Control microbiano, la clave para alargar la vida útil de las emulsiones de aceite
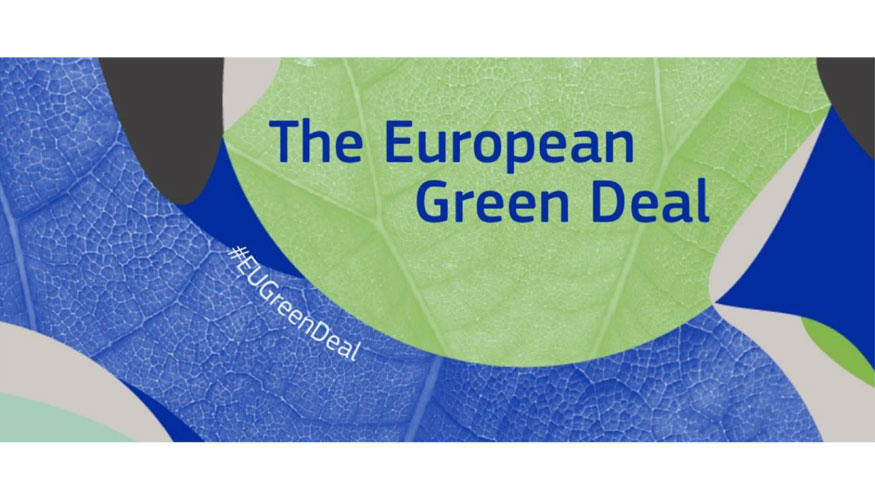
En el sector del mecanizado, con el fin de dar respuesta a esta demanda el objetivo ha sido reducir —incluso eliminar si es posible— los fluidos de corte de los procesos de corte. Concretamente esta línea comenzó con el desarrollo de la lubricación MQL (mínima cantidad de lubricación) caracterizada por utilizar como fluido de corte un aceite biodegradable pulverizado en forma de aerosol cuyas partículas tienen un diámetro de 10 micrómetros aproximadamente. Gracias a ello, permite una mejor penetración en la interacción filo/viruta que hace que su capacidad lubrificadora sea excepcional y por tanto el desgaste de herramienta sea constante y no exponencial. Esta tecnología es idónea para el mecanizado de materiales donde los esfuerzos mecánicos prevalecen sobre los térmicos. Por el contrario, si el estrés térmico prevalece sobre el estrés mecánico en el filo de la herramienta, posteriormente se desarrolló la refrigeración criogénica. Esta tecnología, inicialmente utilizaba nitrógeno líquido (LN2) como fluido de corte debido a su poder refrigerante. Sin embargo, desde el punto de vista industrial y práctico el dióxido de carbono licuado (CO2) ha sido el fluido de corte por excelencia. Finalmente, en caso de que el material a cortar implique tanto carga térmica como mecánica extrema sobre el filo de la herramienta, la tecnología CryoMQL desarrollada bajo la licencia BeCold la cual combina ambas tecnologías es actualmente la opción más adecuada para el día a día de los talleres ya que con ella se obtiene un balance entre tecnología y medioambiente.
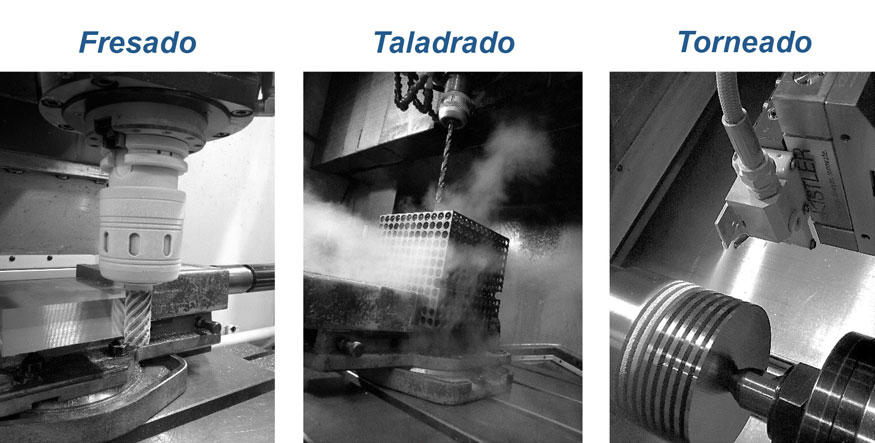
Sin embargo, a pesar de obtener resultados satisfactorios con dichas tecnologías, su implantación industrial tiene que pasar por un período de adaptación en el que se sigan utilizando fluidos de corte convencionales basadas en emulsiones de aceite (taladrinas) principalmente. El uso de la taladrina bien es sabido por los mecanizadores que a pesar de que tecnológicamente ha sido imprescindible desde tiempos inmemoriales su uso implica el sufrimiento de patologías ambientales, así como un coste tanto económico como medioambiental. Entonces, tratar de minimizar el impacto económico y ambiental que generan las taladrinas a través del alargamiento de su vida útil es una forma de poder dar respuesta a estas necesidades en este período de transición.
