Ejecución de columnas de grava como refuerzo de la cimentación de un parque eólico en Nouakchott, Mauritania
La Société Mauritanienne d'Electricité Somelec adjudicó en 2013 a la empresa Elecnor la ingeniería, construcción y mantenimiento del primer parque eólico del país con una capacidad de 30 MW para fortalecer el abastecimiento a la red eléctrica mauritana donde la mayor parte se produce mediante generadores de diésel. La puesta en servicio se produjo en el primer trimestre de 2016.
El campo eólico cuenta con un total de 15 aerogeneradores de 2 MW tipo Gamesa G97, con una altura al rotor de 90 m, sobre una cimentación de 20 m de diámetro (S=314,15 m2) y una altura de tierras de 3,02 m, tal y como se muestra en la figura 1.
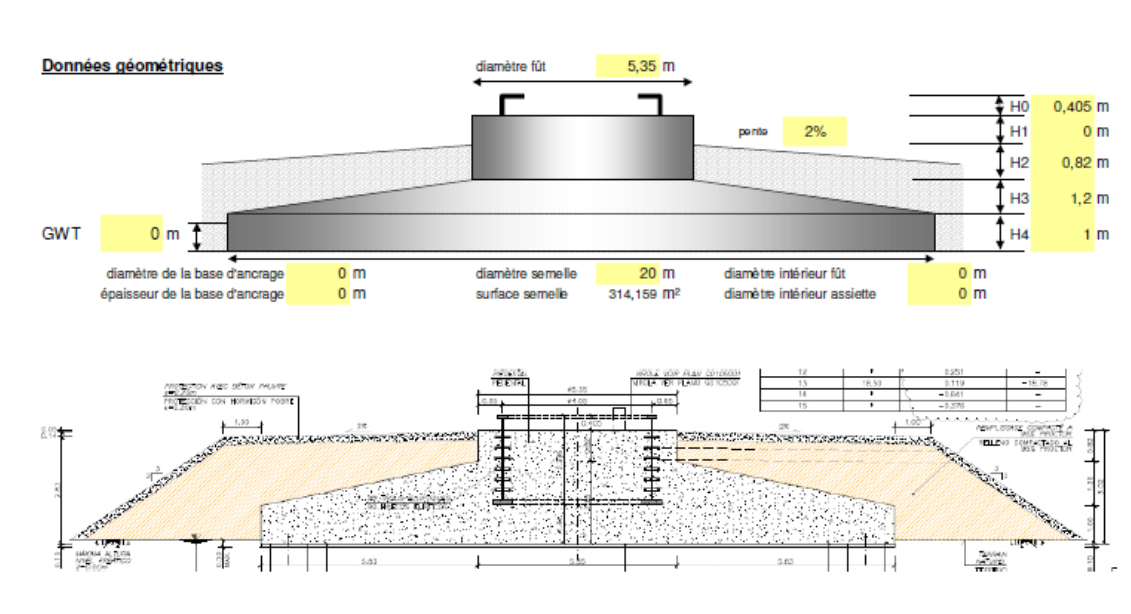
Debido a la existencia de suelos flojos deformables se llevó a cabo un refuerzo de las cimentaciones mediante columnas de grava con el objetivo de aumentar la rigidez del terreno, garantizando el funcionamiento de estos equipos, muy sensibles a las distorsiones o asientos diferenciales.
1.- Descripción del terreno
En cada aerogenerador se llevó a cabo un sondeo mecánico (S) con extracción de terreno y realización de ensayos SPT (N30) cada 1,5 m, y un sondeo presiométrico (PTM), con ensayos cada 1,5 m, obteniendo la presión límite (Pl), presión de fluencia (Pf) y módulo presiométrico (Ep).
En dichas prospecciones se describe una columna litológica compuesta por una alternancia de arenas de tonos ocres a grises muy homométricas, arenas con restos de conchas y lentejones de gravas con arenas. Presencia de niveles cementados superficialmente y nivel freático a profundidades variables de 1 a 4 m.
En los gráficos de la figura 2 se recogen los valores de golpeos del ensayo SPT, y presiones límites/módulo presiométrico relacionados con la profundidad del ensayo de todos los aerogeneradores (WT).
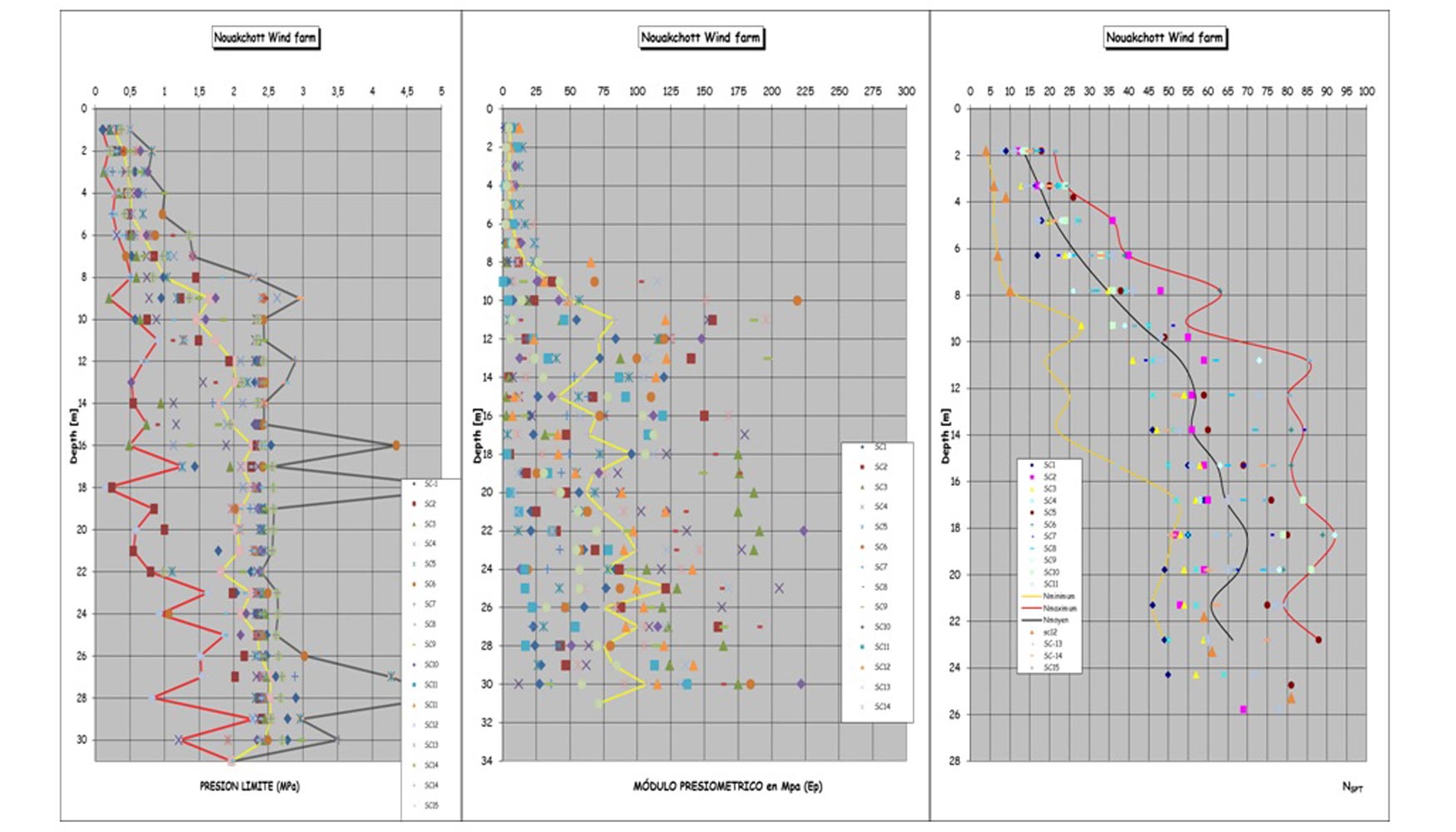
Figura 2. Valores de presión límite (Mpa), módulo presiometrico (Mpa) y golpeo NSPT.
