KH Lloreda crea el primer almacén íntegramente robotizado
19 de noviembre de 2010
El proyecto del nuevo almacén de KH Lloreda se inició en 2007, cuando la compañía adquirió un terreno de 4.000 metros cuadrados e el polígono industrial Can Castells, en la población barcelonesa de Canovelles, con el objetivo de optimizar la gestión logística de la compañía. A principios de 2009 se inició la construcción de la nave que finalizó el pasado mes de agosto. La nueva sede alberga además las oficinas y la fábrica de la compañía. La realización del proyecto ha supuesto una inversión de 9 millones de euros y la intervención de unos 150 profesionales.
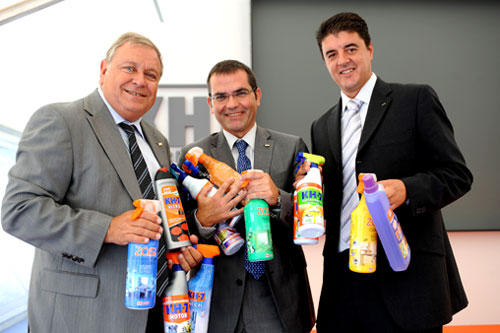
Josep Maria Lloreda, presidente de la compañía, presentó su nueva planta a la prensa especializada justo el día antes de su inauguración oficial. Lo acompañaron Daniel Lancho, director de Operaciones y Carlos Barberà, jefe de Tráfico de la compañía. El acto de inauguración oficial contó con la asistencia de Juan José Guibelalde, presidente de Aecoc, Miquel Valls, presidente de la Cambra de Comerç de Barcelona, y Josep Orive, alcalde de Canovelles.
Innovación e ilusión
KH Lloreda basa su éxito en la innovación y destina gran cantidad de recursos humanos y económicos a desarrollar nuevos sistemas y tecnologías que mejoren los procesos productivos y la gestión integral de la compañía. La innovación es una constante en cada decisión y actuación de la compañía que se transmite desde la dirección a cada uno de los trabajadores. La última iniciativa para fomentar la innovación en la organización son los ‘Innovas’, sesiones grupales donde dos personas formadas en técnicas creativas utilizan diferentes métodos creativos para que un grupo mixto de colaboradores encuentren soluciones innovadoras a distintas necesidades de la empresa abordándolas desde un nuevo enfoque, aunque son muchas las iniciativas llevadas a cabo en esta área. “Invertimos un 3% de nuestra facturación en nuestro departamento de I+D, con más de 10% de nuestra plantilla dedicándose a innovación controlada y todo el resto de la plantilla a innovación espontánea”, afirmó el presidente de la compañía.
En cuanto al proyecto de la nueva planta de fabricación y distribución, en palabras de Josep Maria Lloreda:“La creación de este proyecto ha supuesto un reto para la compañía y tuvimos muy claro desde el principio que nuestro objetivo era desarrollar un sistema altamente automatizado que nos permitiera mejorar el control de nuestra logística y la calidad del servicio”. La total automatización y la mínima intervención de la mano de obra eran las principales premisas del proyecto. Para ejemplarizarlo, Daniel Lancho contó: “Cuando yo empecé a trabajar con Josep Maria, me dijo que su ilusión era que todas las instalaciones funcionaran con solo 3 ingenieros. Es quizás un hito inalcanzable pero marca un poco la filosofía de la compañía”.
El director de Operaciones de KH Lloreda explicó cómo surgió el proyecto, que perseguía desde su origen la máxima calidad en todos los procesos, desde la fabricación hasta la distribución final del producto, eliminando asimismo todo aquello que no aportara valor a la compañía. “El objetivo era conseguir que el primero que tocara la botella de producto fuera el consumidor final”, comentó Lancho. Para ello, KH Lloreda tuvo que internalizar una parte de la cadena de suministro que no estaba en sus manos sino subcontratada a un operador logístico que se hacía cargo del almacenaje, la preparación de productos y la expedición hasta el cliente final.
Automatizando todo el proceso, se pueden evitar los errores de preparación de pedidos. “Con este proceso creemos que es posible la preparación de pedidos con una calidad de entrega del 100%”.