Consecuentemente, en este artículo se expondrán los mecanismos de degradación de la taladrina, así como las investigaciones y desarrollos más relevantes llevadas a cabo que buscan el alargamiento de la vida útil de la taladrina y así lograr atravesar este período de transición hacía la fabricación ECO2.
En pocas palabras… ¿Cómo y por qué se degrada la taladrina?
La degradación de la taladrina es un hecho que todo mecanizador conoce y contra con la que lucha en la medida de la posible para que sea lo menor posible, pero ¿cuáles son las causas reales de degradación de la taladrina? ¿por qué ocurre? La respuesta a estas preguntas es sencilla, la degradación de la taladrina es causada por la proliferación de microbios en su interior. Sin embargo, la respuesta a qué causa esta proliferación y cómo consecuentemente se acorta la vida útil de la taladrina es algo más larga.
Como es sabido, la taladrina debe tener un pH entre 8-9,5 con una concentración de aceite de entre el 5-10% para que esté en perfectas condiciones. Asimismo, se debe controlar la concentración de nitratos y nitritos la cual debe de estar por debajo de 50 mg/l y 20 mg/l, respectivamente. Finalmente, las colonias microbianas deben estar por bajo de 107 cfu/ml ya que si está por encima de esta concentración la taladrina se corrompe y deja de ser útil como fluido de corte. Estos parámetros están relacionados estrechamente y una variación en cualquiera de ellos se traduce en un aumento de la concentración bacteriana, corrompiéndose entonces la taladrina y causando malos olores, dermatitis y problemas respiratorios [Ma et al. 2018, Park et al. 2010].
Concretamente, en la taladrina se encuentran principalmente bacterias y hongos. La influencia de estos en la degradación de la taladrina viene dada principalmente en función qué tipo de microbios son predominantes en su interior, es decir, si predominan los microbios aeróbicos o anaeróbicos, trabajando cada tipo de microbio en una etapa diferente del proceso de degradación de la taladrina. Inicialmente, en la taladrina hay un predominio de los microbios aeróbicos (bacterias y hongos) ya que existe oxígeno en su interior y también penetra la luz por lo que permite hacer la fotosíntesis dichos microbios. Como resultado de este proceso, por un lado, los hongos hacen que la taladrina se oscurezca y por otro las bacterias separan el agua del aceite generando una película de aceite en la parte superior de la taladrina. Esta película hace que deje de penetrar nuevo oxígeno en el interior de la taladrina y por tanto en pocas horas el oxígeno disuelto en la taladrina se termina. En esta etapa, en la capa más profunda de la película de aceite (que contienen también microbios aeróbicos) se forman celdas galvánicas locales, que se caracterizan por pequeños ánodos y grandes zonas catódicas que provocan la corrosión metálica. Además, en el interior de las taladrinas algunas de las bacterias son capaces de cambiar su metabolismo aeróbico a anaeróbico y entonces comienzan el proceso de reducción de sulfato que degrada el sulfato en sulfuro de hidrógeno. Este proceso, combinado con la despolarización catódica, amplía las actividades de corrosión en toda la emulsión de aceite, afectando a sus propiedades de lubricación [Morpeth, 1995]. Además, la reducción de los sulfatos y la degradación de los nitratos/nitritos, que también se inicia en esta fase, son la causa de los extraños olores de las emulsiones de aceite [Walther, 2012].
