Estado del arte de las aplicaciones de texturizado y últimas tecnologías
En la actualidad existen numerosos sectores, como el automovilístico, aeronáutico, óptico, microfluídico o electrónico, en los cuales se está trabajando con la finalidad de desarrollar superficies con objetivos específicos tales como:
- Reducción de los coeficientes de fricción con fluidos o entre superficies. Distribución uniforme del aceite y efecto hidrodinámico
- Mejora de estanqueidad de acoplamientos estáticos y dinámicos
- Absorción de partículas del lubricante
- Mejora de la adherencia de recubrimientos
- Reducción de las tensiones residuales y las desviaciones de forma
- Mejora de la refrigeración y mejora de la reflectancia
- Generación de hidrofobicidad e hidrofilidad
Asimismo son numerosas las tecnologías, tanto por arranque como por aporte de material, que se emplean y son objeto de investigación a esos efectos:
- Torneado con punta de diamante, Rolling, vibrorolling, EDM (electro dischargemachining, ablación Laser, mecanizado por chorro abrasivo, rectificado)
- Electrodeposición de níquel, fotolitografía y electrodeposición de níquel, fotolitografía y oxidación térmica, ataque micro-electrolítico
Relevancia de la funcionalidad tribológica en la eficiencia energética: el rectificado como tecnología productiva para el texturizado
El coste económico y medioambiental que supone la fricción en la maquinaria y en los transportes modernos basados en el desplazamiento de rodadura y deslizamiento es significativamente llamativo y preocupante. Los resultados de estudios realizados en programas de investigación en torno a la tribología de equipos para el transporte por carretera, la generación de energía, las turbomáquinas y la maquinaria industrial indican la posibilidad de ahorrar una décima parte del consumo total de energía a través de mejores prácticas tribológicas, lo cual podría suponer un ahorro energético de miles de millones de euros únicamente en Europa. De hecho, se estima que un tercio de los recursos mundiales de la energía se desperdicia en disipaciones de fricción, desgaste y corrosión.
Estas conclusiones han alertado y orientado a la comunidad científica y tecnológica internacional de la necesidad de implementar estrategias para la reducción de la fricción y control del desgaste. Actualmente sectores como el automovilístico y la fabricación están invirtiendo gran parte de sus esfuerzos en investigaciones al respecto. Para lograr estos objetivos se plantean diferentes líneas de actuación como el empleo de lubricantes de menor viscosidad y mayor duración, el desarrollo de materiales de baja fricción y recubrimientos duros o la generación de superficies funcionales mediante micro-topografías o texturas superficiales.
El texturizado de superficies se ha mostrado ya como una herramienta útil para la reducción de la fricción. Diferentes superficies propensas a promover la micro-lubricación están siendo diseñadas e incorporadas en la especificación de componentes. Uno de los principales retos, en este sentido, consiste en desarrollar métodos de fabricación capaces de producir estas texturas de una manera repetitiva y económicamente viable. Entre los diferentes procesos existentes, el rectificado mediante el empleo de muelas con determinados patrones es una tecnología poco explorada por su complejidad pero con un elevado potencial para la consecución de diferentes texturas sobre cualquier tipo de superficie y material de una manera simple, productiva y de bajo coste.
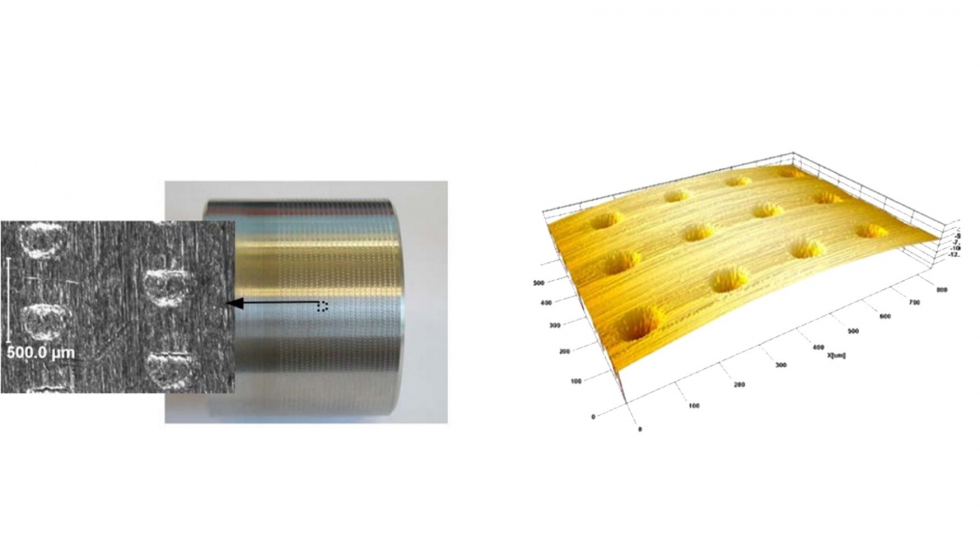
Aplicación del floreteado: un método manual
El rectificado aporta mejoras como la automatización del proceso, la ergonomía del trabajador, menores costes y superficies más uniformes. Entre los métodos de fabricación destinados a la mejora del acabado superficial y la precisión de medida, se encuentran los métodos como el floreteado y rasqueteado. Si bien el objetivo principal del rasqueteado es asegurar el buen contacto entre dos superficies, mediante el floreteado lo que se pretende es conseguir unas depresiones sobre la superficie de deslizamiento para que el lubricante se deposite y permita disminuir el rozamiento durante el movimiento relativo. Se utiliza sobre todo cuando es necesario adaptar dos piezas cuyas superficies deben deslizarse o girar una sobre otra e interesa que su deslizamiento sea perfecto. Algunos ejemplos donde se utiliza ésta clase de acabado son cojinetes, bancadas de máquinas, instrumentos de medida, bases de niveles, reglas y mármoles de verificación. Es un método de acabado superficial que se realiza por extracción de virutas finas y ha de llevarse a cabo sobre superficies que hayan sido mecanizadas previamente.