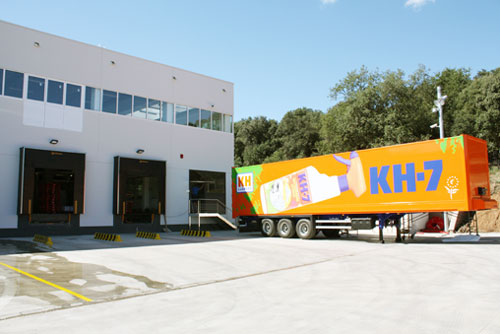
Bajo esta premisa, los responsables del proyecto empezaron a investigar sobre qué soluciones de automatización tenían los principales operadores logísticos y qué opciones ofrecía el mercado para armar este almacén totalmente robotizado. “Todos los almacenes que vimos eran convencionales, con procesos estándar, sistemas de gestión convencionales y un uso intensivo de la mano de obra. Creemos que hay cierto miedo en intervenir en logística: se aplica la tecnología hasta cierto punto, pero a partir de ahí las compañías no se atreven a invertir”, añadió Daniel Lancho.
Otro tanto sucedió a la hora de buscar robots especialmente adaptados para el picking en cajas o a la carga y descarga automática de camiones, por lo que los responsables del nuevo almacén tuvieron que adaptar las soluciones existentes en el mercado a sus demandas.
De 6 horas a 15 minutos
El resultado del proyecto es una nave íntegramente robotizada y equipada con las últimas tecnologías que permite el almacenaje y movimiento de 7.000 palés sin la intervención de ningún operario. Además de la automatización de la carga y descarga de camiones llevado a cabo en el centro de producción y en el mismo almacén y la robotización del proceso de preparación de picking, el proyecto incorpora el etiquetaje con RFID y su integración al ERP de la compañía, que garantiza la fiabilidad de la gestión global del almacén monitorizando todos los movimientos de entrada y salida del almacén así como la preparación del picking.
La etiqueta RFID o tag se coloca en cada caja de producto acabado. De este modo la caja pasa al resto de proceso de paletizado y enfardado totalmente identificada. El paletizador cuenta con unas antenas RFID que le permite identificar el inicio y fin de un palé. Una vez en la enfardadora, el lector de RFID aprovecha el giro de los palés para realizar una lectura completa de los tags que contienen un palé. El sistema asocia en esta fase el contenido del palé a un número de SSCC (contenedor), imprime la etiqueta de SSCC y la aplica al palé. Paralelamente informa al ERP de la empresa del alta de dicho palé, pasando a ser stock en fábrica. El operario de KH Lloreda asigna la salida de los palés de producción a un muelle de carga dotado de unas nuevas antenas de RFID. El sistema recibe una señal que indica el inicio/fin de carga y procede a la lectura de los palés que conforman la carga del vehículo mediante las antenas de muelle. Una vez finalizada la carga física del vehículo, se informa al ERP del contenido de la carga y se iniciará el proceso de impresión de documentos y del mensaje de preaviso al almacén de la entrada.
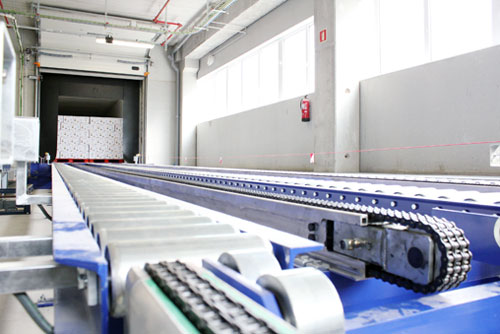
Para las recepciones de palés desde la planta de KH, la compañía ha adquirido dos semirremolques equipados con un sistema de carga y descarga automática consistentes en unos equipos de rodillos y cadenas que, una vez acoplados a los muelles de fábrica y almacén, forman parte del mismo conjunto posibilitando la entrada y salida automática de los palés. A la salida del transporte desde planta de producción, el almacén recibe un preaviso de entrada en el ERP. Una vez en el almacén, el camión se posiciona en el muelle automático e inicia el proceso de recepción. Al formar el camión y muelles un único conjunto la extracción de los 32 palés se realiza a la vez en un tiempo inferior a los 90 segundos. Una vez finalizada la recepción se procede a incorporar los palés en el silo para lo que deberán pasar por el control de gálibo y recorrer el camino de rodillos hasta el transelevador asignado por SGA (Sistema Gestión Almacenes). Paralelamente, en este mismo punto se lleva a cabo la lectura RFID de los palés entrantes. Una vez ubicado por el transelevador en el hueco asignado, el SGA comunicará al ERP que el stock pasa a estado disponible. Carlos Barberá, jefe de Tráfico y Distribución de KH Lloreda añadió un dato sobre la efectividad del nuevo sistema: “Con el operador logístico, el ciclo completo desde que sale el camión de fábrica hasta que vuelve vacío es de 6 horas. Con este proceso es de 15 minutos, teniendo en cuenta la cercanía de la fábrica y la adaptación de los camiones”, anotó Barberá.