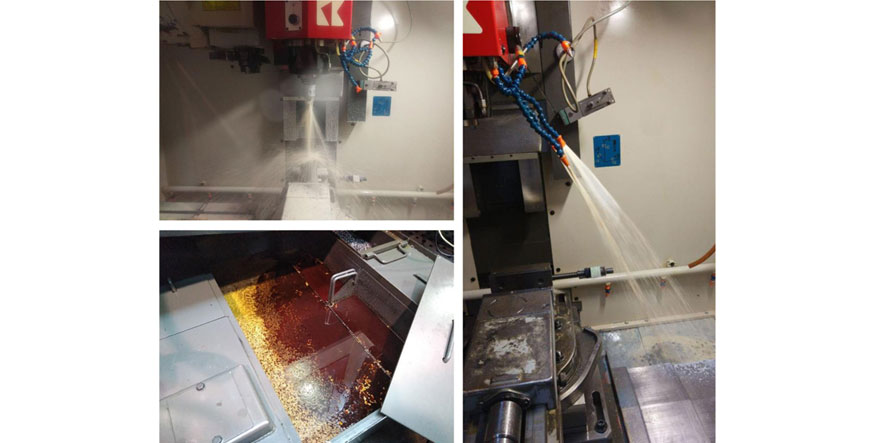
Por ello, como se puede apreciar, controlar la proliferación de bacterias es el punto crítico para poder alargar la vida útil de las taladrinas y así reducir su actual impacto ambiental.
Investigaciones y desarrollos llevados a cabo para el mantenimiento de la taladrina (1940 – Actualidad)
La preocupación del alargamiento de la vida útil de las taladrinas viene de lejos, concretamente en 1940 ya se puede encontrar literatura al respecto. Concretamente en Lee and Chandle 1940 se propuso introducir dióxido de carbono (CO2) en forma gaseosa en el depósito de la emulsión de aceite de tal modo que a las 3 horas los microorganismos eran eliminados en un 90%. Sin embargo, la necesidad de altas concentraciones de CO2 implica el riesgo de asfixia por parte de los operarios ya que el CO2 desplaza al oxígeno al pesar más que éste.
Otra técnica propuesta en 1983 y aún utilizada en la actualidad se encuentra en Shennan 1983. Esta técnica consiste en el uso de biocidas como derivados fenólicos, formaldehidos, derivados alifáticos entre otros para el control de los microorganismos. Sin embargo, estos biocidas implican un riesgo para la salud de los trabajadores ya que causa irritación de la piel, reacciones alérgicas y problemas respiratorios. Además, existe el riesgo de que a través de las pérdidas de emulsión de aceite producidas por fugas hidráulicas y procesos de limpieza acabe en el sistema de alcantarillado y por tanto cause problemas medioambientales. Por tanto, aunque esta técnica es efectiva, debe ser reducida o sustituida por técnicas menos agresivas medioambientalmente y para aumentar la salubridad de los puestos de trabajo.
Una alternativa al uso de elementos químicos como los biocidas es el uso de ozono (O3) o radiación ultravioleta tipo C (luz UV) como agentes esterilizantes que eliminen los microorganismos de la emulsión de aceite. A pesar de que estos elementos son prácticamente inocuos, por sí mismos presentan problemas para su aplicación en los depósitos de almacenaje de emulsión de aceite. En el caso del ozono, este puede ser inyectado en el depósito de la emulsión de aceite, logrando eliminar eficazmente los microorganismos debido a su fuerte acción oxidante. Sin embrago, la generación de O3 implica un alto gasto energético además de la necesidad de grandes de espacios para ubicar dichos generadores, lo que se traduce en un aumento del impacto ambiental (Ma et al. 2018).
Por otra parte, el uso de luz UV como agente esterilizante de pequeñas cantidades de emulsión de aceite presenta una alta efectividad. Por ejemplo, en Johnson and Philips 2002 y en Saha et al. 2014 se aplicó a nivel de laboratorio logrando eliminar el 90% de los microorganismos presentes en la emulsión de aceite. Sin embargo, en depósitos industriales – que pueden ir desde los 500 litros hasta más de 1.500 litros – la luz UV resulta ineficiente. Este caso se dio en Coogan 2005, donde la aplicación de luz UV a nivel industrial se tradujo en una eficacia del 10% debido a que la emulsión de aceite en el depósito presenta turbulencias además de ser opaca y por tanto la luz UV es bloqueada, no penetrando en el interior del depósito.
Con el fin de solventar esta problemática y por tanto poder aplicar la luz UV en la eliminación de microorganismos presentes en las emulsiones de aceite a nivel industrial en CN203715587U se desarrolló un equipo capaz de regenerar las emulsiones de aceite. Este equipo absorbe del depósito principal la emulsión de aceite y lo hace circular por tres etapas de filtrado para después introducirlo en el depósito presente en el equipo de regeneración donde la emulsión de aceite reposará para separar el aceite residual que no forma parte de dicha emulsión para posteriormente recoger la emulsión de aceite limpia, esterilizarla mediante luz UV y devolverla al depósito de almacenamiento de la emulsión de aceite. Un equipo análogo se encuentra en WO2017124437A1. En este caso, la emulsión de aceite se filtra, se elimina el aceite que no está emulsionado y antes de ser esterilizada se pasa por un filtro magnético que elimine la viruta generada para finalmente esterilizar la emulsión de aceite con luz UV y ser devuelta al depósito de almacenamiento de ésta.
