Requerimientos sobre la metrología dimensional para la mejora de los procesos de fabricación en el contexto industria 4.0
Son varios los retos que debe abordar la metrología dimensional para satisfacer las necesidades de medición que se presentan en un ambiente productivo y no controlado y, por lo tanto, ofrecer información con trazabilidad dimensional. Estos retos se presentan en forma de falta de trazabilidad en mediciones fuera del laboratorio, condiciones ambientales inestables, reducción de los tiempos de medición para la medición 100% de la producción o gestión de grandes volúmenes de información metrológica. Sin embargo, el principal reto en la actualidad es conocer el error de medida de los sistemas de medición que se emplean en los entornos productivos y en escenarios de medición de alto rango.
1. Introducción
A diferencia de la actividad de medición que se realiza en un laboratorio de metrología dimensional, donde las verificaciones y calibraciones se realizan exclusivamente con máquinas de medir por coordenadas (MMC) debidamente caracterizadas según la normativa actual, la actividad de medición en el entorno productivo se lleva a cabo con MMCs de gran tamaño, MMCs portables menos conocidas e incluso con los propios medios productivos o robots que participan en el proceso de fabricación. La normativa actual no contempla todos los procedimientos para la asignación de incertidumbre de todos los sistemas de medición que se emplean in-situ y por ese motivo, se deben emplear procesos de calibración y caracterización a medida. Para la calibración de MMC de gran tamaño, empleada frecuentemente en sectores como automoción y aeronáutico, la norma ISO 10360-2:2010 [1] permite emplear la interferometría láser como patrón para calibración de MMC de gran tamaño empleadas para la medición de dimensiones lineales. Para los sistemas de medición portables, los dos equipos de medida más utilizados en el entorno productivo y escenarios de gran volumen son los brazos articulados de medición y los láseres tracker. En el caso de los brazos articulados, existen dos normas que permiten caracterizar el comportamiento de estos sistemas, la norma ASME B89.4.22-2004 y la recomendación VDI 2617_9-2009 [2]. Para la calibración del sistema de medida láser tracker existe una norma americana conocida como ASME B89.4.19 que define un procedimiento de calibración, pero a día de hoy el uso de esta norma no es extendida porque el proceso de calibración muestra un grado alto de variabilidad [3]. En cuanto a utilizar los medios productivos como sistemas de medición en proceso de fabricación, cada vez es más habitual que las maquinas herramienta (MH) incorporen sistemas de palpado táctil que permiten llevar a cabo mediciones en MH.
Sin embargo, la trazabilidad de estas mediciones no está asegurada en la actualidad y por ello, no se puede emplear esta información como feedback metrológico para mejoras del proceso de fabricación o validación de pieza en MH [4]. En cuanto a utilizar robots como sistemas de medición, el sistema robótico como tal no ofrece buenas prestaciones de medición comparado con los sistemas portables mencionados arriba. Sin embargo, ofrecen la posibilidad de funcionar como posicionadores para que mediante un marco metrológico externo se pueda garantizar la precisión de las mediciones realizadas con el robot. En la actualidad es habitual encontrar aplicaciones donde se utiliza un láser tracker o sistema de seguimiento externo (laser radar, sistemas de digitalizado con targets en el mensurando…) que aporta precisión a la solución final [4–10].
2. Trazabilidad de los sistemas de medición
En este apartado se describen los procedimientos y normas conocidas para la asignación de incertidumbre de los sistemas de medición que se emplean en entornos productivos para garantizar la calidad del producto fabricado. Además, se describen procedimientos de medición novedosos desarrollados por IK4-Tekniker para completar y garantizar la trazabilidad en aquellos casos donde la trazabilidad no está asegurada por normativa.
2.1. Trazabilidad para MMC de gran tamaño
La organización ISO (International Organization for Standardization) realizó una revisión de la parte 2 de la norma técnica ISO 10360 en el año 2010. En esta revisión se introdujo la posibilidad de utilizar la interferometría láser como un patrón válido para la calibración de MMCs destinadas a la medición de dimensiones lineales [11]. Además, el uso de patrones físicos en la calibración (barras de bolas patrón, calas patrón…) hace que la calibración de la MMC sea muy costosa ya que la problemática principal reside en la complejidad de utilizar patrones muy largos de manera rápida y fiable.
