La compensación volumétrica de los errores geométricos en máquinas-herramienta
Desde hace aproximadamente 3-4 años la compensación volumétrica de las máquinas-herramienta ha sido introducida a la industria. Por una parte, los fabricantes de los controles más importantes del mercado han integrado los algoritmos necesarios en sus controles para llevar a cabo la compensación de los errores geométricos; y por otra parte, nuevas herramientas hardware y software de metrología han sido desarrolladas para realizar la verificación volumétrica de la geometría en máquinas-herramienta de 3, 4 y 5 ejes.
1. Introducción
Los sectores más exigentes del mercado industrial muestran una tendencia hacia piezas unitarias de mayor valor añadido y precisión, lo que requiere de medios productivos más flexibles y precisos. Para cumplir con esta última característica una máquina debe cumplir dos requisitos indispensables. Por una parte, debe mostrar una repetibilidad muy alta y por otra parte, su error geométrico debe ser prácticamente despreciable. Así como la repetibilidad es una característica común entre los medios productivos de altas prestaciones, el error geométrico depende del tipo, tamaño y configuración de máquina. Es aquí, donde la verificación y compensación volumétrica de máquina-herramienta (MH) cobra mayor relevancia, ya que permite aumentar las prestaciones de una máquina sin afectar a su coste de fabricación y montaje.
2. Error geométrico de las MH
El error geométrico de una MH es el causante principal en la falta de precisión en el posicionamiento de la máquina. Las causas principales de este error geométrico son los defectos de fabricación y montaje, así como las cargas que soporta la propia máquina. La descripción de las componentes del error comienza con el supuesto de sólido rígido de la máquina. Cada movimiento de un eje de la máquina se puede describir a través de seis grados de libertad: tres traslaciones y tres rotaciones, cuando el movimiento nominal del eje es de un único grado de libertad, ya sea de traslación o de rotación.
La notación del movimiento de cada eje está estandarizada según la norma ISO 841: X, Y, Z denotan los movimientos lineales; A, B, C las rotaciones en torno a los ejes X, Y, Z. [1]
2.1 Error de movimiento lineal
Para un movimiento nominalmente lineal, las seis componentes del error son tres errores lineales y tres errores de giro:
- Error de posicionamiento, y dos movimientos de error de rectitud
- Error de giro (roll), error de cabeceo (pitch) y de alabeo (yaw)
![Figura 1. Componentes de error del eje lineal x según ISO TR 16907. [2] Figura 1. Componentes de error del eje lineal x según ISO TR 16907. [2]](https://img.interempresas.net/fotos/1272280.jpeg)
El caso más común es encontrar con una MH de 3 ejes lineales donde el error geométrico se descompone en 21 componentes, 6 por eje como explicado en este punto, más un error de perpendicularidad por cada pareja de ejes.
2.1 Error de movimiento rotatorio
Para un movimiento nominalmente rotatorio, las seis componentes de error son:
- Dos movimientos de error radial, y un movimiento de error axial.
- Un error de posicionamiento radial y dos movimientos de error de alabeo
![Figura 2. Componentes de error del eje rotativo C según ISO TR 16907. [2] Figura 2. Componentes de error del eje rotativo C según ISO TR 16907. [2]](https://img.interempresas.net/fotos/1272281.jpeg)
3. Verificación volumétrica de MH
Para realizar la compensación del error geométrico de una MH en todo su volumen se debe caracterizar previamente dicho error en todo el volumen de la máquina. A través de los sistema de medida más tradicionales y aplicados en la industria como son: interferometría lineal, niveles electrónicos, escuadras…es complicado obtener el error geométrico de la máquina en todo el volumen, sobre todo en máquinas de gran tamaño donde el acceso a las partes altas de la máquina se convierte en muy complicado. Además, el hecho de combinar todos estos sistemas de medición por una parte, no te garantizan la obtención de todas las componentes del error geométrico de una MH y por otra parte, se dilatan mucho en el tiempo; este último factor además de suponer un coste añadido en el presupuesto económico, permite la aparición de derivas térmicas y su efecto en el aumento de la incertidumbre final alcanzada.
