90.000 toneladas de neumáticos y 6.000 camiones expedidos en un año
La fábrica de Michelin de Valladolid, la más eficaz del mundo
Esto es lo que está consiguiendo Michelin en su planta de Valladolid. Lo ha hecho introduciendo nuevos modelos de gestión del trabajo, la producción y el almacenaje en su planta. Pero vayamos por partes. Dos de octubre de 1973: ese día la factoría vallisoletana produjo su primera goma. Hoy en día, la factoría dispone de cadenas automáticas para la confección de neumáticos de turismo de gama media-alta, equipadas con los últimos avances tecnológicos para este tipo de procesos.
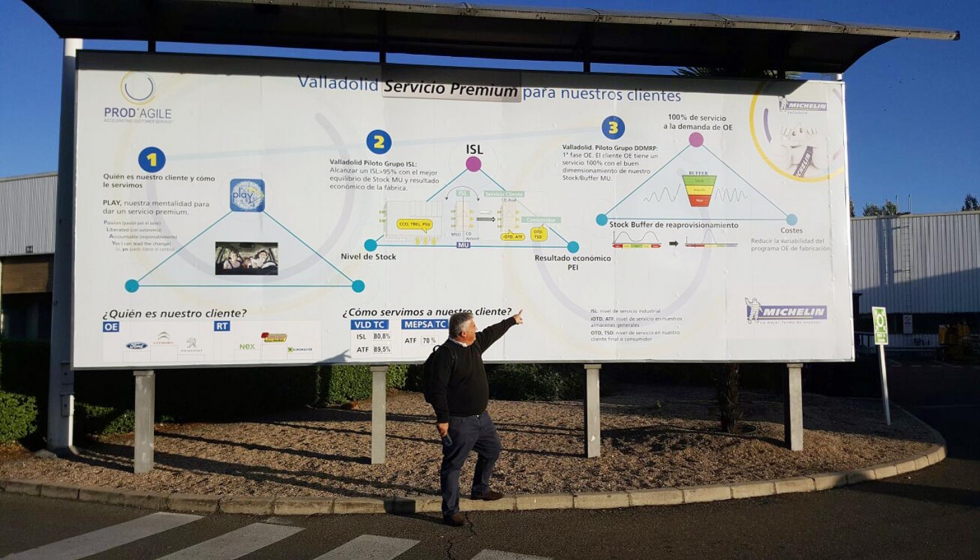
Todo esto convierte a la fábrica en una de las más modernas de la compañía, lo que permite a la marca contar con una cultura industrial propia y asentada. Sin embargo, Michelin es consciente de que el servicio en algunas líneas de producto de la fábrica es mejorable… sobre todo en neumáticos de recambio.
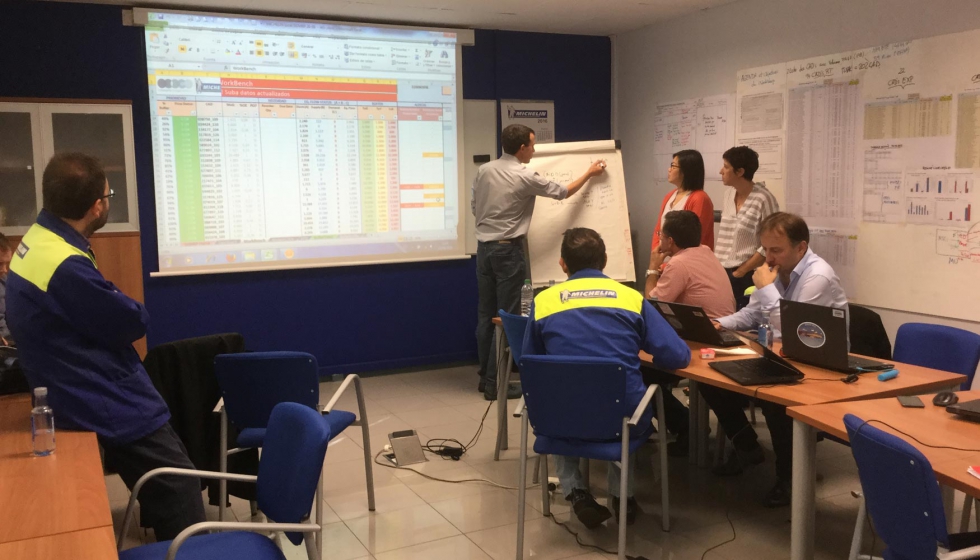
De más de seis meses para conseguir un 600 hasta (casi) el aquí y el ahora
Hasta ahora, pese a la información que ofrecían los sistemas MRPs (Material Requirement Planning -Planificación de las necesidades de materiales-), las fábricas se anotaban un nivel de servicio alto, pero con muchos esfuerzos económicos –cambios de planificación, horas extra, envíos urgentes-.Este sistema, válido en los años 70/80 del pasado siglo y que permitió que el plazo de entrega de un Seat 600 pasara de un año a sólo seis meses, ya no es suficiente para competir en el siglo XXI.
¿Y qué ha cambiado? El Cliente actual, más informado y exigente, quiere un modelo de neumático particular y lo quiere en el acto, haciendo que la demanda sea variable e imprevisible y que la fábrica deba modificar constantemente los planes de producción generados por el MRP, además de aumentar los costes de producción, para, en algunas ocasiones, no llegar a tiempo.