Otros trabajos desarrollados con la que controlar la proliferación de microorganismos en las emulsiones de aceite sin utilizar luz UV se encuentran en ES103455U y CN203904303U. En ES103455U se desarrolló un equipo que fuerza a la emulsión de aceite a pasar por su interior donde se encuentra un bloque de tratamiento compuesto por dos metales diferentes (cobre-zinc por ejemplo) que origina una diferencia de potencial, depurando así la emulsión de aceite para devolverla al tanque de almacenamiento de la emulsión de aceite. Asimismo, a este equipo se le puede proveer de un sistema de filtrado y separador de aceite residual no emulsionado, el cual es colocado previamente a los bloques de metales disimilares. En cambio, en CN203904303U, la proliferación de los microorganismos se controla a través de la medida del pH. En caso de que este disminuya, el equipo inyecta un potenciador del pH que aumente su valor y así se evita que los microorganismos proliferen en la emulsión de aceite.
Asimismo, existen otros trabajos donde se han desarrollado equipos con los que aumentar la vida útil de las emulsiones de aceite a través de la limpieza de impurezas, pero sin controlar la proliferación de microorganismos activamente. Como se indicó anteriormente, el proceso de degradación de las emulsiones de aceite comienza cuando los microorganismos aeróbicos desemulsionan el aceite del agua, formando una película superficial de aceite que evita la entrada de oxígeno y por tanto éste se agota en el interior de la emulsión de aceite en pocas horas. Estos equipos lo que hacen es eliminar dicha película de aceite superficial permitiendo a la emulsión de aceite permanecer oxigenada y por tanto evitar que proliferen los microorganismos anaeróbicos y aumentar así la vida útil de la emulsión de aceite. Para ello, en EP1607126B1 se desarrolló un equipo que capaz de eliminar impurezas de las emulsiones de aceite a través de su absorción para llenar el depósito disponible en el equipo donde se deja reposar la emulsión de aceite haciendo así que el aceite no emulsionado ascienda y forme una película en la superficie de la ésta, la viruta en el fondo y en medio la emulsión de aceite limpia que es retornada al depósito de almacenaje de ésta.
Finalmente, en ES2245551B1 se desarrolló un equipo que mediante una boquilla absorbe directamente la película de aceite en el depósito de almacenaje de la emulsión de aceite. Esta película absorbida es llevada al depósito del equipo donde se decantan las partículas sólidas y se deja reposar para que la emulsión de aceite absorbida fortuitamente quede en el fondo del depósito y pueda ser devuelta al depósito de almacenamiento de la emulsión de aceite.
Conclusiones. Líneas futuras
Como se ha podido observar, existen dos formas de aumentar la vida útil de las emulsiones de aceite a través del control de microorganismos: de forma activa o de forma indirecta.
En el caso del control activo, las investigaciones que tienen una viabilidad industrial se basan principalmente en el uso de luz UV. Dichos desarrollos presentan un inconveniente común y es que debido al contacto existente entre la emulsión de aceite y las lámparas emisoras de luz UV se adhiere suciedad a las paredes de éstas últimas que hace que el rendimiento del equipo disminuya progresivamente, necesitando ser limpiadas constantemente. Existen otros desarrollos de control activo que se basan el control y corrección del pH o el uso de biocidas. En este caso, implica tener que introducir sustancias químicas que, aunque efectivas, ponen entredicho la salubridad de los puestos de trabajo, así como la huella ambiental generada por las emulsiones de aceite. También se puede controlar activamente la proliferación de bacterias a través del uso de un diferencial de potencial. En este caso, la problemática es similar al presentado por los desarrollos basados en el uso de luz UV en el cual las paredes metálicas que generan la diferencia de potencial necesitan ser limpiadas para conservar su efectividad.
Por otra parte, los desarrollos de control indirecto se basan en la eliminación de la película superficial de aceite generada por los microorganismos aeróbicos a través de su absorción. Al absorber esta película se evita el aumento de los microorganismos anaeróbicos y por tanto una rápida degradación de la emulsión de aceite. Sin embargo, los microorganismos aeróbicos siguen estando presentes y por tanto siguen desemulsionando el aceite. Este efecto sumado a que se está eliminando constantemente la película superficial hace que la concentración de aceite en la emulsión disminuya y por tanto tenga que ser controlada y repuesta según la cantidad de aceite eliminado.