Del análisis de estos datos se desprende la existencia de suelos flojos en los primeros 7,5 a 10,5 metros, con intercalación de niveles parcialmente cementados. En la tabla 1 se recoge para cada posición (WT) los espesores de suelos flojos detectados.
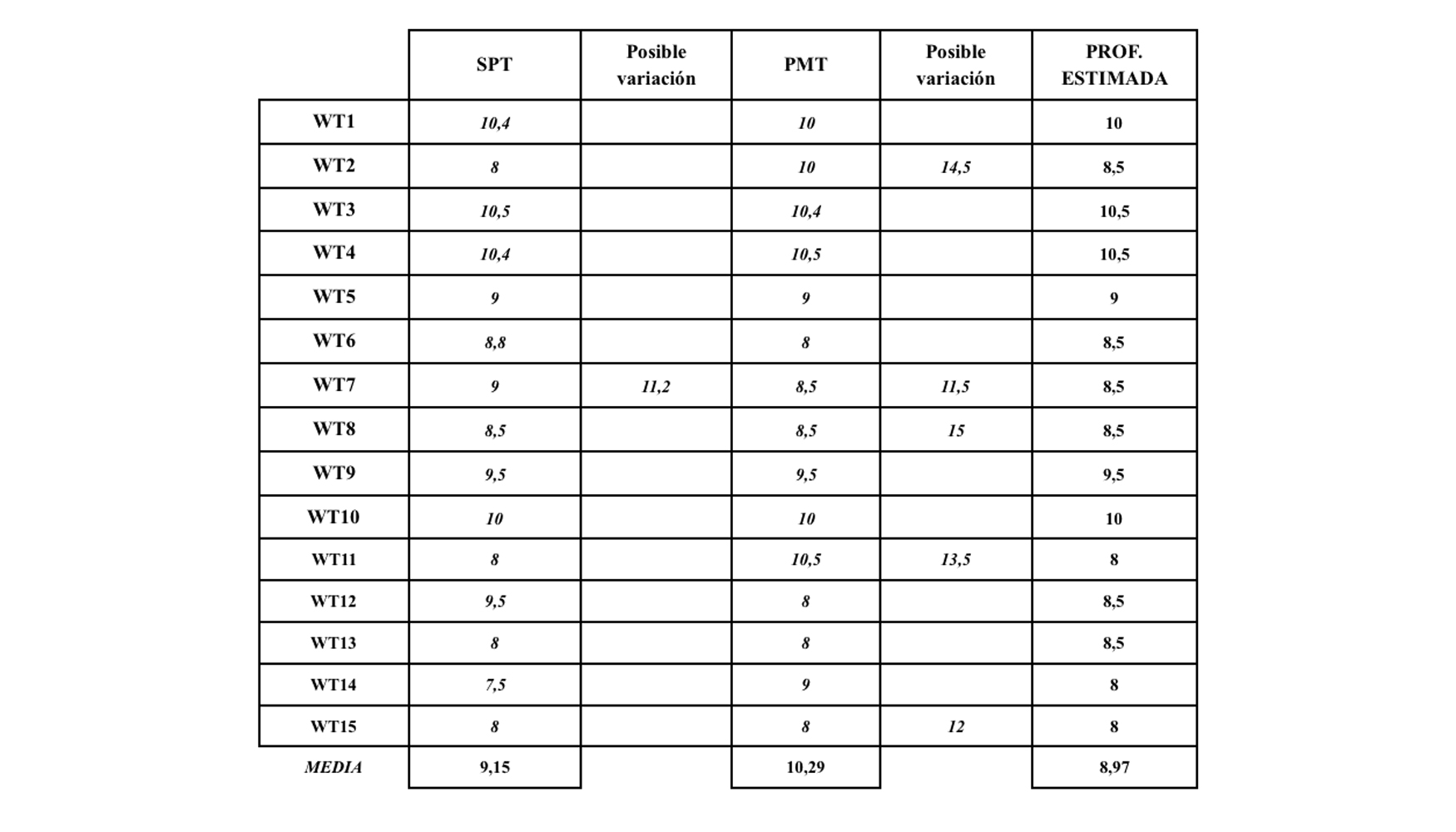
La columna litológica media sería la siguiente:
- 0,00-3,50 m: arenas flojas, con valores medios de presión límite Pl=0,4Mpa y módulo presiométrico Ep=4,5MPa.
- 3,50-7,5/10,5m: arenas flojas a medias, con valores medios de aproximadamente Pl=0,7 Mpa y Ep=6,7MPa.
- >7,5/10,5m: arenas densas con Pl=2,15Mpa y Ep=40,5Mpa.
En la figura 3 se muestra el huso granulométrico de los suelos a mejorar en función de la clasificación de Glover según el grado de vibrocompactación para diferentes terrenos.
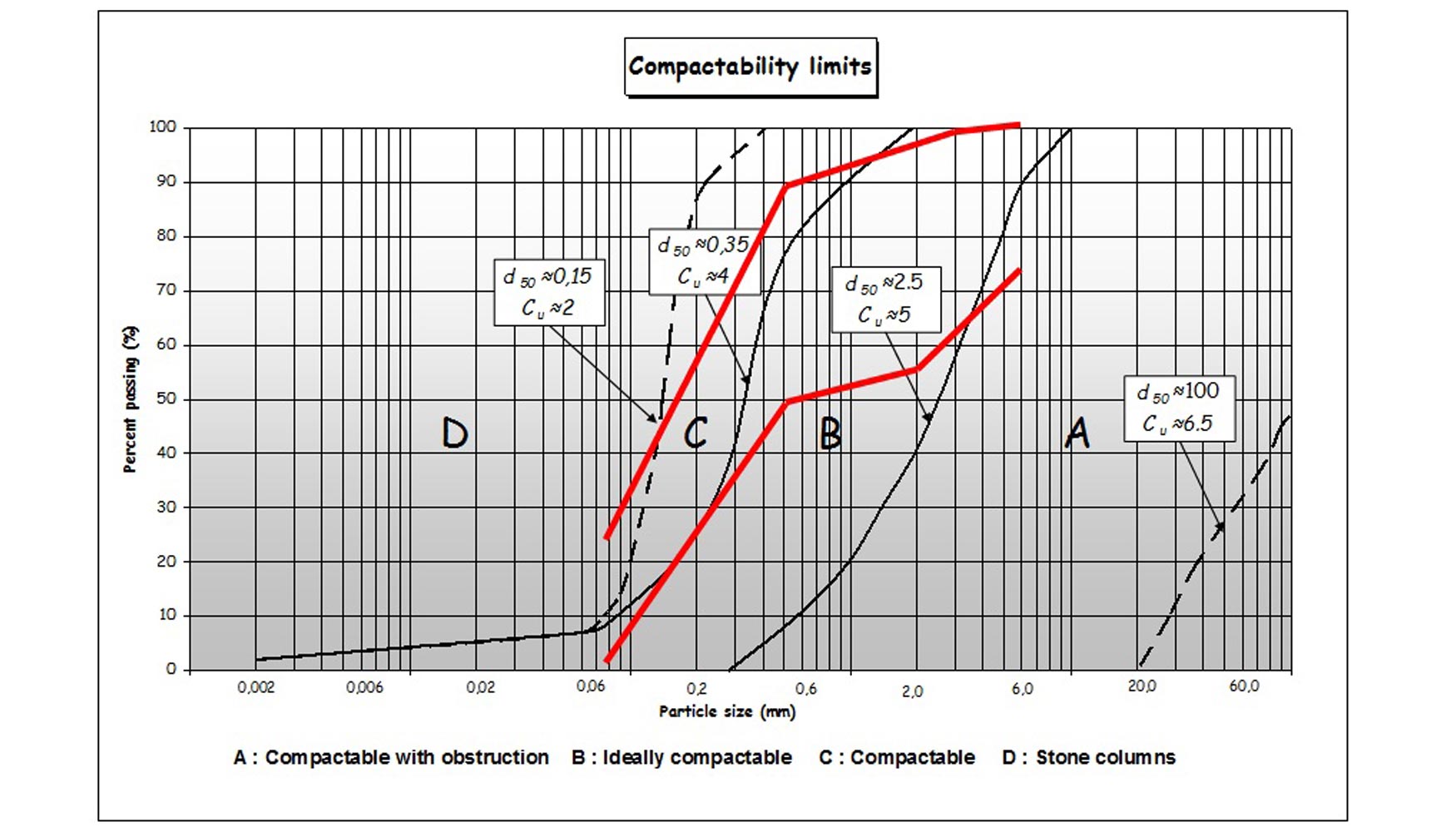
Debido a la naturaleza arenosa del terreno y la presencia de un nivel freático alto, se trata de suelos susceptibles a procesos de licuefacción.
