Perspectivas de futuro de las aplicaciones industriales del láser
Las ventajas del mecanizado con láser son la alta flexibilidad con respecto a los materiales, la alta productividad, la capacidad de automatizar los procesos y el poco calor que aplica al material; lo que garantiza menos modificaciones metalográficas en la zona afectada y una distorsión menor que con otros sistemas.
La principal ventaja de la soldadura con haz láser son, por un lado, la alta intensidad de energía que se aplica a la pieza mecanizada, lo que implica una penetración profunda de dicha energía.
En este contexto, algunas de las rutinas de láser en la industria de la automoción, son la soldadura del láser de techo, del tubo de escape, la perforación, la soldadura de los cilindros de freno o el corte de texturas de la bolsa de aire. Sin embargo, cada vez son más las aplicaciones que se emplean en éste y en otros sectores.
Coches más ligeros
Los materiales más utilizados para reducir el peso de los automóviles son el aluminio, el magnesio, el titanio, los polímeros de fibra reforzada y las espumas de metal. Estas últimas son entre el 25 y el 90% menos densas en comparación con los respectivos materiales masivos [1]. [...]
Desarrollar una construcción orientada hacia la reducción de peso implica una combinación de materiales tomando en cuenta las ventajas óptimas de las propiedades del material requerido al peso mínimo: fuerza mecánica, absorción de energía, y amortiguación de vibraciones. Tal enfoque también incluye los materiales inteligentes que adaptan sus características a los impactos exteriores. Por lo tanto, los usos futuros del láser tienen que centrarse en las técnicas de proceso para estos materiales y combinaciones de materiales. [2]. Los procesos que permiten conservar las propiedades específicas de la espuma son importantes.
En el láser Zentrum Hannover e.V., ya se han alcanzado los primeros éxitos en la soldadura de láser de espumas de aluminio [3].
El objetivo de los fabricantes de automóviles es utilizar la positiva relación rigidez-masa integrando estructuras de espuma en la parte posterior o en la parte inferior de la carrocería [4, 5], lo que permite una mejora significativa de la rigidez torsional de la misma. El empleo de las estructuras de espuma como sustituto para las placas inferiores convencionales ya se presentó en unos primeros estudios [5, 6].
Las investigaciones sobre la soldadura de láser de las espumas de aluminio han demostrado que pueden surgir problemas al procesar este material. Al utilizar el láser durante el ensamblaje, la espuma se colapsa durante la transición de sólido a líquido. Después, en el proceso de fabricación de espuma, el elemento espumante (TiH2) está principalmente presente en forma de residuos metálicos y no se puede asegurar que el metal fundido por el láser vuelva a espumar. [7].
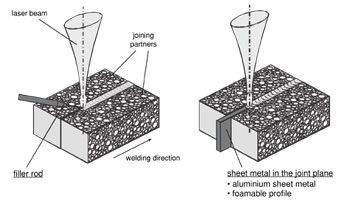
Soldadura de acero
Una forma de minimizar los errores al posicionar el haz y de reducir la demanda de pequeña tolerancia a los componentes es usar procesos híbridos en los que se combinan láser con soldadura de arco.
Otra técnica que puede mejorar la calidad del ensamblaje y aumentar la velocidad del proceso, así como la profundidad de la soldadura es el uso de técnicas de doble foco, que combinan dos haces láser. Por ejemplo una combinación de un diodo con un Nd:YAG hace posible disfrutar de las ventajas de ambos.
Además de las construcciones ligeras, otro reto de la ingeniería de producción y que ha dado lugar a nuevas tecnologías es el cambio de la líneas de diseño exterior del coche. Las piezas de la carrocería de gran tamaño y complejidad no pueden ser fabricadas como piezas únicas sin usar técnicas de corte. Ello implica la existencia de uniones, que son visibles puesto que son exteriores. Se requiere pues de técnicas de ensamblaje que satisfagan los más altos estándares de calidad respecto a apariencia, resistencia mecánica y a la corrosión, etc.