Por todos estos motivos, en los últimos 4-5 años se ha desarrollado una solución para la caracterización volumétrica de los errores geométricos de una máquina con un único sistema de medición, en un tiempo reducido y con una precisión interferométrica. Esta solución se basa en medir la distancia entre un sistema de medición fijo y un reflector móvil que se mueve junto con el cabezal de la MH con un procedimiento secuencial. Se define una nube de puntos que representa el volumen de trabajo de la máquina-herramienta, y en cada uno de los puntos se registra el desplazamiento existente entre el sistema de medición ubicado sobre la mesa de la MH y el reflector ubicado cerca de la punta de la herramienta. Todos los desplazamientos medidos se procesan a través de la técnica de la multilateración, es decir, en base a múltiples medidas de desplazamiento se consigue situar cada punto de parada de la máquina con precisión interferométrica en el espacio. El hecho de disponer de un único sistema de medición hace que sea necesario ubicar el sistema de medición en 4-5 posiciones diferentes del volumen de la MH. En la figura 3, se puede observar en formato gráfico el proceso de adquisición de la solución descrita.
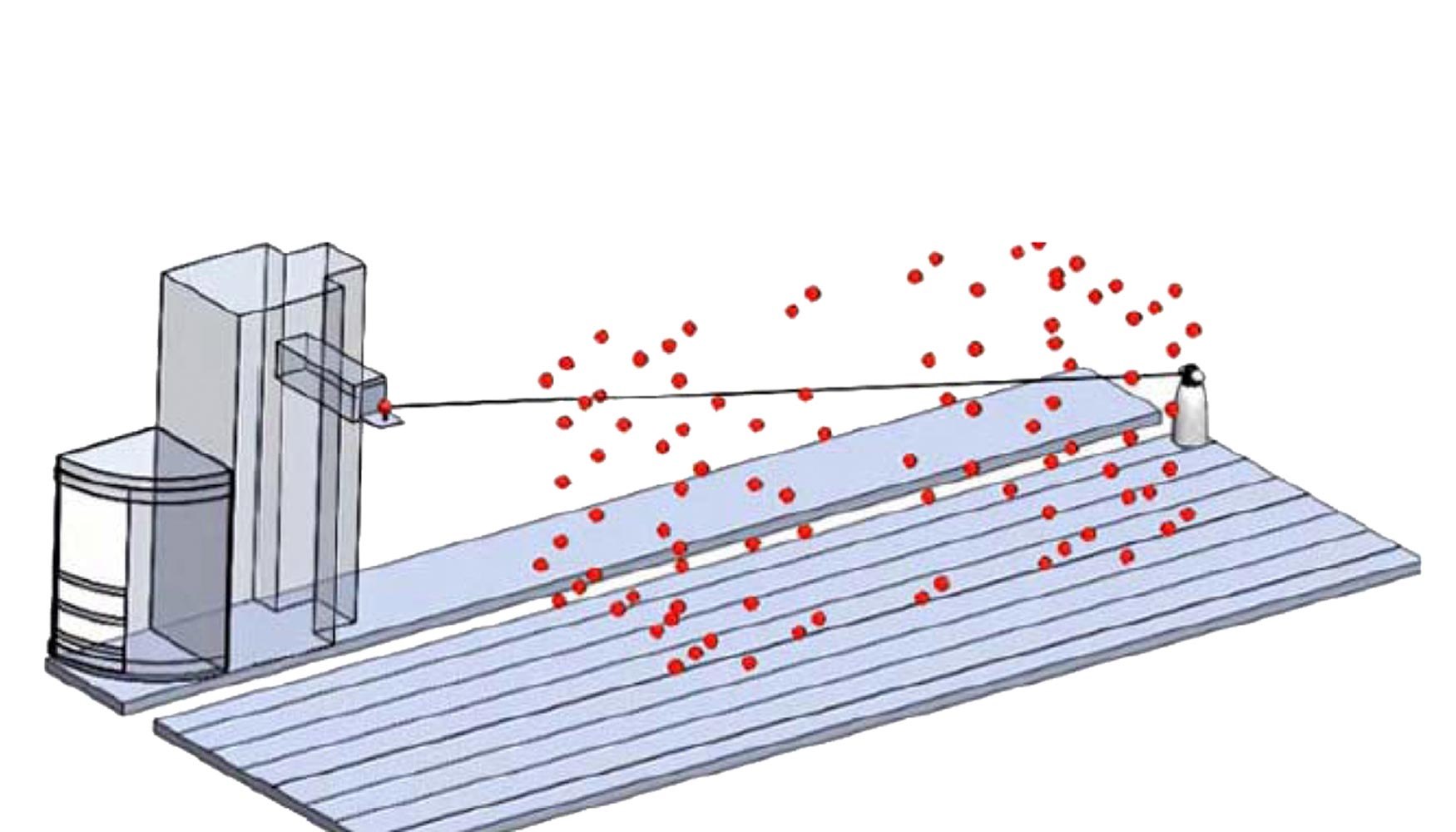
Para la realización de estas mediciones existen dos sistemas de medida que pueden ser empleados, por una parte, un láser tracker comercial donde se prescinde de las mediciones de los encoder y solo se tiene en cuenta la medición del interferómetro y por otra parte, el sistema de medida láser tracer [3] comercializado por la empresa Etalon AG, spin-off del PTB (Centro primario de metrología alemán) y que se utiliza exclusivamente para realizar la medición de volumetrías con la técnica de multilateración. En la figura 4, se puede observar la incertidumbre de medición de cada una de los sistemas de medición y los recorridos de MH en los que se aplican.
