Máquinas de cinemática paralela: implementación industrial y futuras tendencias
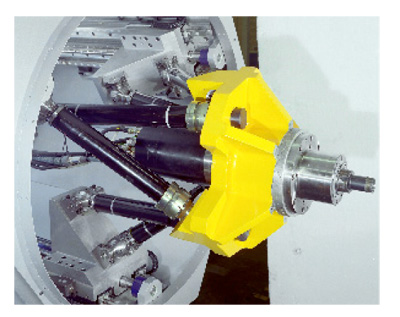
Breve historia
Las máquinas seriales (MCS), también llamadas 'máquinas convencionales', son las más comunes. Se construyen utilizando una arquitectura cartesiana. Los ejes de la máquina se colocan en una configuración en serie, alineados con los ejes cartesianos X, Y, Z. Estas máquinas son muy interesantes por su sencillez, especialmente en lo que respecta a su fabricación y su control. Sin embargo, esta configuración en serie supone también una perdida de dinamismo: cada accionamiento tiene que llevar el peso de los que le siguen. Son configuraciones con grandes masas en movimiento, por lo que resulta complicado obtener altas dinámicas.
Las máquinas-herramientas con 'arquitectura paralela' (MCP) por lo general tienen unos actuadores fijos en la estructura, o que se mueven muy próximos a ella. A pesar de los actuadores de movimiento, la principal ventaja de estas maquinas es que ninguno de los ejes debe llevar otro eje en movimiento; todos ellos conectan la estructura fija con el cabezal de corte o el efector. Como consecuencia de ello, los accionamientos pueden ser más pequeños, al igual que las masas en movimiento de la máquina.
El objetivo de construir máquinas-herramienta paralelas es (i) alcanzar mayores aceleraciones, y (ii) aumentar la rigidez de la máquina. El aumento de las aceleraciones se puede obtener debido a dos factores principalmente, la reducción de las masas y el factor de multiplicación.
Incremento de la dinámica
La capacidad de un robot o una máquina herramienta para alcanzar una alta dinámica está directamente unida al par (o la fuerza) que requiera en el movimiento. Por lo tanto, si el par requerido es bajo, el mecanismo será capaz de alcanzar mayores aceleraciones para un par máximo disponible. Se ha simulado un movimiento idéntico para el extremo del mecanismo. El movimiento impuso una aceleración lineal de 10 g y una velocidad de 6 m / s.
El resultado obtenido muestra que el par requerido en el accionamiento para el caso de la estructura serie es cuatro veces superior al par requerido en la estructura paralela. En consecuencia, si el accionamiento seleccionado es el mismo, las prestaciones dinámicas en la estructura paralela son cuatro veces superiores.
Incremento de rigidez
La figura 1 muestra un ejemplo. En uno de los extremos de los brazos, en el lado del cabezal, se disponen juntas esféricas. En el otro extremo se disponen juntas tipo cardan. Con esta configuración, no es posible transmitir esfuerzos de flexión a lo largo de los brazos, a la vez que los seis brazos soportan las fuerzas de corte.
En realidad, en comparación con las MCS, las MCP incrementan de forma muy importante la relación entre masa y rigidez. Es posible obtener la misma rigidez que una máquina cartesiana con mucha menos masa móvil y, en algunos casos, la rigidez se incrementa notablemente.
La figura 1 muestra la máquina Space 5H de Fatronik-Tecnalia. Se trata de una máquina de cinco ejes, con una parte paralela de tres ejes (dos rotaciones A, B y una translación en Z, igual que la figura 4) colocada sobre una columna vertical (eje Y) y dos mesas (eje X). Esta máquina tiene el sector aeronáutico como mercado objetivo.
La gran ventaja de esta máquina se encuentra en el sistema empleado para obtener las rotaciones. Los cabezales de giro convencionales están formados habitualmente por sistemas de engranajes y reducen notablemente la rigidez total de la máquina. Sin embargo, con la solución basada en cinemática paralela, dichos valores de rigidez se incrementan notablemente. La siguiente tabla muestra las diferencias entre un cabezal convencional y la solución de cinemática paralela.
En la máquina Space el ángulo de giro está limitado a 30º debido al diseño de las juntas. Según el proceso, este valor puede ser limitante, sin embargo, para la mayoría de las piezas aeronáuticas estructurales este valor es más que suficiente.