Es en este contexto, donde la capacidad de seguir a un reflector ubicado cerca del palpador de la máquina combinado con la medición de desplazamientos lineales, hace que el sistema de medición láser tracker [12] sea de especial interés para las calibraciones de MMC de tamaño entre 1.500 y 13.500 mm de longitud de eje. Según la normativa actual, la medición consta de 105 longitudes repartidas en 7 líneas de medición (obligatorio: 4 diagonales en el espacio, restante: a elegir por el usuario de la máquina), en cada una de estas 7 líneas se miden 5 longitudes de ensayo y se repite cada una de ellas 3 veces. En total, se realizan 105 mediciones que permiten obtener los dos parámetros de referencia:
- EL: Error de medida en la longitud
- R0: Rango de repetibilidad del error en la medida de longitud
Especificaciones de la máquina a definir por el fabricante:
- EL, MPE: Máximo error permitido en el error de medida en la longitud
- R0, MPE: Máximo límite permitido del rango de repetibilidad
Comparando el error obtenido en el ensayo con las especificaciones definidas por el fabricante de la MMC, se puede certificar que el sistema de medición cumple con las especificaciones y que, por lo tanto, se convierte en una fuente de información trazable de cara a asegurar la calidad de los productos fabricados.
Como novedad, la revisión introduce la necesidad de realizar la verificación de la MMC con un palpador de longitud de 150 mm para conocer el funcionamiento de la máquina cuando se trabaja con palpadores largos. Esta parte de la norma no es obligatoria, por lo que, si el usuario lo ve conveniente y así lo expresa por escrito, esta parte se puede anular, simplificando así el ensayo [13].
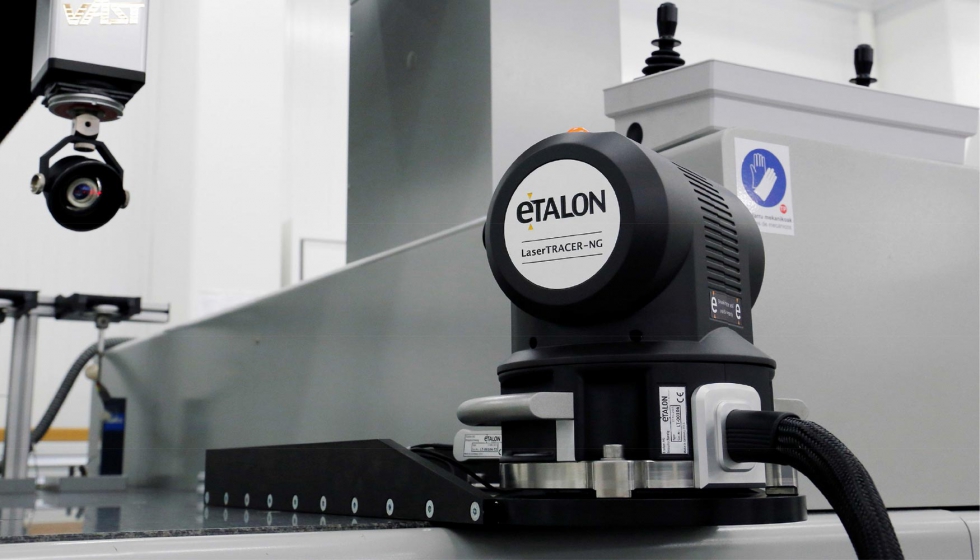
2.2. Trazabilidad para sistemas de medición portables
La trazabilidad de los sistemas de medición portables como láser tracker y brazos articulados se han trabajado sobre todo en el mercado americano mediante las normas ASME especificadas arriba. Sin embargo, en el mercado europeo y por lo tanto en el mercado español, se han estudiado menos. Uno de los proyectos que tiene el Centro Español de Metrología (CEM) en activo consiste en establecer la estructura y metodología necesaria para la calibración de sistemas láser tracker [14]. Por lo general, el sistema de medición láser tracker parte desde una incertidumbre de 0,03 mm [15] y los brazos articulados parten desde 0,06 mm [16], pero el modelo de expansión de incertidumbre es diferente ya que el principio de funcionamiento de ambos equipos es realmente diferente.