Para conseguir esta necesaria actualización en el modo de gestión del trabajo, producción y almacenaje, Michelin ha puesto en marcha dos herramientas en su fábrica de Valladolid. Por un lado, el proyecto Prod'Agile ha permitido mejorar el nivel de servicio al cliente, en términos de efectividad, haciendo la estructura de trabajo y producción de la fábrica más flexible. Dicho objetivo se ha conseguido invirtiendo en máquinas más versátiles, donde los tiempos de preparación y cambios son más pequeños y con la implantación del modelo de gestión Demand Driven MRP.
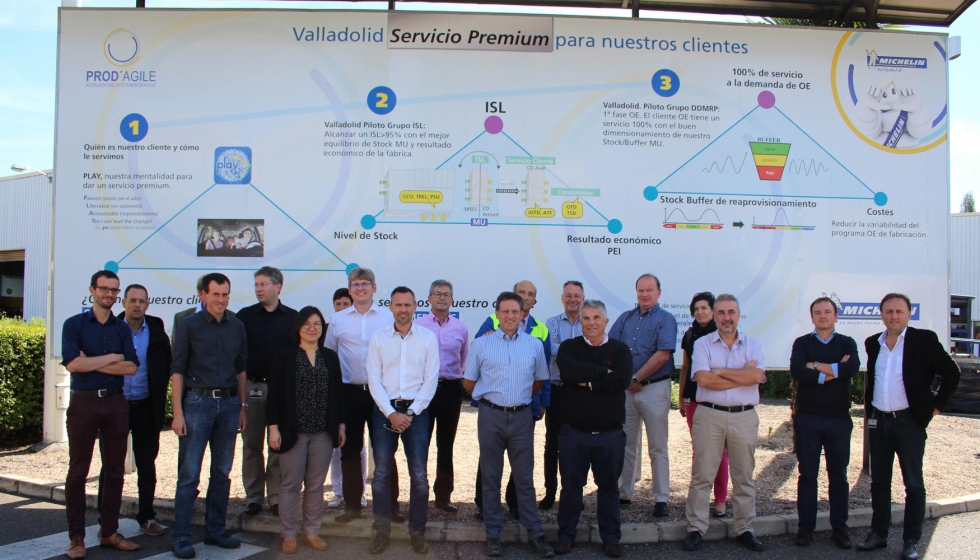
Fabricar en función de las ventas reales
Todo un cambio de filosofía. Esto es lo que ha supuesto la introducción del modelo de gestión Demand Driven MRP en la factoría vallisoletana de Michelin. En pocas palabras, esta innovadora metodología de trabajo permite que, en vez de fabricar de acuerdo a la previsión de ventas, se produzca en función de las ventas reales.
Con este objetivo, se ha diseñado un buffer de producto, dinámico y cambiante en función de las ventas. El buffer se encarga de dar servicio al cliente. De este modo, cuando Murphy actúa sobre compras o producción en curso y la cadena de suministro se desconecta por un breve periodo de tiempo, la fábrica puede seguir dando una respuesta rápida a los pedidos confirmados de cliente.
Además, Demand Driven MRP permite asegurar un nivel de servicio del 100%, establecer un vínculo directo entre la planta y el departamento de Servicio al Cliente, mejorar la calidad y nivel de los stocks y, por último, absorber posibles fluctuaciones de la demanda.
Ampliación del centro logístico
En las obras, la compañía ha invertido 13 millones de euros, lo que permitirá albergar los neumáticos de turismo y agrícola destinados a todos los continentes, además de los neumáticos renovados de camión con destino a Europa, producidos todos ellos en la fábrica.
La ampliación ha supuesto la construcción de 30.000 metros cuadrados de almacén que, unidos a los 25.000 metros cuadrados existentes, eleva la superficie de almacenamiento hasta los 55.000 metros cuadrados. ¿El objetivo de los trabajos y la inversión? Adaptar los flujos de material en almacén y la salida del producto a la capacidad de servir una demanda mayor y más compleja, propiciada por el proyecto Prod'Agile.
Los nuevos almacenes permiten albergar la producción de neumáticos de la fábrica de Valladolid, con destino a todos los continentes. Anualmente desde el Centro Logístico de Valladolid se expiden más de 90.000 toneladas de neumáticos, es decir, unos 6.000 camiones.
Estos proyectos de mejora de la competitividad de la fábrica de Michelin Valladolid, como eslabón clave dentro de una cadena de suministro del siglo XXI, han permitido mejorar el nivel de servicio industrial y que el departamento Servicio Cliente Michelin de Neumáticos de Primer Equipo para Europa haga la siguiente afirmación:
“Los procesos Demand Driven MRP han mejorado significativamente la gestión de flujos en el corto plazo. Ya desde el inicio de la fase piloto, no hemos identificado ninguna crisis y hemos notado un aumento de la sensibilidad de la fábrica a las necesidades de cliente. Actualmente, la comunicación con la fábrica de Valladolid es más fluida y esto permite que seamos capaces de responder incluso ante modificaciones de pedidos firmes”.