Nueva generación de MCP
Con la idea de mejorar estas dos limitaciones, se crea una nueva generación de máquinas de estructura paralela. La estrategia más común consiste en reducir los grados de libertad empleando elementos pasivos. En algunos casos, la máquina resultante es completamente paralela, como Ulyses de Fatronik-Tecnalia, mientras que en otros casos se combina la parte paralela con elementos serie (máquina Ecospeed de DS Technolgie and Space 5H de Fatronik-Tecnalia). Esta última solución es especialmente interesante en caso de que uno de los ejes sea muy largo.
La Universidad de Nantes (IRCCyN) ha realizado una comparativa entre MCS y MCP [PHD]. Este estudio comparativo incluye seis MCS y seis MCP de última generación. Dos de las MCS tienen tres ejes (SKM OO y SKM O), mientras que las cuatro restantes son de cinco ejes. Una de las máquinas de cinco ejes posee un cabezal twsit (SKM A), mientras que las otras tres tienen mesas de dos giros (SKM B, SKM C, SKM D). De las seis MCP, dos de ellas son totalmente paralelas (máquinas PKM E y PKM G) mientras las máquinas PKM F, H, I y J son máquinas híbridas (paralelo+serie). PKM-I es la máquina Verne y PKM-J es Space-5H, ambas de Fatronik-Tecnalia.
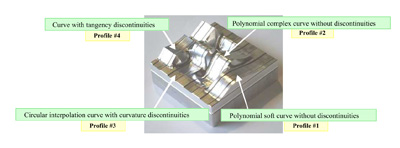
La figura 3 muestra la precisión de contorneado según distintas condiciones de mecanizado para MCS y MCP.
La figura 4 muestra la productividad de para diferentes máquinas. En el eje X se indica el modelo de máquinas, mientras que el Y refleja la productividad.
La principal conclusión de este estudio es que cada máquina necesita una optimización de todos sus parámetros y de sus condiciones de corte, para obtener así el mejor resultado, tanto en MCS como en MCP. Sin embargo, está claro que las MCP son capaces de realizar tareas de MAV con unos resultados comparables a MCS.
Durante la fase de diseño de las MCS es importante conocer las tareas que va a realizar la máquina, incluyendo los procesos de mecanizado.
En el caso de las MCP este análisis es, si cabe, más importante aún, dado que permite optimizar el volumen de trabajo necesario así como la rigidez de la máquina.
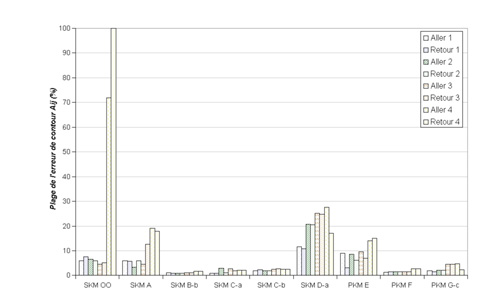
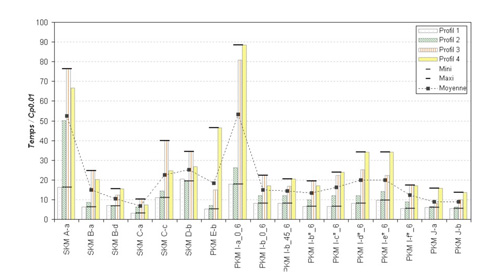
MCP en producción
Algunas de estas máquinas, implementadas industrialmente, son totalmente paralelas: de tres ejes, como la Quickstep de from Krause&Mauser, la SKM400 de Heckert o la Ulyses de FATRONIK-Tecnalia; de cinco ejes como la P800 de Metrom; o de seis ejes (HexaM de Toyoda y PM600 de Okuma).
Existen también estructuras híbridas, como la Ecospeed de DS Technologie, Hera o Verne, ambas de Fatronik-Tecnalia. Todas ellas combinan un cabezal de cinemática paralela de tres ejes (dos rotaciones y una translación) con dos ejes serie. Otra estructura interesante es la máquina Tricept, que combina una cinemática paralela de tres ejes con un cabezal de dos ejes de giro, para convertirse así en una máquina híbrida de cinco ejes. Otro concepto interesante es la máquina Pegasus de Reichenbacher. Esta máquina usa motores lineales, y el mismo secundario es compartido por ambos primarios.
Cinemática paralela en robótica
Este tipo de robots posee los actuadores fijos a la estructura base y un conjunto de brazos de fibra de carbono que unen la plataforma fija con la plataforma móvil. Mediante esta construcción, el mecanismo puede alcanzar altas prestaciones dinámicas. De hecho, los robots industriales (vendidos por ABB y Bosch) pueden alcanzar aceleraciones de 10 G, mientras que los robots serie de tamaño similar pueden alcanzar únicamente 2G.