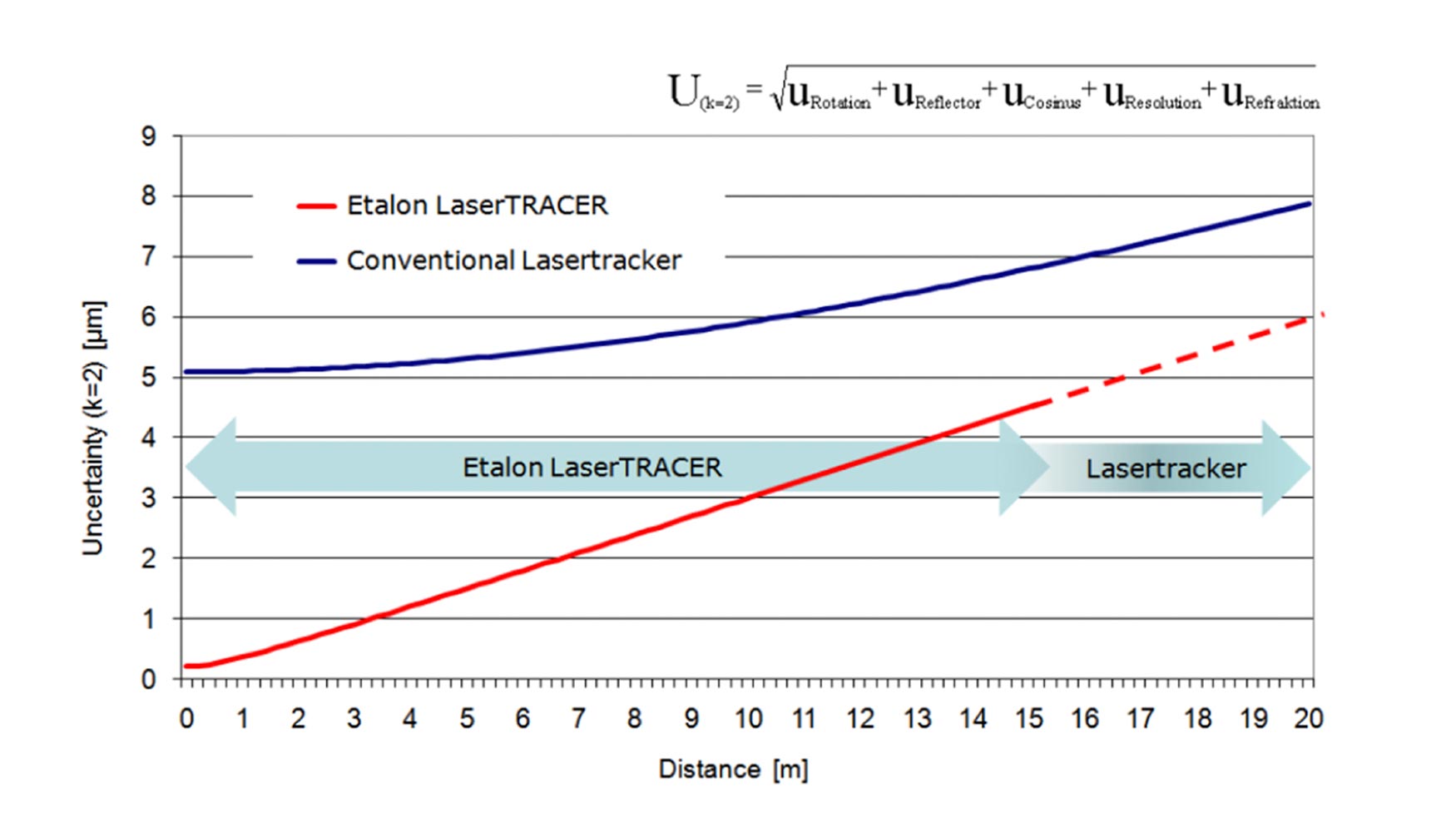
3.1 Factores importantes en la verificación volumétrica
Existentes varios factores importantes que se deben tener en cuenta para que la caracterización geométrica de la MH sea válida y apropiada. Por orden de importancia, la temperatura es el factor más importante a la hora de realizar una verificación volumétrica adecuada, es decir, el hecho de dilatar la medición en el tiempo hace que la MH sufra derivas térmicas y la repetibilidad en un proceso secuencial como es la multilateración se ve afectada. Por este motivo, es importante reducir el tiempo de medición al mínimo necesario y por otra parte mantener la estabilidad térmica de las mediciones en la máquina-herramienta. A continuación, se muestra la distribución de la desviación estándar