La obra se sitúa en una zona con escasa actividad sísmica, el sismo de mayor registro es de 4,5 con aceleraciones de cálculo, an=0,1 m/sg2. Se comprueba que no existe riesgo de licuefacción para sismos de intensidad inferior a 5,5, a excepción de los emplazamientos de los aéregeneradores 11 y 12. No obstante, con el tratamiento de columnas de grava se aumenta el coeficiente de seguridad frente a este riesgo (FS>1,25) según el eurocódigo EC-8.
2.- Criterios de diseño de la solución planteada
En fase de proyecto, se analizaron diferentes tipologías de posibles soluciones tanto por medio de cimentación profunda (pilotaje) como por medio de tratamientos del terreno.
Tras el análisis de los condicionantes técnicos, de ejecución y geográficos, se contempló como la solución más ventajosa un tratamiento mediante columnas de grava según el método ‘Dry Bottom Feed’.
Esta técnica consiste en la sustitución parcial del terreno deformable por una grava compactada introducida a través de un vibrador que desplaza lateralmente el terreno hasta alcanzar las capas más resistentes en profundidad.
A medida que se extrae el útil, se rellena la cavidad con la grava que cae por gravedad a la punta del vibrador y alimentación a partir de la cámara de descarga que se sitúa en la parte superior. El proceso de compactación de la grava se favorece con la inyección continuada de aire a presión.
Las gravas rellenan la cavidad abierta y se compactan mediante ciclos de subida y bajada del propio vibrador de unos 40 a 60 cm de altura. Estos ciclos se repiten continuamente hasta alcanzar la superficie. En la figuras 4 y 5, se muestra el procedimiento de ejecución y características del equipo utilizado para esta actuación.
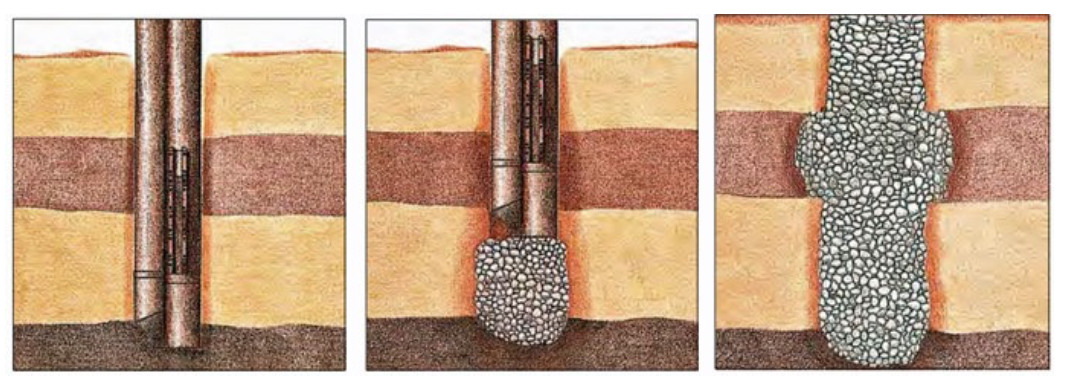
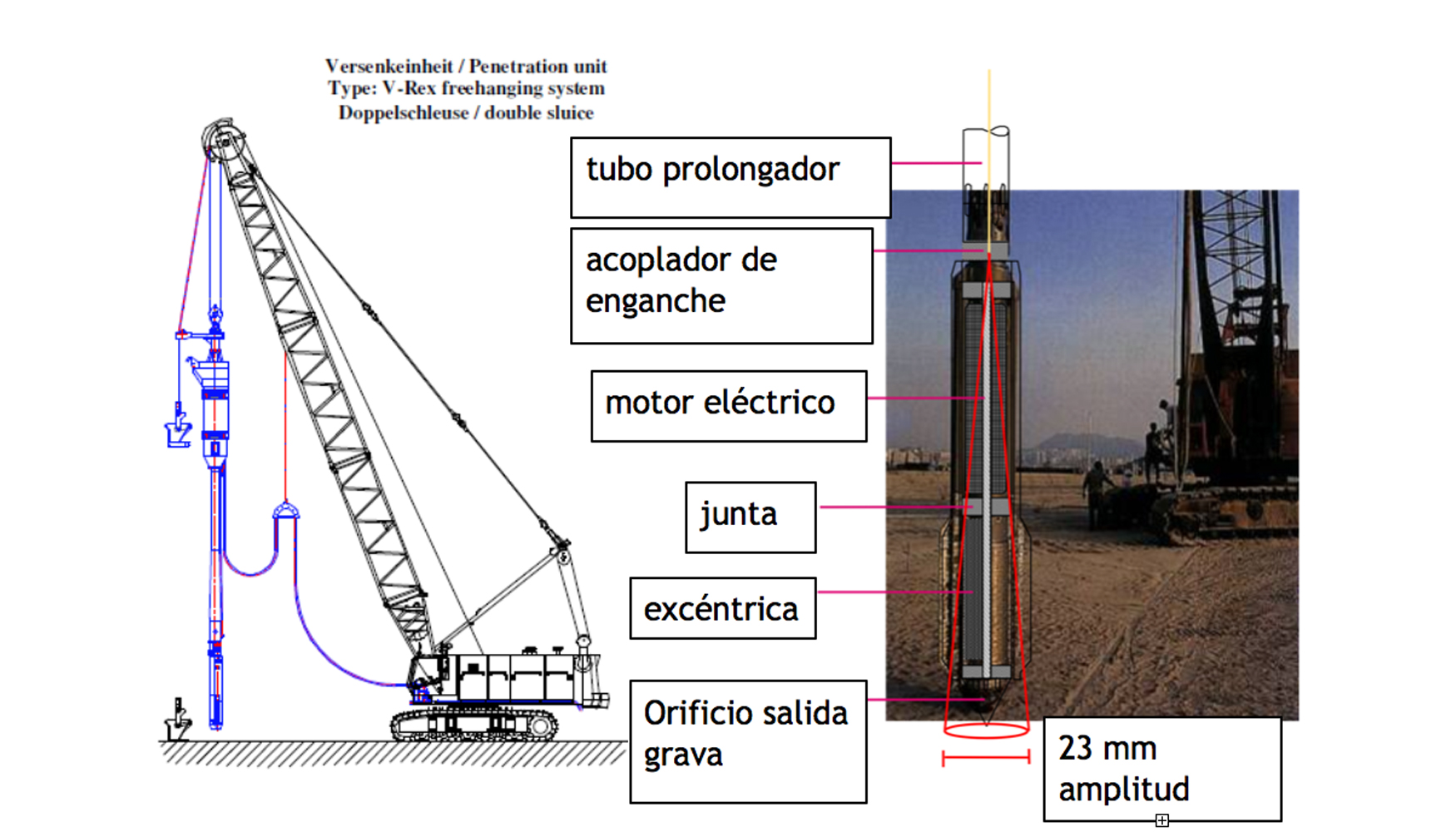
Los requerimientos del diseño del tratamiento fueron los siguientes:
- Capacidad portante según ELS mínimo de 200 kPa.
