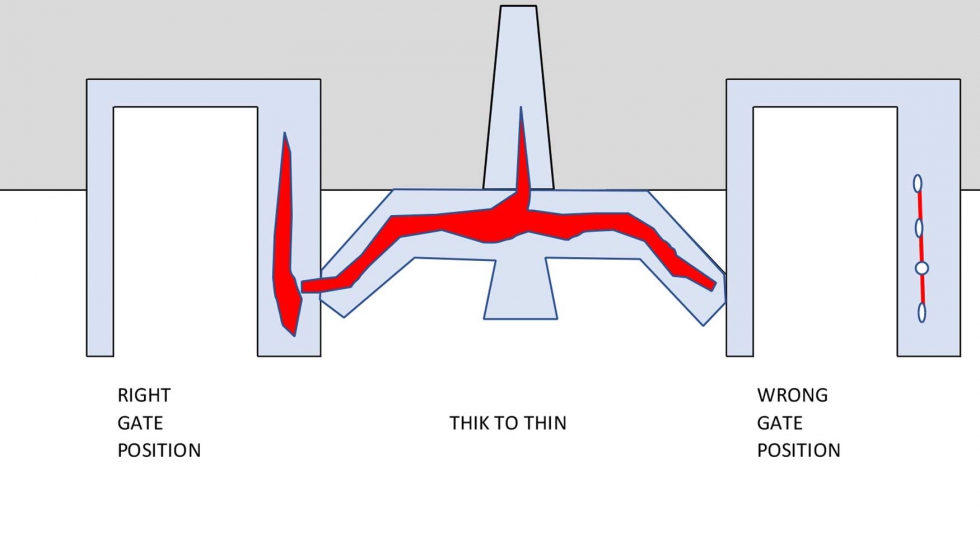
Correderas
La pieza tiene correderas a ambos lados. Al abrir el molde las correderas se desplazan a la vez pero las piezas, en lugar de quedar centradas para su expulsión, se desplazan con una de las correderas. Cuando intervienen los expulsores estos no empujan las piezas.
¿Se puede añadir un nervio o punto de expulsor para actuar como fijador de las piezas en su posición central?
Hay que intentar fijar la pieza sin desplazamientos laterales para que la correderas puedan desmoldear sin desplazarla. Revisar conicidades de desmoldeo, refrigeraciones, etc.
Mano de obra
Hemos previsto que un operario atienda mas de una máquina, para esto, las máquinas deber funcionar en modo automático y requerir una supervisión del operario que permita atender varias inyectoras.
En el caso de, por ejemplo, una rebaba, o un chequeo frecuencial, esto hace que aumente el tiempo de dedicación del operario y por tanto su saturación global. Esto impide que se el operario pueda atender el número de máquinas previsto y presupuestado.
La automatización de operaciones, tales como cortes de colada, embalado de las piezas, etiquetado, embolsado, etc. hacen que un operario pueda atender más máquinas y por tanto, ser más productivo. No se trata de que el operario corra más, se trata de que tenga los medios para atender más máquinas trabajando a una actividad normal.
En el sistema de costes, cuanto mayor es el tamaño de la máquina mayor es el coste horario. Por el contrario, el coste de la mano de obra directa es un coste que no se ve afectado por el tamaño de la máquina. El precio horario del operario es el mismo independientemente del tamaño de la máquina que esté atendiendo.
Por ello, cuando estamos ante máquinas grandes, de alto coste horario, lo prioritario no es el coste de la mano de obra si no del tamaño de la máquina y también el ciclo. Sin embargo, cuando estamos ante máquinas más pequeñas, con un coste inferior incluso al coste del operario, la prioridad debe ser el coste de la mano de obra y por tanto, es primordial la automatización y que este coste se diluya en el mayor número de máquinas atendidas posibles.
La lista de chequeo o check list
Estos ejemplos comentados en estos artículos son solo algunos, pero hay muchos más “incidentes” que se pueden producir en unas primeras pruebas de molde y todos ellos nos deben llevar a confeccionar un check list previo de chequeo que permita anticiparnos en la medida de lo posible a su aparición y solucionarlos con antelación.
Esa teórica lista de chequeo puede mantenerse viva con cada nueva experiencia y es de gran valor, tanto para el inyectador como para el moldista, ya que si una situación ha sido prevista y además tenemos planes de acción para intervenir en el caso de que el incidente ocurra siempre será menos impactante y lo podremos solucionar y gestionar mejor.
Confeccionen si no la tienen ya creada, primero una normalización de los estándares de molde que evite las sorpresas de recepción de moldes y una lista de comprobación de factores que, aunque a veces parece que no puede pasar (Murphy está en plantilla), nos pueden afectar de modo importante en los costes en un lanzamiento de un nuevo proyecto de fabricación de piezas inyectadas.
José Ramón Lerma es autor de los libros: 'Libro Manual Avanzado de Inyección de Termoplástico', que tiene como objetivo ser, por un lado, una herramienta para la formación y, por otro, un manual de ayuda para todo el personal de una empresa de inyección de plásticos y, del recientemente editado, 'Scientific Injection Molding Tools. Productividad a través del dominio del proceso'. Ambas publicaciones, comercializadas por Plásticos Universales / Interempresas (libros@interempresas.net), consta de detallados casos prácticos, amplia información de moldeo científico y un ‘pendrive’ con 20 hojas de cálculo y herramientas de SC Molding o Scientific Injection Molding, además de optimización y definición de proceso, lo que lo hacen único en el mercado. Página web sobre Scientific Injection Molding: www.asimm.es