Molinos para un plástico cada vez más reciclado
No olvidemos que, tras la recogida selectiva y el cribado de materiales, la trituración es uno de los procesos principales en el reciclaje. Lo cierto es que cada vez se deben reciclar más productos lo que provoca que los trituradores deben ser cada vez más versátiles. También la tipología del residuo es muy variable, ya que podemos estar hablando de molinos muy pequeños de sobremesa o para laboratorio, hasta molinos de mayor tamaño que se sitúan a pie de máquina para triturar las coladas y rebabas de los procesos de inyección y soplado de plásticos u otro tipo de trituradores de grandes dimensiones que se instalan con frecuencia en el sector del reciclado. Aunque todas estas actividades recuperan materiales desechados, requieren condiciones y capacidades muy diferentes. De hecho, existen diferentes tipos de sistemas trituración, como los molinos, los desgarradores o los destrozadores. Estos últimos sirven en la industria del reciclado para una gran diversidad de residuos difíciles de destruir: plástico, caucho, neumáticos, fibra, papel, madera, componentes eléctricos y cables que son.
No es fácil generalizar y señalar en pocas palabras los factores importantes a la hora de adquirir uno. Es obvio que no es lo mismo triturar rebabas a pie de una inyectora, que triturar tuberías, láminas, films, nylon, caucho, botellas de plástico o plásticos procedentes del automóvil, por poner algunos ejemplos. El tamaño de entrada para el residuo y la dimensión del propio triturador ya determinan de partida el tipo de actividad para el que puede ser utilizado.
Desde luego trabajar con menos polvo, menos ruido y con un consumo de energía significativamente menor son algunas de las premisas que se valoran con frecuencia. El diseño del rotor y el tipo de cuchillas que incorpore puede mejorar notablemente el consumo energético. Así por ejemplo, el corte tipo guillotina no solo reduce el consumo sino también el impacto sobre el material y, consecuentemente, el tipo de material resultante. Para reducir el polvo, en ocasiones se recurre al corte inclinado y en muchos casos se valora el círculo de corte constante mediante cuchillas rotativas y fijas ajustables.
La velocidad
Desde otro punto de vista, la velocidad del rotor es también importante, ya que no solo depende de ella la rapidez de la trituración, sino muchas veces también su calidad e incluso la granulometría resultante del proceso de molido. Una velocidad del rotor de 460 rpm, por ejemplo, ya se considera rápida. Con frecuencia el usuario, el potencial comprador de un molino, requiere una granulometría muy concreta, además de una capacidad de kilos por horas determinada. Velocidad y configuración del equipo influyen en el tipo de material que se puede triturar y en el rendimiento y productividad del equipo.
Con frecuencia se recurre a molinos de cuchillas para materiales blandos, con velocidades de 200-250 rpm. Pero cuando se trata de plásticos reforzados con fibra de vidrio, por ejemplo, se utilizan muchas veces molinos de baja velocidad que rondan las 25 rpm, dependiendo en cierto modo del material específico a procesar. En el caso de materiales frágiles, por debajo de esas revoluciones se reduce mucho la generación de polvo, pero también el ruido. Según algunos fabricantes, en estos rangos de velocidades una reducción de 10 rpm puede suponer un 50% menos de ruido, mejorando así mucho las condiciones de los trabajadores de la fábrica.
Asimismo la propia construcción del molino determina sus funcionalidades y otros aspectos relevantes, como su limpieza. Facilitar la limpieza, el cambio de cuchillas y el mantenimiento es importante porque evitará problemas en el día a día del usuario. Algunos fabricantes optan por molinos robustos, diseñados para altos rendimientos, y que puedan tratar materiales abrasivos y piezas voluminosas, en campos de aplicación muy diversos y con accesibilidad óptima a la cámara de trituración para la limpieza y mantenimiento.
Lo cierto es que en la construcción de los molinos los fabricantes aportan diferencias para mejorar unos u otros aspectos. Algunos sitúan los rodamientos en el exterior de la cámara de corte para permitir el trabajo con líquidos, otros incorporan un sinfín transversal en la tolva de salida para la descarga lateral del producto triturado, otros cuentan con sistemas automáticos de apertura de la tolva y de bajada de la cama de la rejilla... Las opciones son muy numerosas.