Una nueva tecnología que aumenta la productividad es la aplicación de sistemas de soldadura láser remotas, proceso en el que el haz es guiado con espejos de escaneo y alcanza la pieza por un lado. La velocidad de soldadura no se incrementa, pero el tiempo de post-procesamiento se puede reducir debido a que la velocidad del haz es de más de 100 m/min. Esto requiere un láser de CO2 de alta calidad, o un láser de disco bombeado por diodos [16, 17, 18]
Los haces láser siempre son guiados por sistemas automáticos con la excepción de las aplicaciones médicas. Otra tecnología que actualmente se desarrolla son los sistemas que permiten guiar el láser de modo manual para ser aplicados en procesos de soldadura de pequeñas series, con el objetivo de ahorrar los costes de programación de los sistemas automáticos.
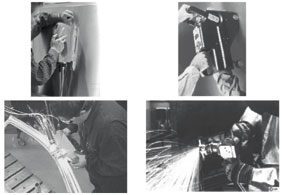
Para los componentes pequeños, como boquillas de inyección o elementos sensores, y siguiendo la tendencia de continua miniaturización de los componentes, se necesitan nuevos métodos de micro-mecanizado. Desde hace tiempo existen procesos de tal tipo basados en la tecnología láser. Sin embargo, los sistemas láser convencionales están limitados en relación a su capacidad de mecanizar estructuras en escalas micrométricas. Los láser de femtosegundo ofrecen un gran potencial para la ablación de cualquier tipo de materiales con un daño mínimo [23]. Metales, e incluso materiales transparentes o materiales muy sensibles a la temperatura se pueden mecanizar con precisión con unos efectos secundarios despreciables. Una de las aplicaciones más prometedoras es el perforado de boquillas de inyección de combustible [24]. Las especificaciones actuales (diámetros de agujero de 250 µm en materiales de 1 mm de espesor, sin rebabas y con gran reproducibilidad) para las boquillas se pueden conseguir por medio de electroerosión o microperforación. Sin embargo, los diseños del futuro exigirán diámetros significativamente menores de 100 µm y ángulos de incidencia no rectángulos, con el fin de proporcionar un menor consumo de combustible y una mayor potencia. Estas especificaciones superan las posibilidades de los métodos convencionales. Sin embargo, los láser de pulsos ultracortos parecen cumplirlas.
La industria del automóvil se ha tomado como ejemplo para mostrar las posibles tendencias para futuras aplicaciones láser. Las mismas jugarán un papel significativo tanto en la industria del automóvil como en otros sectores industriales. Además, se incrementará el número de aplicaciones existentes. Las tendencias en las aplicaciones láser se moverán en consonancia con las tendencias hacia la reducción de consumo energético, las construcciones ligeras y la continua miniaturización de los componentes.
Referencias
- Ostermann, F.: Anwendungstechnologie Aluminium. Springer-Verlag Berlin Heidelberg, 1998, Germany
- Sedliaková, N. et al.: Joining of Aluminum Foams, Metallschäume, (Ed. Banhart J), Verlag MIT Bremen, Germany, 1999, p. 177 -185
- Haferkamp, H., Goede, M., Bunte, J.: Metallschäume mit dem Laserstrahl schweißen,Blech Rohre Profile (10/99), Meisenbach-Verlag, Bamberg, Germany, 1999, p. 36-40
- Kretz, R., Hombergsmeier, E., Eippner, K.: Manufacturing and testing of aluminium foam structural parts for passenger cars demonstrated by example of a rear intermediate panel, Metal Foams and Porous Metals Structures, (Ed. Banhart J, Ashby M F, Fleck N A), Verlag MIT Bremen, Bremen, Germany, 1999, p. 23-26
- Seeliger, H. W.: Application Strategies for Aluminum-Foam-Sandwiches, Metal Foams and Porous Metals Structures (Ed. Banhart J, Ashby M F, Fleck N A), Verlag MIT Bremen, Germany, 1999, p. 29-36