de un proceso completo de verificación volumétrica para tres casos diferentes de máquina. En el primer caso, se muestra una máquina de medir por coordenadas de 1 m3 (MMC) en un laboratorio de metrología. En segundo y tercer se muestran una MH de 1 m3 y una MH de 30 m3 en un taller de mecanizado. Para todos los casos el tiempo de medición es similar pero el cambio de temperatura y la configuración de la máquina suponen un ajuste del proceso en diferentes órdenes de precisión. En la figura 5, se representa la desviación estándar del proceso para los tres casos de máquina descritos.
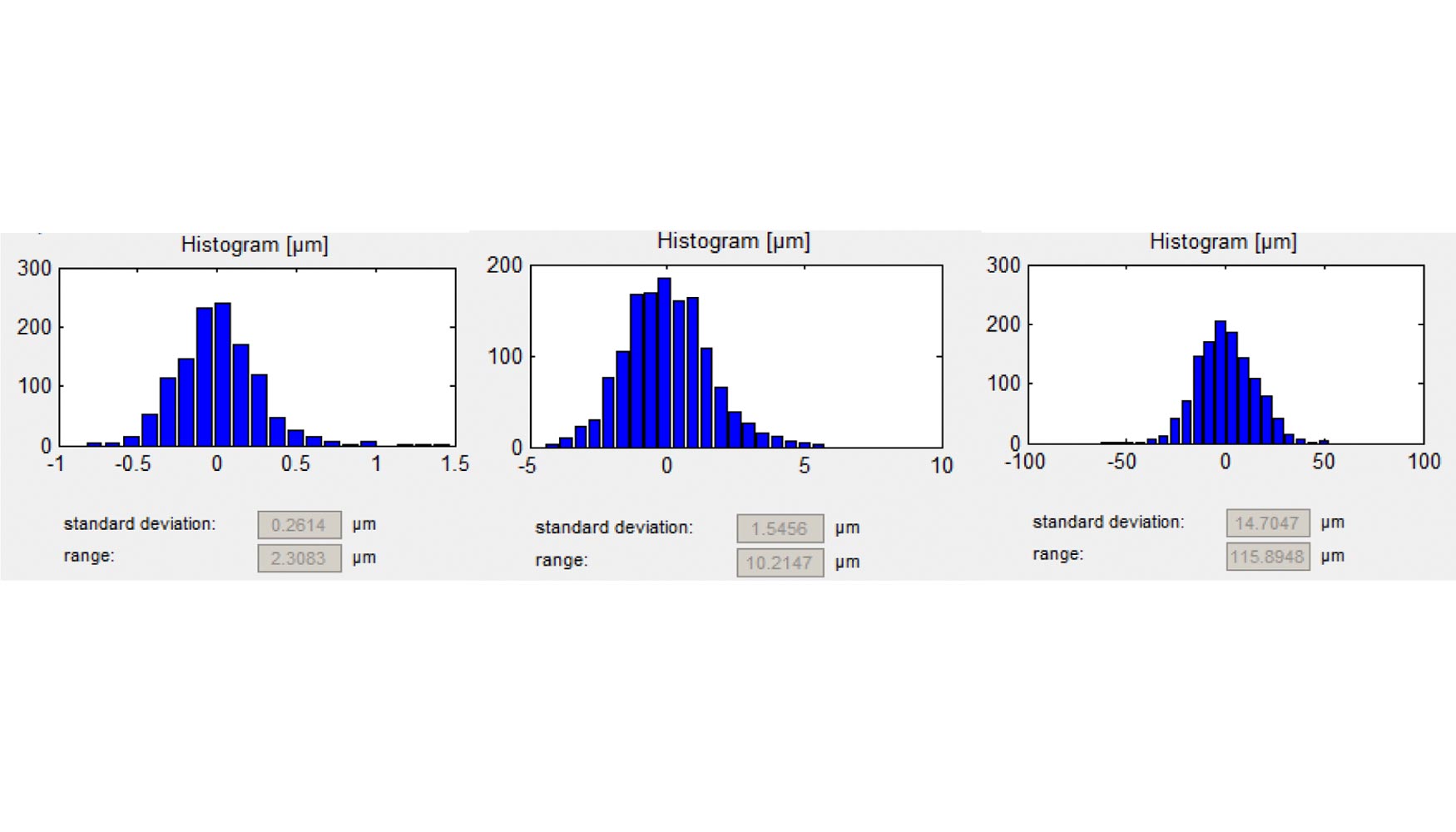
Además de la temperatura, la repetibilidad de la máquina es otro de los factores importantes a tener en cuenta en la adquisición de las mediciones. La propia deriva