En lo que se refiere a la asignación de incertidumbre para los sistemas de medición portables, en la actualidad la metodología más empleada consiste en aplicar la norma ISO 15530-4 [17]. En esta norma se describe el uso de la herramienta de simulación de Montecarlo para en base a una simulación numérica asignar incertidumbre a un proceso concreto de medición. Para ello, se debe modelizar el error del sistema de medición empleado y a partir de ahí se ejecuta la simulación. En la práctica, existe una herramienta software conocida como Spatial Analyzer que permite realizar este ejercicio de asignación de incertidumbre de manera robusta y fiable [18–21].
Desde IK4-Tekniker se ha puesto en marcha la calibración de brazos articulados de medición en base a la norma ASME B89.4.22-2004 [16]. En el proceso de análisis inicial se compararon las dos normas existentes para definir el procedimiento de calibración de dicha actividad y finalmente fue la norma americana ASME la elegida para el proceso de certificación con ENAC [2].
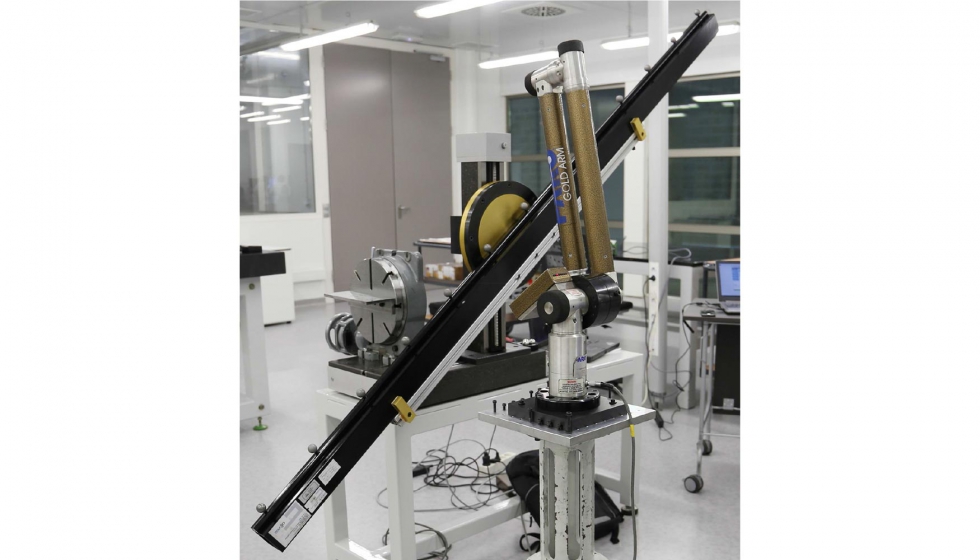
2.3. Trazabilidad para MH como MMC dimensional
Desde hace una década, se está investigando sobre el empleo de la MH como sistema de medición en los propios entornos productivos [4,22–24]. El hecho de emplear una MH como sistema de medición permite que el proceso productivo sea más flexible. El principal motivo reside en que la medición en MH permite caracterizar el error geométrico de la máquina, agilizar los procesos de alineamiento de la pieza, proporcionar información al proceso productivo para corregirlo y validar la pieza en máquina y así evitar su traslado a un laboratorio de medición.