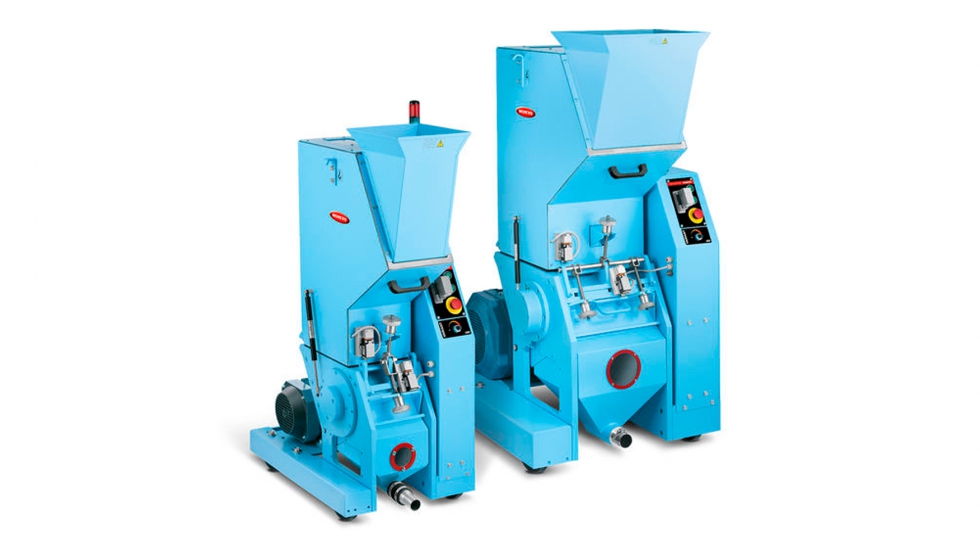
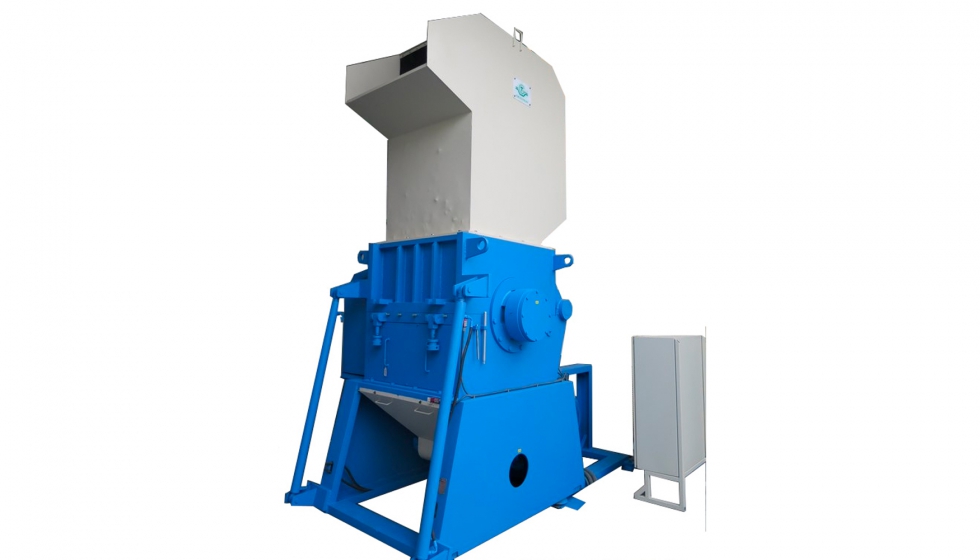