térmica y el error de reversión de la máquina afectan directamente a la repetibilidad volumétrica de la máquina. A diferencia de las MMC, las MH tienen una gran capacidad de repetir una posición el espacio ya que han sido concebidas para ello. En la figura 6, se puede observar la repetibilidad de los tres casos descritos anteriormente con su correspondiente monitorización de temperatura.
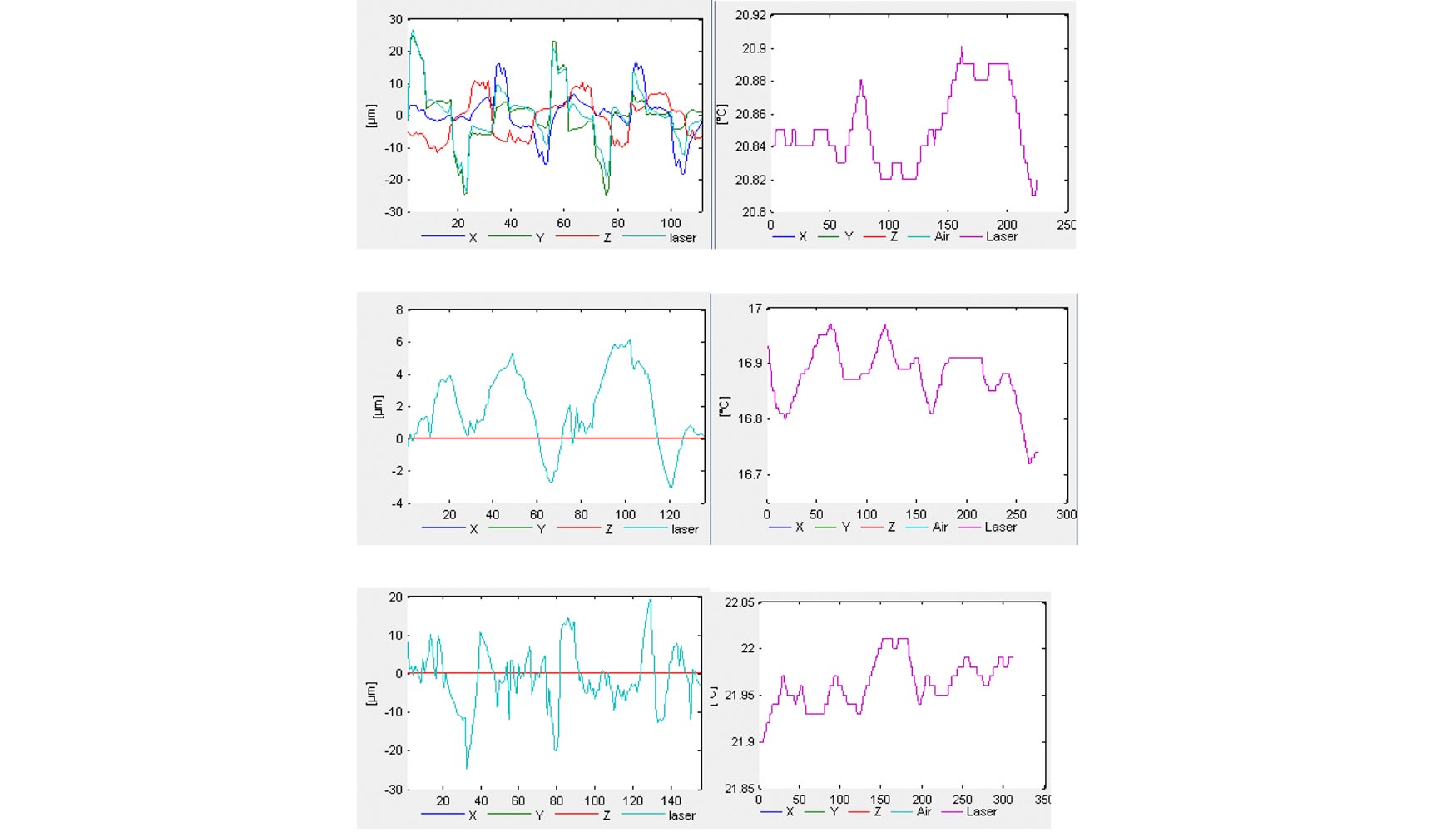
Además de los dos factores mencionados, existen otros factores que se deben tener en cuenta a la hora de realizar la verificación volumétrica de una máquina, entre todos ellos destacaría como la óptima distribución del sistema de medida para reducir la incertidumbre de cálculo del proceso de multilateración y así reducir la incertidumbre del resultado.