![Figura 3. Mediciones trazables en MH [25] Figura 3. Mediciones trazables en MH [25]](https://img.interempresas.net/fotos/1612092.jpeg)
Debido a la similitud entre una MH y una MMC, algunos de los métodos empleados para la asignación de incertidumbre en MMC se han adoptado para MH. De todas formas, el procedimiento general para la asignación de incertidumbre se especifica en la guía ISO 98- 3:2008 (GUM) [26]. En la práctica, son tres las aproximaciones para la asignación de incertidumbre de una medición realizada en una MH:
- El método de substitución basado en la norma ISO 15530-3: En este procedimiento se emplea una pieza patrón calibrada con características similares a la pieza que se fabrica en el proceso productivo en el que se llevará a cabo la calibración. Además, el proceso de medición y las condiciones ambientales deben de ser similares entre el proceso de evaluación de incertidumbre y medición de la pieza en proceso [27].
- La segunda aproximación está basada en el uso de la simulación para la asignación de incertidumbre en MH, como comentado en el caso de los sistemas de medición portables [17]. El procedimiento está basado en la norma ISO 15530-4 y por ahora ha sido aplicado en MMC. En un esfuerzo conjunto entre proveedores de equipos de metrología, universidades y centros nacionales de metrología como el National Physical Laboratory (NPL), en la actualidad existe una herramienta para la asignación de incertidumbre en MMC conocida como Virtual Coordinate Measuring Machine (VCMM) [28].
- La última opción describe la realización de la asignación de incertidumbre mediante la ejecución de un presupuesto de errores. En este caso, se deben conocer y caracterizar todas las fuentes de incertidumbre que afectan al proceso de medición y contemplarlos como se describe en la recomendación VDI 2617-11 [29].
En el caso de MH de tamaño medio y grande la primera opción es la aproximación que se está empleando en la actualidad para la asignación de incertidumbre de mediciones realizadas en MH. En este caso, el uso de una pieza como pieza patrón es un factor que prácticamente cualquier empresa se puede permitir, facilitando y agilizando el proceso de asignación de incertidumbre.
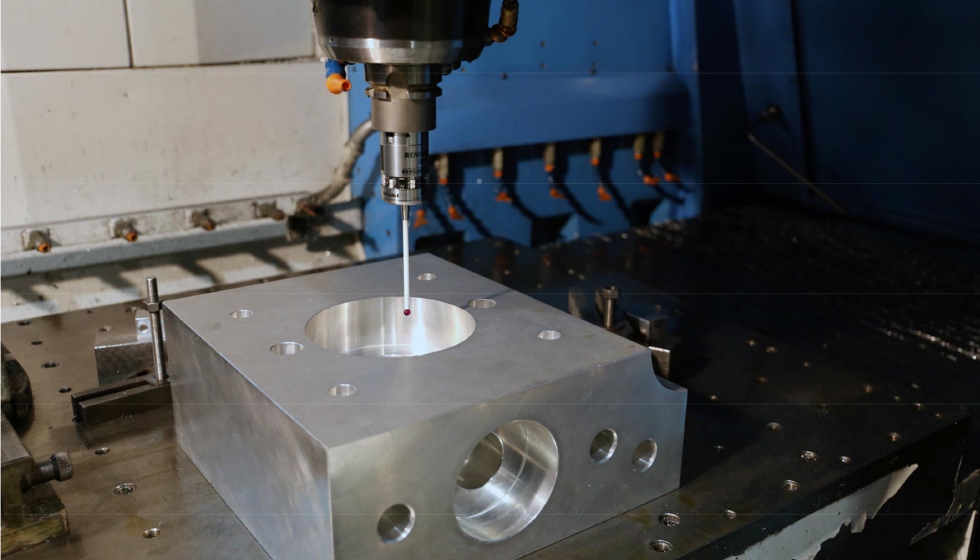
En cambio, para las MH de gran tamaño no es viable emplear una pieza patrón como artefacto de calibración ya que el coste de la pieza es muy alto y la manipulación de la pieza muy costosa. Por este motivo, la aproximación basada en presupuesto de errores es la opción que más se está investigando en este caso para realizar la asignación de incertidumbre. El hecho de realizar un presupuesto de errores exige conocer y caracterizar cada fuente de incertidumbre que se contempla en la realización del presupuesto y es aquí donde la caracterización del comportamiento de una MH de gran tamaño tiene su dificultad. El principal enemigo de la geometría de una MH es la variación de temperatura ya que genera un error de comportamiento variable que es complicado de caracterizar [30–34]. Por ello desde IK4-Teknikerse están desarrollando procedimientos y metodologías para la caracterización del error geométrico de una MH en condiciones de taller no controladas. En el año 2012, IK4-Tekniker desarrolló una solución novedosa para la caracterización del error geométrico de una MH de gran tamaño en base a la técnica de multilateración [35]. Esta solución permite conocer el error geométrico de una MH en un tiempo de medición reducido, pero se ve afectado por la deriva térmica que sufre la MH y que afecta a la calidad del resultado.