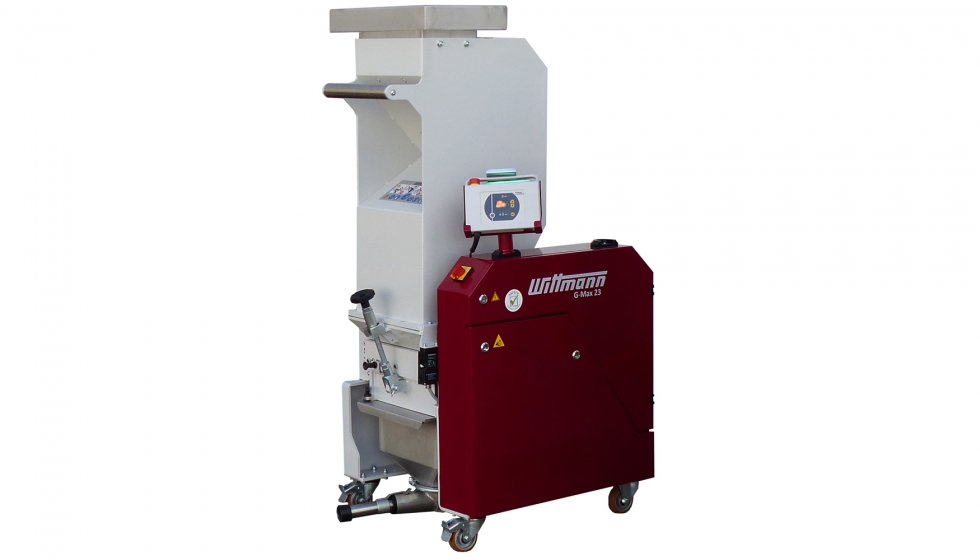

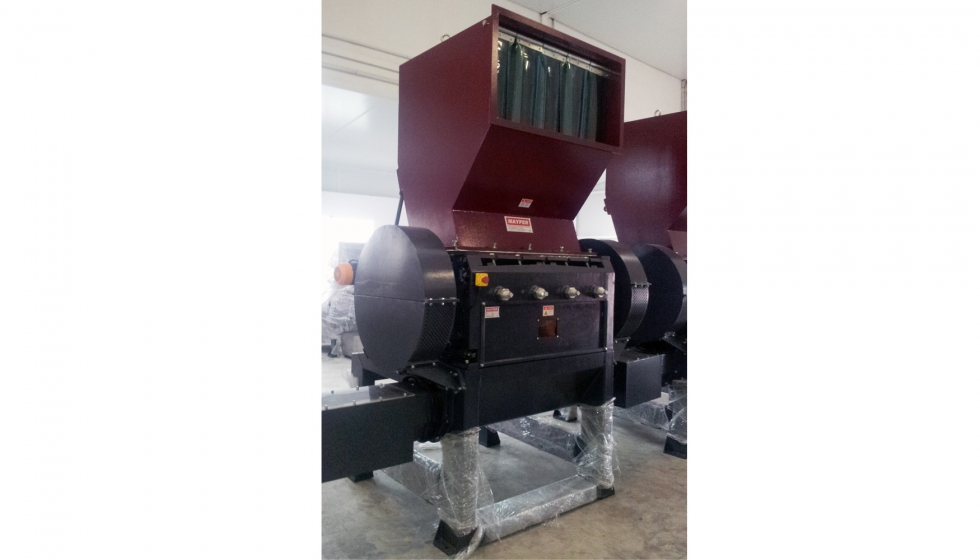
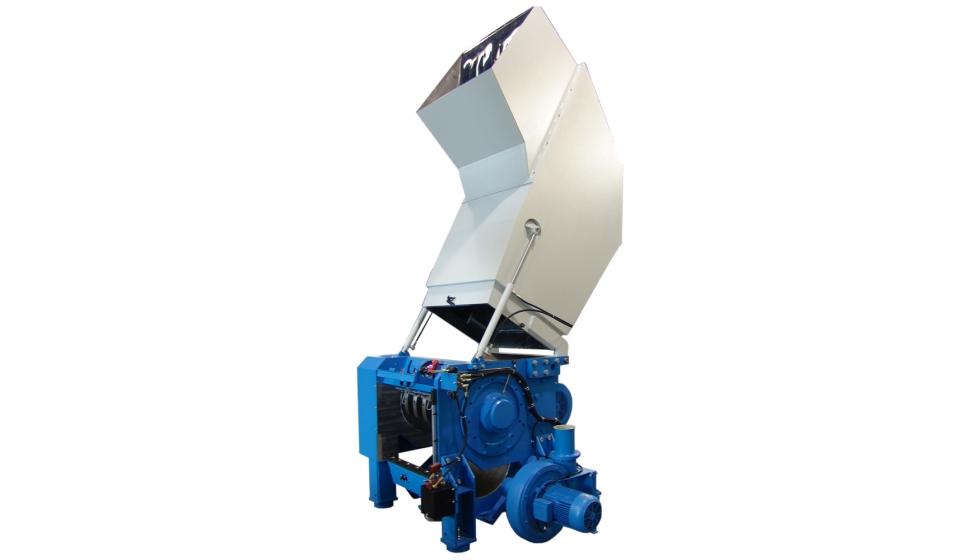