4. Compensación volumétrica de MH
Partiendo de que la caracterización geométrica se ha realizado correctamente, el siguiente paso es la introducción de la corrección geométrica a realizar por la máquina en el propio control. Así como en el mundo de las MMC la compensación volumétrica de la máquina a través de la introducción de las 21 componentes de error, es algo en lo que ha venido trabajando en la última década, en el mundo de la máquina-herramienta, las compensaciones más habituales son la compensación del posicionamiento y la compensación cruzada. Estas compensaciones no ofrecen la posibilidad de compensar la máquina en todo su volumen y por ese motivo los fabricantes de los controles más usados en el mercado han introducido un módulo en sus respectivos controles para llevar a cabo esta compensación. Antes de entrar a analizar, las características de los módulos de compensación de cada control, a continuación se incluye una tabla donde se describe el estado actual de la compensación volumétrica en una MH.
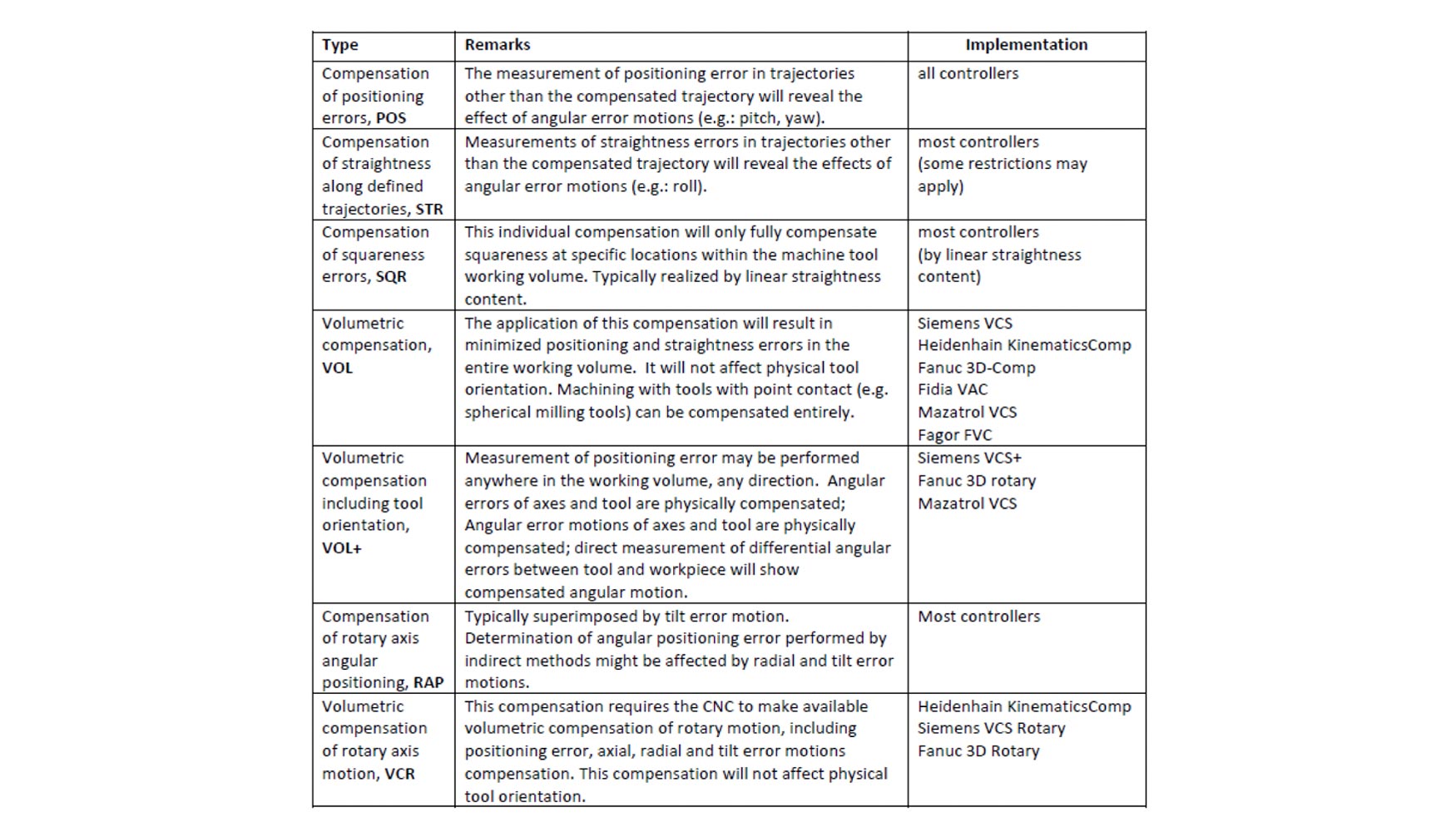
En lo que se refiere a los controles más utilizados del mercado, Siemens a través de su módulo VCS ofrece la mayor oferta en compensación volumétrica de ejes lineales y ejes de rotación del mercado. Por una parte, se pueden introducir dos archivos de compensación por separado, por ejemplo para dos temperaturas diferentes de la máquina, y el propio control se encarga de interpolar entre ellos. Además, permite la opción de introducir archivos de compensación para diferentes longitudes de herramienta. Heidenhain por su parte, a pesar de que el proceso de introducción y activación de los archivos sea más complejo, permite introducir tantos archivos de compensación volumétrica como se quiera. Este hecho, permite caracterizar y controlar su comportamiento en diferentes temperaturas y estados de la máquina.