Con el objetivo de agilizar las mediciones de la volumetría de las MH y evitar el efecto de la temperatura en el proceso de medida, Zayer e IK4-Tekniker han desarrollado una solución conjunta conocida como multilateración simultánea en la que se emplean cuatro sistemas de medición al mismo tiempo para realizar la multilateración de la geometría de la MH y reducir así el tiempo de adquisición a prácticamente 20 minutos. Así se cumple un doble objetivo: Evitar el efecto de la temperatura en la medición y ser capaces de medir la variación de la geometría de la MH acorde a la variación de temperatura.
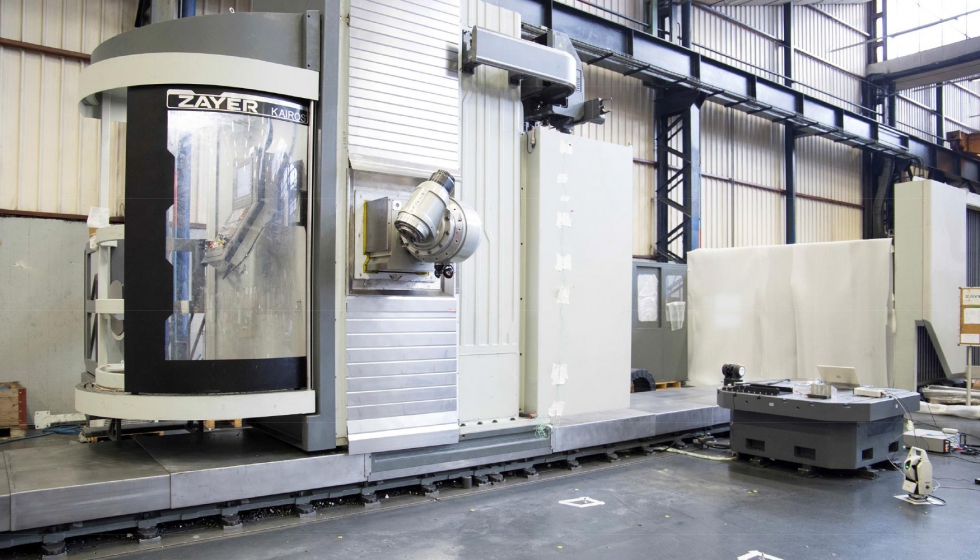
2.4. Trazabilidad para los robots como MMC dimensional
La idea de utilizar un sistema robótico como sistema de medición no es nuevo [4–10]. Sin embargo, el robot no está diseñado para procesos de medición y de ahí que no pueda ofrecer buenas prestaciones en posicionamiento y repetibilidad espacial. En base a estas características, cualquier ejercicio de precisión mediante un robot tiene que ser ejecutado mediante un sistema de medición externo o bien tratar de realizar la calibración del robot. Actualmente, es habitual encontrar aplicaciones donde se utiliza un sistema de seguimiento externo (láser radar, láser tracker o sistemas de digitalizado con targets en el mensurando) para tratar de aumentar la precisión de la solución de medida basada en un robot. En realidad, es estas aplicaciones el empleo del robot es de mero posicionador del sistema de medida o retroreflector mediante el cual se ejecutan las medidas.