La preparación del picking introduce otra de las principales innovaciones de la planta de KH Lloreda. En la planta superior del almacén se ha desarrollado un robot a medida que permite la realización totalmente automática de palés mixtos. Ante la inexistencia de este tipo de robots dedicados exclusivamente al picking, lo que hizo KH fue adaptar la tecnología que había en el mercado a sus necesidades: “Adquirimos un robot antropomórfico de esos habituales en el sector de la automoción y lo programamos con las tareas que habitualmente haría un operario”, comentó Barberá.
Una vez lanzada la carga de trabajo, el robot analiza cada pedido y valora si existe algún condicionante de preparación: referencia por palé, altura máxima, etc. Una vez analizados todos los condicionantes el robot evalúa las líneas del pedido y determina el orden adecuado de preparación, generando de la forma más óptima los palés solicitados. Una vez terminado el palé de picking, este se envía a enfardar y es en este momento donde aprovechando el movimiento giratorio de los palés, se realiza la captura de los tags con unidad lectora RFID y se asocia el contenido a un nuevo número de contenedor. El palé de picking debidamente identificado se reincorpora como entrada en silo. El SGA posiciona el palé en la zona de cabecera de muelles a la espera de su expedición junto con los posibles palés completos de la preparación.
“Cada cliente de grandes superficies tiene sus condiciones de recepción y estas no son iguales. Algunos quieren la mercancía por columnas, otros quieren un palé mixto, otros referencia por palé y todo eso ha sido la dificultad para programar los movimientos del robot. Cuando un operario hace picking se rige por la ley del mínimo esfuerzo y nosotros hemos conseguido que el robot reproduzca estos movimientos, es decir, que si solo tiene que coger 10 cajas, no coja 40. Esto, aunque parece sencillo, ha dificultado la programación del robot”.
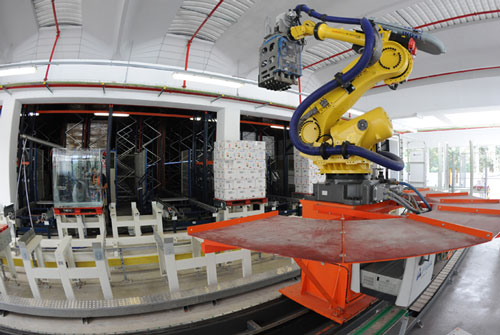
“Si no existe, nos lo inventamos nosotros”
Todos los pedidos para las áreas de Cataluña, Baleares y Canarias se entregarán directamente desde este nuevo almacén de distribución de KH Lloreda. Y los pedidos del resto de la península se entregarán en función del volumen a través de envíos directos desde el nuevo almacén o bien a través de la red de distribución capilar del operador logístico designado. “Con este nuevo sistema KH puede entregar el 65% de los pedidos directamente; para el otro 35% nos apoyaremos en el operador, pero le entregaremos el pedido ya preparado y su función será únicamente el transporte”, indicó Barberá.
El nuevo modelo de KH introduce otra novedad. En palabras del jefe de Tráfico de KH Lloreda: “Queremos ser capaces de acercar la mercancía a la plataforma final de servicio, es decir, en un ‘cross docking’ habitual, lo que hace el fabricante es acercar toda la mercancía al operador y él se preocupa de pasarlo por su plataforma de servicio y después hacer la entrega. Nosotros nos atrevemos a entregar directamente la mercancía a la propia plataforma de servicio, evitando manipulaciones, optimizando nuestro transporte y consiguiendo que se toque la mercancía una sola vez”.
Para cargar camiones que no estén adaptados como los suyos, KH Lloreda se encontró con el problema que no existe una herramienta en el mercado que facilitara la tarea. “Josep Maria tienen una máxima, que es que si una cosa no existe, nosotros la inventamos —añadió Carlos Barberá— y por ello, KH7 diseñó, proyectó y desarrolló esta nueva herramienta. Hemos unido una serie de elementos ya existentes en el mercado y una ingeniería ha conseguido robotizar todos los elementos de manera que se puede cargar y descargar camiones convencionales que no están especialmente adaptados sin la intervención de ninguna persona”. Este sistema consta de un brazo de grúa al que le se le ha aplicado un mástil de carretilla y un posicionador triple de horquillas y al que se le ha automatizado todos los movimientos hidráulicos de manera que ayudado por un lector láser es capaz de cargar y descargar los camiones de forma autónoma.
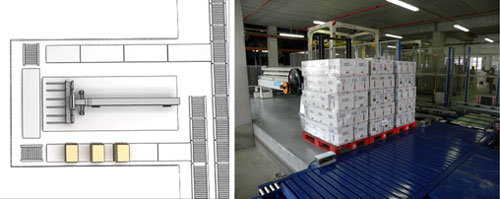