Fidia por su parte, ofrece la posibilidad de introducir un único archivo de compensación en el control. El proceso de introducción y activación de la compensación volumétrica es el más simple de todos ellos.
4.1 Límites de la compensación volumétrica
La compensación volumétrica aporta numerosos beneficios a las máquinas susceptibles de ser compensadas de esta forma, pero no se debe pasar por alto sus propios límites.
- La estabilidad a largo plazo de la máquina no podrá ser garantizada ya que es intrínseca a la propia máquina.
- Las deformaciones termo-elásticas seguirán apareciendo en la máquina siempre que no se mantenga una estabilidad térmica de la máquina.
- La repetibilidad de la máquina como se ha mencionado arriba no se podrá compensar a través de este tipo de compensación, ya que depende del propio funcionamiento de la máquina.
- Se podrá compensar la volumétrica de la máquina para una longitud de herramienta (la más habitual a no ser que se disponga de los módulos más avanzados de Siemens, Fanuc y Mazak.
4.2 Caso real de verificación y compensación volumétrica
Se ha verificado y compensado una centro de mecanizado de 3 ejes Heller MCH 400D. El tipo de configuración es de mesa móvil y los recorridos de la máquina para un orden cinemático FZXY son de 1.400 x 1.200 x 1.400 mm. La temperatura durante la adquisición de las mediciones se ha mantenido estable dentro de 18,6 y 19,4 °C y se ha decidido compensar la máquina a esta temperatura ya que es la temperatura habitual de trabajo de la máquina. El control disponible es un control Siemens 840D con el módulo VCS activado. A continuación, en la figura 7 se muestra la verificación volumétrica de la máquina sin compensar y acto seguido se muestra la verificación volumétrica tras ser compensada. Se puede observar que la máquina mejora en un amplio porcentaje para convertirse en una máquina con unas prestaciones en vacio por debajo de 15 μm.