- Capacidad portante según ELU mínimo de 300 kPa.
- Rigidez dinámica de rotación mínima del cimiento de kφmin=80GN.m/rad. Lo que equivale a un módulo de Young para el terreno mejorado en su conjunto de 25Mpa.
- Factor mínimo de seguridad contra la licuefacción del suelo FS> 1,25 según EC8.
En cuanto al diseño de la solución, debe garantizarse la estabilidad durante la vida útil, para ello es fundamental una estimación correcta de la transferencia de cargas que recibe el terreno y un análisis de la deformabilidad relacionada con la rigidez rotacional.
Las comprobaciones del diseño fueron las siguientes:
a) Debido a que se trata de elementos muy esbeltos, la acción predominante en las hipótesis de cargas es el efecto del viento, esto se traduce en un importante momento que provoca fuertes excentricidades y concentración de tensiones. Por ello es necesario comprobar el ‘no despegue’ de la cimentación para las diferentes hipótesis de cargas.
En las siguientes tablas se muestran las diferentes hipótesis de combinaciones de cargas consideradas:
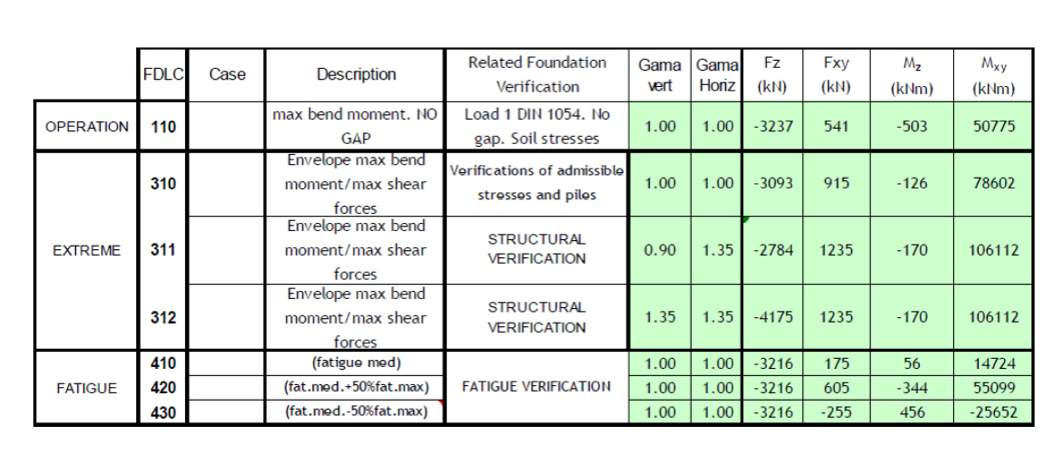
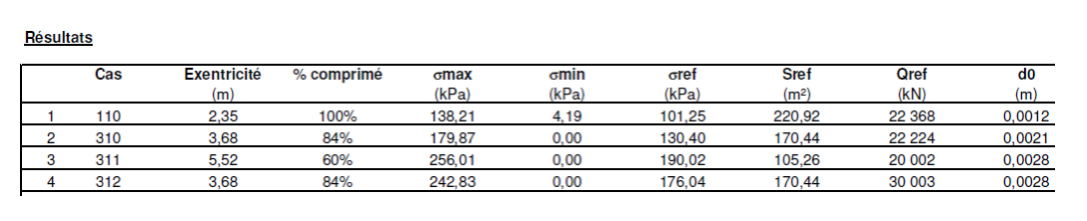
b) Comprobación de la capacidad de carga global considerando ELS y ELU del tratamiento en función del número de inclusiones del área a compresión, a partir de las siguientes expresiones:
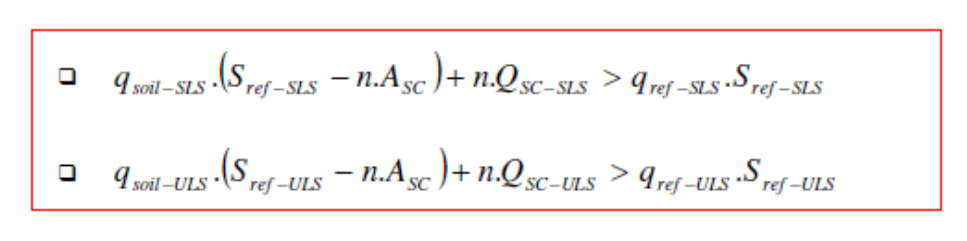
Considerando:
- QSC-SLS= Min (2xPle; 800kpa)=402 kN
- QSC-ULS= 1,5 x QSC-SLS= 603 kN
- n= número de columnas bajo la superficie comprimida.
- qsoil-SLS= kp Ple= 400Kpa/3= 133 Kpa
- qsoil-ULS= kp Ple= 400Kpa/2= 200 Kpa
Los resultados obtenidos para las diferentes hipótesis de cálculo se muestran la tabla 4:
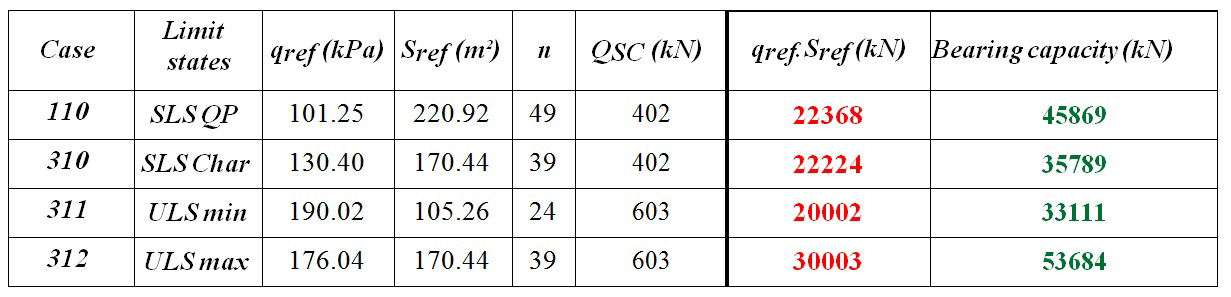
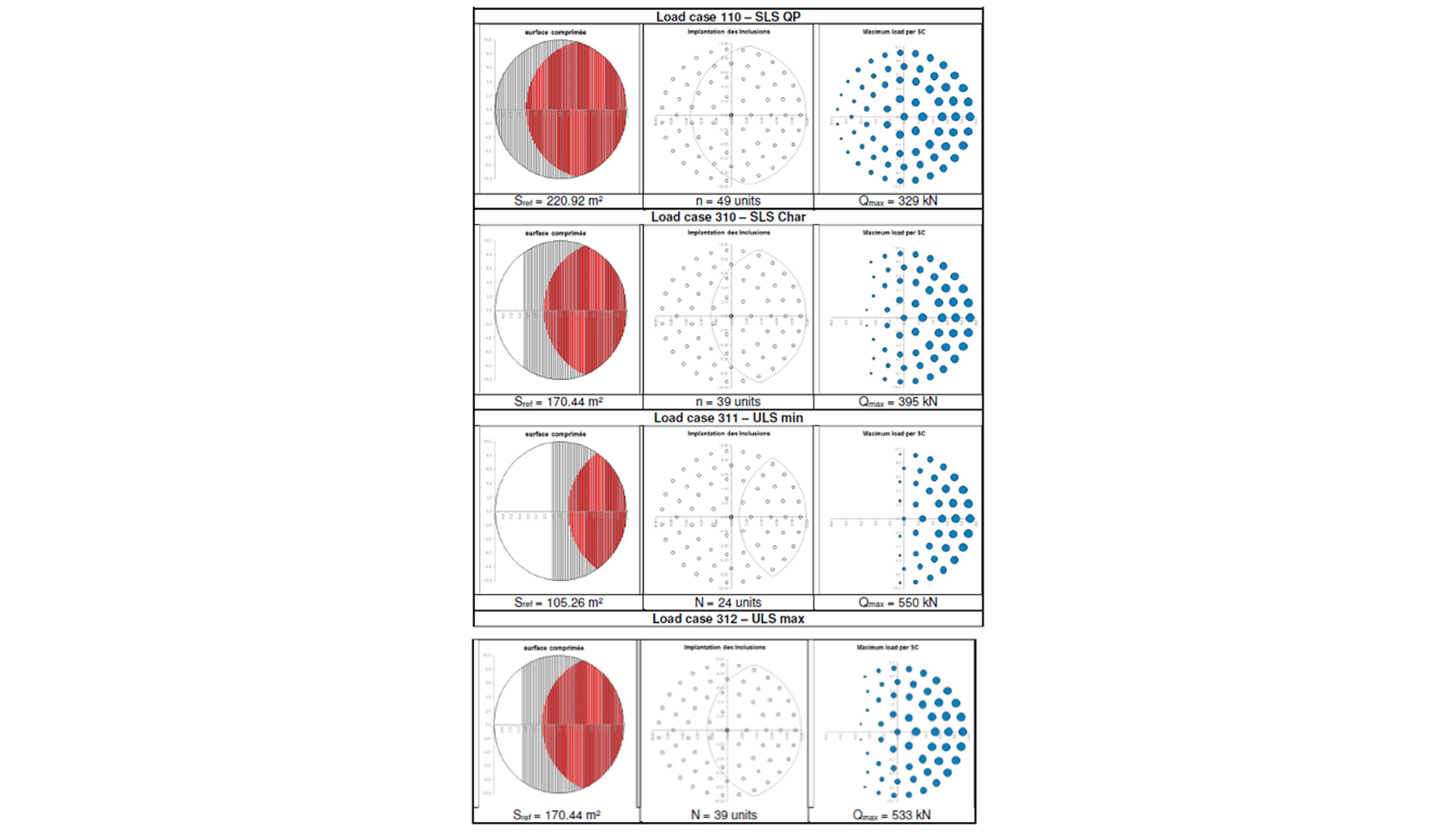
c) Verificación de la capacidad de carga local, es similar a la comprobación global, pero se aplica a la columna con mayor concentración de cargas.
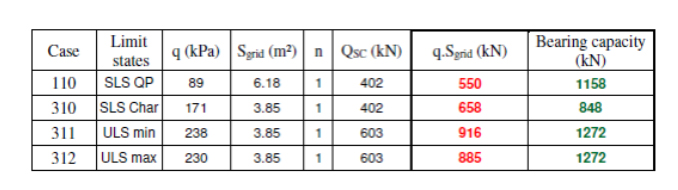
Tabla 5. Capacidad portante ELS y ELU inclusión.