El proceso de floreteado supone varios días de mano de obra de operario, un trabajo donde la ergonomía y salud del operario se ven afectadas de forma considerable. Si bien existen rasquetas eléctricas que producen el movimiento de vaivén de manera automática para comodidad del usuario, el proceso de floreteado no mejora sustancialmente porque el acabado final de la pieza queda igualmente en manos del buen hacer del usuario.
Esta operación manual a día de hoy tiene definidos unos escasos parámetros de validación orientativos en cuanto a forma de la huella, orientación de la misma y porcentaje de huella sobre la superficie total, pero no se llega a realizar ninguna medición cualitativa de la geometría de la superficie lograda ni de su capacidad tribológica.
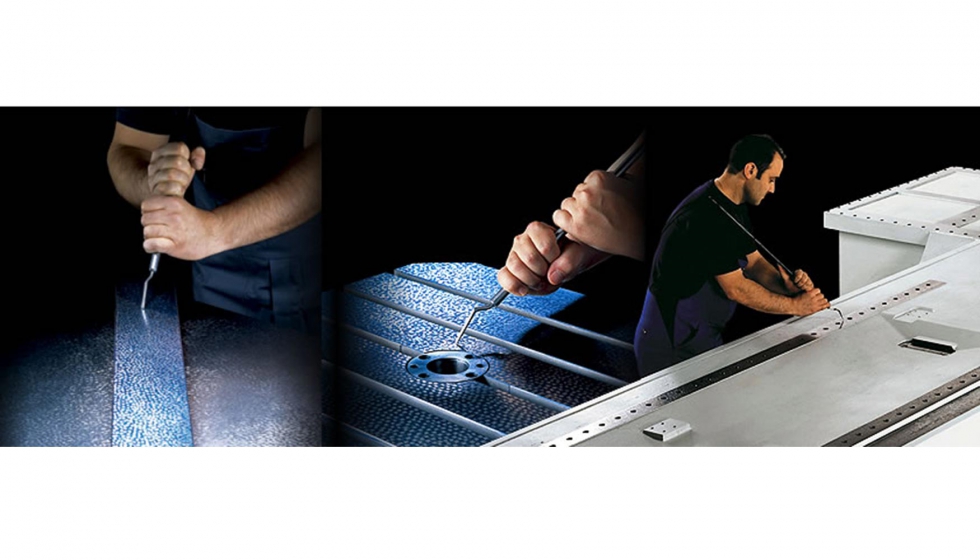
Figura 2. Proceso manual de floreteado. Fuente: Dixi Machines.
Mediante la texturización de la muela rectificadora se pueden solventar las problemáticas relacionadas con este proceso, consiguiendo:
- Una reducción del tiempo necesario para llevar a cabo el proceso, aumentando la productividad. Hay que tener en cuenta que normalmente el proceso previo al floreteado es el propio rectificado.
- Una mejora de la ergonomía del operario por la automatización del proceso.
- Una uniformidad en la topografía de la superficie rectificada con la que controlar de manera óptima la disminución del rozamiento entre las superficies deslizantes.
Prototipo desarrollado y resultados obtenidos
El sistema desarrollado para conseguir esta texturización de muela se basa en un diamantador activo que actúa sobre la profundidad de pasada del proceso de diamantado en sincronía con el resto de parámetros de proceso (velocidad transversal de diamantado y velocidad de giro de la muela rectificadora) en función de una señal comandada. Mediante esta tecnología se pueden conseguir multitud de texturas en la muela rectificadora que posteriormente son copiadas en la superficie de la pieza rectificada en función de las condiciones de proceso.
