Case Study de Addimat e Ibarmia
Recuperación de husillos de extrusoras de caucho
Addimat, Asociación Española de Tecnologías de Fabricación Aditiva y 3D
18/02/2020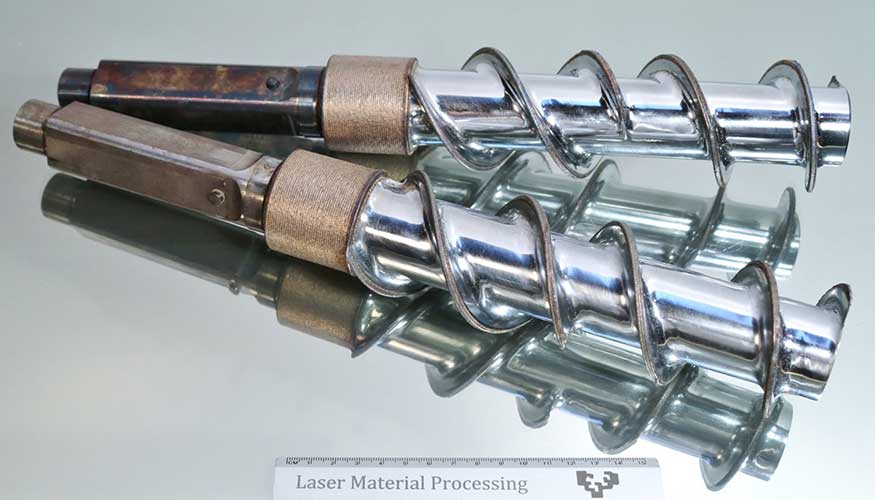
Sector: Automoción
Reto: La empresa Michelin, dentro del marco del proyecto europeo Paraddise, plantea la recuperación de husillos de extrusión de caucho dañados.
Solución: La solución propuesta consiste en el recubrimiento de las zonas dañadas del husillo de extrusión mediante la tecnología de láser cladding.
Reto
Para la producción de neumáticos, Michelin fabrica al año 200 husillos extrusores de caucho. Durante el proceso de extrusión, el caucho es calentado y empujado por la rotación del husillo hacia la cabeza de la extrusora.
Debido a la alta fricción y temperaturas a los que se ven sometidos, los filetes de los husillos sufren un alto desgaste, disminuyéndose así su vida útil.Los husillos de extrusión están hechos de 42CrMoS4 (AISI 4140, DIN 1.7227), el cual es un acero estructural de baja soldabilidad.
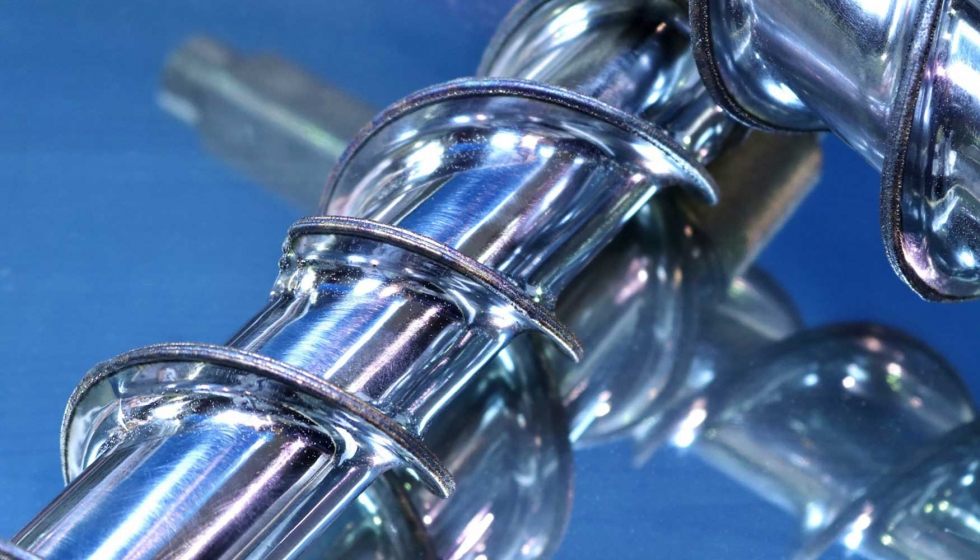
Solución
El láser cladding es una tecnología ampliamente empleada para la realización de recubrimientos y reparaciones de componentes de alto valor añadido de diversos sectores industriales. Este proceso se caracteriza por su capacidad de generación de recubrimientos con propiedades semejantes a las del material base, al cual se encuentra unido metalúrgicamente produciendo una mínima afección térmica. Además, tiene una gran flexibilidad en cuanto a generación de geometrías y es aplicable a una amplia variedad de materiales metálicos.