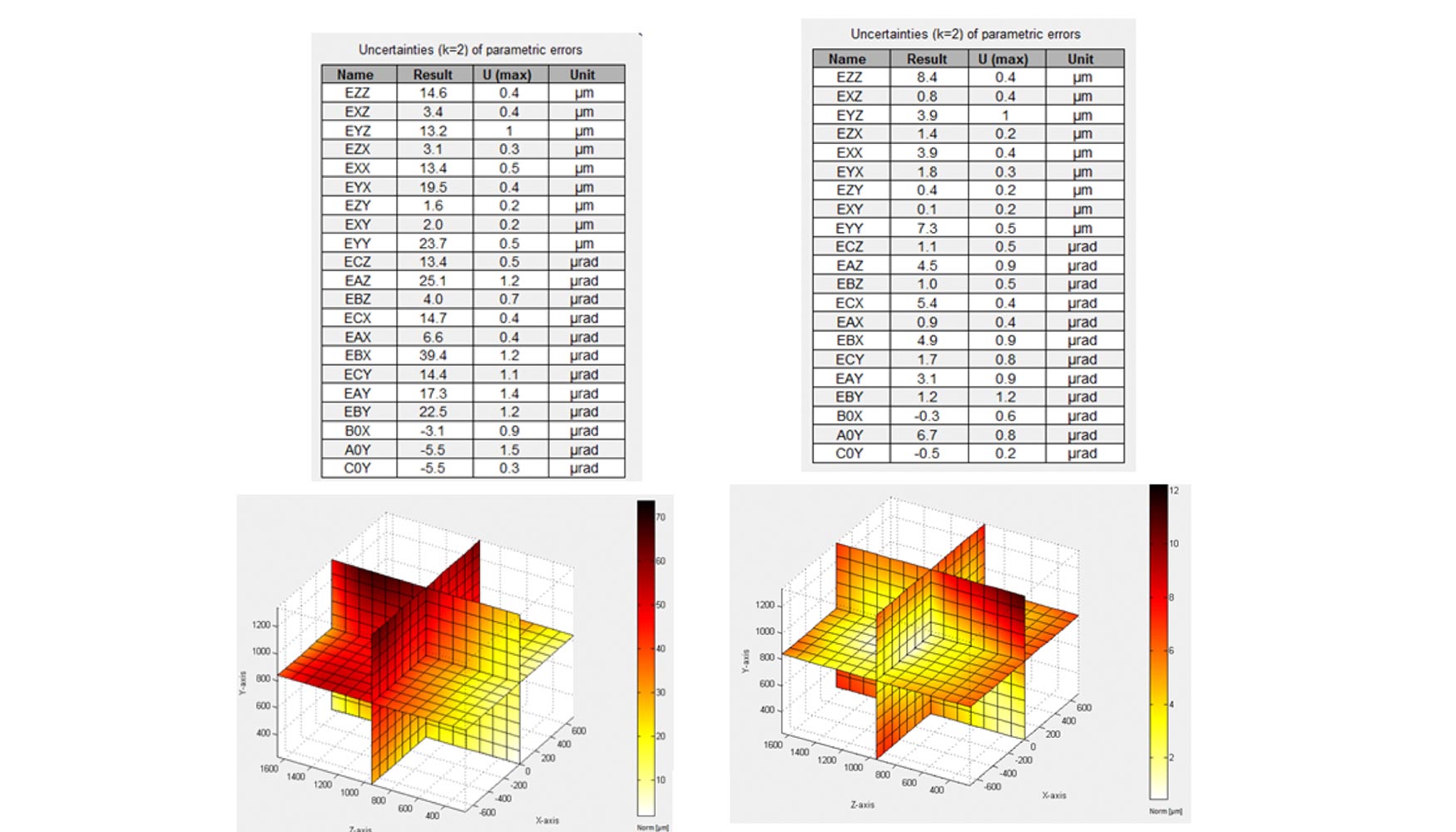
6. Conclusiones
La compensación volumétrica de MH y MMC ofrece la posibilidad de mejorar las prestaciones de las máquina en un amplio porcentaje a través de un proceso de calibración basado en incertidumbre interferométrica. La gran ventaja de este proceso es que se puedencompensar máquinas de diferentes configuraciones compuestas por ejes lineales y ejes de rotación. Para ello, factores como la estabilidad térmica y la repetibilidad de la máquina deben ser garantizadas durante el proceso de medición para garantizar unos resultados aptos para ser introducidos en el control.
Referencias
[1] ISO 841:2001. Industrial automation systems and integration - Numerical control of machines — Coordinate system and motion nomenclature.
[2] Norma ISO TR 16907:2015. Machine tools — Numerical compensation of geometric errors.
[3] Schwenke, H., Hunting the limits of accuracy: State of the art for volumetric compensation of machine tools – International Manufacturing Technology Show (2012).