Si consideramos que el 60% de la carga transmitida se la llevan las columnas de grava, comprobamos que no supera la carga última de rotura de la misma 402 Kn(ELS) y 603 Kn (ELU):
- Load case 110 (SLS qp): Qmax = 329 kN < QSC-SLS
- Load case 310 (SLS char): Qmax = 395 kN < QSC-SLS
- Load case 311 (ULS max): Qmax = 550 kN < QSC-ULS
- Load case 312 (ULS min): Qmax = 533 kN < QSC-ULS
d) Verificación de la rigidez dinámica.
Para comprobar que se cumple con la especificación marcada con relación a la rigidez dinámica, es preciso establecer el módulo de deformación del terreno mejorado.
Este módulo se establece a partir del modelo de homogeneidad, en base a la tasa de sustitución y módulo de deformación de la grava compactada.
Una vez establecido el modulo equivalente, se determina la rigidez rotacional a partir de la equivalencia del modulo dinámico G, a partir de las recomendaciones de Gazetas sobre la rigideces horizontal y rotacional para una cimentación circular bicapa:
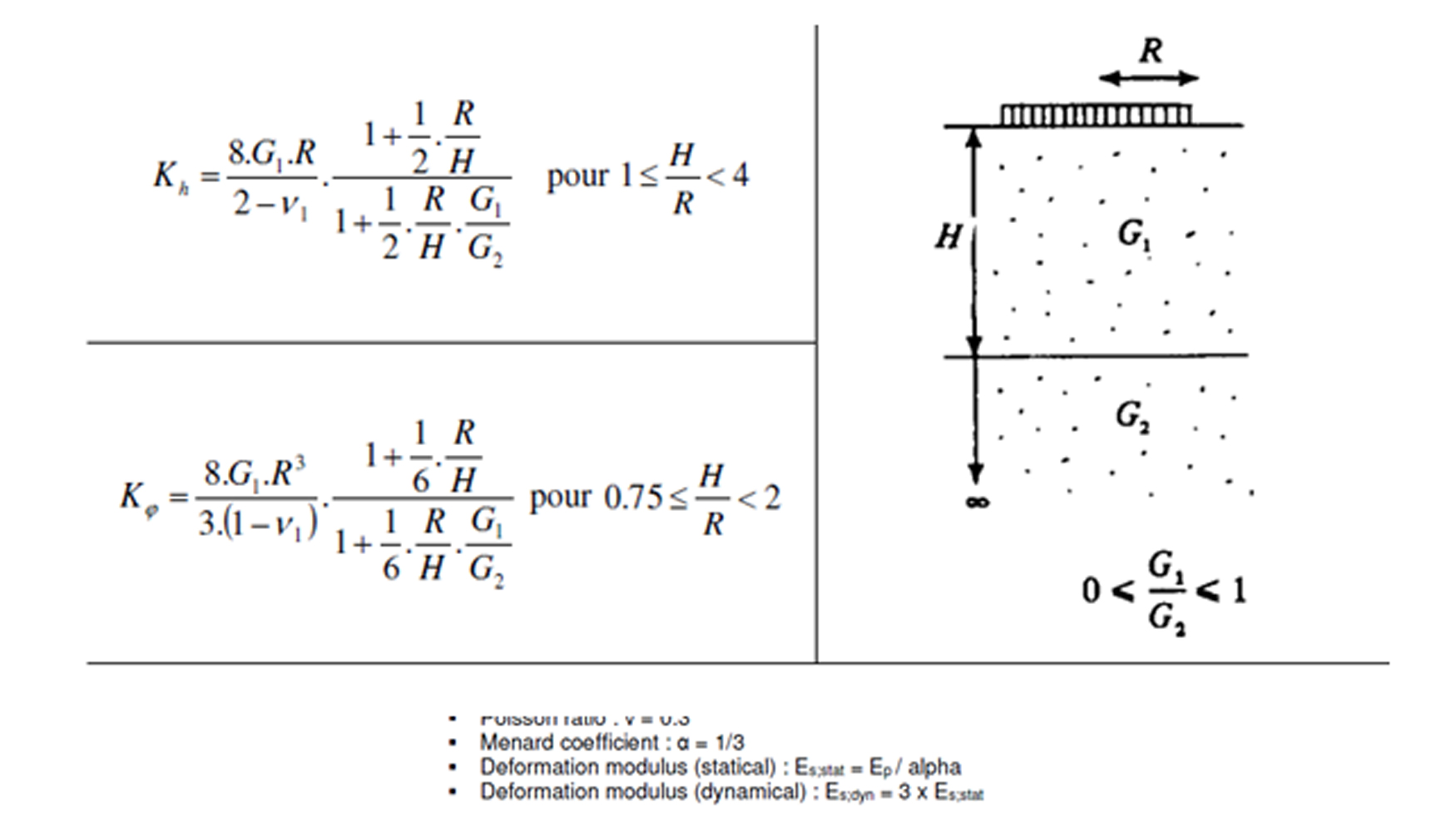
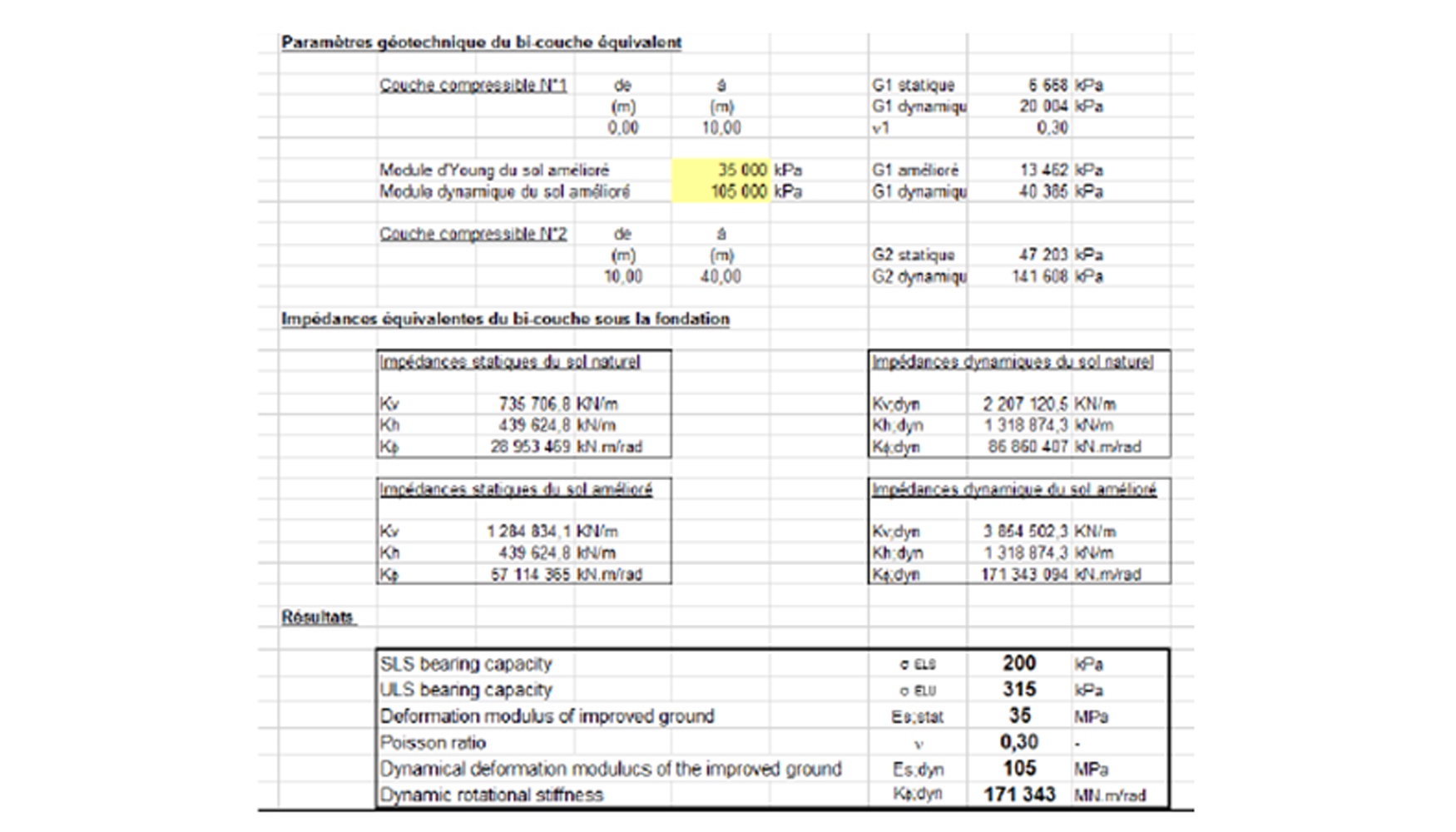
Para cumplir todos esos requisitos, el diseño de la solución de mejora fue el siguiente:
- Longitud de las columnas: las columnas se instalaron desde la plataforma de trabajo atravesando los niveles de arenas flojas hasta alcanzar el pie de la columna la capa de arena densa infrayacente. Las longitudes podían variar de 7,5 a 15 m, con una longitud media alrededor de 8-10 m.
- Diámetros: Ø 700 a 900 mm.
- Número de columnas por aerogenerador: 70 unidades/WT.
- Material de relleno: gravas de machaqueo limpias con huso granulométrico 8/40 mm, con un contenido en finos no superior al 2% y desgaste de Los Angeles < 35.
- Debido a la presencia discontinua de posibles capas de suelos cementados dentro de la profundidad tratada, se estimó la necesidad de apoyo para la ejecución de un equipo auxiliar de pre-perforación con barrena CFA con posibilidad de alcanzar 9 m de profundidad.
3.- Preparación logística