En consecuencia, el láser cladding es una tecnología válida para la recuperación de husillos de extrusión. Se opta por recubrir las zonas dañadas de dos husillos de extrusión de caucho con Eutroloy 16606, el cual tiene una estructura martensítica con una alta resistencia al desgaste por abrasión, incluso a altas temperaturas combinadas con cargas de fatiga, lo cual se adecúa a las condiciones de trabajo de los husillos en cuestión.
Debido a la naturaleza del material de aporte, resulta necesario evitar grandes gradientes de temperatura entre éste y el material base. Este requerimiento, unido a la baja soldabilidad del material base, 42CrMoS4 (AISI 4140, DIN 1.7227), hace necesario introducir una etapa de precalentamiento de la pieza a reparar, para la correcta consecución de la reparación. Con todo ello, una vez parametrizado el material a aportar y teniendo en cuenta la geometría a reparar, se procede a efectuar la recuperación de las piezas objeto de estudio, añadiendo una demasía respecto de las dimensiones finales, para así facilitar su posterior mecanizado. Como resultado, se obtienen unos recubrimientos de 61 HRC de dureza y libres de defectos como grietas o poros.
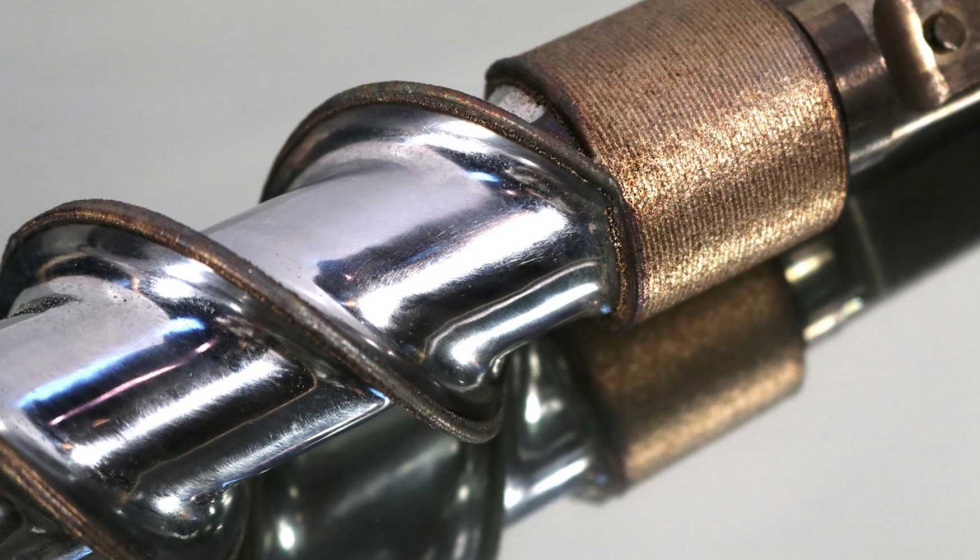
Beneficios
Además, esta propuesta de recuperación de piezas dañadas no está exenta de beneficios técnicos, dado que, en función del material añadido, se obtienen recubrimientos de alto rendimiento, con mejores propiedades frente al desgaste, corrosión o fatiga térmica, entre otros.
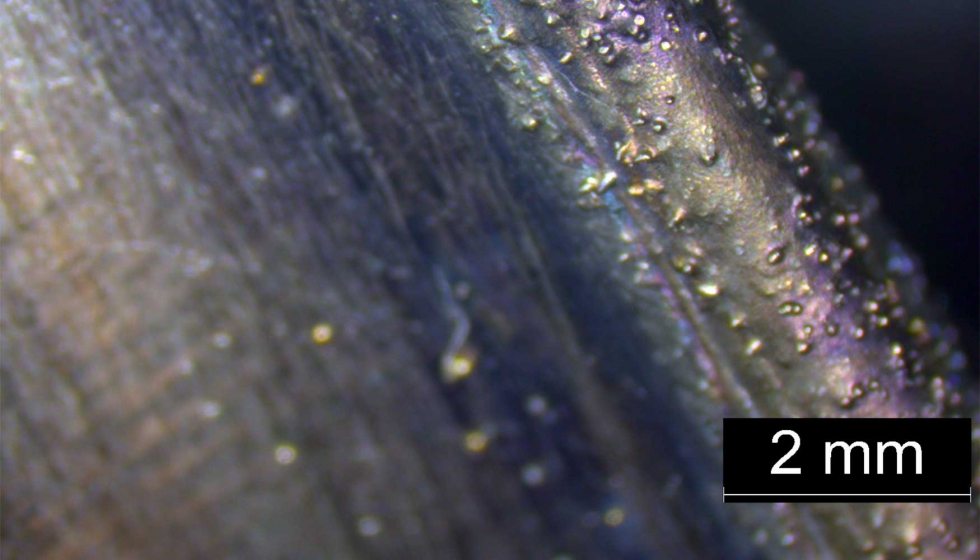