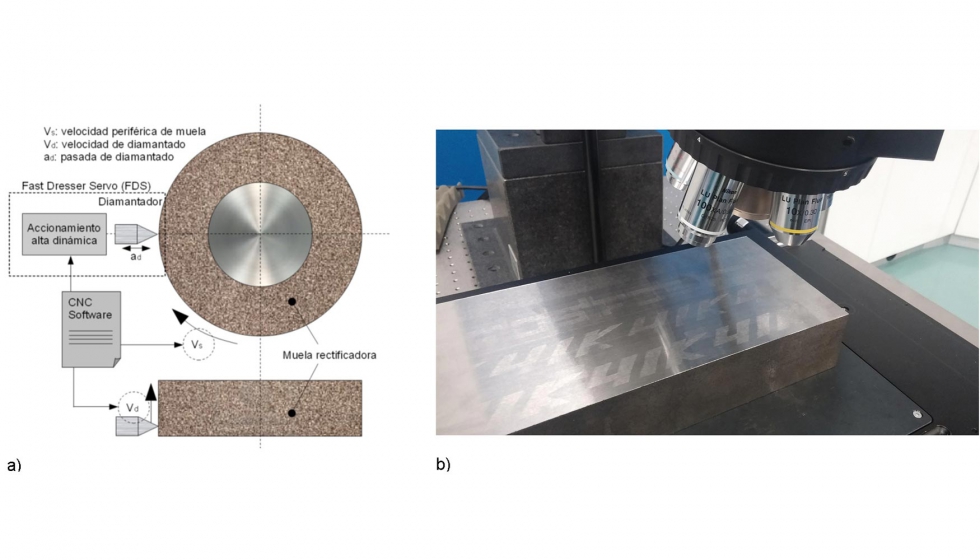
Aplicando esta tecnología del diamantado activo es posible entonces conseguir superficies donde se reduzca la fricción. Con este objetivo, en primer lugar se ha analizado la topografía obtenida en la pieza mediante un floreteado manual. Para caracterizar esta superficie, el análisis se ha centrado en la profundidad de las marcas generadas y en el porcentaje de área que ocupan sobre el total de la superficie. De esta forma y tras una serie de mediciones en diferentes condiciones y con diferentes operarios, se han obtenido unos resultados medios de 20 micras de profundidad de surco en las zonas A, B y C de la figura 4 (a), ocupando un área del 35% sobre el total.
Teniendo en cuenta dichos valores, se ha programado el sistema de diamantado para conseguir sobre la pieza unas condiciones similares. De esta forma, se han generado sobre la superficie de la pieza unas depresiones de forma elipsoidal tal como se aprecia en la siguiente figura 4 (b).
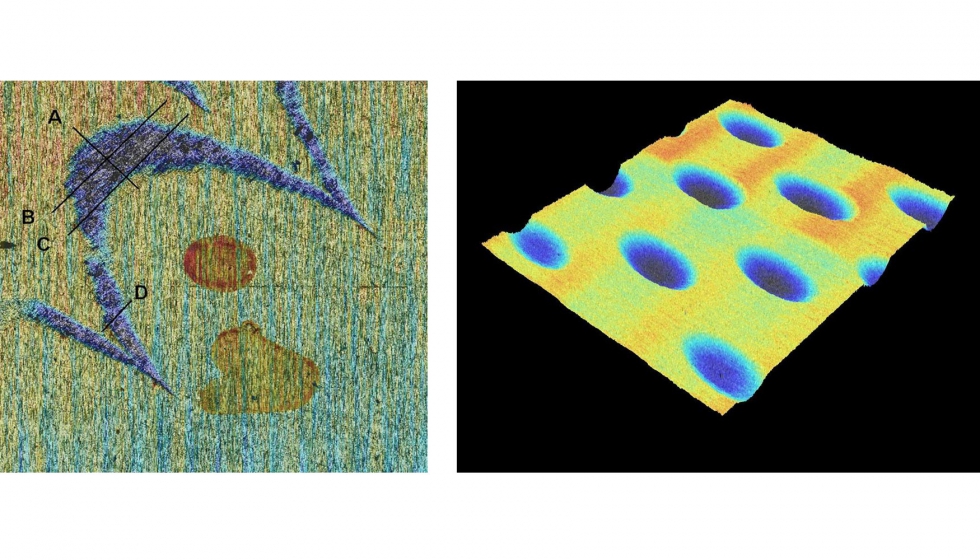
Las mediciones sobre la topografía obtenida con esta tecnología revelan unos resultados similares a los obtenidos con el proceso manual: una profundidad máxima de 20 micras, ocupando un área aproximada del 30% del total. De esta forma, se demuestra la viabilidad del sistema para conseguir topografías adecuadas para la reducción de la fricción.
Además de esta aplicación, las posibilidades que ofrece esta tecnología son múltiples en relación a las texturas que se pueden generar, pudiendo conseguir superficies donde se mejore la estanqueidad o se aumente la fricción. También se logran procesos de rectificado y diamantado más eficientes en cuanto a consumo energético o aumento de vida de herramientas.