- Thurow, W. D.: Die Potenziale der Werkstoffe aus der Sicht der Automobilindustrie, Stahl, Aluminium, Magnesium im Wettbewerb, Stuttgart, Germany, 1998
- Haferkamp, H., Ostendorf, A., Goede, M., Bunte, J.: Potential of Laser Welding of Metal Foam, Proceedings of MetFoam2001, 18.-20.06.2001, Bremen
- Dilthey, U., Ghandehari, A., Keller, H, Budak, I.: Leichtbau mit Stahlwerkstoffen - schweißtechnische Voraussetzungen. In: Proceedings Große Schweißtechnische Tagung, 11. - 13. September, Essen (2001), p. 7-12
- Prange, W., Engl, B.: Innovative Stahlwerkstoffe für den Karosseriebau von morgen. In: Proceedings Tag der Karosserie, 4. Oktober, Aachen (1999), p. 1-16
- Brenner, Gnann, Duschek, Lynen, Beyer: Laser Induction welding of hardenable Steels, Proceedings ICALEO, 17. - 20. Nov, San Diego, USA (1997)
- Beyer, E., Imhofff, R., Neuenhahn, J.: A new welding technique and device for enhanced welding efficiency. In: Proceedings IBEC, 26. - 29. September, Detroit, USA (1994) , p. 101-103
- Diltey, U., Lueder, F., Wieschemann, A.: Technical and economical advantages by synergies in laser arc hybrid welding, Proceedings IIW International Conference The human factor and it’s environment, 19. - 20. Juli, Lisboa, Portugal (1999), p. 141-152
- Petring, D., Kaierle, S., Dahmen, M., Kasimir, M., Cottone, F., Maier, C.: Extended range of applications for laser beam welding by laser-MIG hybrid technique. LaserOpto, 33 (2001) Nr. 1, p. 50-55
- Geiger, M., Schultz, M., Hoffmann, P., Hutfless, J.: Welding of Aluminium Alloys with a CO2-Laser of High Beam Quality., Takács, J., Göndöcs, B. (Hrsg.): 2. International Colloquium Advanced Manufacturing and Repair Technologies in Vehicle Industry. Balatonfüred (1995), p. 78-84.
- Haferkamp, H., Ostendorf, A. Bormann, A.: Innendruckumformen mit von Aluminiumplatinen mit gestaltbestimmender Laserstrahlschweißnahtanordnung, Abschlussbericht EFB/AiF, 2001
- Frauenpreiss, T.: Hochgeschwindigkeitsschweißen mit frei geführtem Laserstrahl, Maschinenmarkt, 24/2000, p. 32-33
- Heston, T.: Remote Laser Beam Welding Shows Potential in the Body Shop, Welding Journal, June 2000, p. 39-42
- N.N.: Fraunhofer-Institut für Werkstoff- und Strahltechnik: lasertronic-Systeme aus dem Fraunhofer IWS Dresden. Dresden, 2001. Firmenschrift
- Haferkamp, H., Goede, M., Schmid, C., Drygalla, M.: Manually operated laser welding and cutting device. MM Industrial Magazine Western Europe, Vol. 16, No. 3, Sept 2000, p. 27-29
- Haferkamp, H., Drygalla, M., Goede, M., Schmid, C.: Hand-Guided Laser Material Processing, Proceedings of the SheMet International Conference, 17.-19.4.2000, p. 291-300
- Haferkamp, H., von Busse, A., Thürk, O., Goede, M.: Welding of Automotive Polymeric Components Using Laser Radiation, Proceedings ATTCE 2001 (Automotive Transportation Technology Conference and Exhibition), Vol. 3 Manufacturing, p. 51-58
- Haferkamp, H., Goede, M., Thürk, O.: Einsatz von Lasern in der Kunststofftechnik, Tagungsband “Laserschweißen von Kunststoffen; Potential und Grenzen eines neuen Verfahrens”, 18.01.2000, Essen, p. 21-36
- Nolte, S., Kamlage, G., Korte, F., Bauer, T., Wagner, T., Ostendorf, A., Fallnich, C., Welling, H.: Microstructuring with Femtosecond Lasers, Advanced Engineering Materials 2000, 2, No. 1-2, Feb. 2000, p. 23-27
- Tönshoff, H. K., Ostendorf, A., Nolte S., Kamlage, G., Wagner, T., Korte, F., Bauer, T.: New Applications of Femtosecond Lasers in Micromachining, Proceedings
of the 1st euspen Topical Conference on Fabrication and Metrology in Nanotechnology, Vol. 1, Copenhagen, 28.-30.5.2000, p. 10-17