Con la idea de obtener soluciones más rápidas, se ha desarrollado un nuevo mecanismo paralelo para las tareas de manipulación. Dicho robot ha sido desarrollado conjuntamente por el Lirmm (laboratorio Francés de robótica y microelectrónica de la Universidad de Montpellier) y Fatronik-Tecnalia (ver figura 5). Este robot fue patentado en 2005 y Adept posee la licencia de venta en exclusiva.
![Figure 5: Robot Quattro (Adept) [APT] Figure 5: Robot Quattro (Adept) [APT]](https://img.interempresas.net/fotos/214425.jpeg)
Otro campo de aplicación para los robots de cinemática paralela es la manipulación de alta precisión de componentes de pequeño tamaño, principalmente con plataformas de seis grados de libertad. En esta línea se sitúan el Paros, de Micos GMBH, el AC970-V de Acutronic o el Hexapod de Alio Industries.
Otras aplicaciones de robots de cinemática paralela son la manipulación de componentes para ensamblaje (Fanuc F-200 iB) y el doblado de tubos (Hexabend del Fraunhofer IWU).
Hoy en día, las máquinas de cinemática paralela son una realidad y se usan en procesos de mecanizado típicos: taladrado y fresado en tres ó cinco ejes. Como se ha mostrado, la productividad para el mismo nivel de precisión, puede ser mayor que la de las máquinas cartesianas estándar.
Las MCP pueden ser usadas sin ningún tipo de limitación en aplicaciones de media o baja precisión, en torno a las 20 ºm. Estas máquinas implican menores costes de producción debido al incremento de la productividad y los mismos costes de adquisición. El siguiente paso para las MCP es conseguir un nivel de precisión superior, con valores por debajo de las 20ºm y cercanos a 5 ºm.
Con la intención de alcanzar este objetivo, se están realizando labores de investigación y desarrollo en diversas líneas. La prioridad de estas líneas varía según el enfoque, sea del usuario o del fabricante.
Desde el punto de vista del usuario, los intereses principales son:
- Calibración: El proceso de calibración tiene que estar integrado como un elemento estándar en la máquina y tiene que ser realizable por el usuario en un corto espacio de tiempo, dos horas como máximo. Actualmente, en la mayoría de los casos la presencia del fabricante es necesaria, así como el uso de un complejo sistema de medición
- Estabilidad térmica: Dado que la mayoría de las MCP usan brazos largos para conectar la parte fija a la parte móvil, los cambios de temperatura pueden tener una influencia significativa en la precisión de la máquina. Es necesario por lo tanto integrar en las máquinas las estrategias adecuadas para controlar estos efectos.
- Desde la perspectiva del fabricante de máquinas, las principales líneas de trabajo son:
- Diseño mecánico: Optimización de máquina, análisis de prestaciones en la etapa de diseño, volumen de trabajo y análisis de puntos singulares.
- Integración en control: Integración de algoritmos de transformación básicos (cinemática directa/inversa). Integración de módulos de calibración y compensación térmica. Desarrollo de módulos para las transformadas de velocidad y aceleración. Modelado dinámico de máquina.
- Creación de trayectorias: Mejoras en la precision y la productividad de la máquina debido al empleo de trayectorias no convencionales.
- Modelado dinámico: Creación de modelos dinámicos de máquina. Empleo de estos modelos para maximimar productividad y precisión.
- Calibración: Desarrollo de estrategias y métodos para calibración en la industria. Determinación de medidas redundantes para calibración y/o compensación.
- Estabilidad térmica: Modelado térmico de máquina. Definición de sensores para medición y estrategias de compensación.
Referencias
[Dougas02]
Dugas A., Terrier M., Hascöet J.Y., Free from surface measurement met hod and machine qualification for high speed milling, 4th Int. Conf. on Integrated Design and Manufacturing in Mechanical Engineering, Clermont-Ferrand (France), Mai 2002
[Dougas03]
Dugas A., Lee J.J., Terrier M., Hascöet J.Y., Development of a Machining simulator considering Machine Behaviour, Int. Jl. Of Engineering Manufacture Volume 217/B, pp 1333-1339, 2003
[PHD]
Thèse de Doctorat, Myriam Terrier, 09/2005
[APT]
Adept (www.adept.com), acceso a página web 11/2007.