La preparación de los recursos y los medios necesarios para poder acometer una obra de esta naturaleza en un contexto de país como Mauritania, requiere de una correcta planificación y evitar todas las posibles incertidumbres para tener plenas garantías de éxito.
Dentro de este apartado se detallan las necesidades de gestiones previas de exportación, maquinaría, personal y suministros necesarios para acometer la obra:
Gestiones administrativas
a) El tiempo de preparación y movilización de los equipos fue de tres meses desde la adjudicación. Al no existir una ruta marítima comercial directa, el transporte de los equipos desde su embarque fue de aproximadamente un mes.
b) Gestión de todos los permisos de visado y expatriación del personal. Menard desplazó un equipo humano formado por siete personas y el apoyo de dos operadores locales.
c) Vacunación y reconocimiento médico del personal según las recomendaciones de Ministerio de Exteriores, con un mes máximo de antelación antes de la expatriación del personal, documento imprescindible a presentar a las autoridades para la entrada al país.
c) Gestión de Aduanas para la exportación temporal de equipos y materiales (packing list).
Movilizaciones de equipos
La movilización de equipos fue en su totalidad externa, exceptuando la retroexcavadora de base para la barrena de la pre-perforación y para el vuelco de la grava en la tolva.
Los equipos que intervinieron fueron los siguientes:
- Grúa de soporte 90 Tn modelo Caterpillar ZT 600HD, con una longitud de brazo de 25 m, capaz de levantar 12 Tn de peso en un radio de acción de 10 m.
- Tres vibradores eléctricos tipo V23 de 60Hz,130KW de capacidad de motor y 23 mm de amplitud.
- Tubo prolongador tipo Tremie, tolva móvil y cámara de alimentación.
- Dos barrenas de 500 mm de preperforación de tipo CFA, modelo DIGA PD25 sobre base retroexcavadora 30 (Tn), capaz de alcanzar 9 m de profundidad.
- Manipulador telescópico con cazo adaptado a las dimensiones de la tolva.
- Compresor 7 bares/17 m3.
- Grupo Atlas Copco de 200 KVAS.
- Torres de iluminación.