Sin embargo, lo realmente interesante es emplear el robot como un sistema de medición autónomo. En este proceso, se debe llevar a cabo una calibración del robot que se fundamente en la normativa que regula esta calibración [36,37]. En estos procedimientos se busca la caracterización de varias características del robot como la precisión, la repetibilidad y la pose. En realidad, el proceso de calibración de un robot supone modelizar, medir y resolver los parámetros geométricos de interés del sistema en cuestión, para poder ajustar a la realidad los parámetros físicos del robot. Una vez estimados estos parámetros se actualiza el modelo y se utiliza, lo que supone el uso de un robot calibrado.
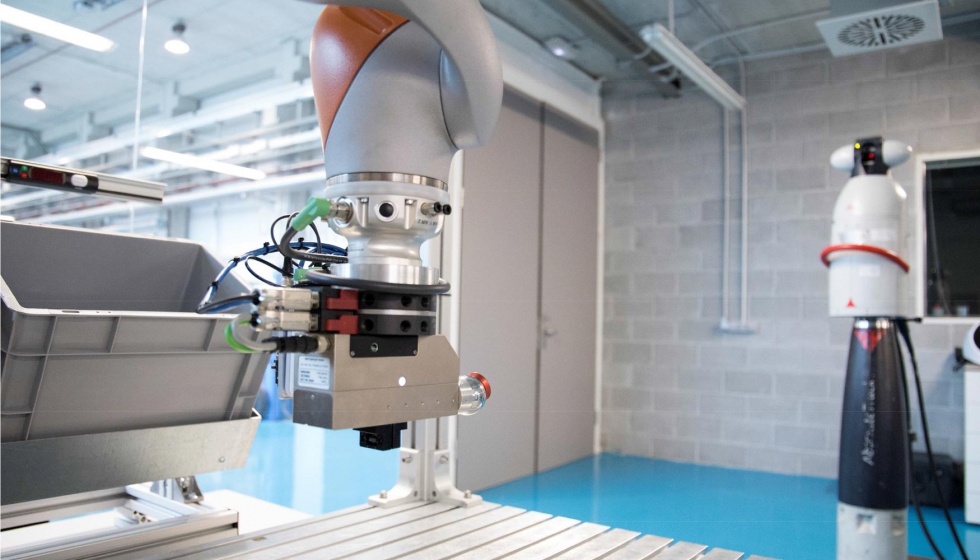
3. Conclusiones
Existen diferentes retos que debe abordar la metrología como tecnología transversal en el contexto de la industria 4.0 como es la falta de trazabilidad en mediciones fuera del laboratorio, condiciones ambientales inestables, reducción de los tiempos de medición para la medición 100% de la producción o gestión de grandes volúmenes de información metrológica. Sin embargo, el principal reto en la actualidad está en una fase anterior. La caracterización y conocimiento de los sistemas de medición que se emplean en los entornos productivos y de gran volumen, como el sector eólico o aeronáutico.
Entre los sistemas que más se emplean en el entorno productivo están las MMC de gran tamaño, los sistemas de medición portable, las MH como MMC y los sistemas robot. Cada una de estas tecnologías se encuentra en un estadio en lo que a su trazabilidad se refiere y es por ello, que IK4-Teknikerestá realizando un esfuerzo en caracterizar y definir procedimientos de calibración y uso adecuado, con el objetivo que la incertidumbre de uso de estos equipos en planta productiva sea el menor posible.
Referencias
[1] ISO, Geometrical product specifications (GPS) — Acceptance and reverification tests for coordinate measuring machines (CMM) — Part 2: CMMs used for measuring linear dimensions, 2009. https://www.iso.org/standard/40954.html.
[2] J. Santolaria, a C. Majarena, D. Samper, J.J. García, J.J. Aguilar, Comparación de estándares internacionales de verificación de brazos articulados de medición por coordenadas: ASME B89. 4. 22- 2004 vs VDI 2617 _ 9-2009, XVIII Congr. Nac. Ing. Mecánica. (2009) 1–9.