Por todo ello, actualmente la Universidad del País Vasco (UPV/EHU) se encuentra inmersa en el desarrollo de su propio sistema de conservación de taladrinas con el fin de aumentar su vida útil a través de un equipo que combina luz UV con aire comprimido de tal modo que evite las problemáticas descritas en los párrafos anteriores además de presentar otras ventajas como que este sistema es instalado en los propios depósitos de almacenaje de la emulsión de aceite y por tanto no necesita espacio propio en las plantas industriales. Los primeros resultados realizados con el prototipo desarrollado muestran como su uso implica una menor proliferación de bacterias en la taladrina, abriendo un futuro esperanzador a esta línea de investigación que sirva de transición hasta alcanzar una fabricación ECO2.
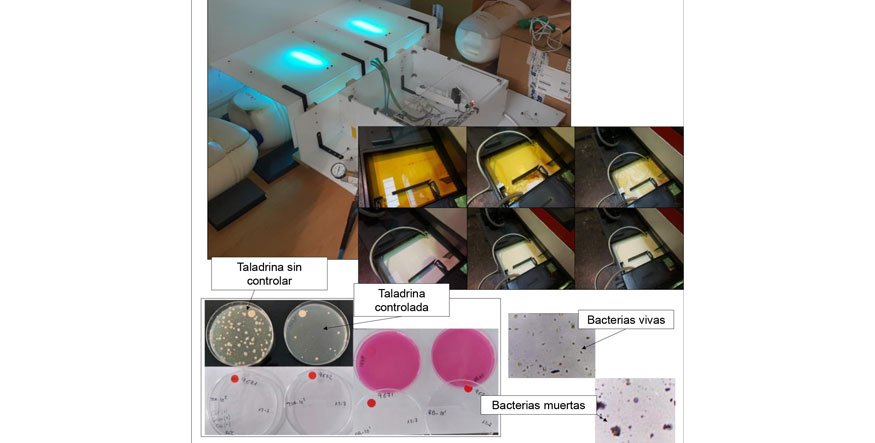
Agradecimientos
Los autores deben un agradecimiento al grupo universitario del Gobierno Vasco IT 1573, Mecanizado de alto rendimiento, MiCINN PDC2021-121792-I00 Producción de nuevas herramientas de corte para la fabricación de componentes de turbomaquinaria de alto valor añadido con el acrónimo: HCTAYLOR. Por último, los autores quieren hacer una mención especial a al programa BIZIALAB del Vicerrectorado de Desarrollo Científico-Social y Transferencia de la Universidad del País Vasco por el apoyo recibido en las primeras fases de este desarrollo.
Bibliografía
- Ma Sukhwal; Kim, Kangil; Huh Jinyoung; Kim Da Eun; Lee Sangju; Hong Yongcheol. Regeneration and purification of water-soluble cutting fluid through ozone treatment using an air dielectric barrier discharge. Separation and Purification Technology, 199: 289–297, 2018.
- Kyung-Hee Park; Jorge Olortegui-Yume; Moon-Chul Yoon; Patrick Kwon. A study on droplets and their distribution for minimum quantity lubrication (mql). International Journal of Machine Tools and Manufacture, 50(9):824 – 833, 2010.
- Morpeth, F. F. (Ed.) Preservation of Surfactant Formulations. Springer Netherlands: Dordrecht, p. 284-310, 1995.
- Walther, P. Maintenance of metalworking fluids, Cap. 8. Metalworking Fluids (MWFs) for Cutting and Grinding Woodhead. Publishing Series in Metals and Surface Engineering. Woodhead Publishing, 2012.
- Lee, M.; Chandler, A. C. A study of the nature, growth adn control of bacteria in cutting compounds. Journal of Bacteriology, 41: 373-386, 1940.
- Shennan, J. L. Selection and evaluation of biocides for aqueous metal-working fluids. Tribology International, 16(6): 317 – 330, 1983.
- Johnson, David; Phillips, Margaret. UV Disinfection of Soluble Oil Metalworking Fluids. AIHA journal: a journal for the science of occupational and environmental health and safety, 63: 178-83, 2002-2003.
- Saha, Ratul; Donofrio, Robert S.; Bagley, Susan T. Determination of the effectiveness of UV radiation as a means of disinfection of metalworking fluids. Annals of Microbiology, 64(2): 831-838, 2014.
- Coogan, Jj. Pathogen Control in Complex Fluids with Water-coupled Excimer Lamps at 282 and 308 nm. Photochemistry and photobiology, 81:1511-7, 2005.