Para la movilización de todos estos equipos fue necesario cuatro contenedores más la grúa de celosía.
Búsqueda del suministro de la grava
Para acometer la obra fue necesario un suministro total de unas 10.450 Tn de grava. La grava fue gestionada por Elecnor antes de la llegada de los equipos.
Se realizó una comprobación de la calidad de ocho posibles graveras/canteras a lo largo de una gran área debido a la inexistencia de explotaciones válidas en las proximidades a la obra.
La grava debía cumplir los siguientes requisitos:
- Estar limpia, no se permite que la grava contenga finos.
- Granulometría limitada: 8-40 mm.
- Ángulo de rozamiento: φ=35 a 38º (grava natural) / φ=38 a 42º (grava de machaqueo).
- Desgaste de los Angeles (DLA) inferior a 35.
- Microdeval húmedo MDE < 35.
- DLA+MDE < 60
Explanadas, caminos de acceso y colchón de reparto
Para el acceso de toda la maquinaria para el montaje de los molinos y ejecución de las columnas de grava, fue necesario realizar numerosos caminos de conexión entre los molinos. Para ello, la constructora utilizó una planta de machaqueo para poder obtener materiales groseros de diferentes diámetros para el recebo y la corrección de las arenas existentes.
Para el colchón de reparto o capa de transferencia de carga (PLT) entre el suelo tratado y la cimentación, se dispuso de una capa de 30 cm de espesor de un suelo granular con un contenido en finos inferior al 35%, que cumpla una vez compactado un módulo de deformación en el segundo ciclo no inferior a 45 Mpa.
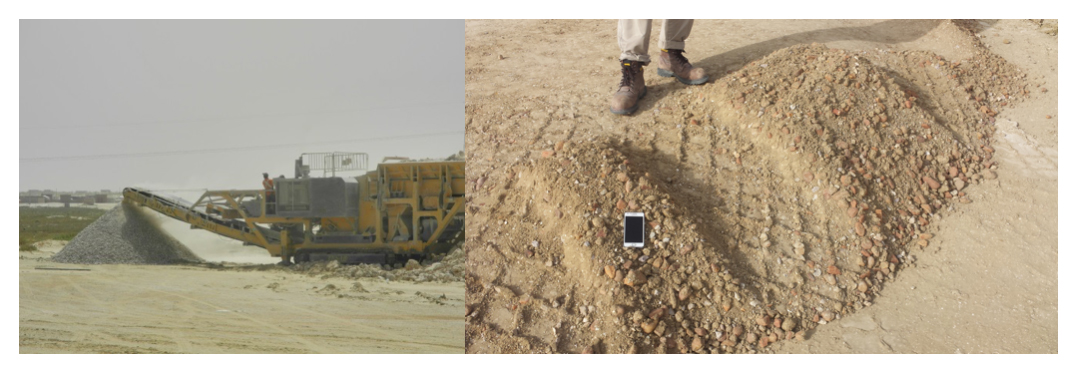
Figura 7. Detalle del material empleado en el colchón de reparto.
4.- Ejecución
Se ejecutaron un total de 1.050 columnas de grava de un diámetro medio de 80 cm, repartidos en las 15 posiciones, con distancias entre las mismas de 0,5 a 2 Km.
La medición total fue de 9.617 ml repartidas en un total de 74 turnos de 12 horas, con un rendimiento medio por turno de 130 ml, con picos de producción de 225 ml.
Los trabajos se llevaron a cabo en un plazo de 8 semanas (6 días de trabajo por semana a doble turno), contando a partir de la llegada de los equipos a obra. El montaje de los equipos se llevó a cabo durante cinco días. Comenzaron los trabajos el 8 de junio y finalizaron el 28 de julio de 2014, con jornadas de producción de 20-22 h al día y mantenimiento diario de unas 2-4 h de los equipos.
Las variaciones en los rendimientos por turno han estado condicionados a una serie de retrasos como consecuencia del alto mantenimiento de los equipos debido a diferentes causas que a continuación se detallan:
- Deficiente calidad del gasoil que provocaba tareas constantes de mantenimiento y cambio de filtros diarios e incluso por turno.
- Refrigeración de los equipos debido a las condiciones extremas de temperatura, 45 a 50º durante un buen número de horas y presencia de un elevado contenido de polvo en suspensión debido al constante viento procedente del Sahara.
- Dos días de paradas obligadas por tempestades de arenas, a pesar de estar fuera de los meses de ese fenómeno, y necesidad de limpieza de todos los útiles y sistemas de refrigeración de todos los equipos.
- Imposibilidad de encontrar recambios de garantías para las piezas básicas de mantenimiento o desgastadas por el propio trabajo de estos equipos.
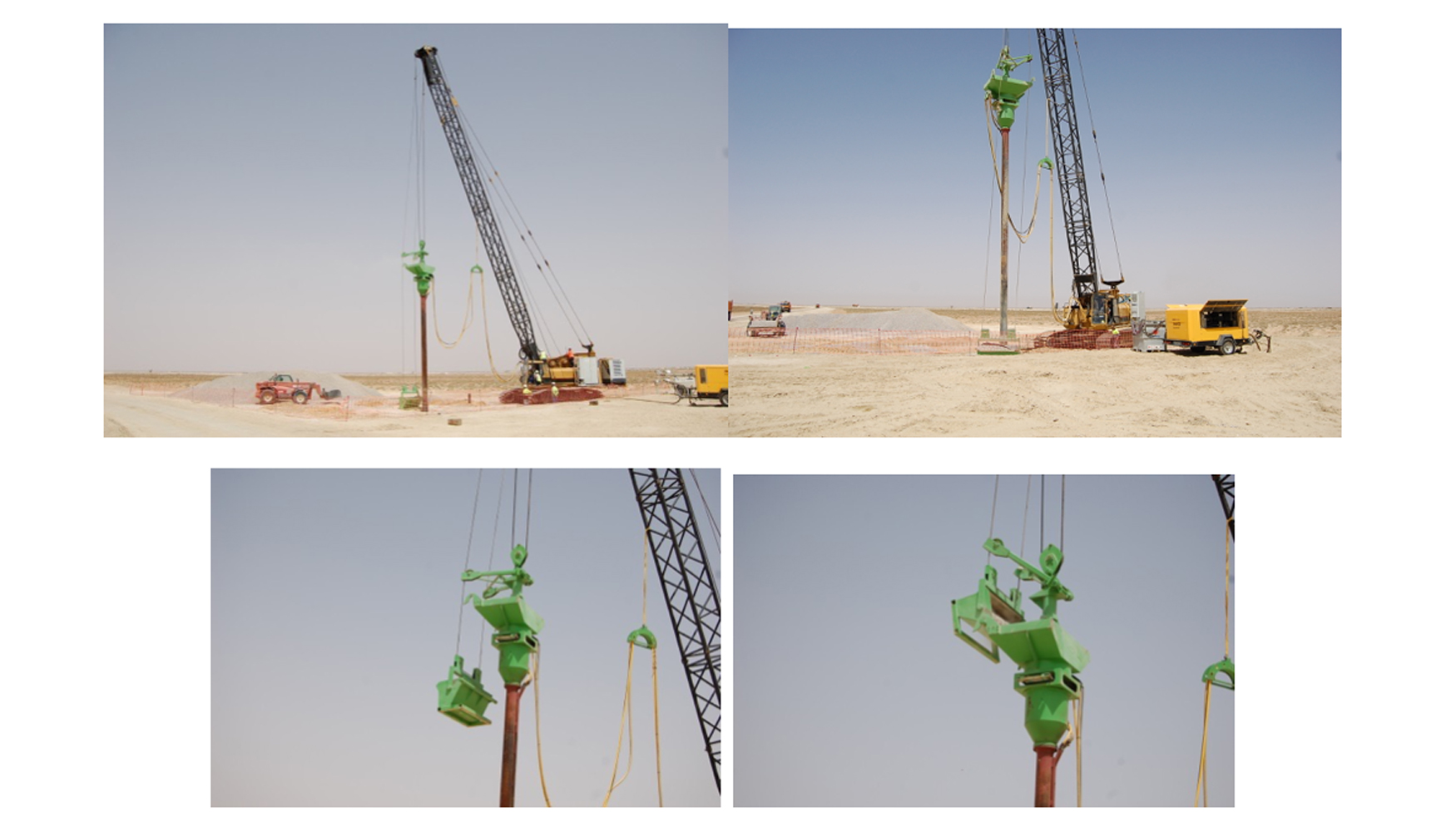
Figura 8. Detalle del equipo de columnas de grava empleado.