[3] K.M. Nasr, A.B. Forbes, B. Hughes, A. Lewis, ASME B89.4.19 standard for laser tracker verification – experiences and optimisations, Int. J. Metrol. Qual. Eng. 3 (2012) 89–95. doi:10.1051/ijmqe/2012014.
[4] R. Schmitt, M. Peterek, E. Morse, W. Knapp, M. Galetto, F. Härtig, G. Goch, B. Hughes, A. Forbes, W. Estler, Advances in Large-Scale Metrology – Review and future trends, CIRP Ann. - Manuf. Technol. (2016). doi:10.1016/j.cirp.2016.05.002.
[5] J. Jamshidi, A. Kayani, P. Iravani, P.G. Maropoulos, M.D. Summers, Manufacturing and assembly automation by integrated metrology systems for aircraft wing fabrication, Proc. Inst. Mech. Eng. Part B J. Eng. Manuf. 224 (2010) 25–36. doi:10.1243/09544054JEM1280.
[6] R. Schmitt, M. Peterek, S. Quinders, Concept of a Virtual Metrology Frame Based on Absolute Interferometry for Multi Robotic Assembly, m (2014) 79–86.
[7] N. and J.M.. Usman, Z.; Monfared, R.P.; Lohse, An investigation of highly accurate and precise robotic hole measurements using non-contact devices, 204 (2016) 0–37. doi:10.1051/ijmqe/2016007.
[8] J.E. Muelaner, O.C. Martin, P.G. Maropoulos, Achieving low cost and high quality aero structure assembly through integrated digital metrology systems, Procedia CIRP. 7 (2013) 688–693. doi:10.1016/j.procir.2013.06.054.
[9] R. Schmitt, C. Lamers, F. Demeester, Global referencing systems and their contribution to a versatile production, Int. Conf. Indoor Position. Indoor Navig. (2011) 21–23.
[10] A.R. Norman, A. Schönberg, I.A. Gorlach, R. Schmitt, Validation of iGPS as an external measurement system for cooperative robot positioning, Int. J. Adv. Manuf. Technol. 64 (2013) 427–446. doi:10.1007/s00170-012-4004-8.
[11] David Flack - National physical laboratory (NPL), Good Practice Guide for CMM verification, 2011. http://www.biosecurity.govt.nz/files/regs/animal-welfare/pubs/naeac/guide-for-animalsuse.pdf.
[12] Etalon AG., Laser tracer MT, Http://www.etalon-Ag.com/en/products/lasertracer-Mt/. (n.d.). http://www.etalon-ag.com/en/products/lasertracer-mt/.
[13] IK4-TEKNIKER, Calibración acreditada de Máquinas de Medir por Coordenadas (MMC) con interferometría láser, 2016. https://issuu.com/ik4-tekniker/docs/fichametro_calibracioninterferometr.
[14] C.E. de Metrología, Calibración de sistemas láser tracker, (n.d.). http://www.cem.es/cem/estructura-del-cem/%C3%A1rea-de-longitud/laboratorio-deinstrumentos-topogr%C3%A1ficos.
[15] S. Aguado, J. Santolaria, D. Samper, J.J. Aguilar, Influence of measurement noise and laser arrangement on measurement uncertainty of laser tracker multilateration in machine tool volumetric verification, Precis. Eng. 37 (2013) 929–943. doi:10.1016/j.precisioneng.2013.03.006.
[16] U. Mutilba, G. Kortaberria, A. Olarra, A. Gutiérrez, E. Gomez-Acedo, M. Zubieta, Performance calibration of articulated arm coordinate measuring machine, in: Procedia Eng., 2013. doi:10.1016/j.proeng.2013.08.264.
[17] ISO, ISO 15530-4:2008. Geometrical Product Specifications (GPS) — Coordinate measuring machines (CMM): Technique for determining the uncertainty of measurement — Part 4: Evaluating task-specific measurement uncertainty using simulation, 2008.
