T-Systems desarrolla un modelo Plant Simulation para la planificación logística
28 de noviembre de 2011
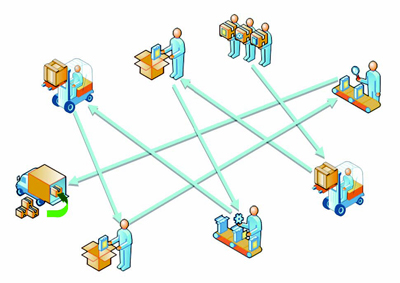
Según Marta Fernández, consultora logística de T-Systems Iberia “el suministro sincronizado está basado en planificar el abastecimiento de forma que el fabricante disponga solamente de la cantidad precisa para garantizar la producción evitando el exceso de material en la línea. En algunas ocasiones la provisión no puede realizarse directamente y se hace necesario el uso de almacenes intermedios dentro de fábrica —conocidos como supermercados— como nexo entre el exterior y la línea de ensamblaje. Una gestión correcta y optimizada de los procesos de preparación del material asegura una mayor calidad y eficiencia de los operarios de la línea de ensamblaje”.
La implementación de los suministros sincronizados permite, entre otros beneficios, una importante reducción de costes debido a la minimización de los desplazamientos de los operarios a pie de línea. Esta forma de aprovisionamiento debe ser cuidadosamente planificada para evitar la carencia de material en la línea, lo que en términos de producción se conoce como rotura de stock, que es una de las situaciones más críticas que pueden producirse en una línea de producción ya que impide la fabricación del producto, repercutiendo en pérdidas económicas para la empresa.
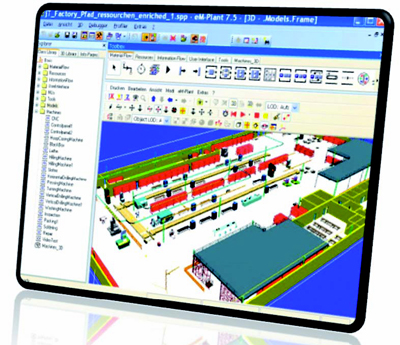
Con la llegada de este nuevo concepto de trabajo, la industria de fabricación ha sido consciente de la necesidad de prever todas y cada una de las nuevas situaciones que se van a dar lugar en sus talleres. La herramienta de simulación de flujos Plant Simulation de Siemens Industry Software permite analizar y evaluar riesgos como soporte a la toma de decisiones antes de modificar un proceso existente o crear uno nuevo.
T-Systems Iberia ha desarrollado una solución sobre Plant Simulation, que permite a sus clientes de una forma sencilla y ágil, simular las múltiples situaciones que se requieran sin tener que dedicar grandes cantidades de tiempo y recursos especializados en la creación de un modelo de simulación. “Un analista logístico sin grandes conocimientos en simulación puede ya analizar rápidamente las nuevas propuestas de trabajo y tomar decisiones con mucha más fiabilidad y rapidez” comenta Juan González Yepes, responsable de Digital Factory en T-Systems.
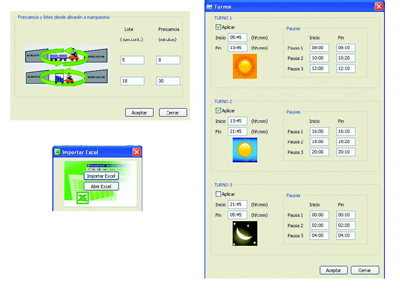
El modelo de simulación permite que el analista pueda modificar, en pocos pasos y de forma sencilla, los parámetros que van a determinar un nuevo escenario en estudio —parámetros de producción, recursos disponibles, requerimientos de materiales en línea, rutas de paso, turnos de trabajo, etc.— mediante simples ventanas de diálogo o ficheros Excel. Una vez definidos los parámetros del escenario en estudio, la solución desarrollada permite analizar tanto los suministros directos a línea desde el exterior como aquellos que se gestionan y preparan a través de los supermercados.
Como resultado, el modelo genera automáticamente una serie de informes —gráficos y tablas— que permiten analizar la saturación de recursos y optimizar sus tiempos de inactividad. Los resultados también permiten evaluar la saturación e intensidad de tráfico en las puertas de acceso y pasillos, así como denunciar riesgos de rotura de stock. En general, todos los datos obtenidos en la simulación sirven de pauta para la toma de decisiones de la forma más fiable posible, así como de eficaz soporte para la presentación de las conclusiones extraídas.
La solución desarrollada por T-Systems, que fue premiada en la 7ª edición de los Premios SIAB a las Mejores Innovaciones Tecnológicas, permite que cualquier empresa se pueda beneficiar de las ventajas que supone la simulación y pueda focalizar sus esfuerzos en la toma de las mejores decisiones para el negocio.