Desde un punto de vista de la propia ejecución, tanto las profundidades como tasa de reemplazo o sustitución se cumplieron acorde a lo estimado en el diseño previo sin desviaciones con respecto a lo establecido.
En la tabla 7 se detalla las profundidades medias obtenidas con respecto a las estimadas, así como el diámetro medio de las inclusiones en función de la grava aportada y la tasa de sustitución resultante.

Los controles de ejecución se llevaron a cabo a partir de los métodos habituales de esta técnica de mejora, resumiéndose en:
a) La profundidad de penetración del vibrador, se controló y vigiló por dos métodos: mediante indicadores de profundidad marcados a lo largo del tubo prolongador para el control visual por parte del equipo de operación y los supervisores; y a través de sensores del propio equipo que se registra automáticamente en ordenador del equipo.
A partir de las pruebas previas se fijaron las profundidades de rechazo a partir de los siguientes criterios:
- Se estableció como rechazo energías de consumo del vibrador de 200 amperios (rechazo del equipo)
- Velocidades de penetración con tendencia a cero, es decir no se produce avance en la perforación no menos de 30 sg y máximo de 60 sg con un estacionamiento del amperaje.
Si uno u otro criterio se alcanzan a las profundidades medias previstas según los datos geotécnicos, se considera que se ha alcanzado la profundidad de rechazo.
Si en alguna inclusión no se alcanzaba el rango de profundidad estipulada se procedía a repetirlas, para confirmar la dureza del terreno a una cota superior a la estimada según los datos geotécnicos previos.
b) Cada tolva de grava que se instalaba, se registraba digitalmente en el control de cabina por el operador de la grúa. Además también se llevó a cabo un control manual mediante un operador, pudiendo estimar el consumo de grava de cada inclusión ejecutada.
c) La compactación de la grava igualmente se controló a partir del amperaje durante el proceso de instalación. El amperaje consumido durante la perforación como durante la compactación se registra automáticamente y de forma instantánea en el ordenador de control de datos del propio equipo.
d) El diámetro medio de la columna de grava se calculó a partir del volumen total real de grava consumida con relación a la longitud real de la columna. En los registros digitales cada escalón de compactación permite estimar la variación del diámetro de la columna con la profundidad en función de la rigidez del suelo.
En la figura 9 se muestra un ejemplo de los registros de control sobre la ejecución de cada columna.
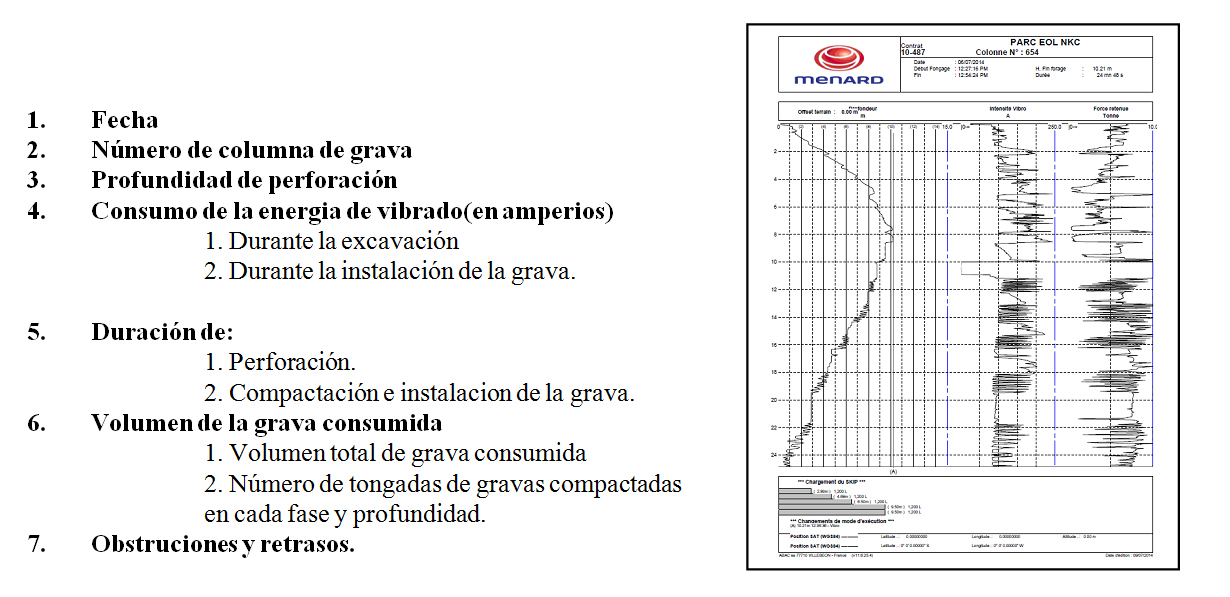
Figura 9. Ejemplo de registro de columnas de grava.
5.- Conclusiones
En este tipo de obras, cualquier eventualidad por pequeña que sea, puede llegar a constituir un problema importante en la producción. Es imprescindible una buena planificación de medios humanos y logísticos para tener éxito en la programación de los tiempos de ejecución y tener una respuesta rápida a todas las eventualidades que surgen a lo largo de una obra de esta tipología.
Con relación a la ejecución de la obra, los aspectos que condicionaron la productividad de la misma, se resumen a continuación:
- Necesidades de un elevado mantenimiento de la maquinaria debido a problemas con la pureza del gasóleo, refrigeración de los equipos debido a temperaturas extremas y el polvo en suspensión procedente del desierto.
- Inexistencia de repuestos básicos originales para cualquier tarea de mantenimiento y pequeñas averías. Lo que obligada a traerlos externamente, con tiempos de respuesta muy dilatados (prácticamente un mes de demora desde su pedido).
Por último, y como experiencia de cara a futuras actuaciones en dicha región se debe tener en consideración las siguientes conclusiones:
- Necesidad de personas de apoyo local para facilitar cualquier tipo de gestión desde las básicas a las logísticas.
- Personal especializado extra debido a las constantes indisposiciones del personal por problemas debidos a las condiciones extremas del país.
- Previsión de un gran número de consumibles de cara a las tareas de mantenimiento de los equipos.
- Expatriación de todo tipo de maquinaria, útiles para reparaciones, piezas, consumibles, etc (Autosuficiencia Absoluta).
Agradecimientos
Menard quiere agradecer la colaboración de Elecnor Infraestructuras por la autorización de la elaboración de este artículo.
Bibliografía
- Norma NF EN 61400 AEN/CTE-2005.
- Recommandations sur la conception, le calcul, l'execution et le contrôle des colonnes ballastees sous batiments et sous ouvrages sensibles au tassement.Version 2. Comité Français de Mécanique de sols (CFMS)- Union Syndicale Géotechinique (USG). Mars 2011.
- Recomendatións sur la conception, le calcul, l'execution et le contrôle des fondations d'èoliennes. Comité Français de Mécanique des Sols et de