[18] A. Meid, S. Sandwith, Dynamic weighting of laser tracker measurements for bundle adjustment, Boeing Large Scale Opt. Metrol. Semin. (2000).
[19] J.M. Calkins, QUANTIFYING COORDINATE UNCERTAINTY FIELDS IN COUPLED SPATIAL MEASUREMENT SYSTEMS, 2005.
[20] J.E. Muelaner, Z. Wang, J. Jamshidi, P.G. Maropoulos, Verification of the indoor GPS system by comparison with points calibrated using a network of laser tracker measurements, Proc. 6th CIRP-Sponsored Int. Conf. Digit. Enterp. Technol. 66 (2010) 607–619. doi:10.1007/978-3-642-10430-5_47.
[21] S. Sandwith, R. Predmore, Real-time 5-Micron Uncertainty with Laser Tracking interferometer Systems using Weighted Trilateration, Boeing Large Scale Metrol. Semin. (2001).
[22] R. Schmitt, M. Peterek, Traceable measurements on machine tools-Thermal influences on machine tool structure and measurement Uncertainty, Procedia CIRP. 33 (2015) 576–580. doi:10.1016/j.procir.2015.06.087.
[23] S. Nisch, R. Schmitt, Production integrated 3D measurements on large machine tools, 2010.
[24] F. Keller, Traceability of on-machine measurements under a wide range of working conditions, Traceable in-process dimensional measurement Final Workshop, (2016).
[25] Physikalisch-Technische Bundesanstalt (PTB)., Traceable in-process dimensional measurements (TIM) EMRP project IND 62, (n.d.). https://www.ptb.de/emrp/ind62-home.html.
[26] ISO, ISO/IEC Guide 98-3:2008: Uncertainty of measurement – Part 3: Guide to the expression of uncertainty in measurement., 2008.
[27] ISO 15530-3: 2004. Geometrical Product Specifications (GPS) — Coordinate measuring machines (CMM): Technique for determining the uncertainty of measurement — Part 3: Use of calibrated workpieces or standards, 2004.
[28] E. Trapet, F. Wäldele, Trapet, Waldele - 1991 - A reference object based method to determine the parametric error components of coordinate measuring machines and machine tools.pdf, Measurement. 9 (1991) 17–22. doi:http://dx.doi.org/10.1016/0263-2241(91)90022-I.
[29] Verein Deutscher Ingenieure (VDI), VDI/VDE 2617-11-Accuracy of Coordinate Measuring Machines - Characteristics and Their Checking - Determination of the Uncertainty of Measurement for Coordinate Measuring Machines Using Uncertainty Budgets., 2011.
[30] S.R. Postlethwaite, J.P. Allen, D.G. Ford, Machine tool thermal error reduction - An appraisal, Proc. Inst. Mech. Eng. Part B J. Eng. Manuf. 213 (1999) 1–9. doi:09544054.
[31] D. Ross-pinnock, G. Mullineux, Compensating for thermal and gravitational effects in structures and assemblies, 2016.
[32] J. Bryan, International Status of Thermal Error Research (1990), CIRP Ann. - Manuf. Technol. 39 (1990) 645–656. doi:10.1016/S0007-8506(07)63001-7.
[33] J. Bryan, International Status of Thermal Error Research, (1967). doi:10.1016/S0007- 8506(07)63001-7.
[34] A. Blazejewski, W. Kwasny, T. Gim, Modelling thermal deformation of tilting rotary table with direct drive system, J. Mach. Eng. 10 (2010).
[35] A. Olarra, M. Zubeldia, E. Gomez-acedo, G. Kortaberria, Measuring positioning accuracy of large machine tools, 2012.
[36] ISO, ISO 9283: Performance criteria and related test methods, 1998.
[37] ISO, ISO TR13309: Test equipment and metrology methods for performance evaluation in accordance with ISO 9283., 1995.
Agradecimientos
Los autores de este trabajo expresan su agradecimiento a la empresa Zayer por su colaboración no solo en la fase investigadora de este trabajo, sino en la publicación del contenido y resultado obtenidos de esta investigación.